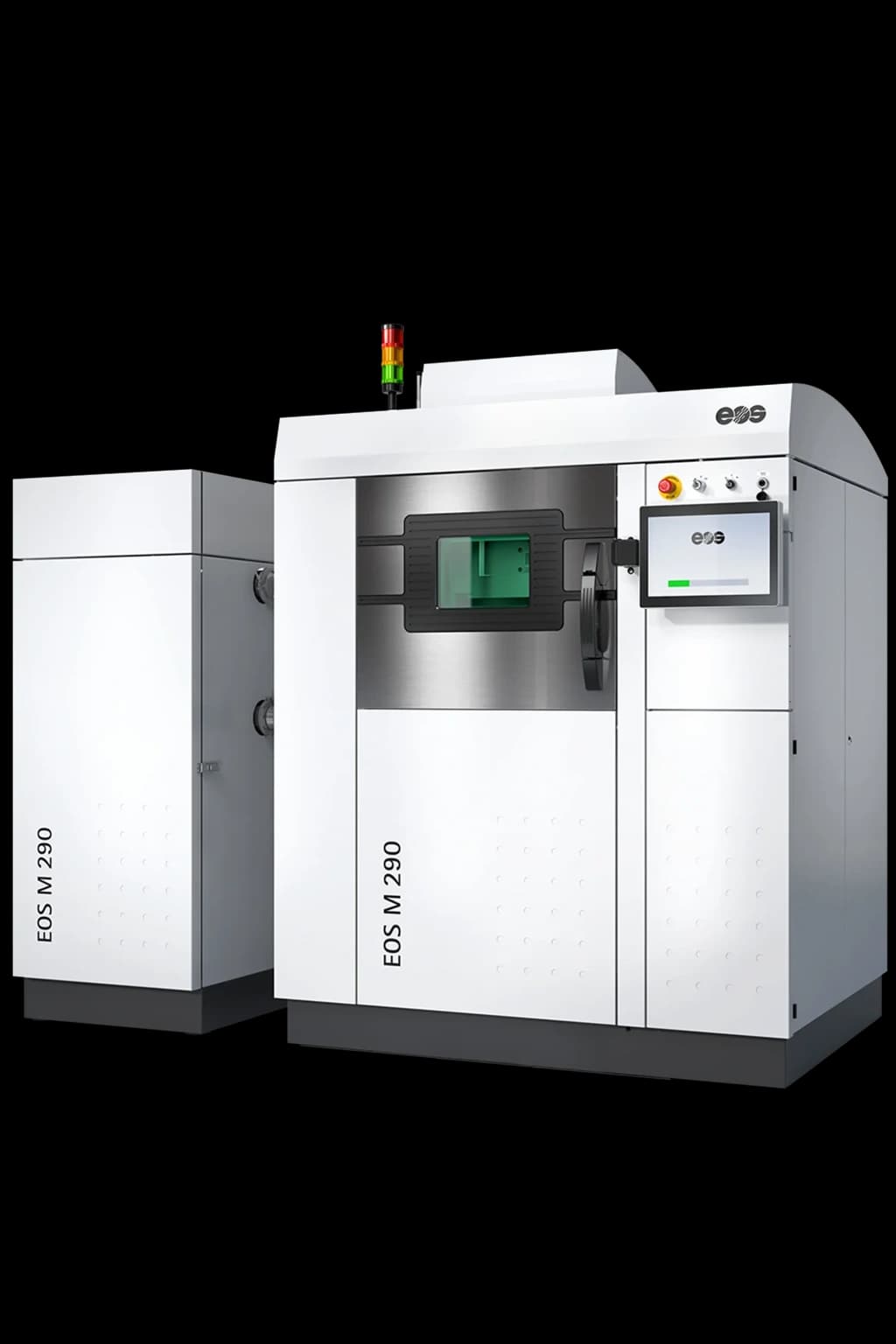
Direct Metal Laser SinteringVolume Production of High Performance End-Use Parts
Direct Metal Laser Sintering (DMLS) is an advanced additive manufacturing technique that uses a high-powered laser to selectively fuse layers of metal powder, resulting in fully dense, functional metal parts with exceptional strength and durability.
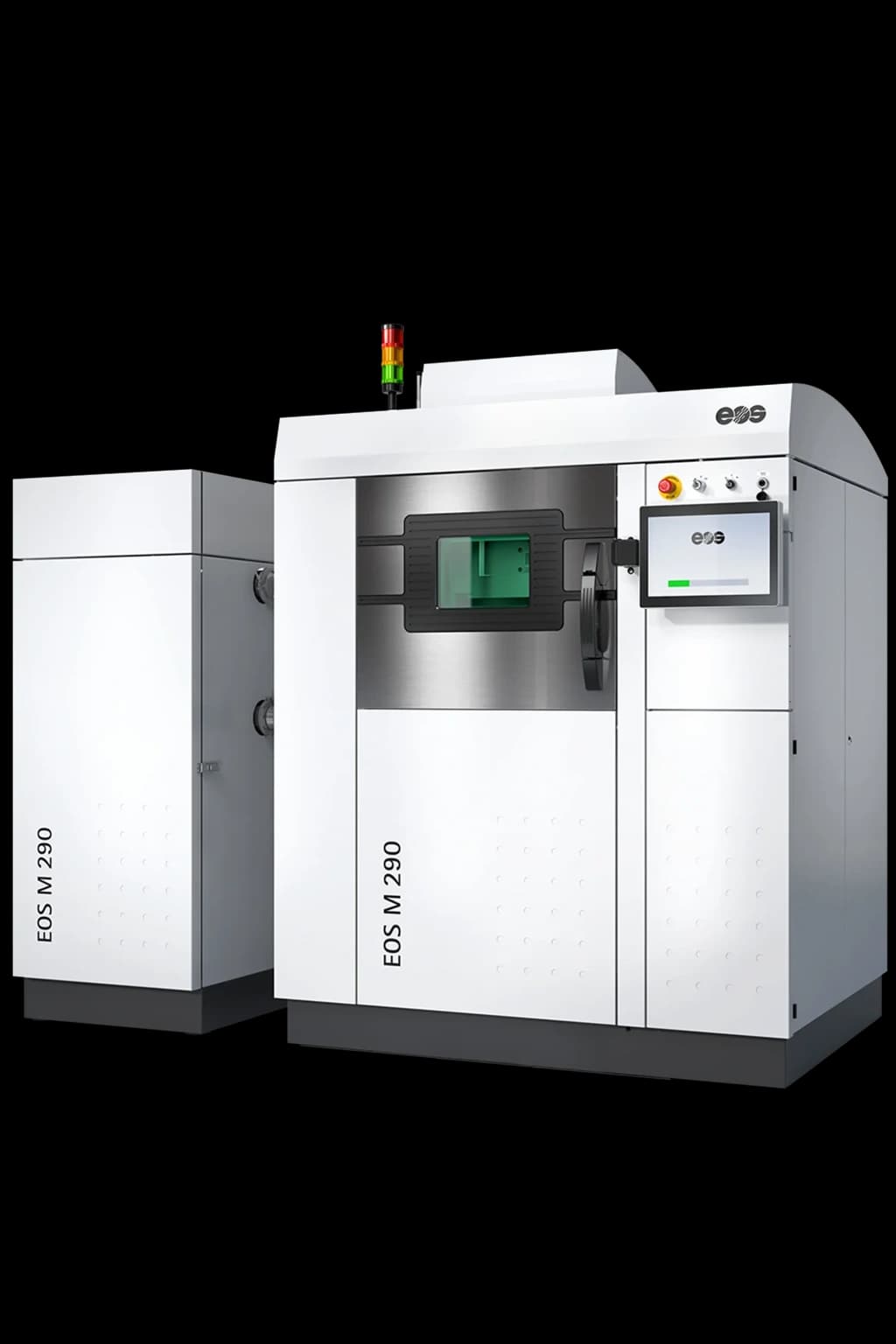
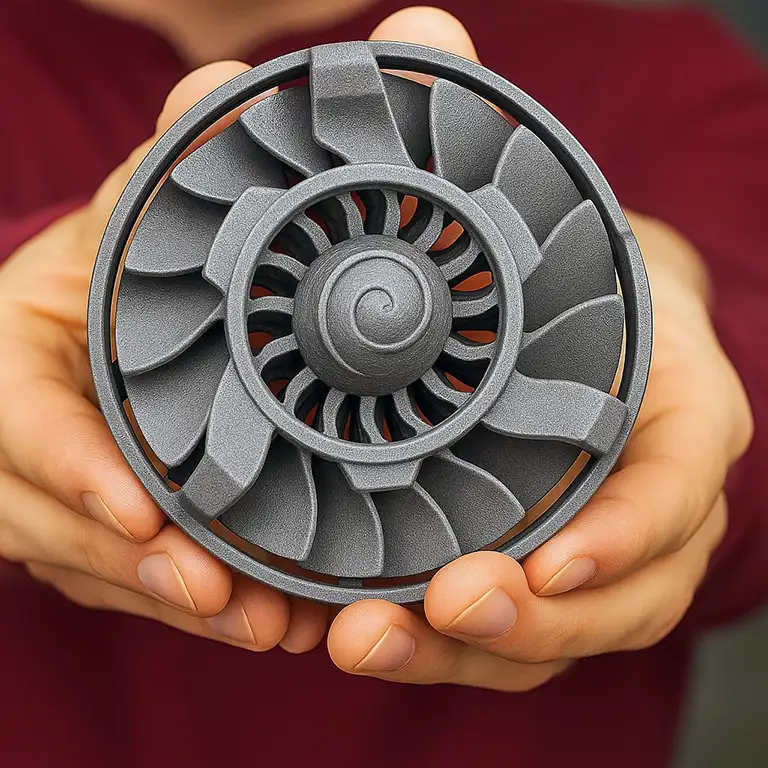
Technology Overview
Fully Dense Metal Components
DMLS produces fully dense metal parts with mechanical properties matching traditional manufacturing. Complex internal geometries and part consolidation enable revolutionary design possibilities in aerospace, medical, and automotive applications.
Advanced manufacturing capabilities enable complex geometries, functional prototypes, and end-use production parts that would be impossible or cost-prohibitive with traditional manufacturing methods. From functional prototypes to end-use production parts, this technology delivers exceptional performance across demanding industries.
Aerospace Manufacturing
Aerospace-Grade Metal Components
Critical for aerospace, medical, and high-performance applications where failure is not an option, DMLS produces fully dense metal parts with properties matching or exceeding traditional manufacturing. From titanium aerospace brackets to surgical implants, this technology enables complex internal geometries and lightweighting strategies impossible with conventional machining. Each part undergoes rigorous quality control ensuring traceability and compliance with aerospace and medical standards.
