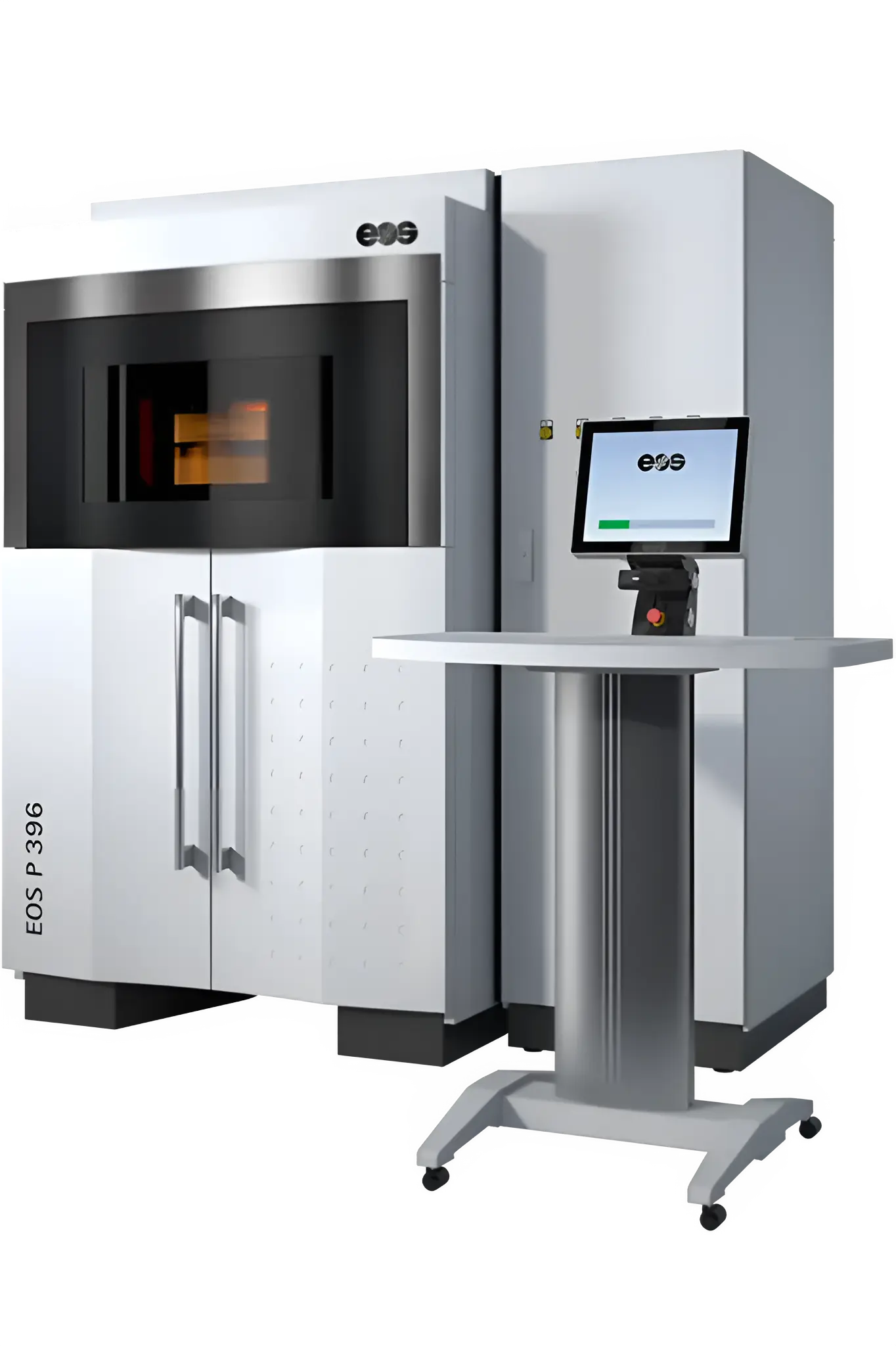
Selective Laser Sintering3D Printing for Complex Geometries & Functional Parts
Support-free manufacturing of complex geometries using engineering-grade material materials. SLS uses a high-powered laser to sinter nylon powder, creating strong, functional parts.
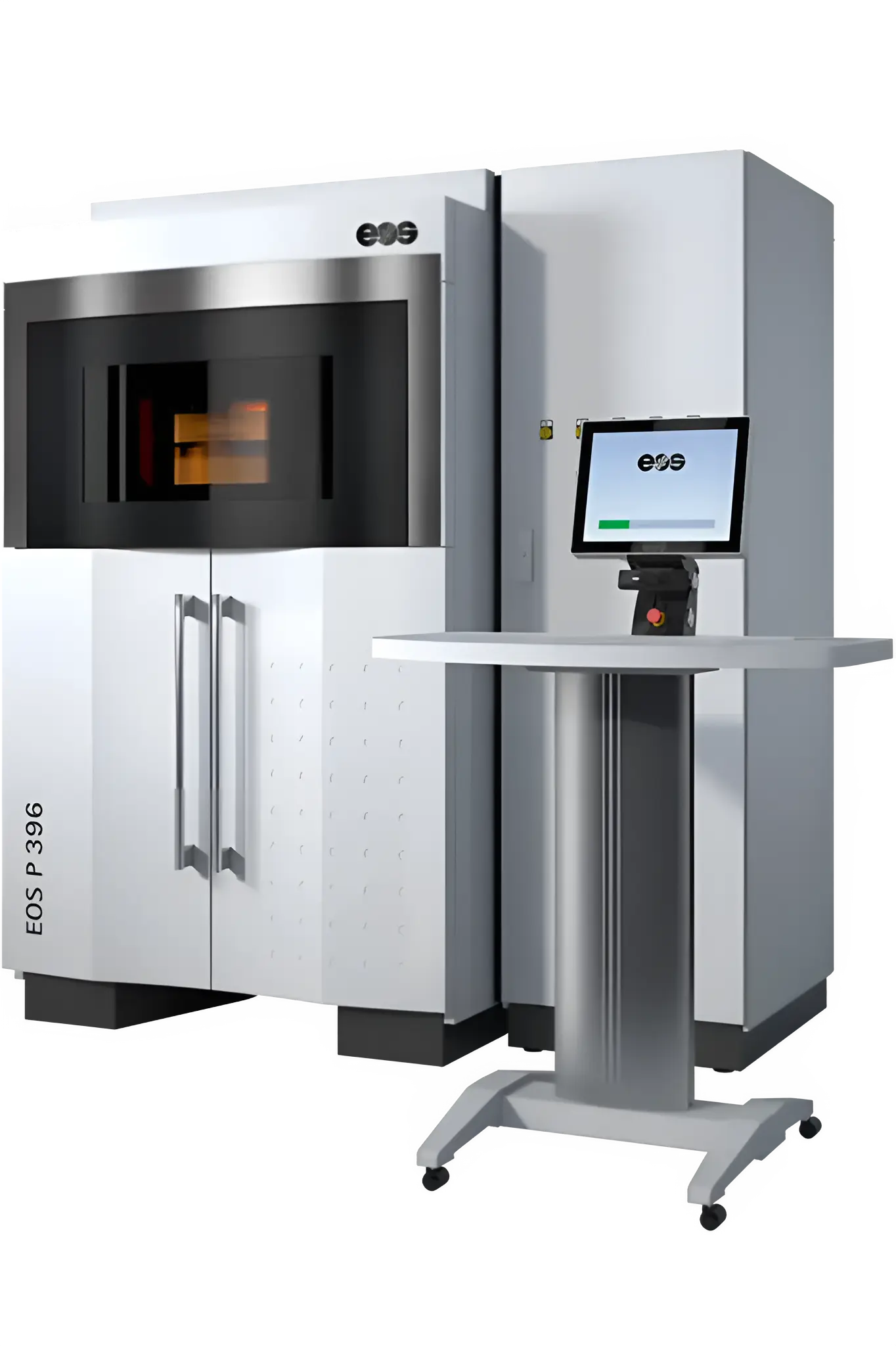
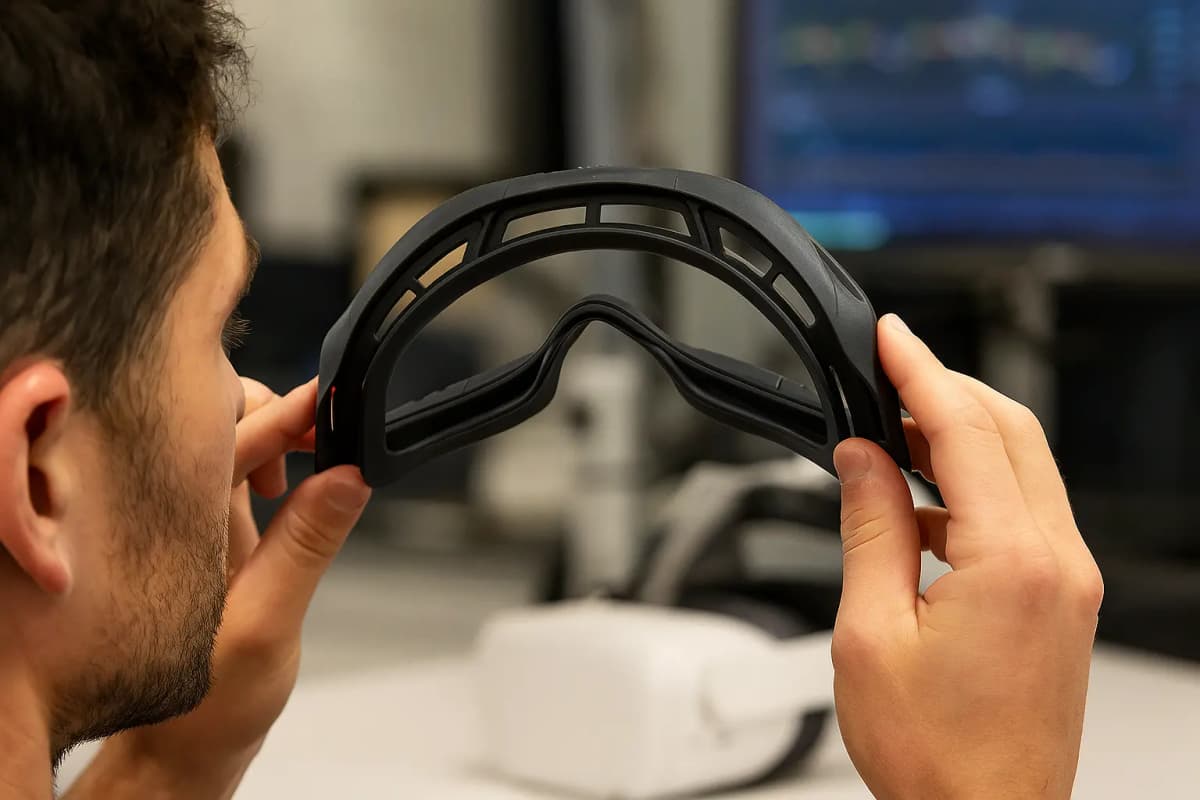
Technology Overview
High Performance End Use Parts at Scale
Selective Laser Sintering (SLS) is a high performance industrial 3D printing technology that eliminates the need for support structures while delivering exceptional strength and complex geometries. Perfect for functional prototypes and end-use parts requiring intricate internal features that traditional manufacturing cannot achieve.
