Design Guidelines
Master the art of designing for additive manufacturing. Our comprehensive design guidelines ensure your parts are optimized for quality, cost-effectiveness, and manufacturability across all 3D printing technologies.
Design for Additive Manufacturing (DfAM)
Each 3D printing technology has unique capabilities and constraints. Our design guidelines help you optimize your parts for the best quality, performance, and cost-effectiveness across all manufacturing processes.
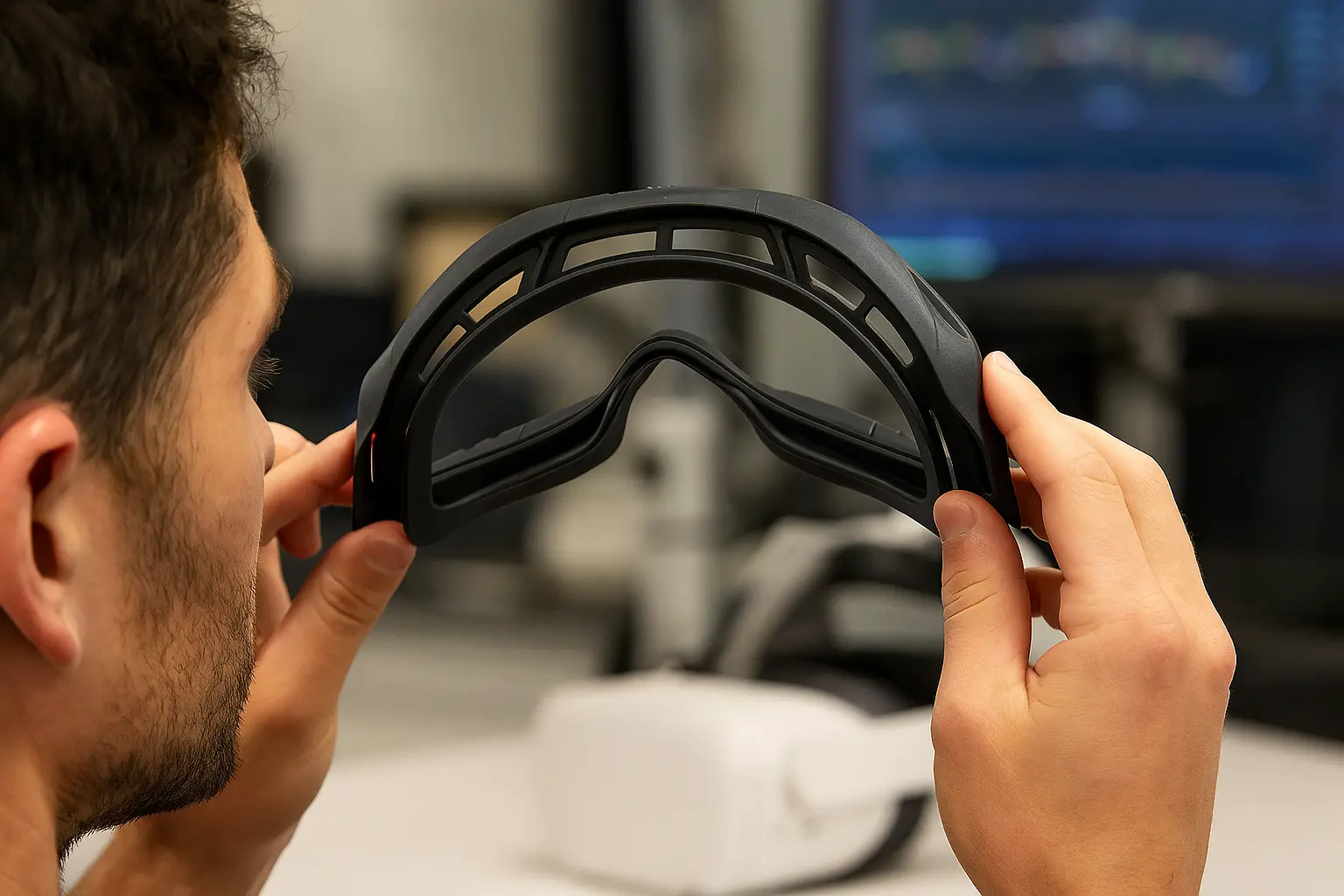
Selective Laser Sintering
Design Guidelines
Best practices for designing parts optimized for Selective Laser Sintering covering all critical manufacturing requirements.