Mission-Critical Components
Aerospace and medical applications require documented material properties and full traceability, which DMLS delivers through certified material batches and detailed build reports. The high-energy laser creates metallurgical bonds equivalent to wrought metals, enabling stress-bearing components that undergo rigorous testing including fatigue, tensile, and impact analysis. Support structures are strategically designed to minimize material waste while ensuring optimal heat dissipation during the build process.
Key Advantages
Complex Geometries: Intricate internal channels, overhangs, and assemblies impossible with traditional manufacturing.
Functional Prototypes: Test mechanical properties and fit before investing in production tooling.
Custom Tooling: Jigs, fixtures, and manufacturing aids tailored to specific production requirements.
End-Use Parts: Production components for aerospace, medical, automotive, and industrial applications.
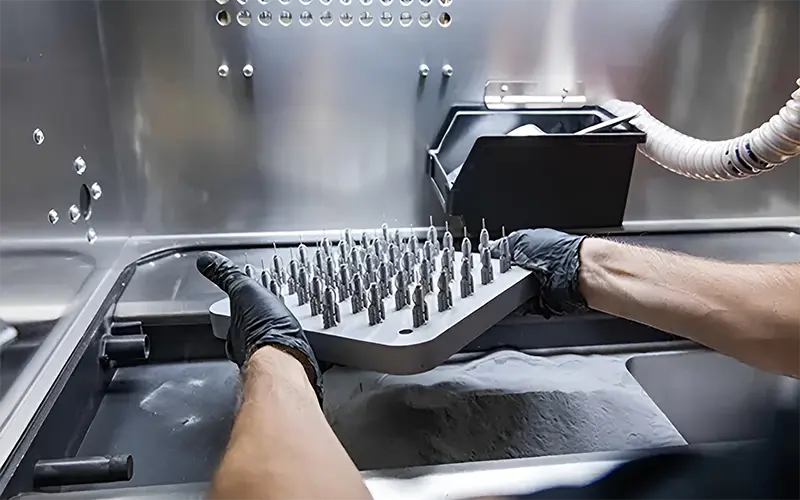
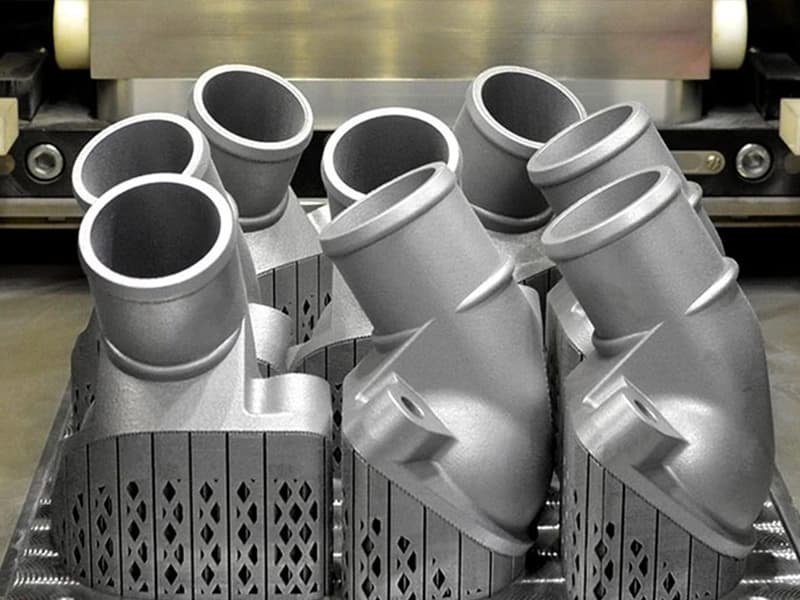
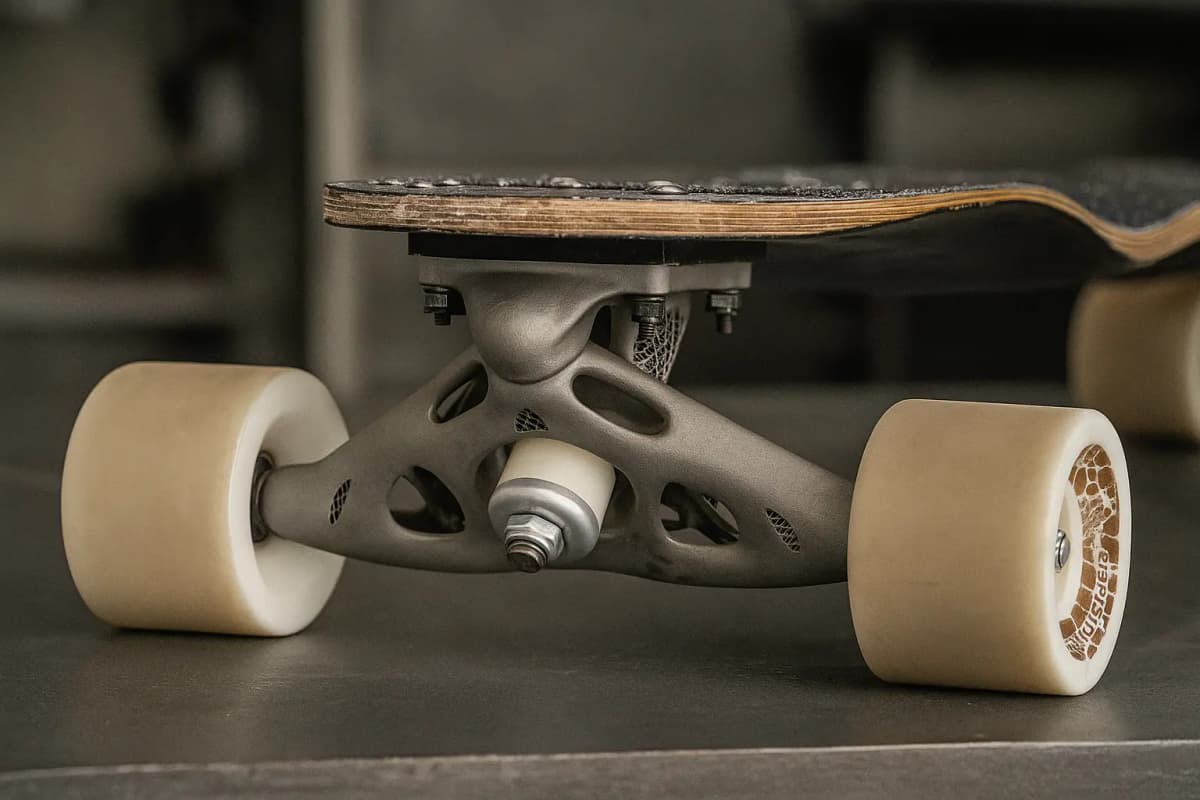
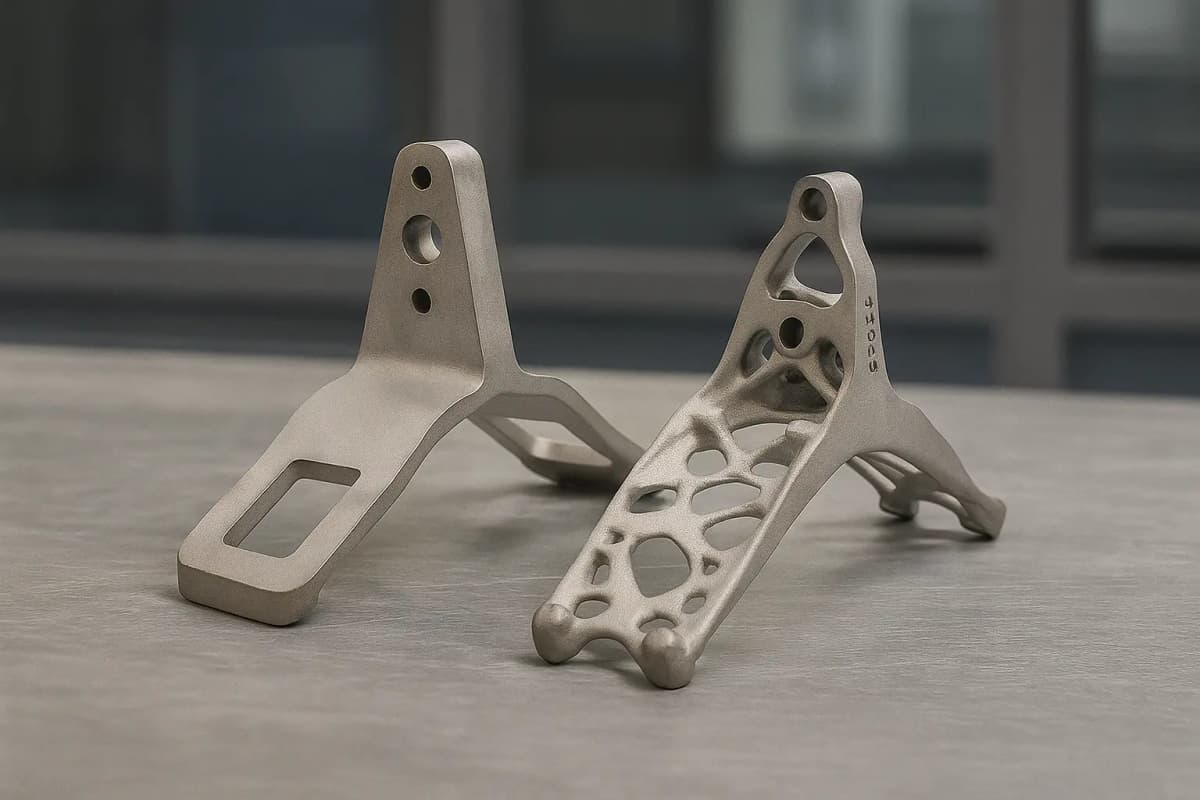
How DMLS 3D Printing Works
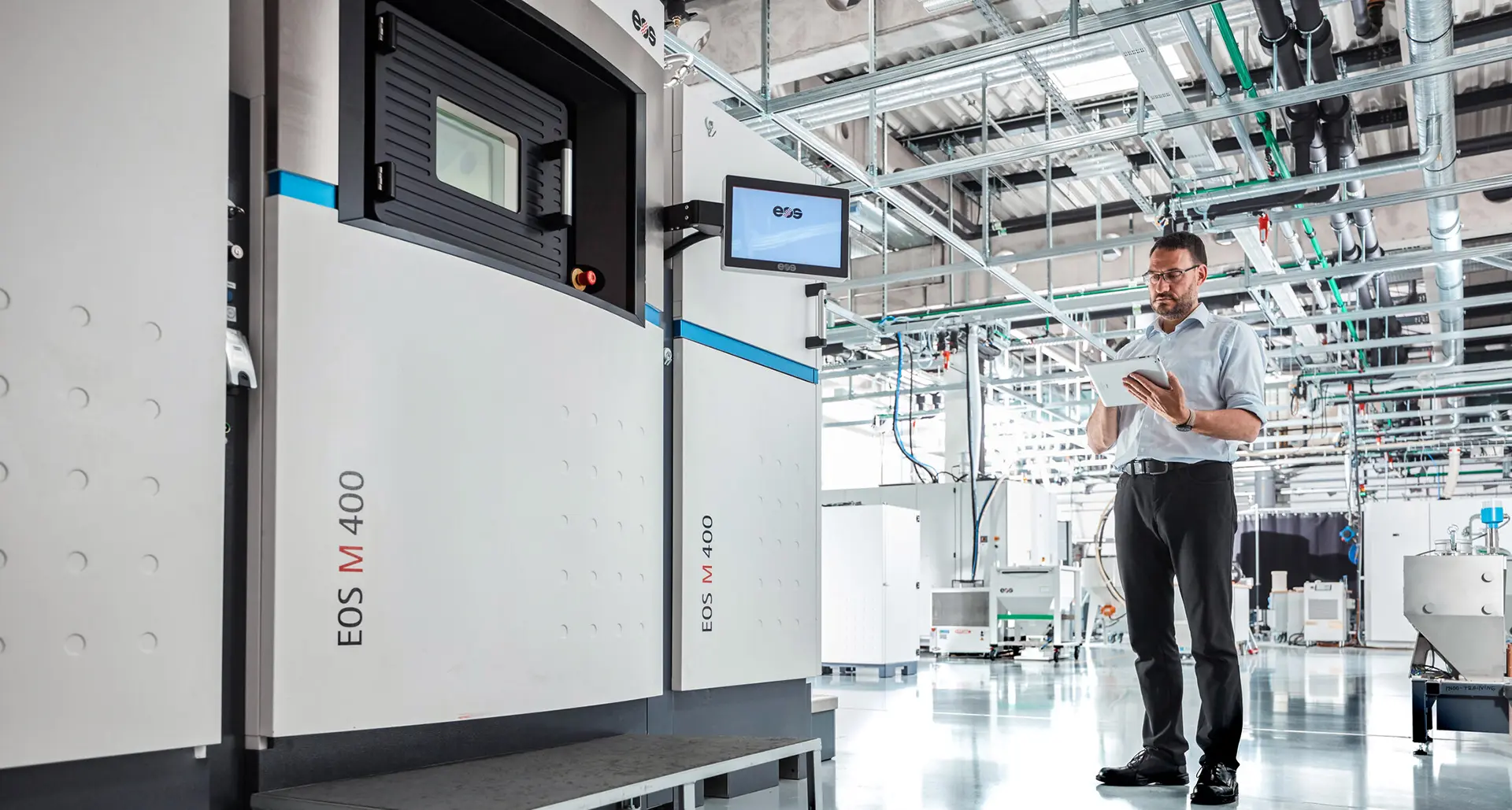
Powder Preparation
Fine metal powder is prepared and loaded into the machine. The build platform is preheated to optimal temperature to reduce thermal stress and improve part quality.