Advanced manufacturing capabilities enable complex geometries, functional prototypes, and end-use production parts that would be impossible or cost-prohibitive with traditional manufacturing methods. From functional prototypes to end-use production parts, this technology delivers exceptional performance across demanding industries.
Engineering Applications
Durable Engineering Components
Widely used in aerospace, automotive, medical, and consumer products, SLS is ideal for durable, high-performance components with consistent mechanical properties. It supports ESD-safe, temperature-resistant, and USP Class VI biocompatible materials, making it well-suited for engineering and industrial applications. Compared to injection molding, SLS is a cost-effective solution for functional prototypes and low-to-mid-volume production — with fast turnaround times and no need for support structures.
3D Printed For The Real World
From automotive brackets to medical devices, SLS technology enables complex geometries without support structures, reducing post-processing time and cost. The powder-bed fusion process creates isotropic mechanical properties, ensuring consistent performance across all orientations while maintaining tight tolerances and excellent surface finish.
Key Advantages
Complex Geometries: Intricate internal channels, overhangs, and assemblies impossible with traditional manufacturing.
Functional Prototypes: Test mechanical properties and fit before investing in production tooling.
Custom Tooling: Jigs, fixtures, and manufacturing aids tailored to specific production requirements.
End-Use Parts: Production components for aerospace, medical, automotive, and industrial applications.
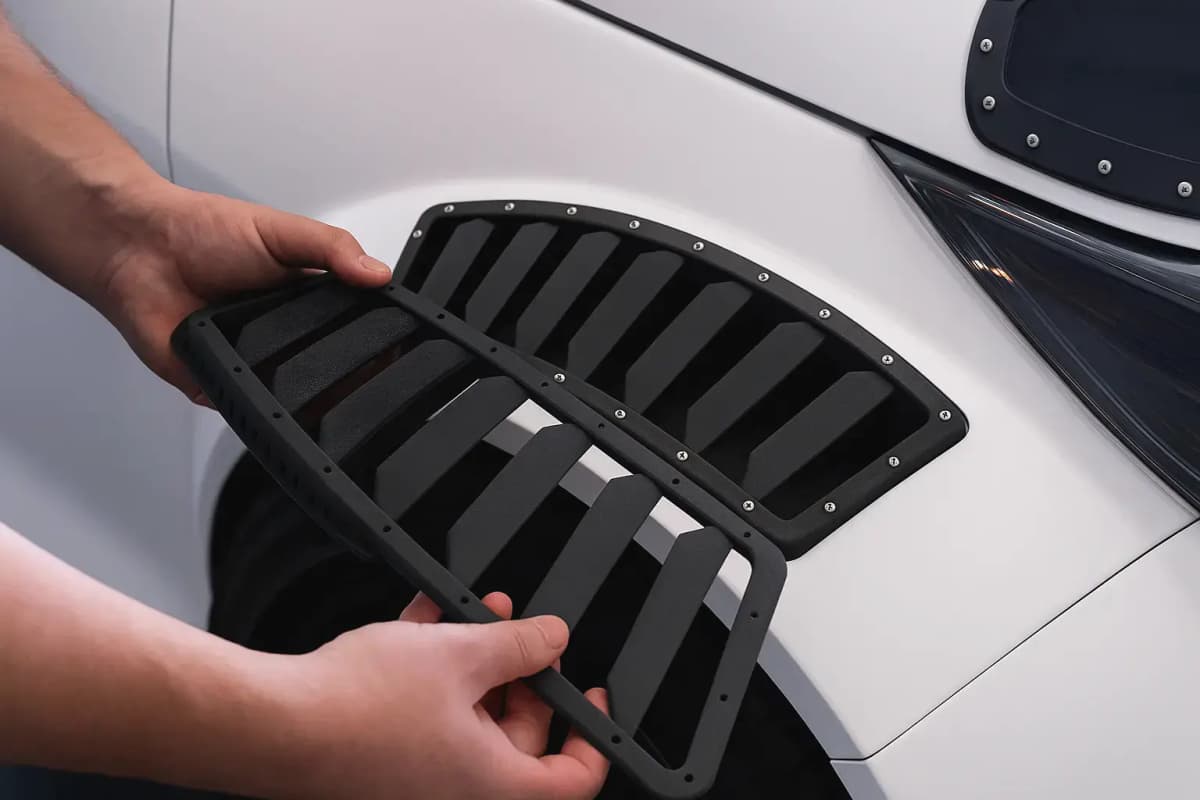
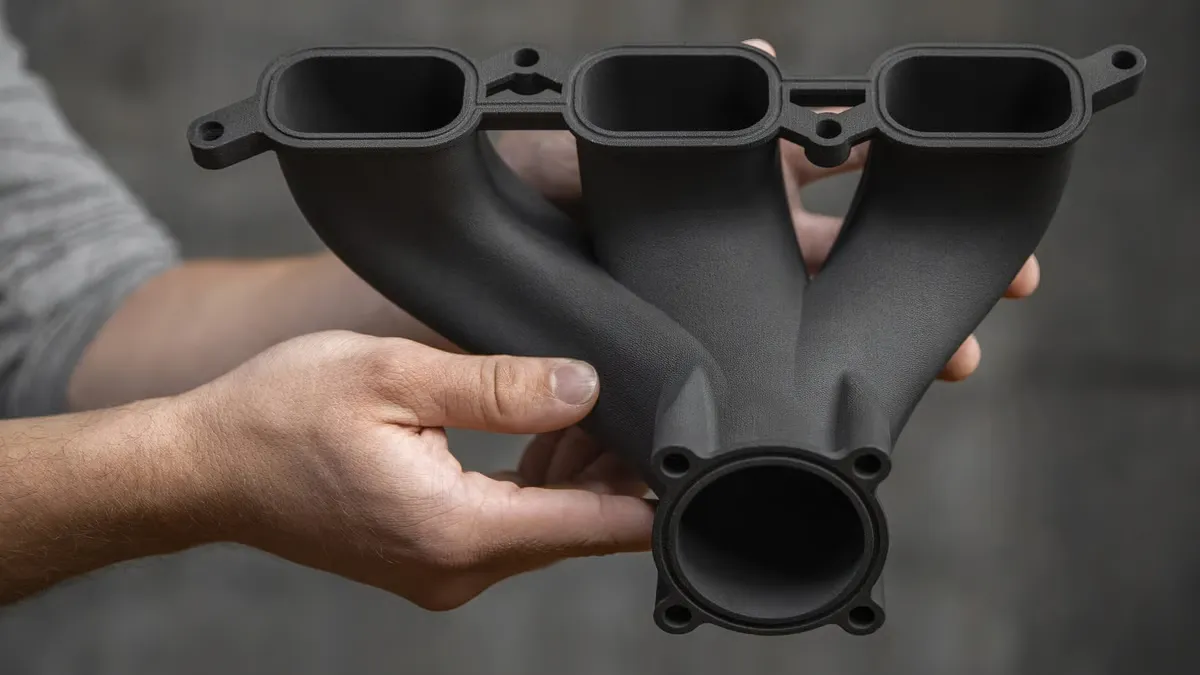
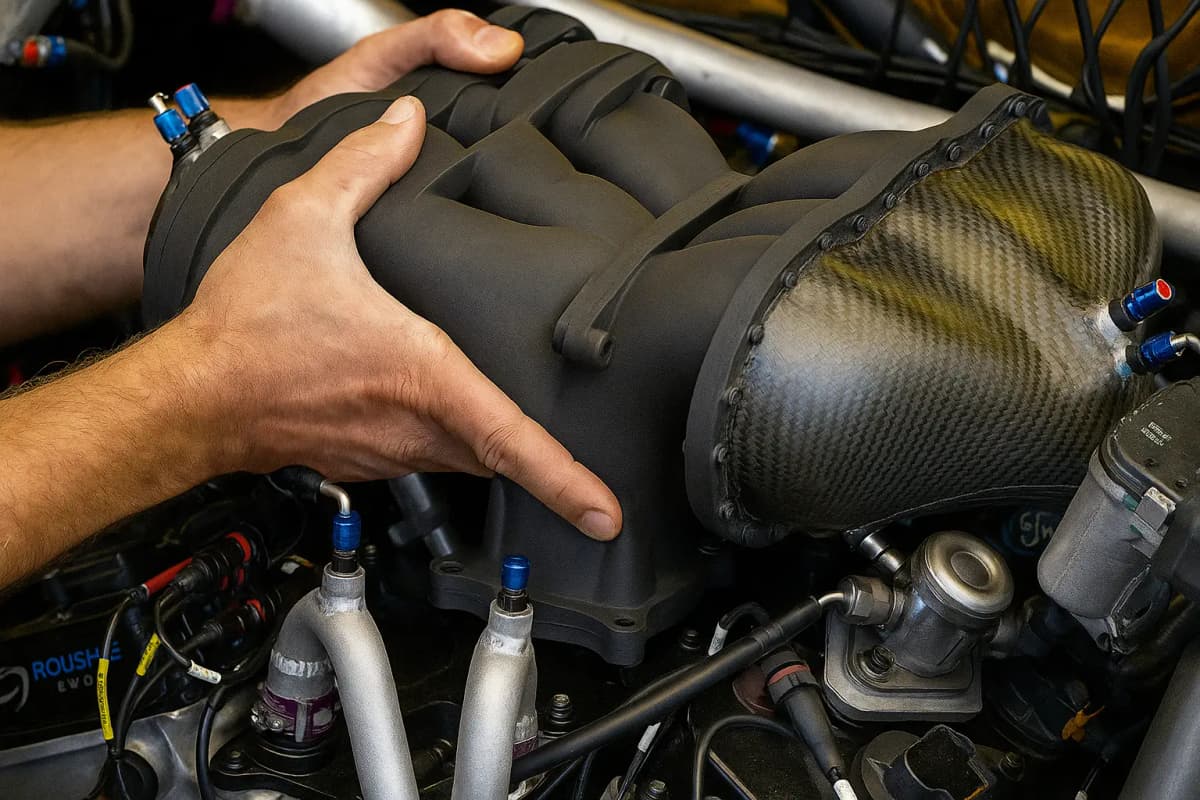
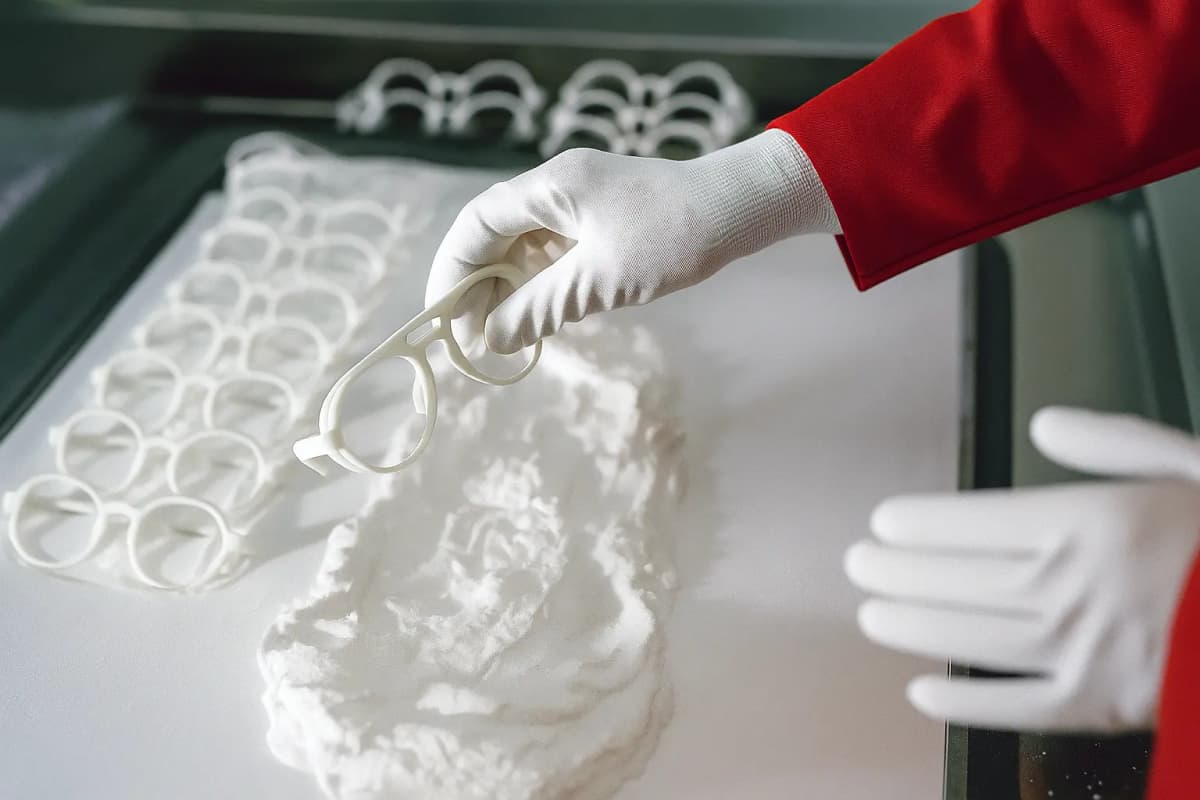
How SLS 3D Printing Works
Selective Laser Sintering uses a high-powered laser to selectively fuse nylon powder particles layer by layer, creating strong, durable parts without support structures.
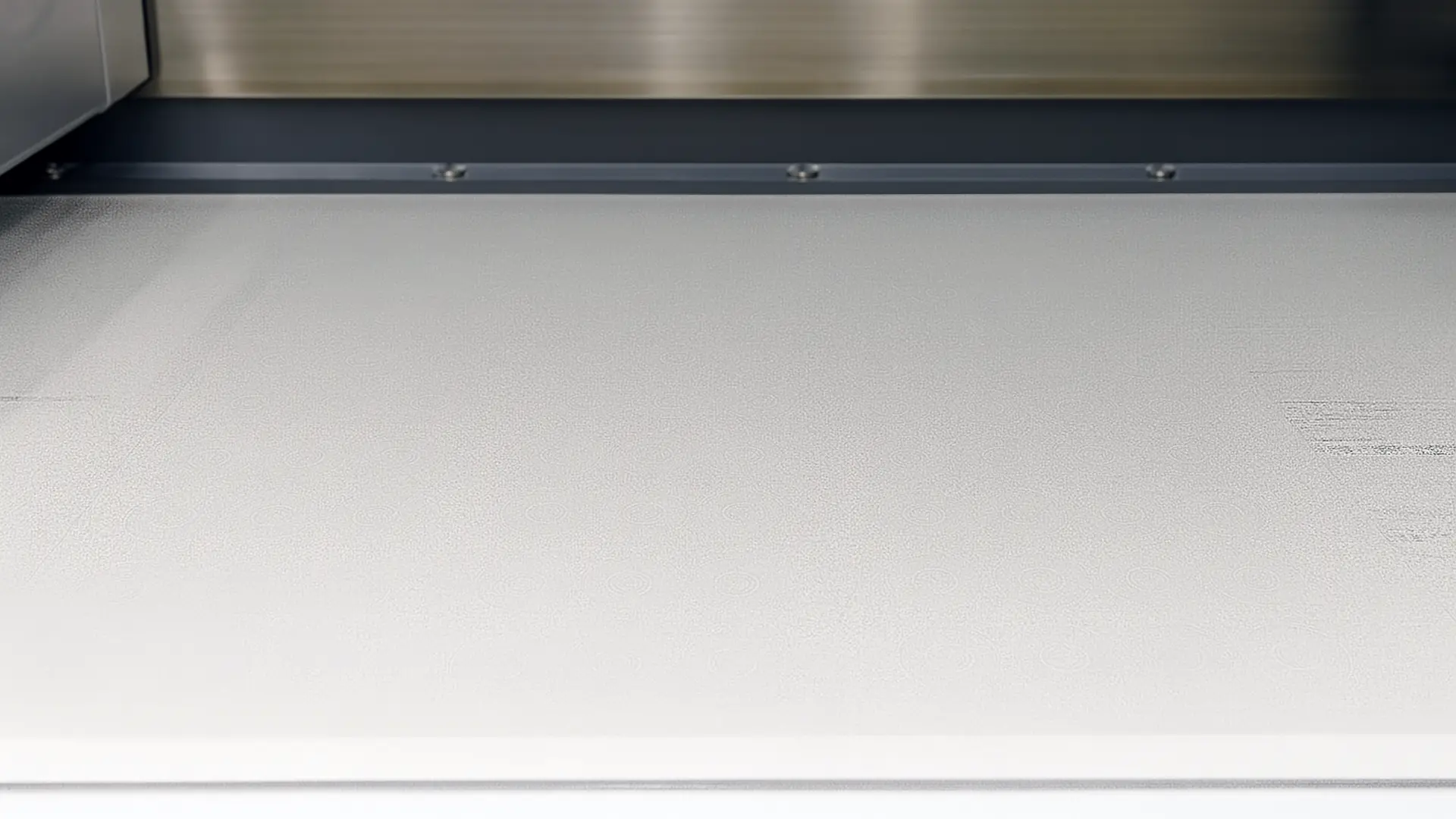
Powder Preparation & Loading
Fresh nylon powder is loaded and preheated to optimal temperature. The build chamber is filled with nitrogen atmosphere.
Step Specifications
High Performance SLS Materials
High-performance SLS materials deliver exceptional mechanical, thermal & chemical properties for functional prototyping and low to mid-volume production. Our advanced polymer selection from EOS, Evonik, and Ultrasint offers superior strength, durability, and surface finish quality.