Build Volume
340 × 340 × 600 mm (13.4 × 13.4 × 23.6 in)
Layer Height
60 - 120 microns (0.06 - 0.12 mm)
Tolerance
±0.25%, Lower limit of ±0.25 mm
Min. Wall
0.8 - 1.0 mm
Key Design Considerations
Design parts with self-supporting geometries when possible
Consider powder escape holes for hollow parts
Maintain consistent wall thickness to avoid warping
+1 more guidelines
Material Category
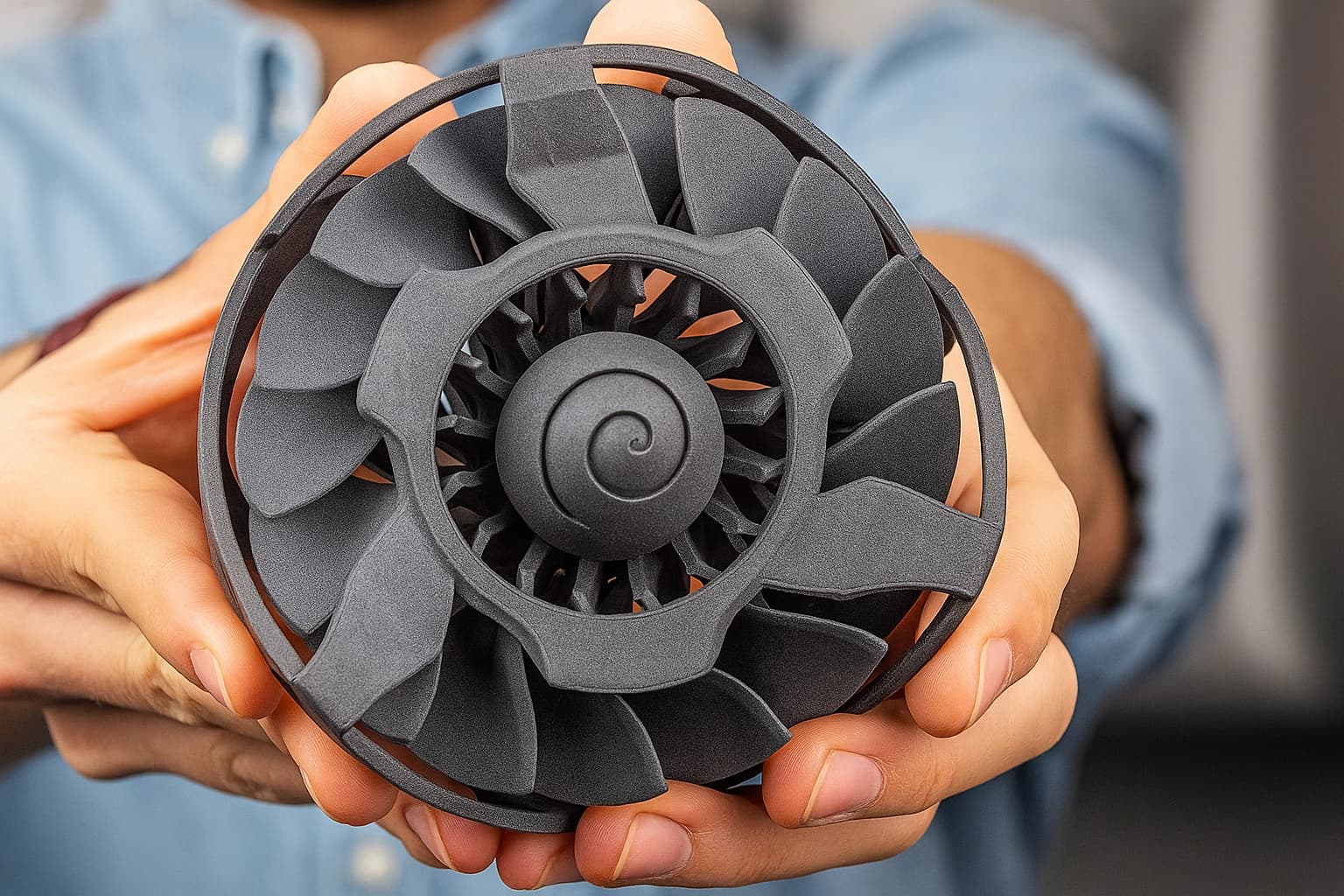
Multi-Jet Fusion
Design Guidelines
Best practices for designing parts optimized for Multi-Jet Fusion covering all critical manufacturing requirements.