Step Specifications
Aerospace Grade Metal Alloys
Aerospace-grade metal powders including stainless steel, aluminum, and titanium alloys. Each material meets stringent industry standards for mechanical properties, offering exceptional strength-to-weight ratios and corrosion resistance for critical applications.
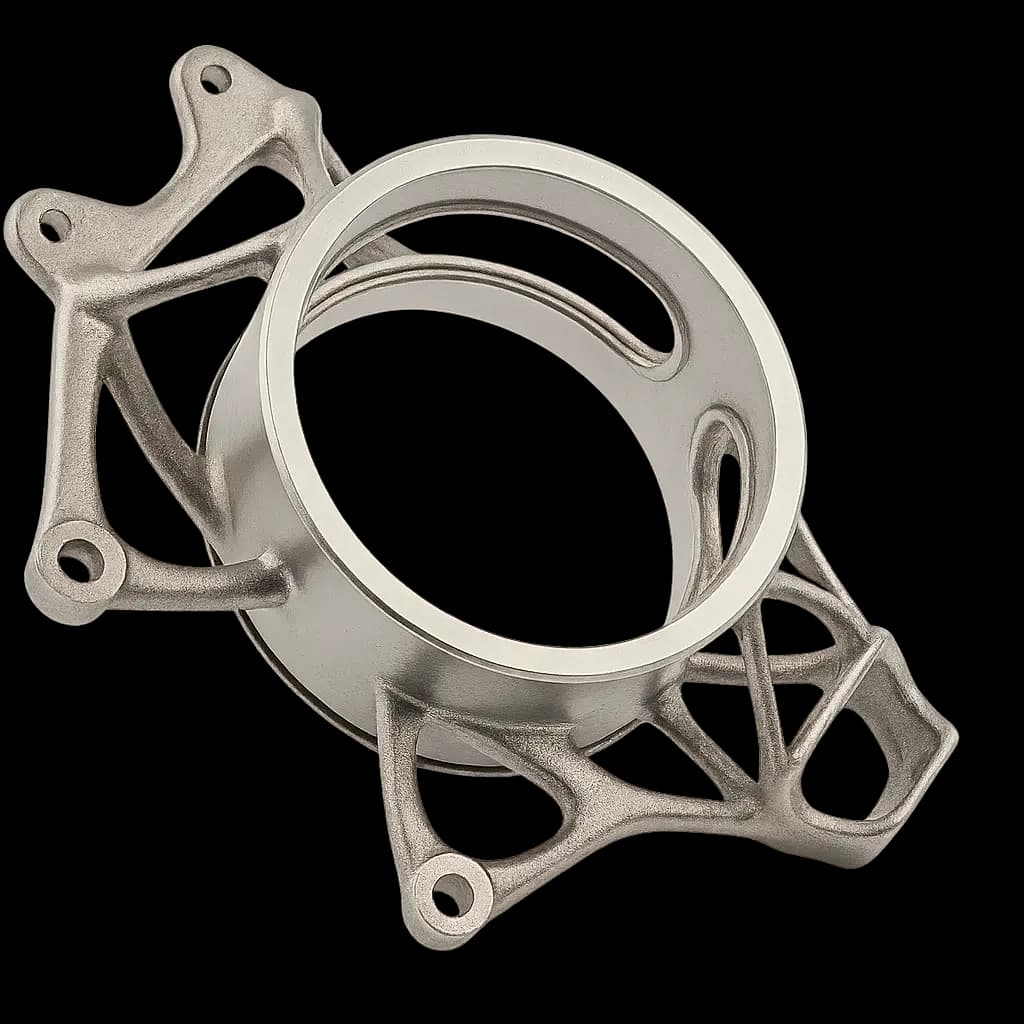
Aluminum AlSi10Mg
Engineering Grade Material
High-performance aluminum alloy known for its excellent strength-to-weight ratio, good thermal and electrical conductivity, and corrosion resistance.
Applications:
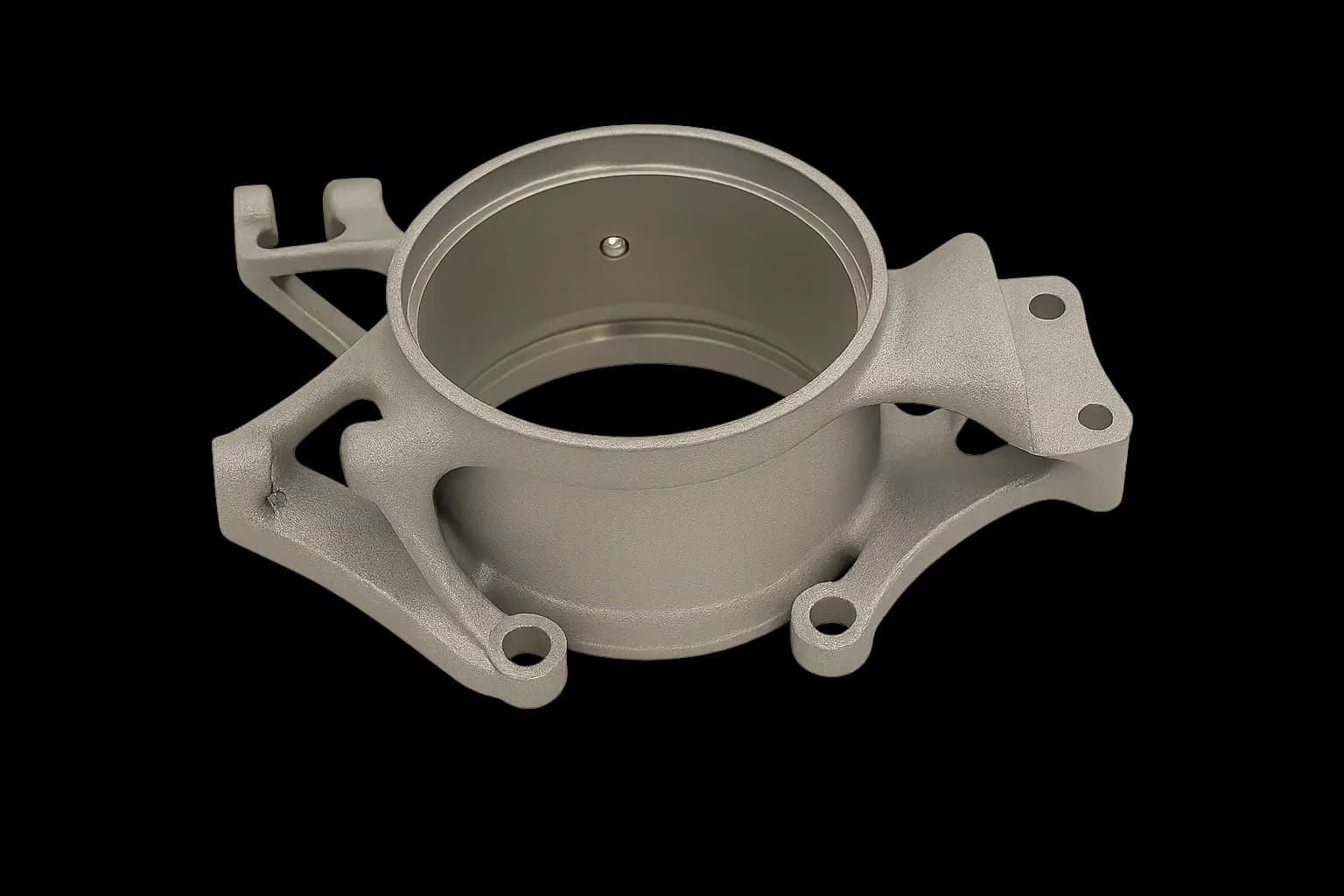
Aluminum 6061
Lightweight Aerospace Grade
Precipitation-hardened alloy known for its balanced strength, corrosion resistance, and excellent weldability with high strength-to-weight ratio.