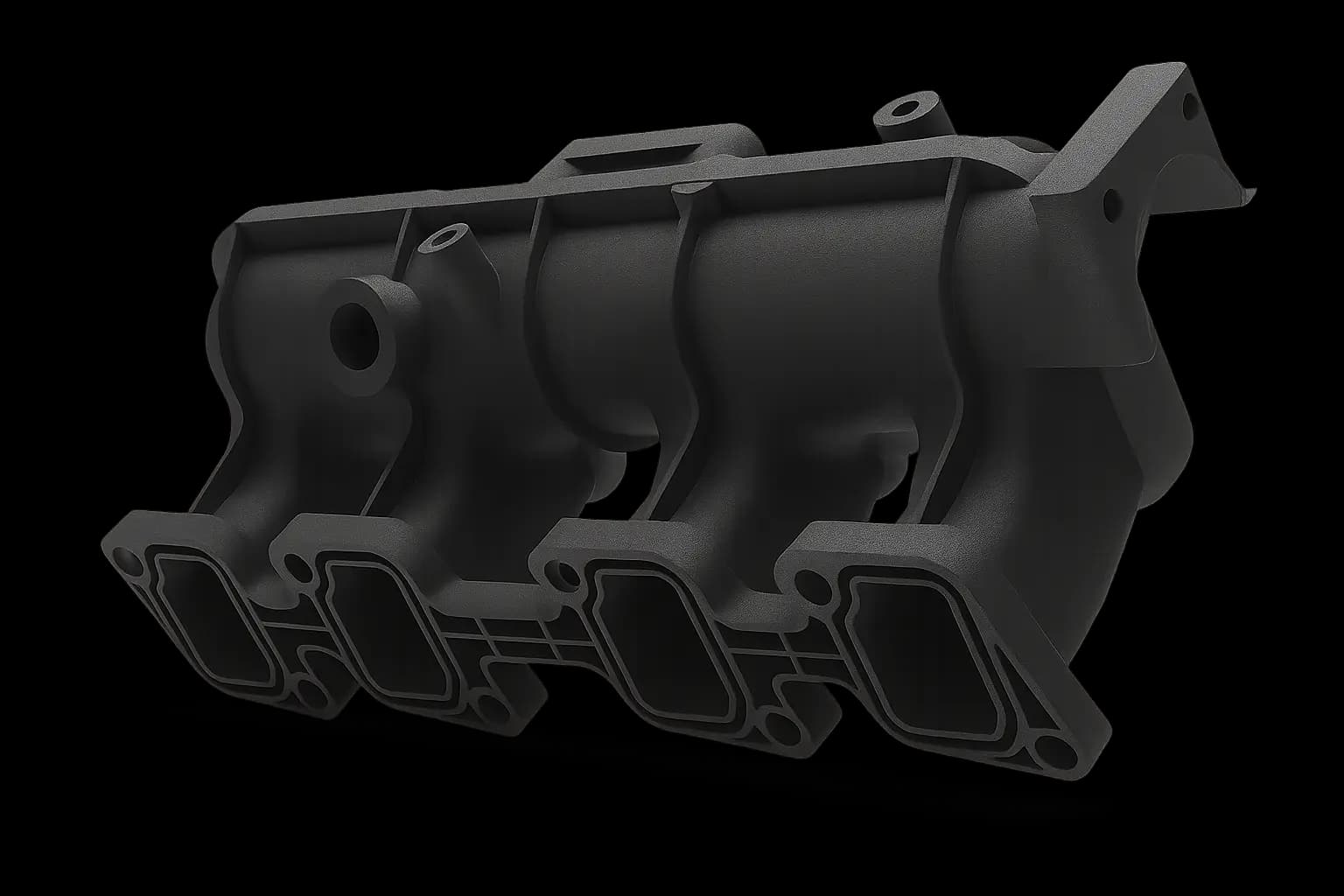
Nylon PA12
Engineering Grade Material
Nylon PA12 is a functional polyamide material that provides a consistent surface finish, excellent resolution and feature detail. Nylon 12 is ideal for both functional prototyping as well as end use applications that require complex thin wall parts, chemical resistance, snap fits and/or low vibration resistance. PA 12 is biocompatible according to EN ISO 10993-1 and USP/Level VI/121 °C
Applications:
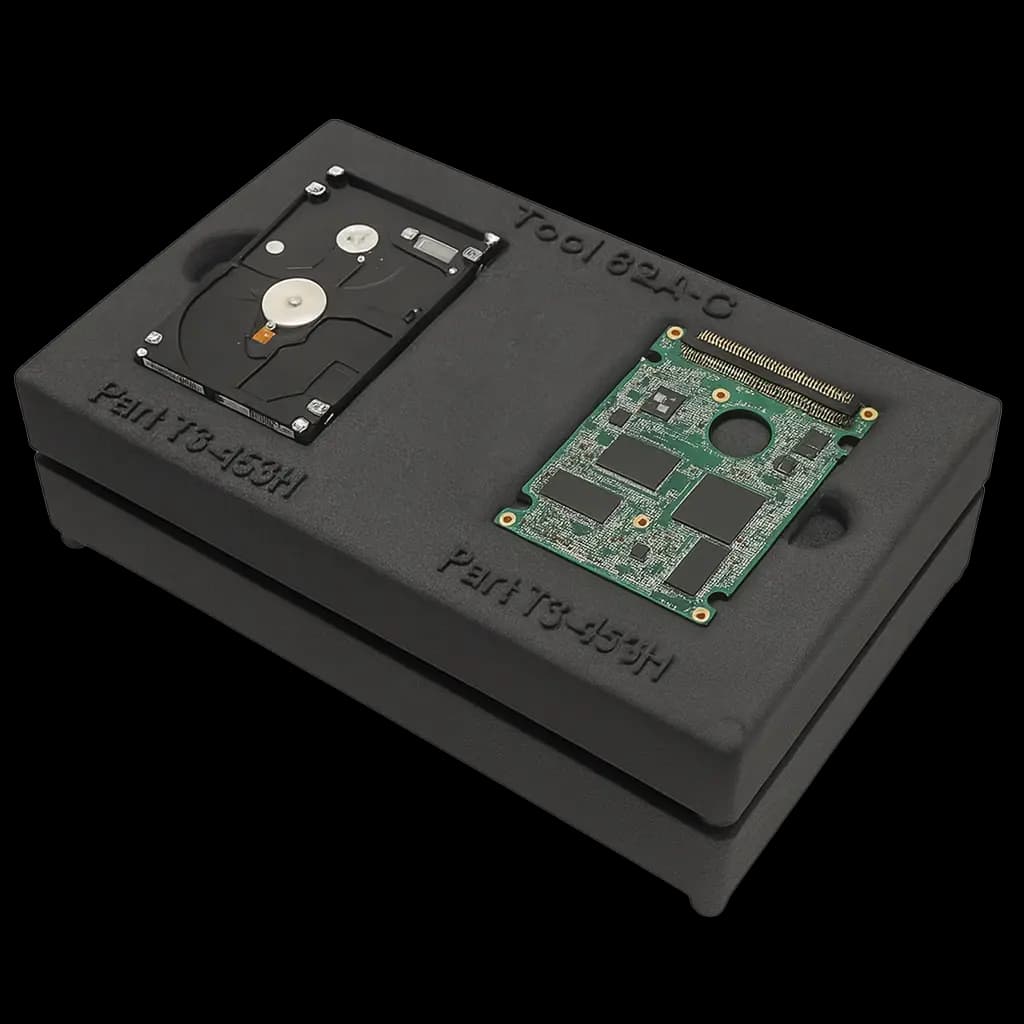
Nylon PA12 ESD
Electrostatic Dissipative Properties
Nylon PA12 ESD combines proven mechanical properties of PA12 with specialized ESD coating. The material is post-processed with 844AR aerosol coating technology to provide reliable electrostatic discharge protection with surface resistance of 1.2 x 10⁷ Ω/sq, ideal for electronics manufacturing and assembly applications. The coating creates a durable, flexible ESD-safe surface that won't crack, chip, or peel.
Applications:
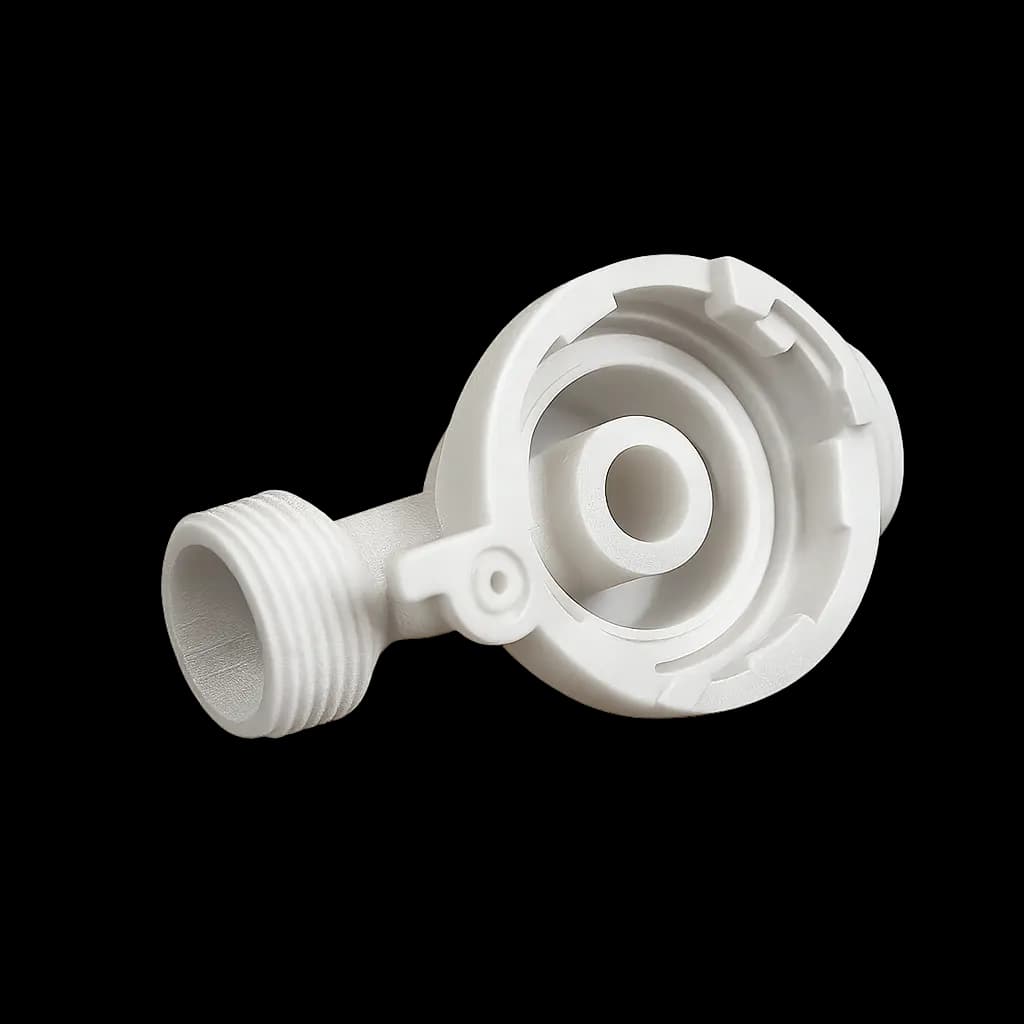
Glass Filled Nylon
High Rigidity Glass Filled
Nylon GF is a glass filled polyamide material ideal for creating exceptionally stiff & hard parts for both prototyping and functional end-use applications. Glass Filled Nylon is best for applications that require high heat resistance and dimensional stability. The unique glass filled infill helps prevent warping and breaking making it a great material for creating large functional parts.