Build Volume
380 × 284 × 380 mm (15 × 11.2 × 15 in)
Layer Height
100 microns (0.10 mm)
Tolerance
±0.3%, Lower limit of ±0.5 mm
Min. Wall
1.0 mm
Key Design Considerations
Optimize part nesting for high-density builds and cost efficiency
Consider powder escape holes for hollow parts
Design with consistent wall thickness to minimize warping
+1 more guidelines
Material Category
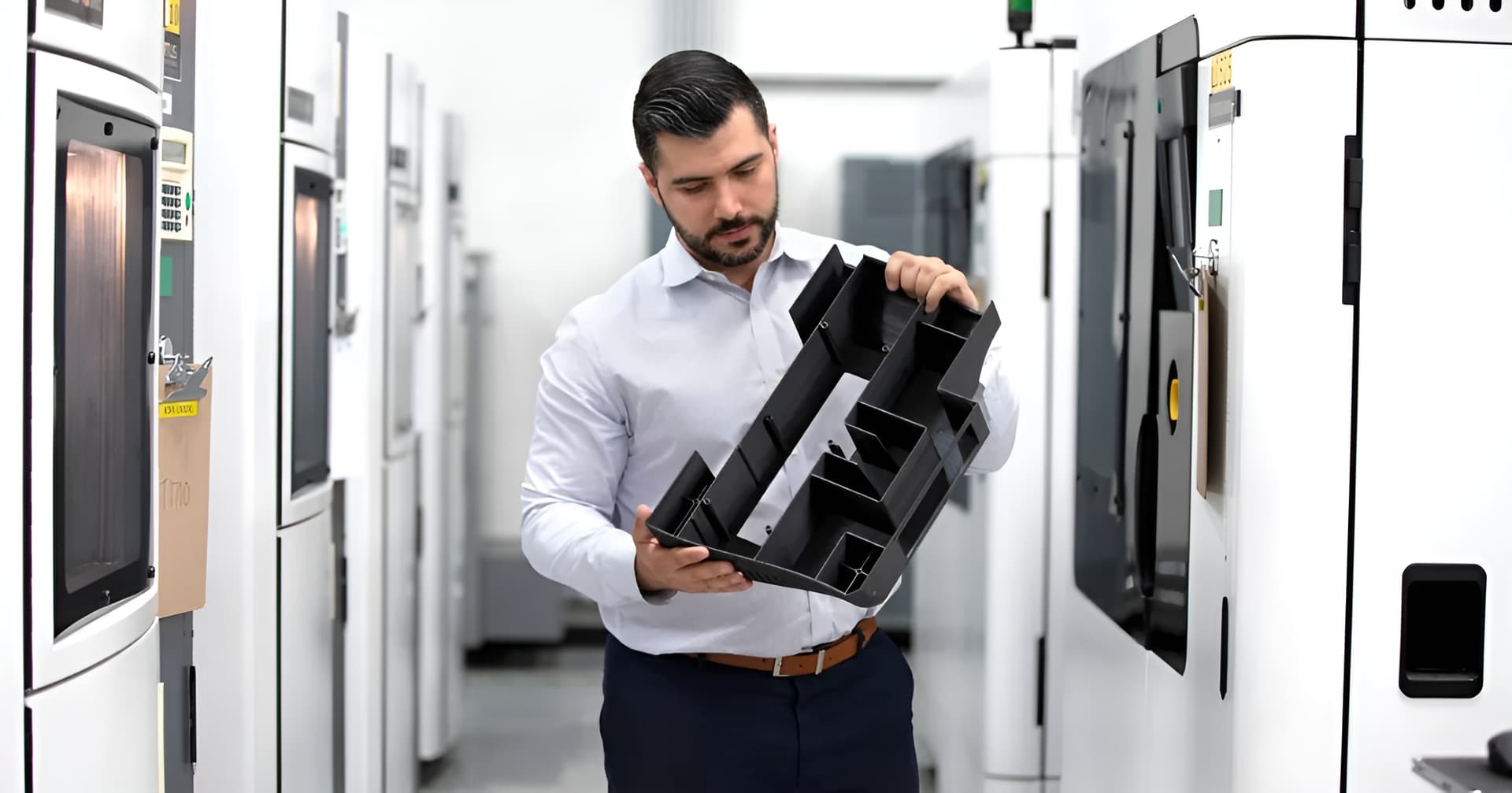
Fused Deposition Modeling
Design Guidelines
Best practices for designing parts optimized for Fused Deposition Modeling covering all critical manufacturing requirements.
Build Volume
914 × 609 × 914 mm (36" × 24" × 36")
Layer Height
127 - 330 microns (0.127 - 0.33 mm)
Tolerance
±0.25 - ±0.762 mm
Min. Wall
1.0 mm
Key Design Considerations
Design with print orientation in mind to minimize supports
Consider anisotropic material properties
Account for thermal contraction during cooling
+2 more guidelines
Material Category

Stereolithography
Design Guidelines