Applications:
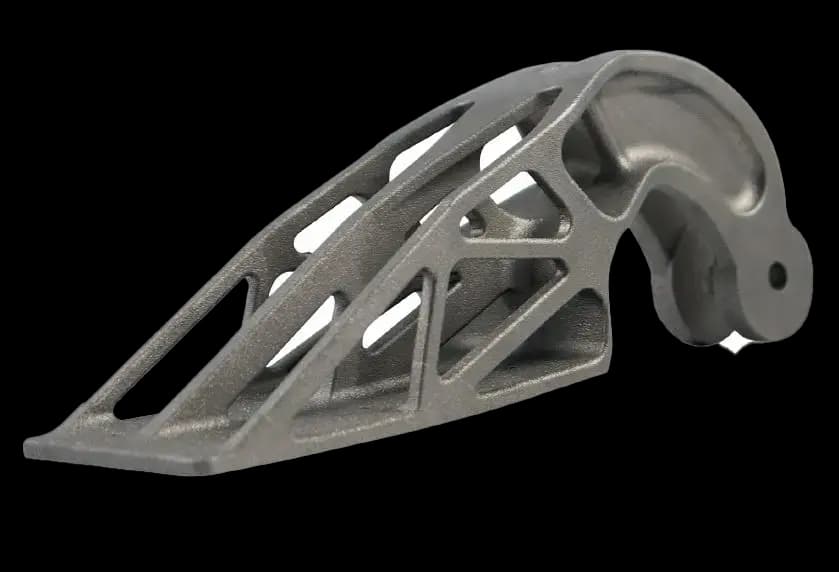
Stainless Steel 316L
Corrosion Resistant Stainless Steel
Low-carbon austenitic stainless steel renowned for its exceptional corrosion resistance, particularly in chloride-rich and chemically aggressive environments.
Applications:
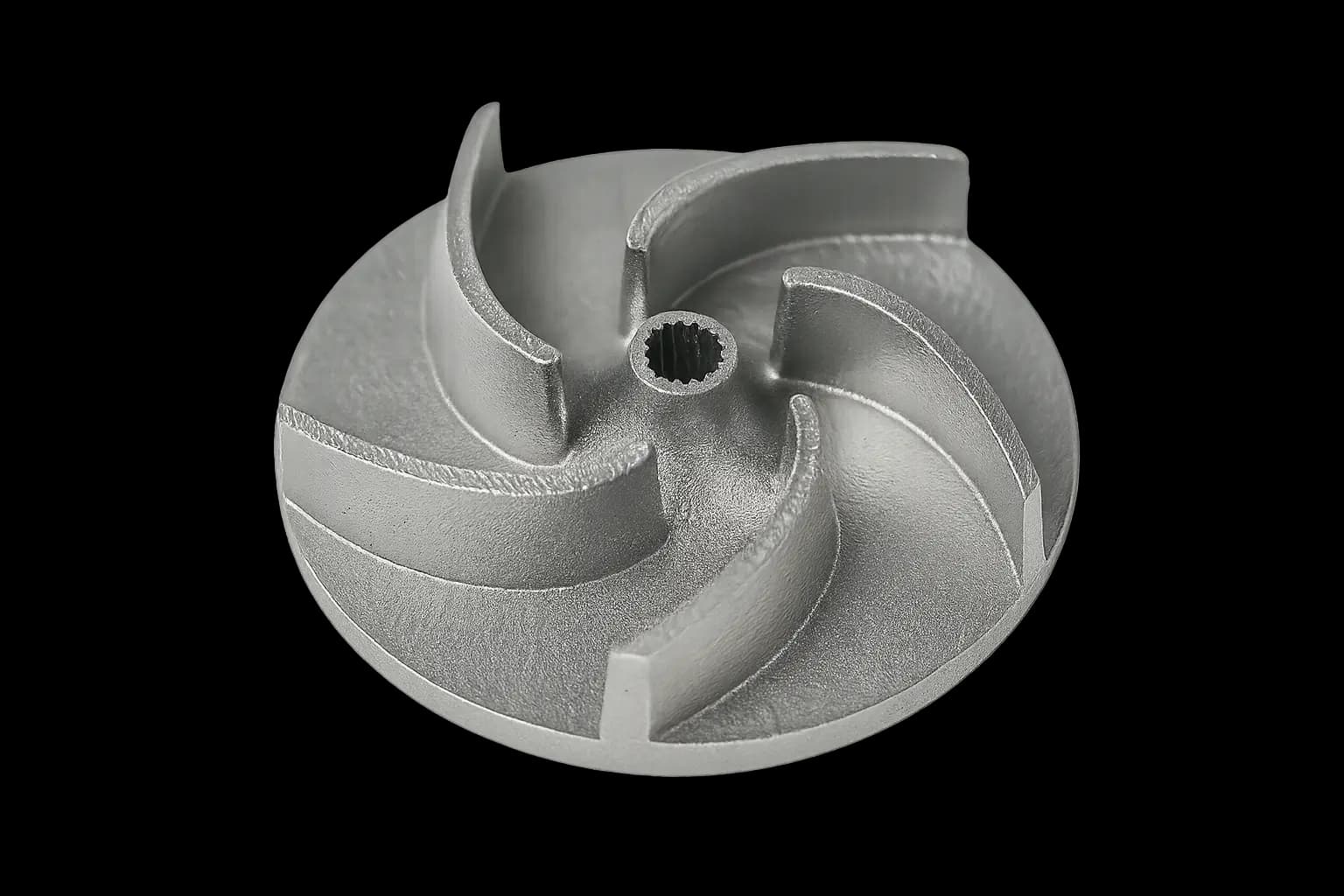
Stainless Steel 17-4 PH
Engineering Grade Material
Precipitation-hardening stainless steel renowned for its high strength, corrosion resistance, and excellent mechanical properties.
Applications:
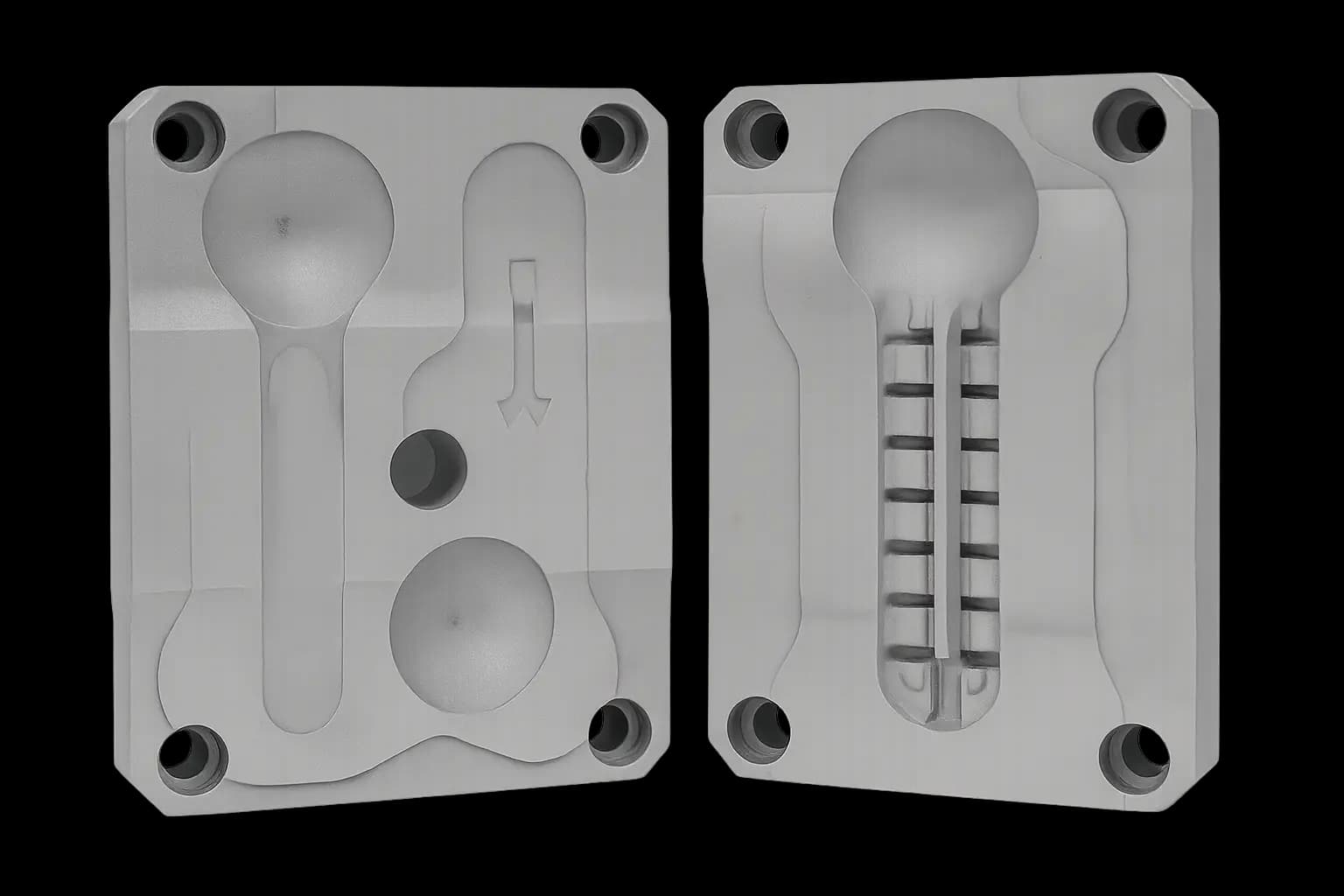
Maraging Steel
Engineering Grade Material
High-strength, low-carbon alloy steel known for its superior toughness, hardness, and excellent mechanical properties through age-hardening.