Applications:
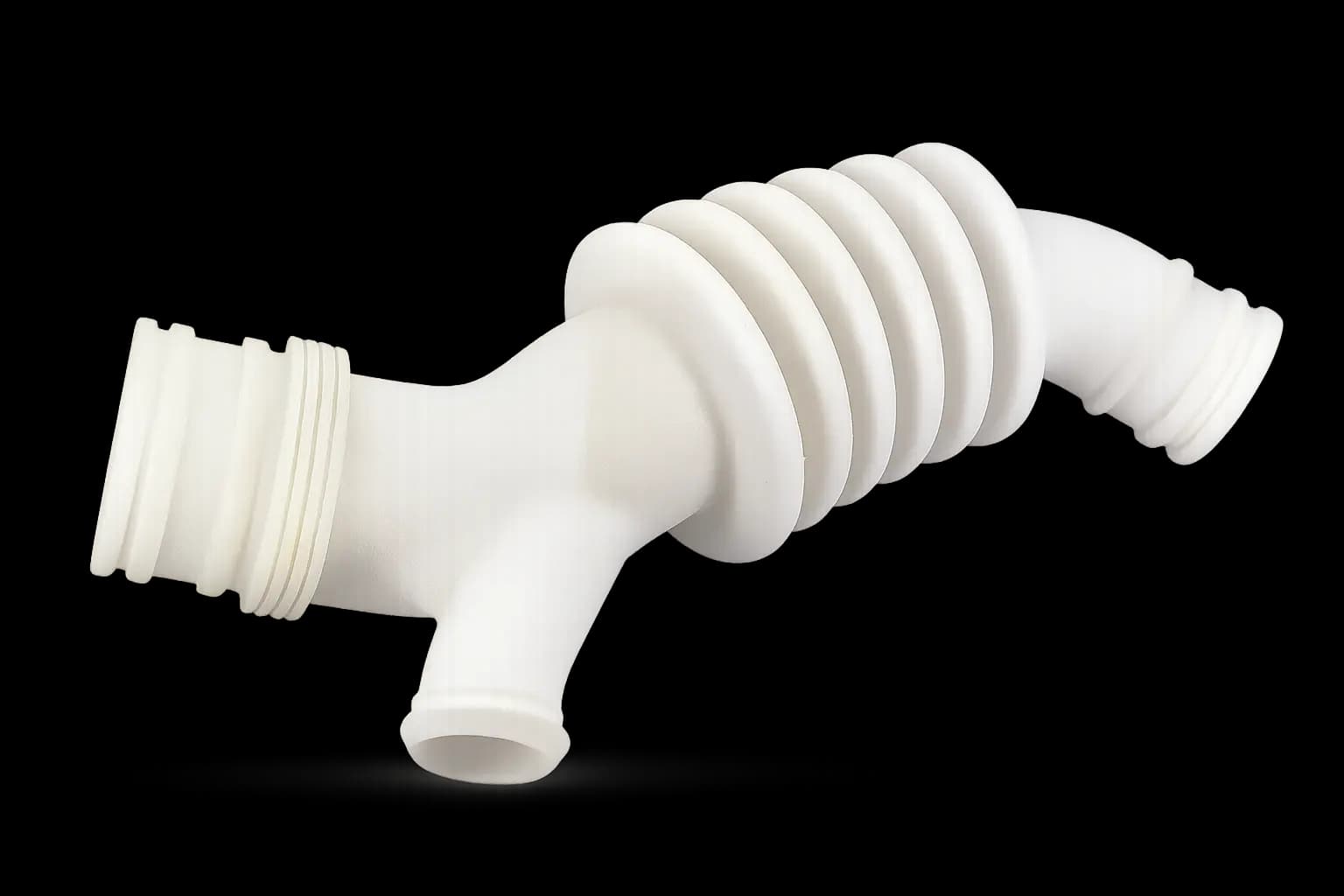
TPU 88A
Flexible & Resilient Properties
TPU 88A is a strong, flexible, and durable properties, combined with its excellent surface quality and level of detail, make it a versatile material for various applications. Its stable white color facilitates easy finishing processes, and its suitability for sports protection equipment, footwear, orthopedic models, car interior components, and industrial tools highlights its adaptability across different industries.
Applications:
Material Surface Finishes
SLS parts feature a fine-textured matte surface finish that is durable and functional, making them ideal for a wide range of applications. While the natural finish is suitable for many uses, SLS parts can be further enhanced through post-processing techniques. Deep color dyeing with DyeMansion technology provides vibrant, uniform colors, while painting allows for a smooth, professional finish that can match precise aesthetic requirements.
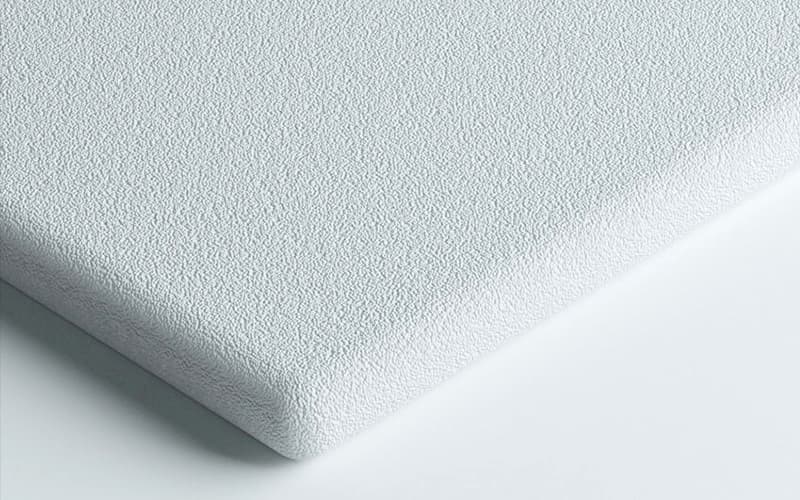
Standard Finish
Fine-textured Matte Surface
Selective Laser Sintered (SLS) parts naturally come in a fine-textured matte surface finish. Parts are depowdered through media blasting, resulting in a bright white color with a slightly grainy texture. The surface is durable, uniform, and functional, making it ideal for both mechanical and aesthetic applications. While intricate details are well-defined, the porous nature of SLS PA12 can lead to a slightly rough feel, which can be improved through post-processing techniques.
Finish Attributes
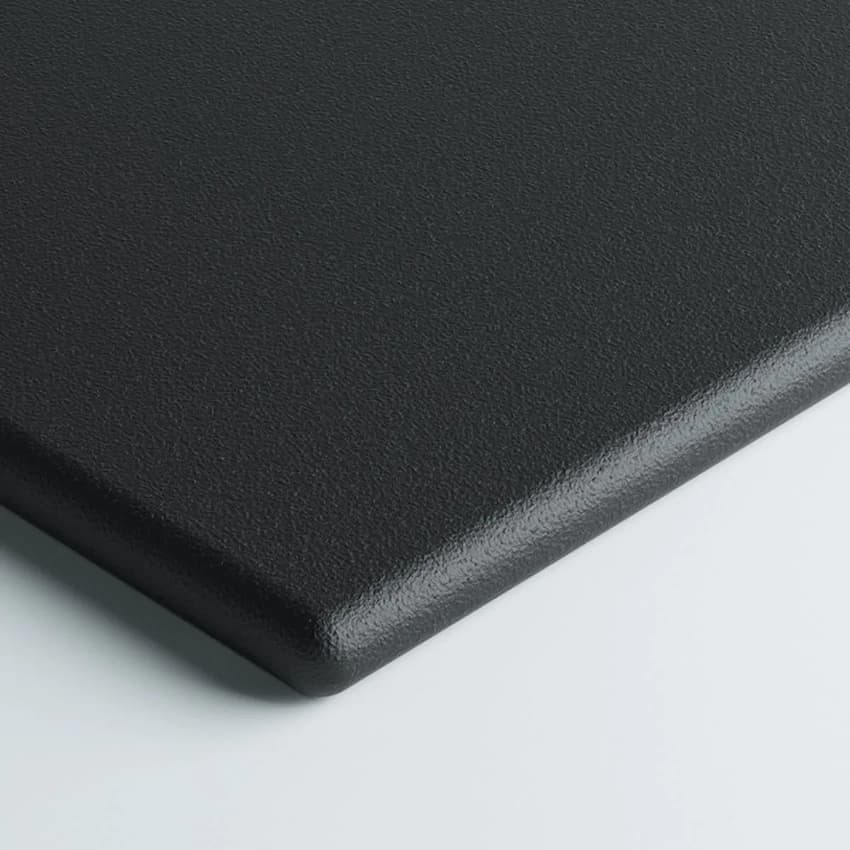
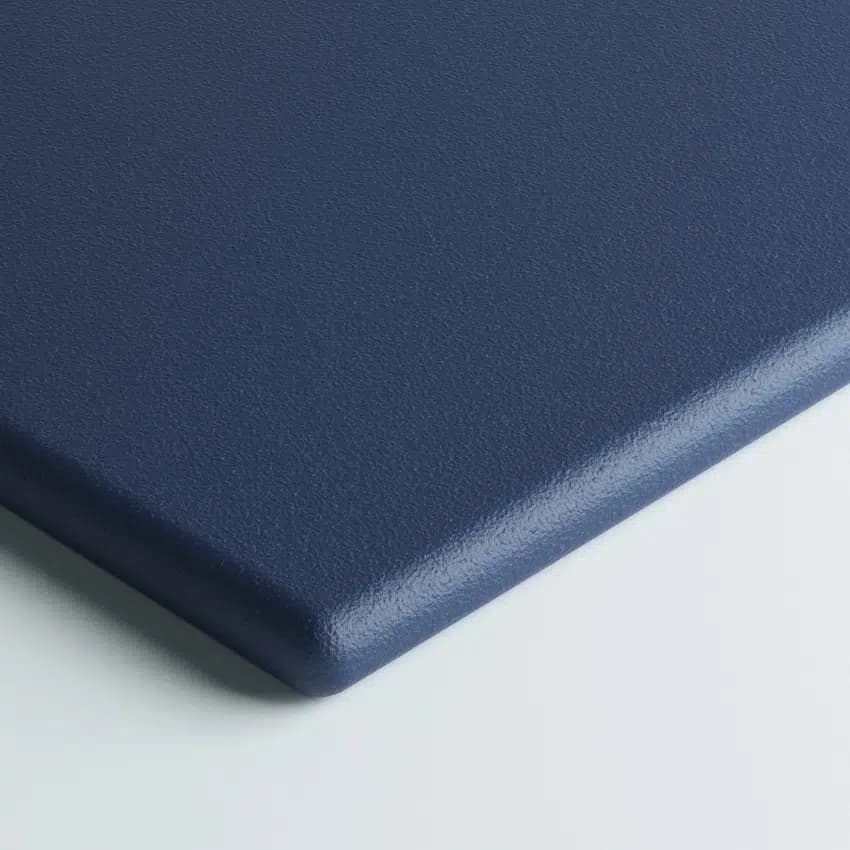
Deep Color Dye
Rich, Uniform Color Coverage
Deep color dying provides a rich, uniform color, improving the overall aesthetics. Suitable for both functional and visually appealing applications. The dye also enhances scratch resistance, making the parts more durable in handling and use. This process ensures consistent color uniformity across the entire part, even for complex geometries or intricate designs.