Best practices for designing parts optimized for Stereolithography covering all critical manufacturing requirements.
Build Volume
380 × 284 × 380 mm (15 × 11.2 × 15 in)
Layer Height
50 - 100 microns (0.05 - 0.10 mm)
Tolerance
±0.25%, Lower limit of ±0.25 mm
Min. Wall
0.8 mm
Key Design Considerations
Design supports for optimal removal
Consider resin drainage for hollow parts
Account for UV curing requirements
+1 more guidelines
Material Category
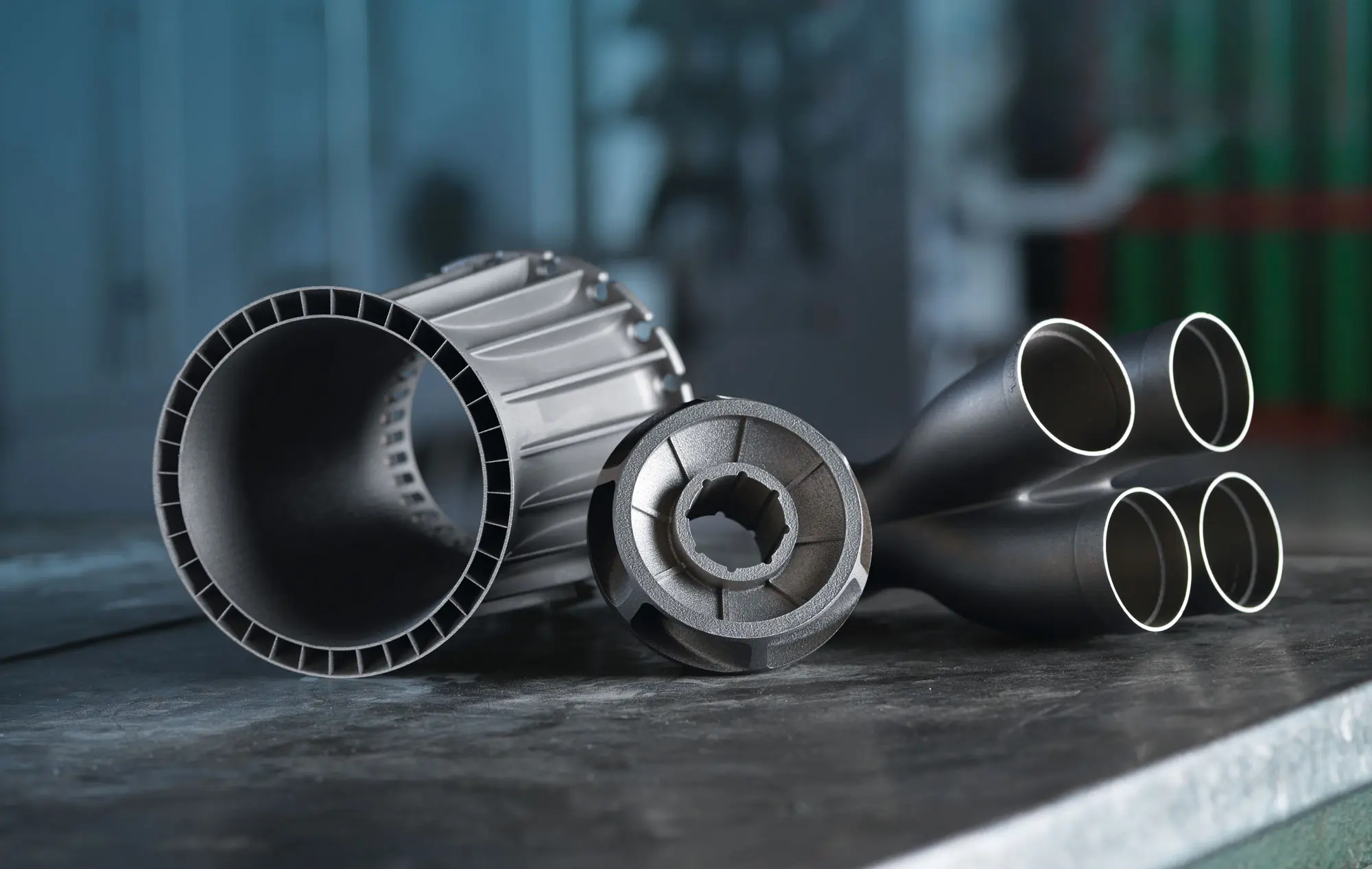
Direct Metal Laser Sintering
Design Guidelines
Best practices for designing parts optimized for Direct Metal Laser Sintering covering all critical manufacturing requirements.
Build Volume
380 × 284 × 380 mm (15 × 11.2 × 15 in)
Layer Height
20 - 80 microns (0.02 - 0.08 mm)
Tolerance
±0.2 - ±0.5 mm
Min. Wall
1.0 mm
Key Design Considerations
Design for minimal supports to reduce post-processing
Consider heat dissipation requirements during printing
Account for thermal stress and potential distortion
+3 more guidelines
Material Category
What Our Guidelines Cover
Each technology guide provides comprehensive information to help you design parts that are manufacturable, cost-effective, and high-quality.
Design Fundamentals
Critical specifications including wall thickness, tolerances, clearances, and feature sizes for optimal part quality.
- • Minimum wall thickness
- • Dimensional tolerances
- • Feature size limitations
- • Build volume constraints
Material Considerations
Material-specific design requirements and behaviors to ensure optimal mechanical properties and surface finish.
- • Material shrinkage factors
- • Support requirements
- • Surface finish expectations
- • Post-processing options
Manufacturing Optimization
Best practices for part orientation, cost optimization, and design efficiency for additive manufacturing.
- • Optimal part orientation
- • Cost reduction strategies
- • Assembly considerations
- • Quality improvement tips
Ready to Design Your Next Part?
Use our design guidelines to create parts optimized for additive manufacturing, or let our engineers review your design for manufacturability.