Applications:
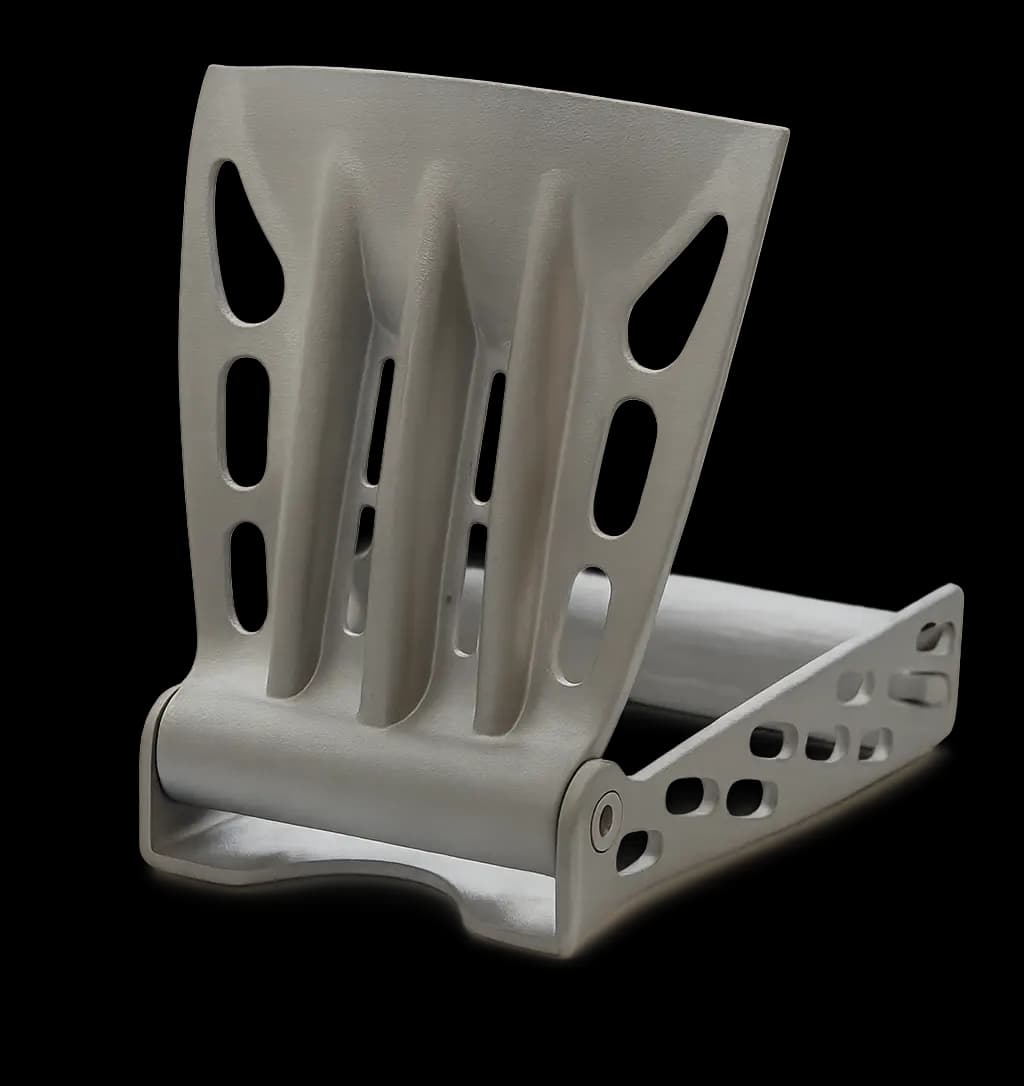
Titanium Ti64 (Ti-6Al-4V)
High Strength-to-Weight Ratio
High-strength, lightweight titanium alloy widely used in aerospace, medical, and high-performance engineering applications.
Applications:
Material Surface Finishes
DMLS parts generally exhibit a slightly rough, matte finish due to the laser sintering process, resulting in a uniform surface texture. While this natural finish is sufficient for many functional applications, Forge Labs offers several post-processing options to enhance aesthetics, accuracy, and performance.
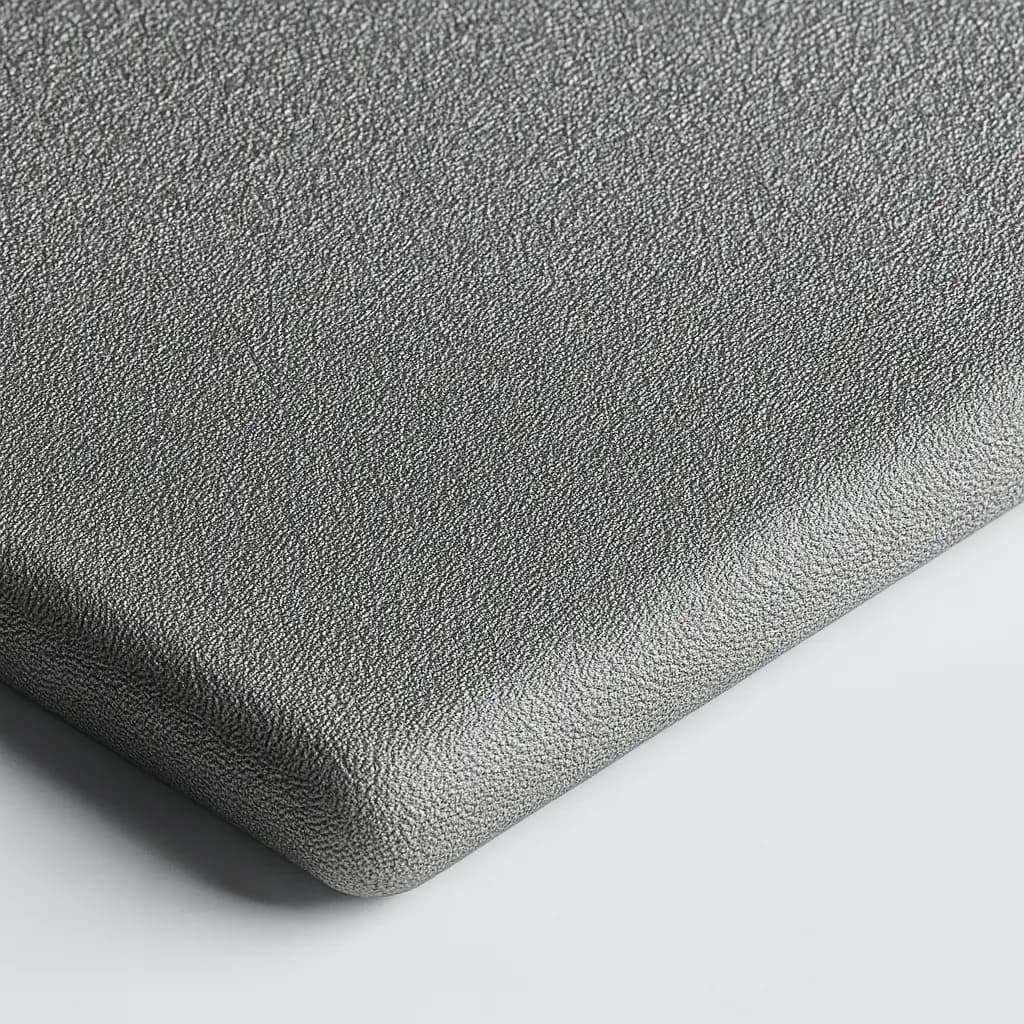
Standard Finish
Natural Grey
Support structures are carefully removed, and parts undergo shot peening to create a uniform, matte surface and help relieve residual stresses. Critical features may receive light machining for tighter tolerances.
Finish Attributes
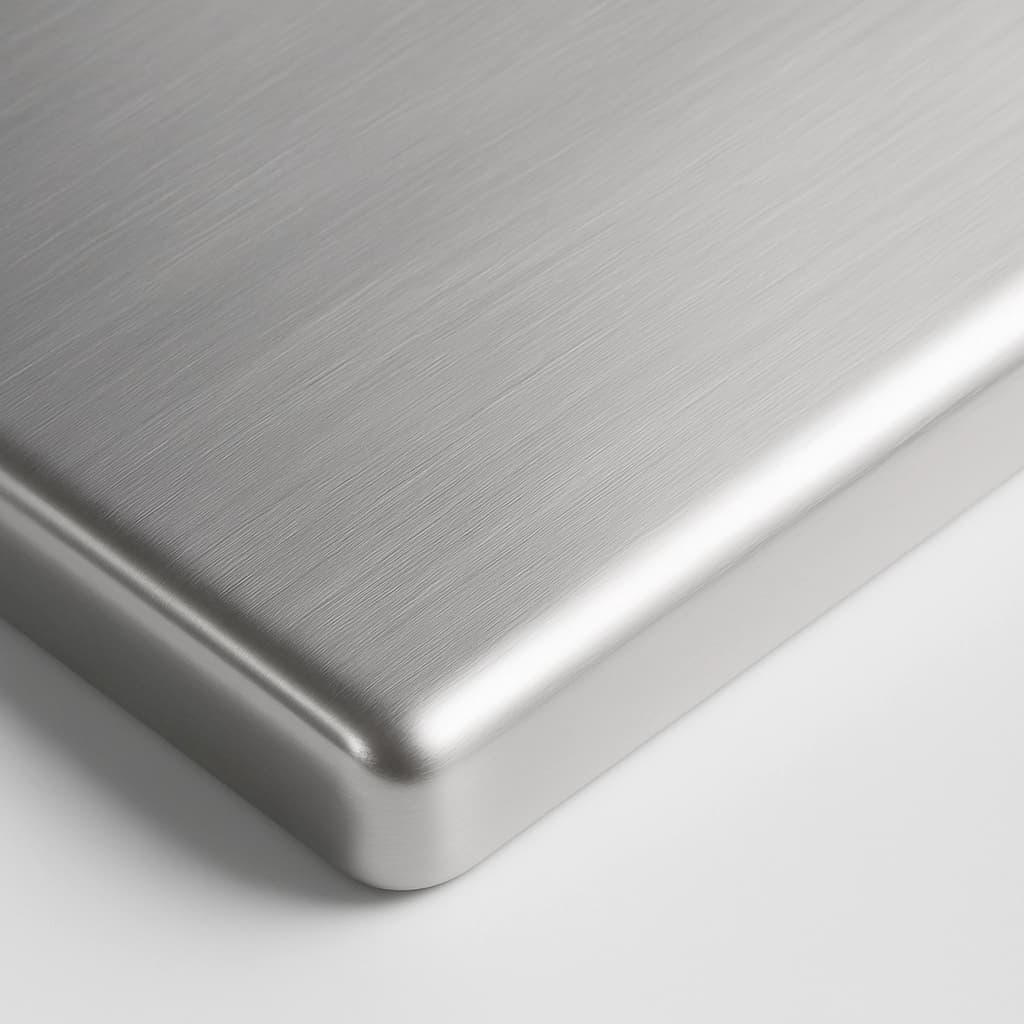
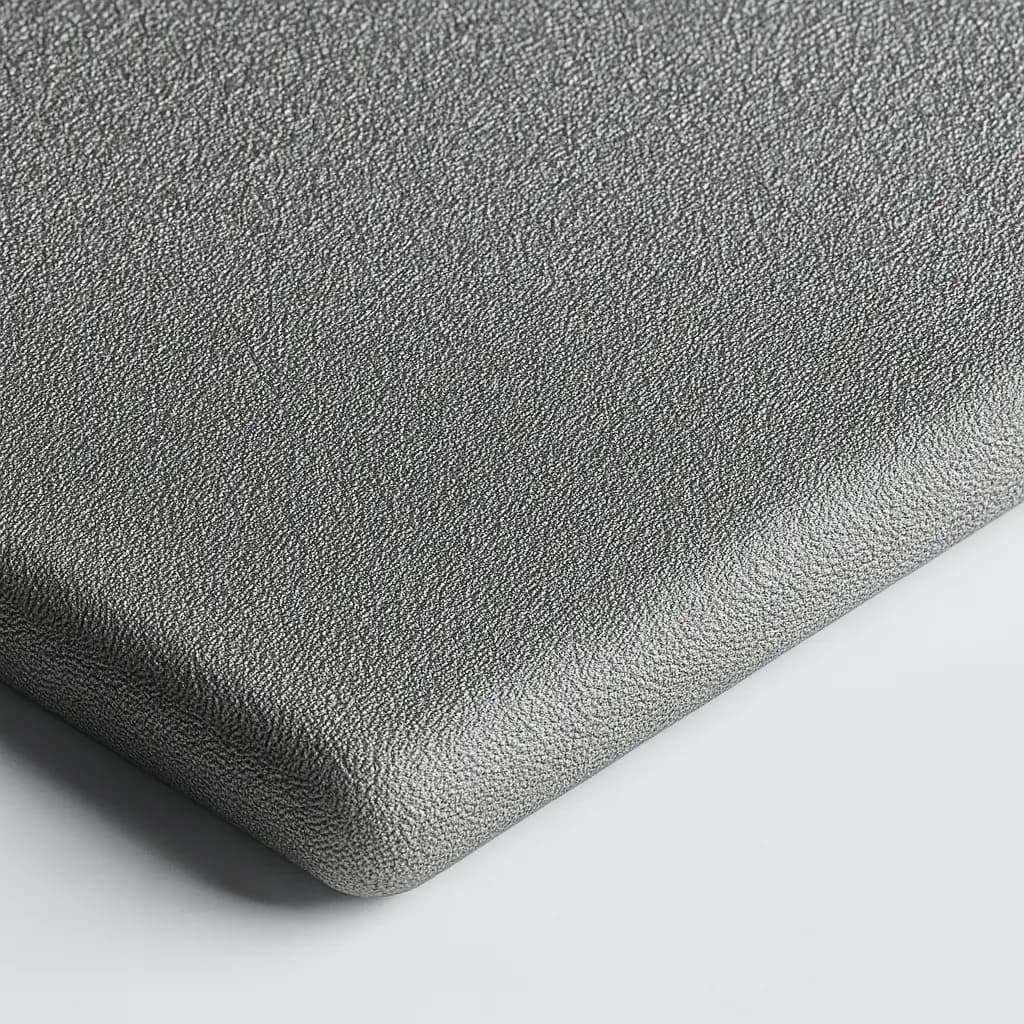
Machining & Polishing
Enhanced Finish
Precision machining and polishing processes enhance surface quality, achieving tighter tolerances and smoother finishes for critical applications.