Finish Attributes
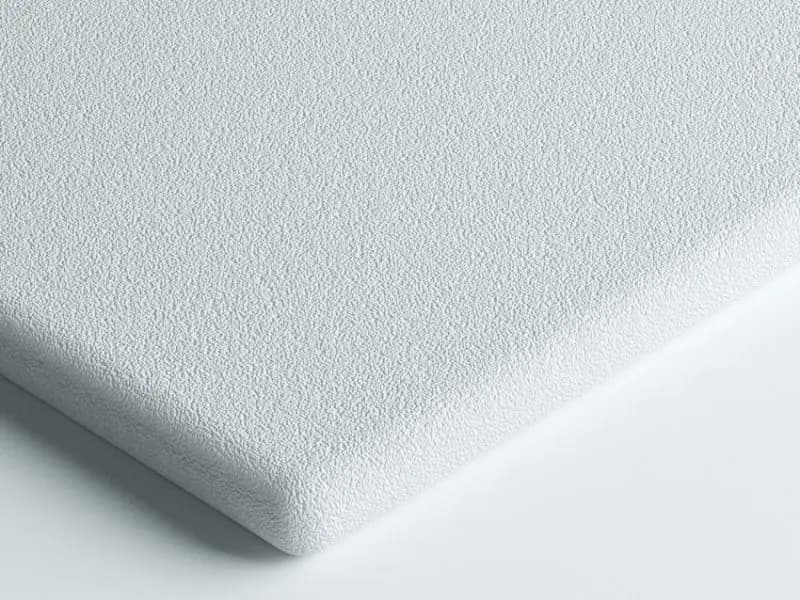
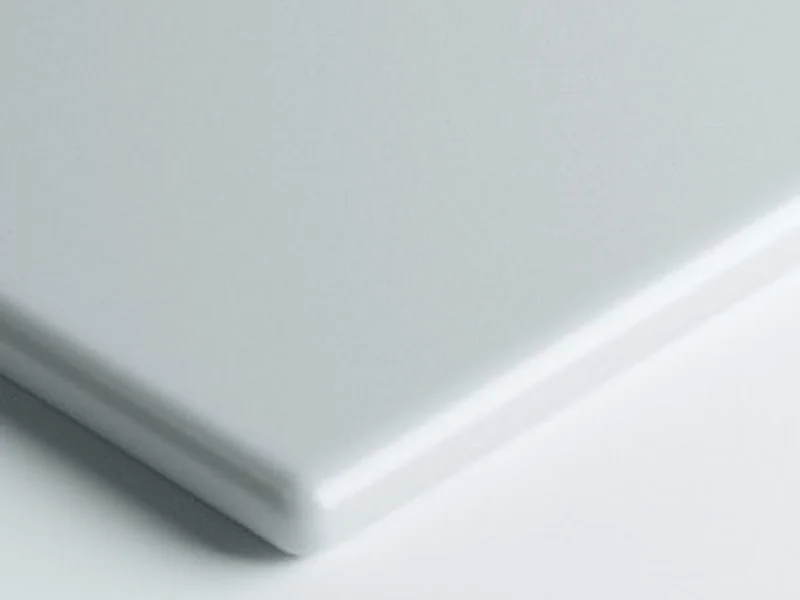
Vapour Finishing
Controlled Chemical Vapour Smoothing
Vapour finishing uses controlled chemical vapour to smooth the surface texture of SLS parts, reducing the characteristic powder grain while maintaining dimensional accuracy. This process creates a more refined surface feel and appearance, making it ideal for parts requiring improved aesthetics or user interaction. The result is a smoother touch feel while preserving the structural integrity and detail definition of the original part.
Finish Attributes
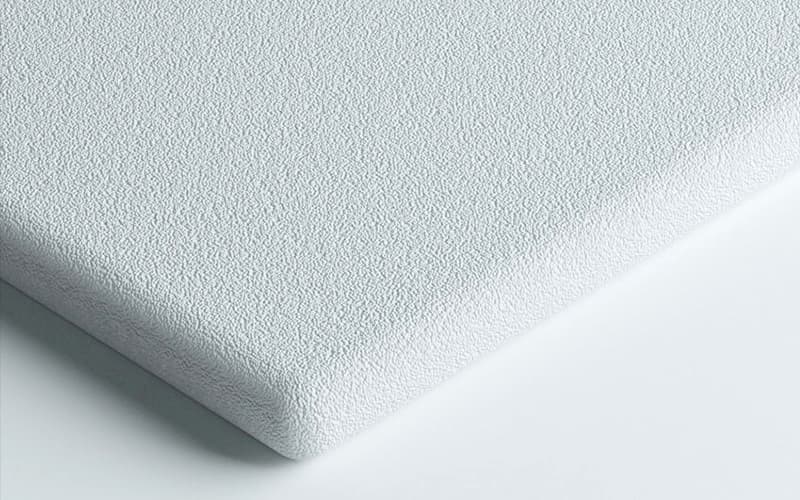
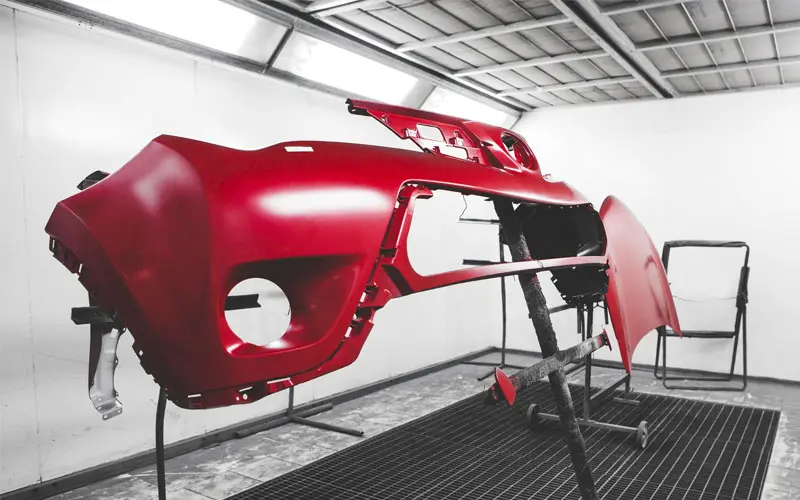
Performance Paint
Automotive-Grade Coating
Painting offers a highly durable, automotive-grade coating that enhances the aesthetics and durability of 3D-printed parts. Each part is hand-finished to ensure smooth surfaces and a premium quality appearance. Using professional-grade coating equipment, this process allows for precise application and exceptional adhesion. Custom color matching is available, making it ideal for applications that require specific branding or visual impact.
Finish Attributes
Additional Manufacturing Services
Complete your SLS parts with our precision post-processing services for production-ready components.
Threading
Precision threads for functional assemblies
Tapping
Drill press tapped holes for connections
Heat Set Inserts
Threaded inserts for durable fastening
Assembly Services
Professional part assembly & integration
CAD Optimization
Optimize parts for production
Manufacturing Design Guidelines
Our manufacturing guidelines help ensure optimal part performance, accuracy, and printability in SLS 3D printing. Key factors such as tolerances, layer height, minimum feature size, and wall thickness directly affect final part quality and functionality. By following these best practices, you can achieve strong, precise, and manufacturable components while reducing the risk of print defects and minimizing post-processing requirements.
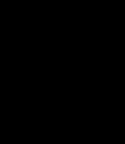
Maximum Build Volume
340 x 340 x 600 mm (13.4 x 13.4 x 23.6 in)
Our EOS SLS machines (EOS P396 and EOS P110 Velocis) offer a maximum build volume of 340 x 340 x 600 mm (13.4 x 13.4 x 23.6 in), allowing for the production of both small, intricate components and large, durable parts. They operate with a standard layer thickness of 100 µm, ensuring fine detail resolution while maintaining efficiency.
Parts designed with large flat planes will likely warp, so this should be avoided if tight tolerances are required.
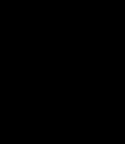
Tolerances
Nylon PA 12: ±0.25%, with a lower limit of ±0.25 mm
If your parts require specific tolerances, please include an engineering drawing along with the part. Parts designed with large flat planes will likely warp, so this should be avoided if tight tolerances are required.