Finish Attributes
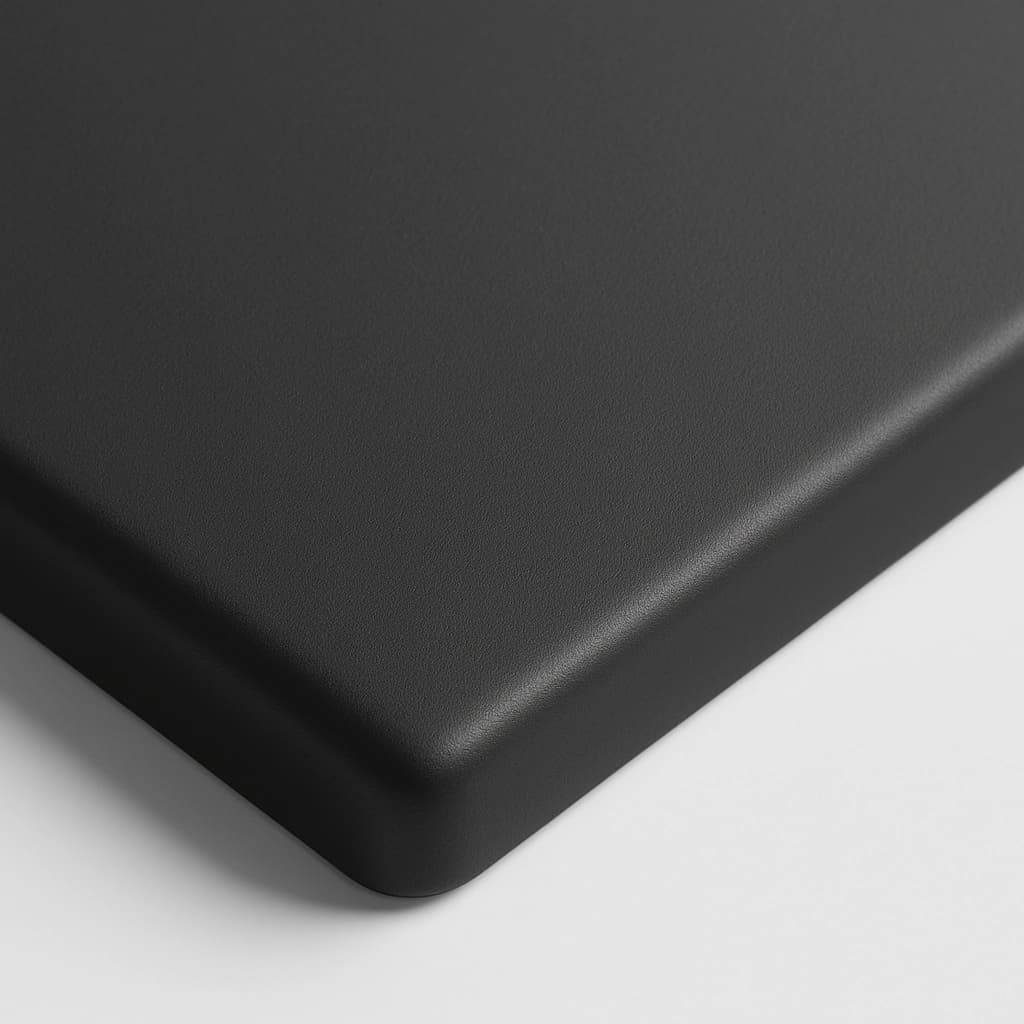
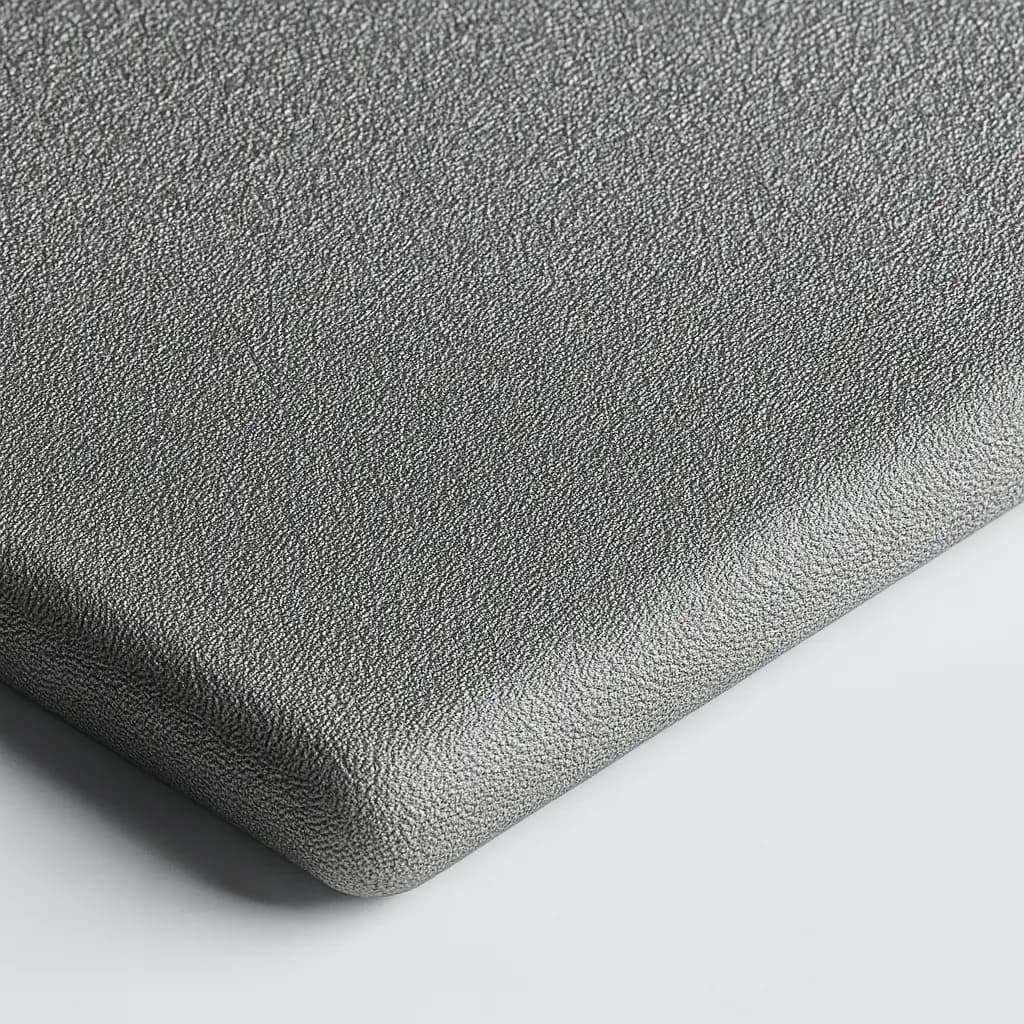
Anodizing
Anodized Finish
For aluminum parts, anodizing forms a protective oxide layer, significantly enhancing corrosion resistance and hardness while improving appearance.