Tolerances differ for TPU: 0-30 mm (XY: ±0.35 mm, Z: ±0.90 mm), 30-50 mm (XY: ±0.40 mm, Z: ±1.15 mm), 50-80 mm (XY: ±0.50 mm, Z: ±1.50 mm)
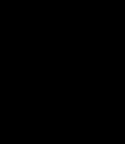
Layer Height
60 - 120 Microns
The layer height is the overall Z resolution of the part; we avoid stepping artifacts on important features of your models by orienting the part(s) along the Z plane or at a 20 degree angle on all sides. Our EOS SLS printers (P396 and P110 Velocis) support layer heights of 60 µm, 100 µm (standard), and 120 µm, allowing for a balance between detail and print speed. Lower layer heights produce finer details and smoother surfaces but increase print time, making them ideal for precision components.
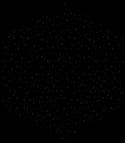
Surface Finish
Uniform, Matte
SLS parts feature a uniform, matte finish with a fine, powdery texture, making them ideal for functional prototypes and end-use applications. The self-supporting nature of SLS eliminates the need for support structures, ensuring consistent quality and design freedom without post-removal marks. The surface is naturally durable and can be further enhanced through bead blasting, tumbling, or vapor smoothing for a refined aesthetic and improved performance.
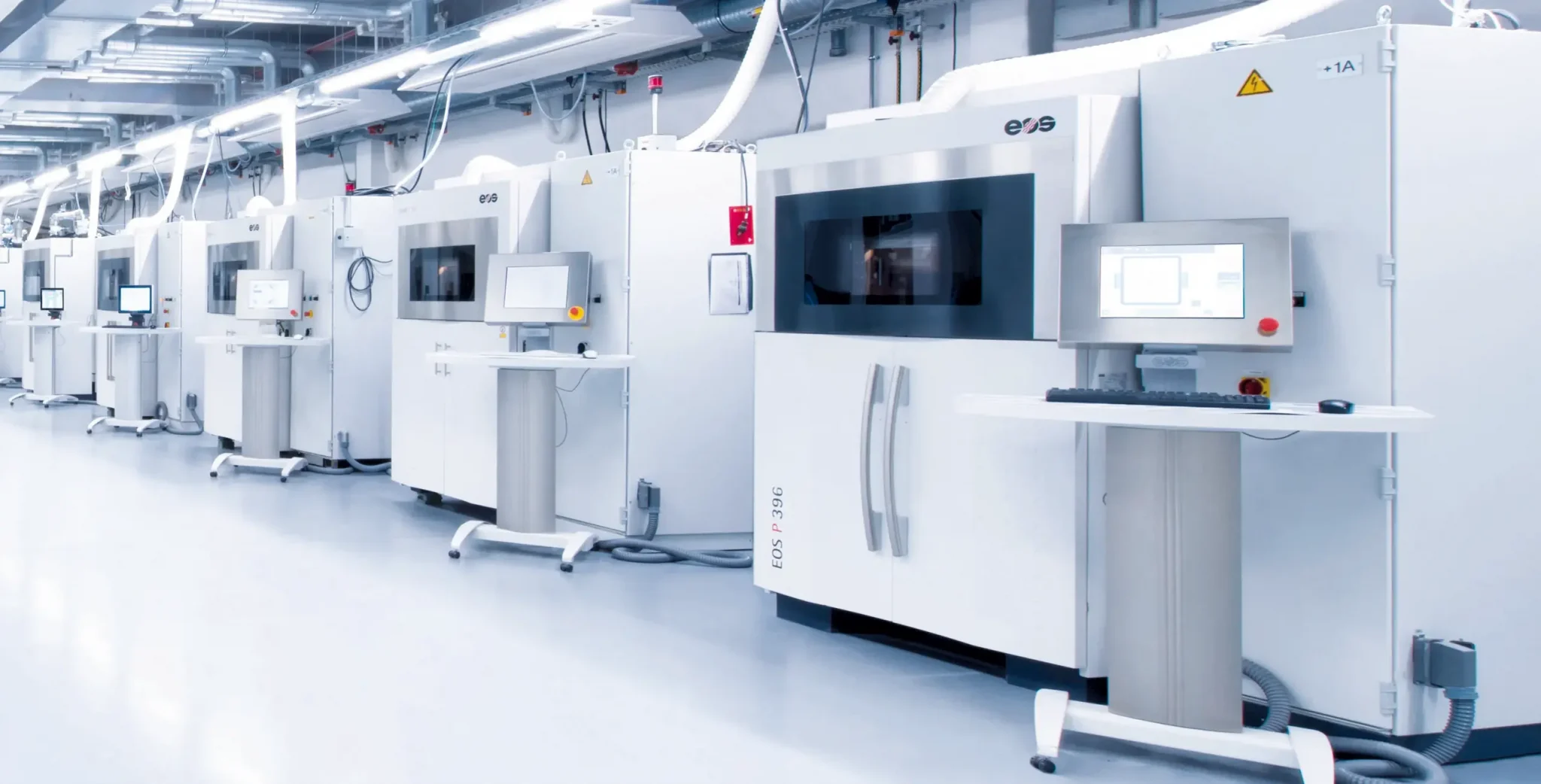
Advantages of SLS 3D Printing for Prototyping & Production
SLS uses a laser to fuse nylon powder layer by layer, creating strong parts without support structures. This enables complex internal geometries impossible with traditional manufacturing, while batch production keeps costs low for small to medium runs.
- No Support Structures
- Create complex internal geometries, lattice structures, and undercuts without supports.
- Cost-Effective for Complex Parts
- Eliminate tooling costs and reduce waste compared to CNC machining.
- Engineering-Grade Materials
- Choose from Nylon PA12, ESD variants, glass-filled, and flexible TPU options.
- Batch Production
- Print multiple parts simultaneously to reduce per-unit costs.
- Production-Ready Parts
- Parts match injection-molded strength for functional testing and end-use.
- Consistent Properties
- Isotropic strength ensures reliable performance in all directions.
Instant Quote Tool
From Upload to Delivery
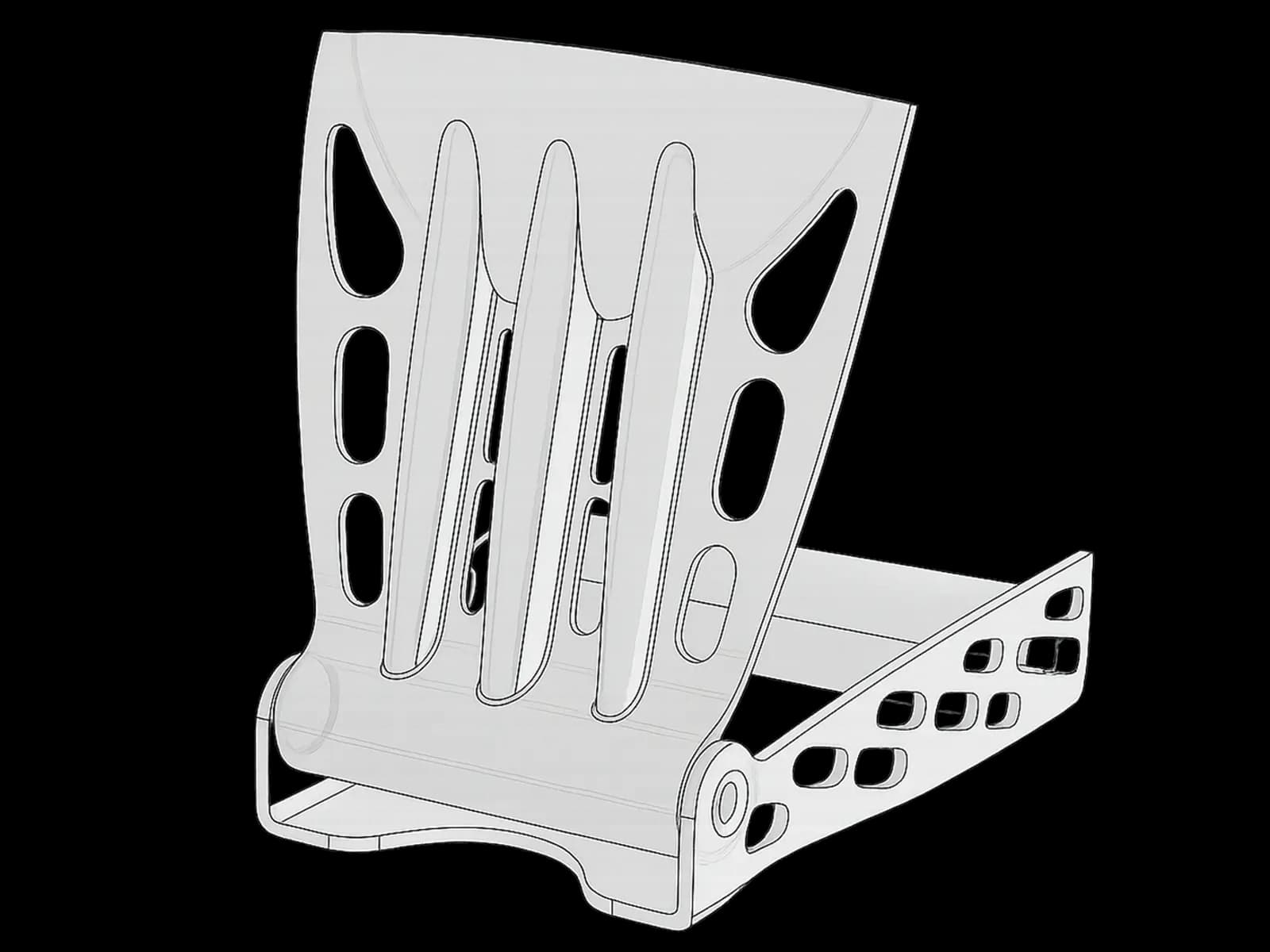
75% complete
Simple File Upload Process
Drag and drop your 3D files or browse to upload. Our system automatically analyzes your designs and provides instant feedback on printability and optimization suggestions.
- Drag & drop multiple file formats
- Automatic design analysis
- Printability feedback
- File optimization suggestions
SLS Applications Across Industries
Discover how Selective Laser Sintering is transforming manufacturing across industries with innovative solutions and enhanced capabilities.