Finish Attributes
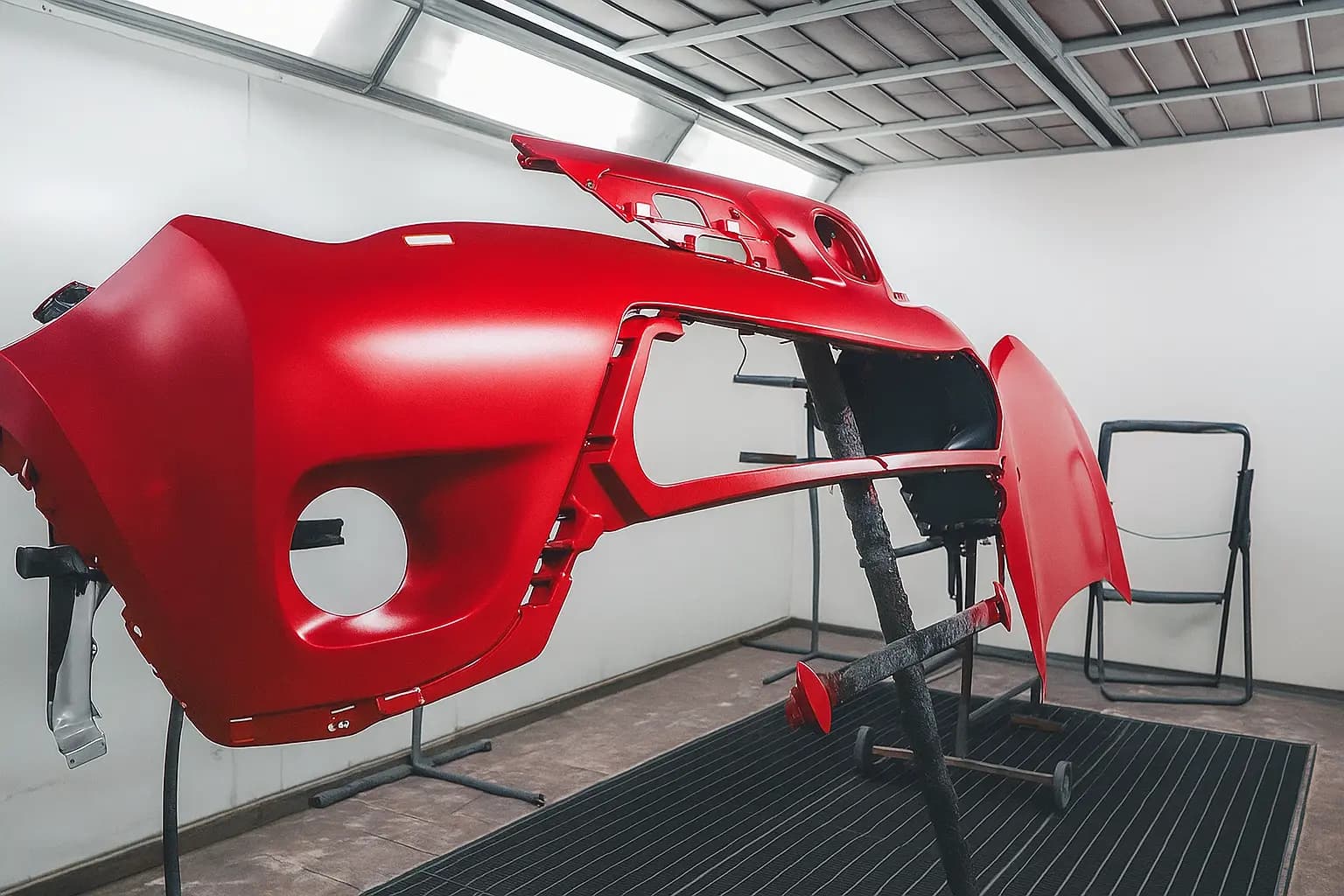
Performance Paint
Premium Finish
Automotive-grade coating that enhances aesthetics and durability. Each part is hand-finished with professional-grade equipment for exceptional adhesion and custom color matching.
Finish Attributes
Additional Manufacturing Services
Complete your DMLS parts with our precision post-processing services. From heat treatment and CNC machining to specialized surface finishes, we ensure your components meet the most demanding specifications for production-ready applications.
Heat Treatment
Stress relief and material property optimization
CNC Machining
Precision finishing for critical dimensions
Surface Finishing
Polishing, shot peening, and texture enhancement
Anodizing
Protective coating for aluminum components
Quality Inspection
Dimensional verification and material testing
Direct Metal Laser Sintering Design Guidelines
Essential design considerations to optimize your Direct Metal Laser Sintering parts for manufacturing success.
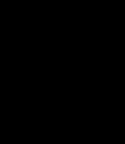
Maximum Build Volume
Varies by Material
Build volumes vary by material: Aluminum (AlSi10Mg) - 400mm x 300mm x 400mm (15.75" x 11.81" x 15.75"), Stainless Steel (316L) - 280mm x 280mm x 350mm (11.02" x 11.02" x 13.78"), Titanium (TC4) - 150mm x 150mm x 200mm (5.91" x 5.91" x 7.87").
Different materials have different optimal build chamber sizes for quality and cost efficiency.
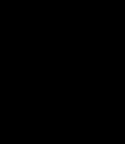
Tolerances
Best achievable tolerances
Best achievable tolerances - <100mm: ±0.2mm, <200mm: ±0.3mm, <300mm: ±0.4mm, 300-400mm: ±0.4-0.5mm. If your parts require specific tolerances, an engineering drawing must be provided when requesting a manual quote.
Parts designed with thin, flat planes will likely warp, so this should be avoided if tight tolerances are required. Polishing removes approximately 0.1mm of material.
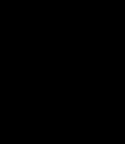
Layer Height
20 - 80 microns
Standard layer height varies by material. Fine layer heights provide better surface finish and detail resolution.
Thinner layers improve surface quality but increase build time and cost.
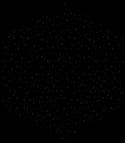
Surface Finish
Visible Layer Lines
Layer lines are visible on faces at a low angle relative to the build plate. Metal supports are removed, which may leave subtle marks in the surface of the part. Metal 3D printed parts are shot peened to a surface uniform roughness of 200 - 400 Ra after support removal.
Post-processing can significantly improve surface finish for critical applications.

Advantages of DMLS 3D Printing for Prototyping & Production
Metal 3D printing with Direct Metal Laser Sintering (DMLS) merges the freedom of additive manufacturing with the proven performance of machined metals, making it especially suitable for low-volume, complex assemblies that need quick turnaround times. By building parts layer by layer, DMLS allows for intricate geometries and consolidates multiple components into a single piece—reducing material waste, tooling costs, and production time.
- Fully Dense Metal Parts
- DMLS uses a high-powered laser to fuse metal powder into solid layers, producing fully dense components with mechanical properties comparable to—or surpassing—traditionally manufactured metals.
- Complex Geometries
- Being an additive process, intricate internal channels, undercuts, and organic shapes can be printed without the traditional constraints of subtractive machining.
- High Strength & Durability
- DMLS parts exhibit excellent mechanical properties and resistance to wear and fatigue, making them suitable for demanding aerospace, automotive, and industrial applications.
- Material Versatility
- A variety of industrial-grade alloys—including stainless steels, aluminum, titanium, and superalloys—enable a broad range of functional end-use components.
- Reduced Material Waste
- Only the powder required for each build layer is fused, and unfused powder can often be recycled, minimizing raw material waste compared to traditional metal fabrication.
- Faster Iterations
- Building parts directly from CAD data shortens lead times, allowing for rapid prototyping and design refinements without expensive tooling.
- Consolidated Assemblies
- DMLS allows multiple components to be combined into a single print, reducing part count, assembly steps, and potential points of failure.
Instant Quote Tool
From Upload to Delivery
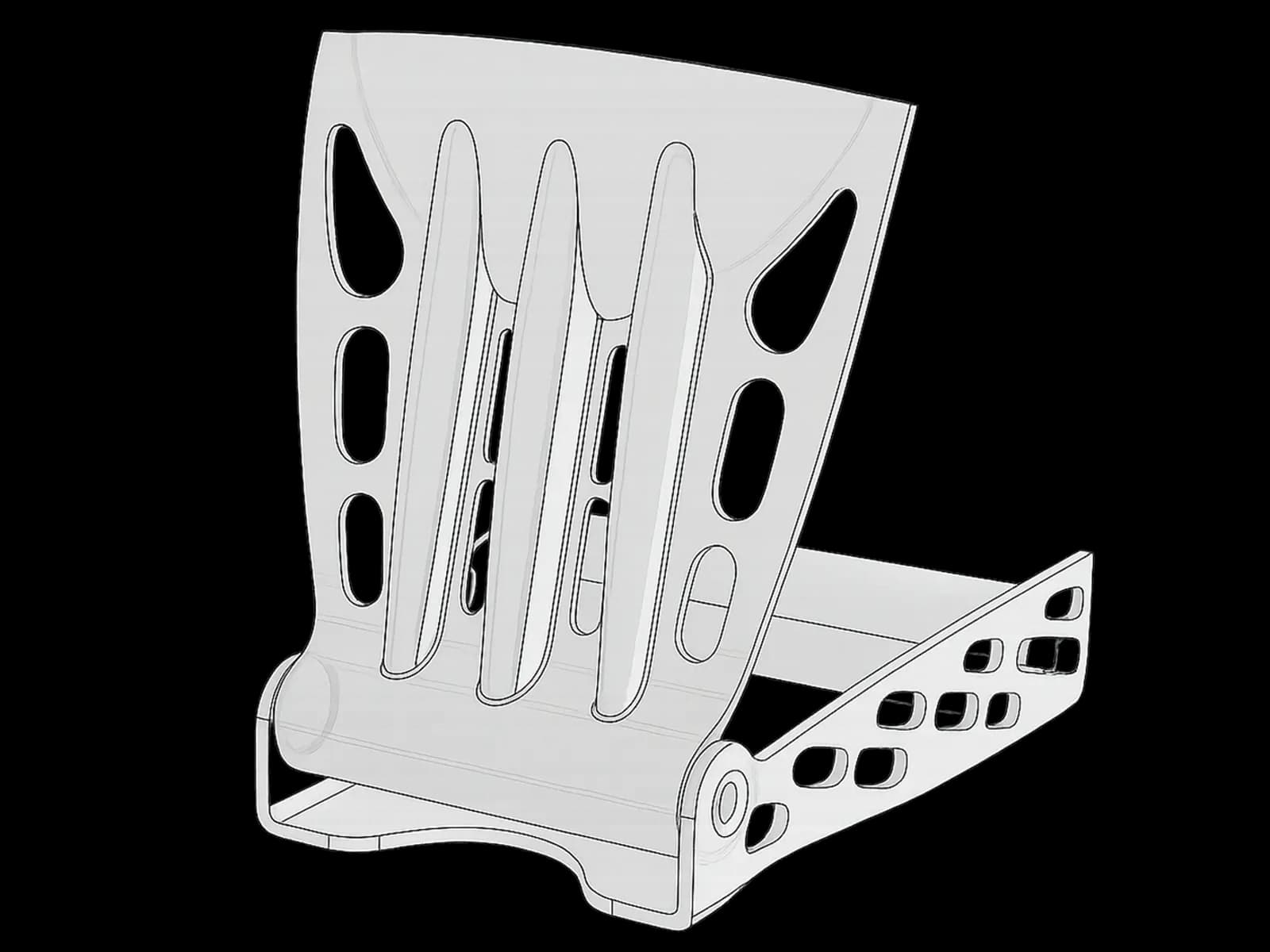
75% complete
Simple File Upload Process
Drag and drop your 3D files or browse to upload. Our system automatically analyzes your designs and provides instant feedback on printability and optimization suggestions.