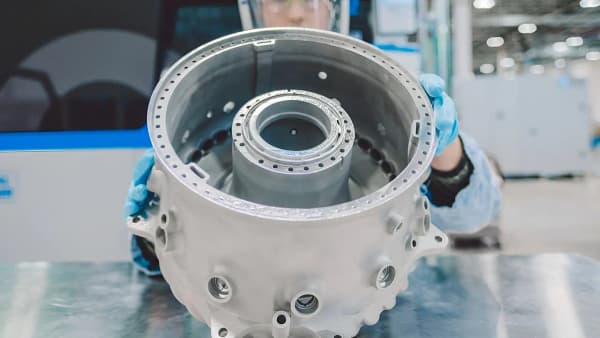
Aerospace Components
Lightweight, strong parts for aircraft interiors and UAV components
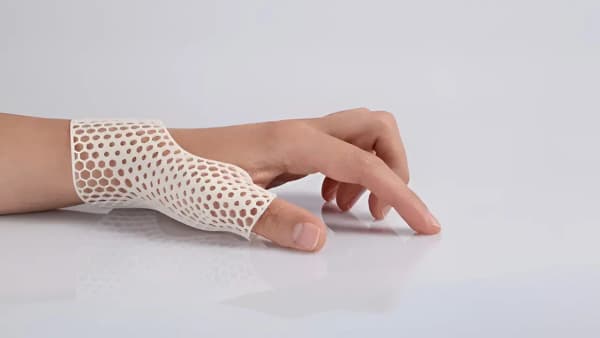
Medical Devices
Biocompatible parts for prosthetics, surgical guides, and medical equipment
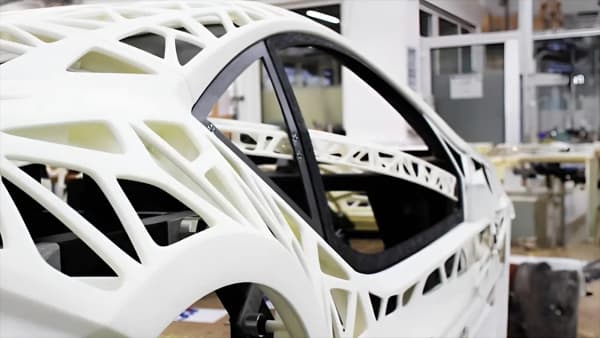
Automotive Parts
Functional components for under-hood applications and interior parts
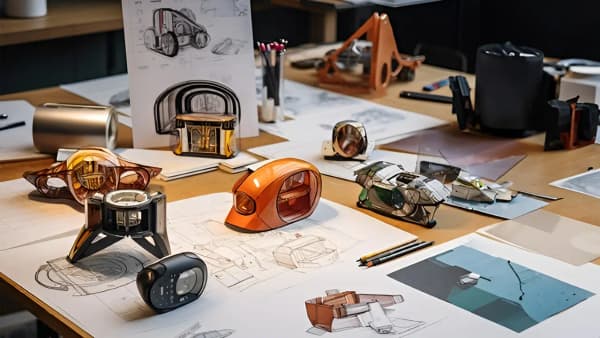
Industrial Tooling
Jigs, fixtures, and custom tools for manufacturing processes
Success Stories
Real results from our SLS manufacturing partnerships
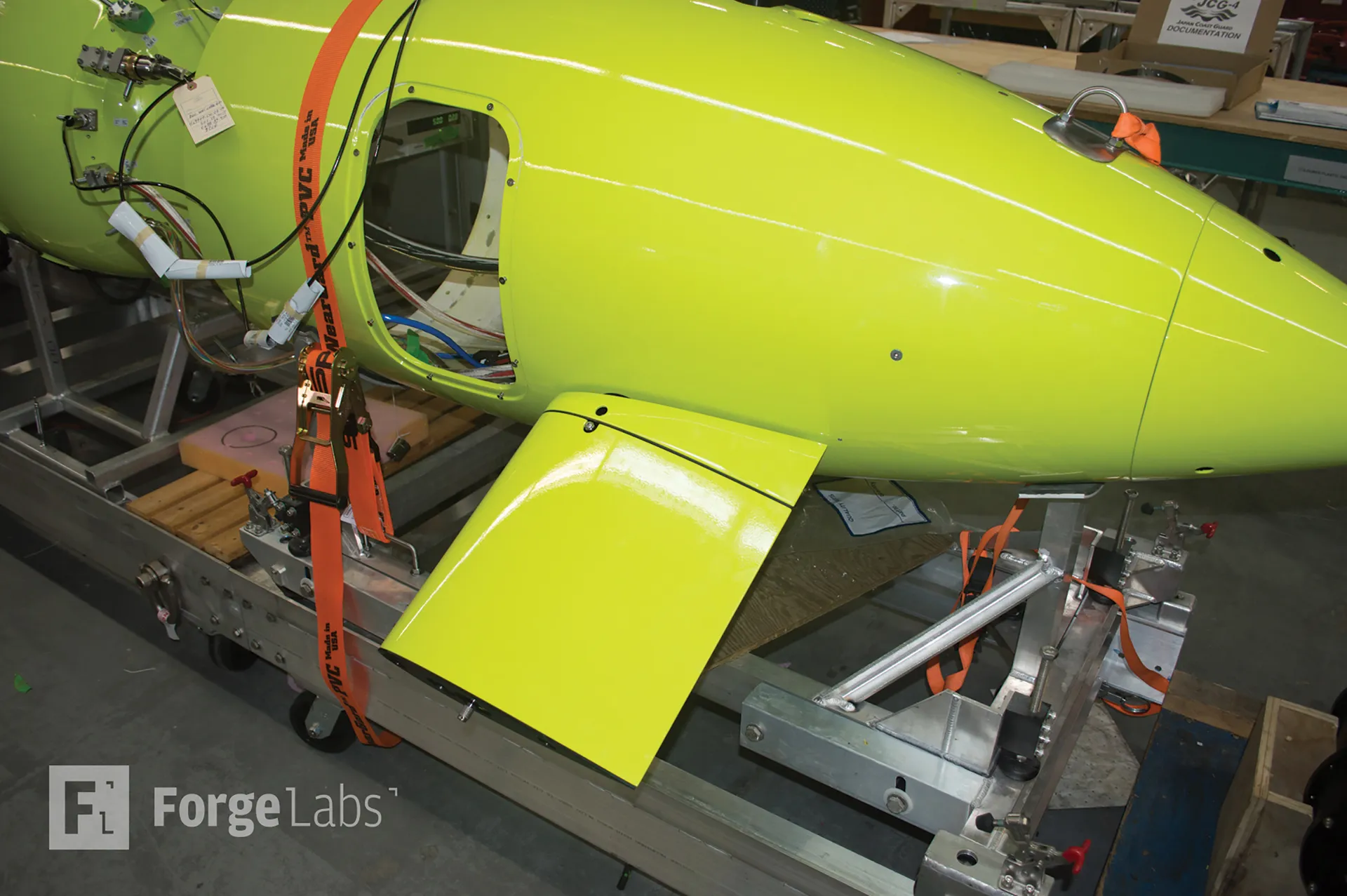
Aerospace Ducting System
Complex internal cooling channels that would be impossible with traditional manufacturing
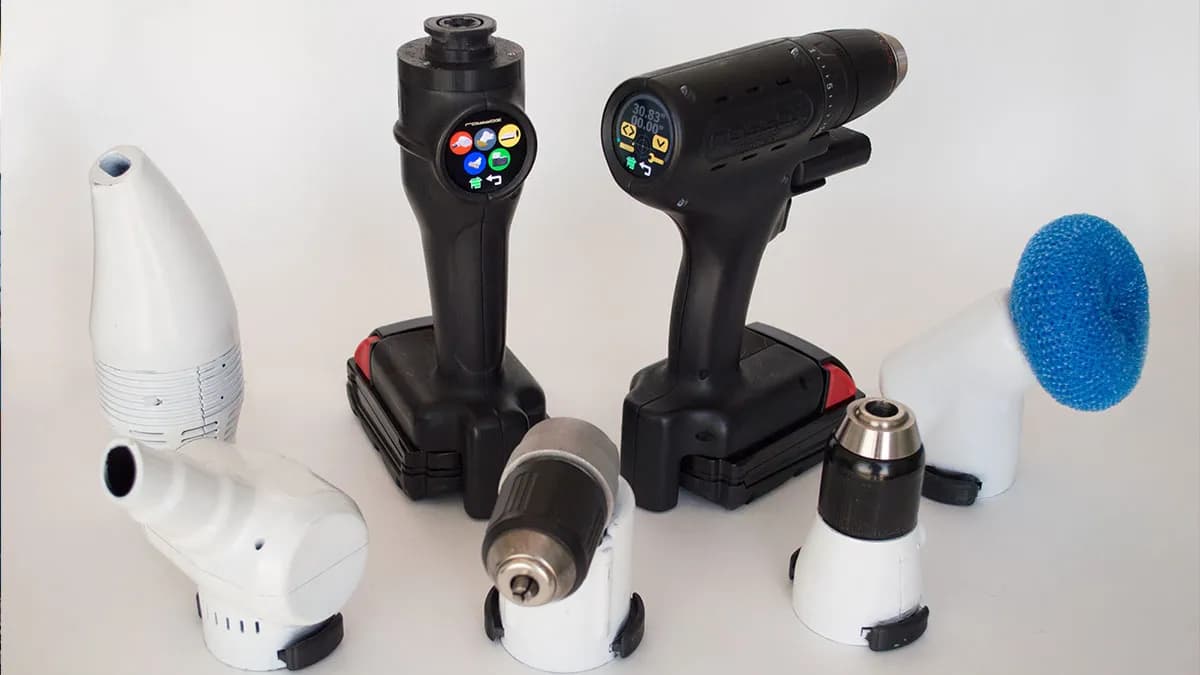
Medical Prosthetic Joint
Custom prosthetic joint with integrated flexion mechanism
Ready to manufacture your parts?
Upload your CAD files to get instant quotes for SLS 3D printing. Professional-grade manufacturing with fast turnaround times.
Click to start your quote
STL, STEP, OBJ, 3MF supported • Get instant pricing
SLS Questions & Answers
Common questions about SLS 3D printing technology. Can't find what you're looking for? Reach out to our technical team.