- Drag & drop multiple file formats
- Automatic design analysis
- Printability feedback
- File optimization suggestions
DMLS Applications Across Industries
Discover how Direct Metal Laser Sintering is transforming manufacturing across industries with innovative solutions and enhanced capabilities.
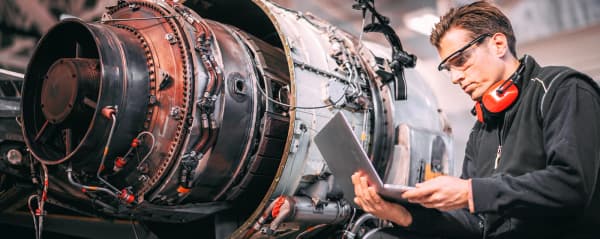
Aerospace Components
Lightweight, high-strength parts for aircraft and spacecraft including brackets, housings, and structural components with complex internal geometries.
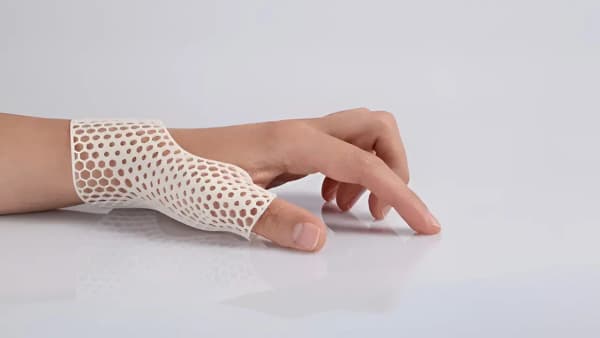
Medical Devices
Patient-specific implants, surgical instruments, and medical device housings requiring biocompatible materials and precise geometries.
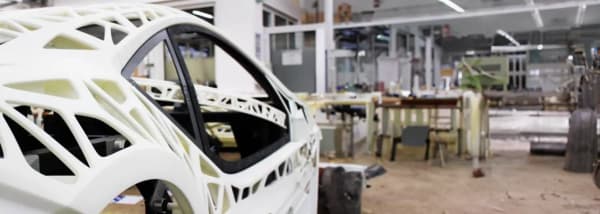
Automotive Applications
High-performance automotive components including lightweight brackets, heat exchangers, and specialized tooling for racing and production applications.
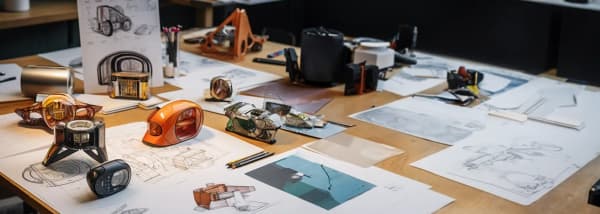
Industrial Manufacturing
Custom tooling, fixtures, and end-use industrial components requiring high strength, precision, and complex geometries impossible with traditional manufacturing.
Success Stories
Real results from our DMLS manufacturing partnerships
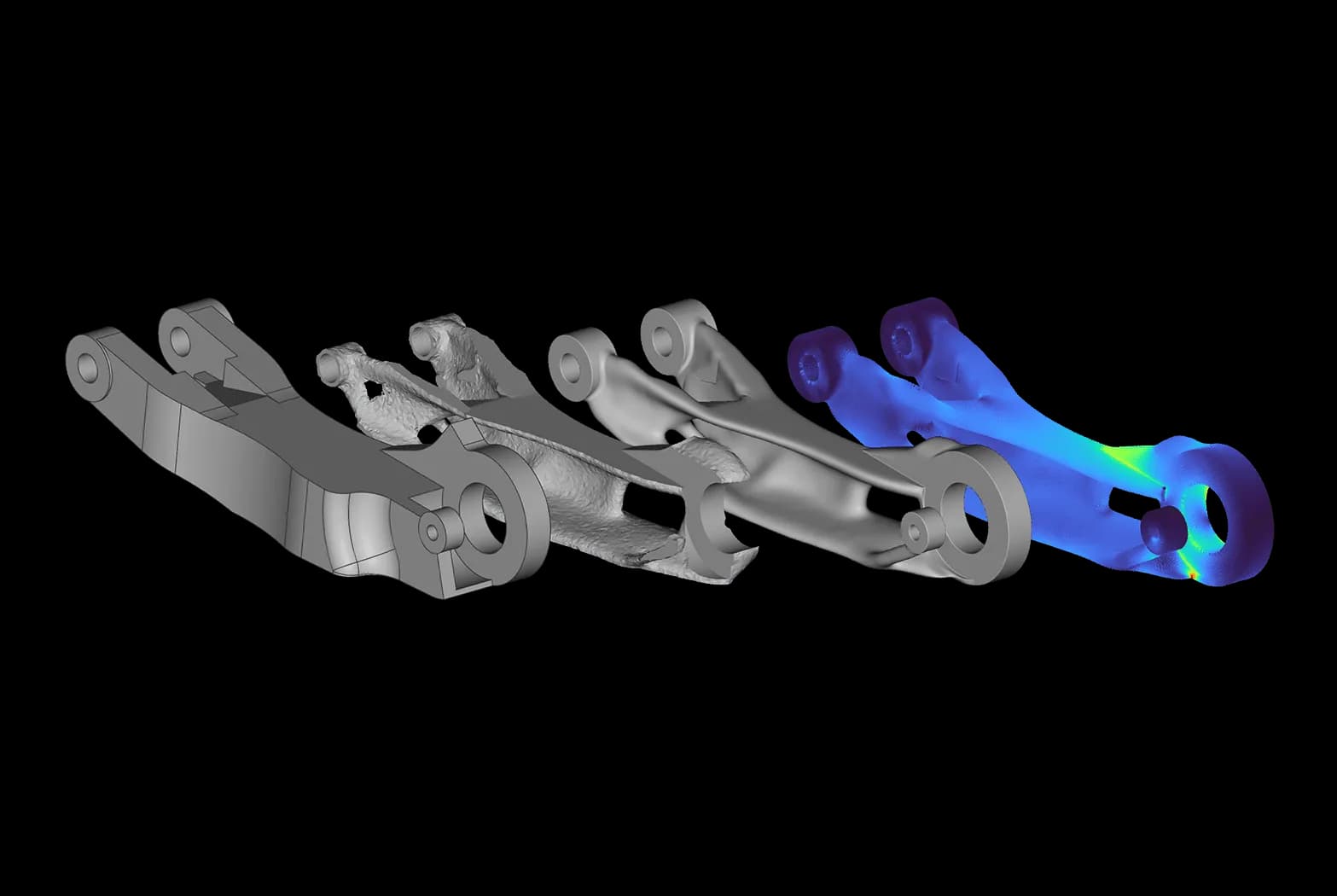
Aerospace Bracket Optimization
Lightweight aerospace bracket design optimization using topology optimization and DMLS manufacturing for 40% weight reduction while maintaining structural integrity.
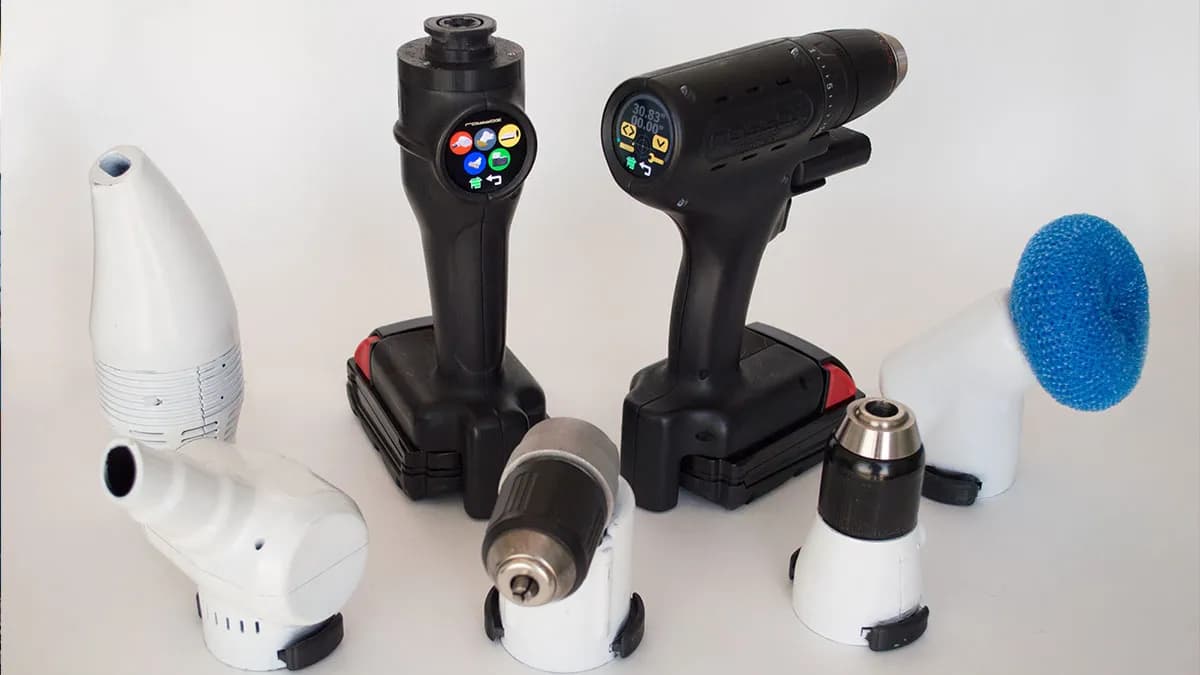
High-Performance Robotics Components
Custom aluminum and stainless steel robotics components with integrated cooling channels and complex internal geometries impossible with traditional manufacturing
Ready to manufacture your parts?
Upload your CAD files to get instant quotes for DMLS 3D printing. Professional-grade manufacturing with fast turnaround times.
Click to start your quote
STL, STEP, OBJ, 3MF supported • Get instant pricing
DMLS Questions & Answers
Common questions about DMLS 3D printing technology. Can't find what you're looking for? Reach out to our technical team.