Accelerate Product Developmentwith Industrial 3D Printing
Forge Labs empowers industrial designers with fast, high-fidelity prototyping and functional parts—ready to test, refine, and launch. No tooling. No delays. Just real parts, fast.

Industrial Design Excellence
Built for Designers Who Build Real Things
From concept mockups to fully functional prototypes, we support industrial design teams with additive manufacturing technologies that reduce lead times, eliminate tooling, and enable better design decisions—faster. Whether you're launching new hardware, building wearables, or testing injection-molded products, our process helps you move faster from sketch to shelf.
Transforming Industrial Design Manufacturing
From concept mockups to fully functional prototypes, we support industrial design teams with additive manufacturing technologies that reduce lead times, eliminate tooling, and enable better design decisions—faster. Whether you're launching new hardware, building wearables, or testing injection-molded products, our process helps you move faster from sketch to shelf.
Key Benefits of 3D Printing in Industrial Design
- Same-day or next-day prototype turnaround through advanced additive manufacturing solutions tailored for industrial design applications.
- Engineering guidance on material selection and DFM through advanced additive manufacturing solutions tailored for industrial design applications.
- High-detail visual and functional parts for testing through advanced additive manufacturing solutions tailored for industrial design applications.
- Eliminate expensive tooling requirements, reducing upfront investments and enabling economical low-volume production.
- Batch production available for pilot runs and market trials through advanced additive manufacturing solutions tailored for industrial design applications.
- CAD review, tolerance guidance, and design optimization through advanced additive manufacturing solutions tailored for industrial design applications.
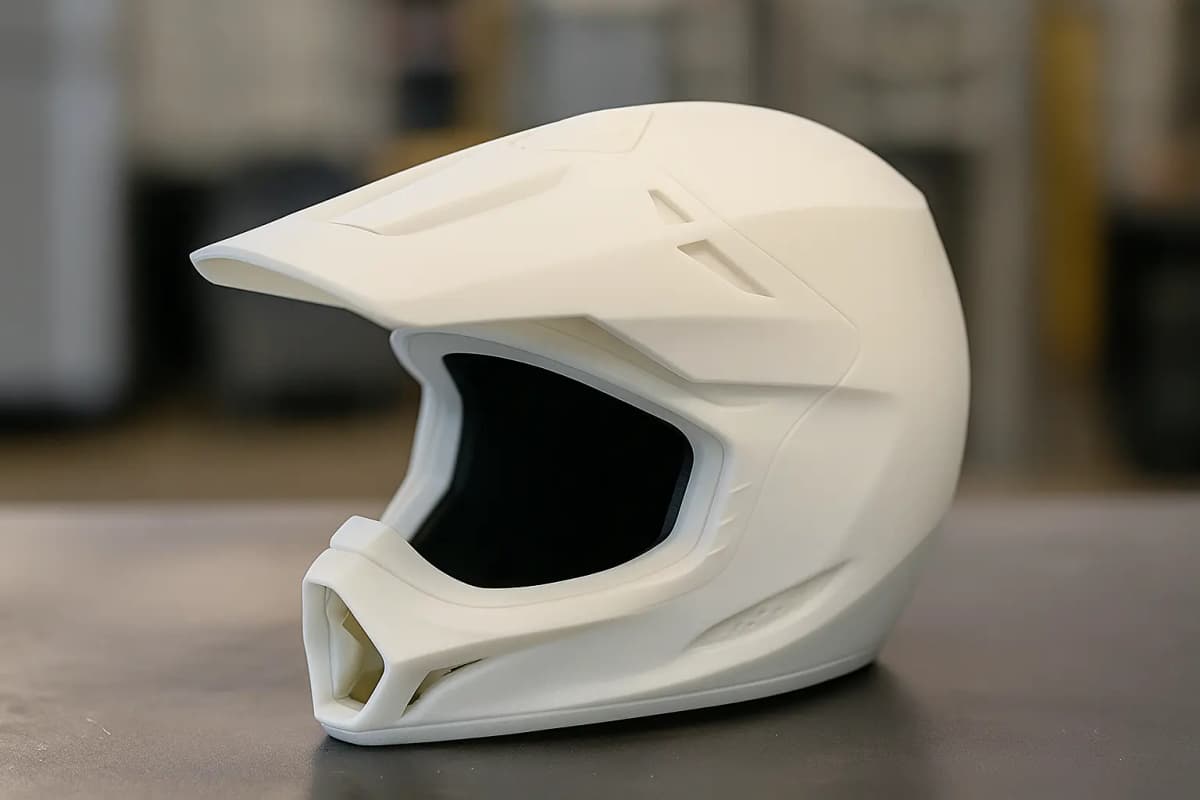
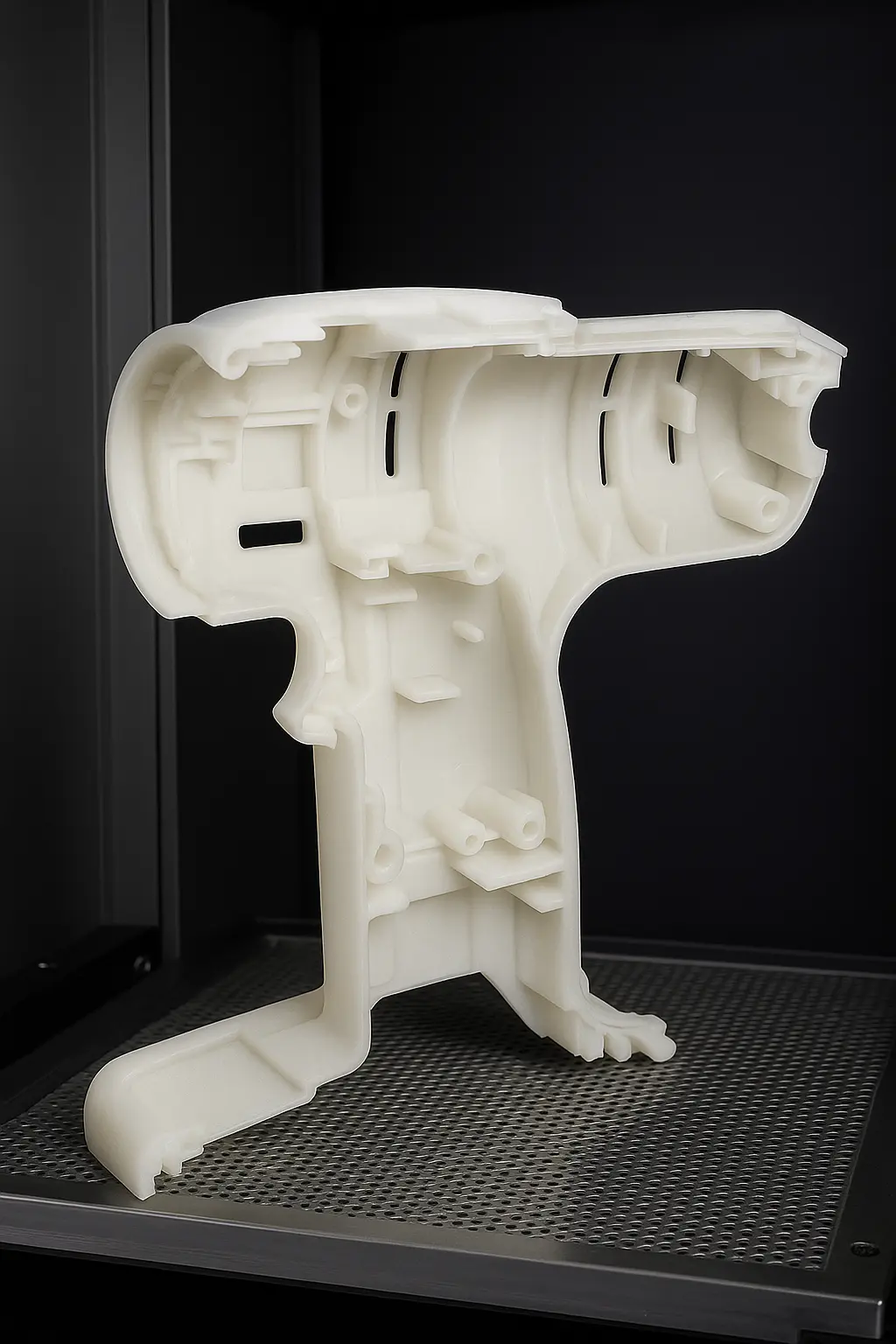
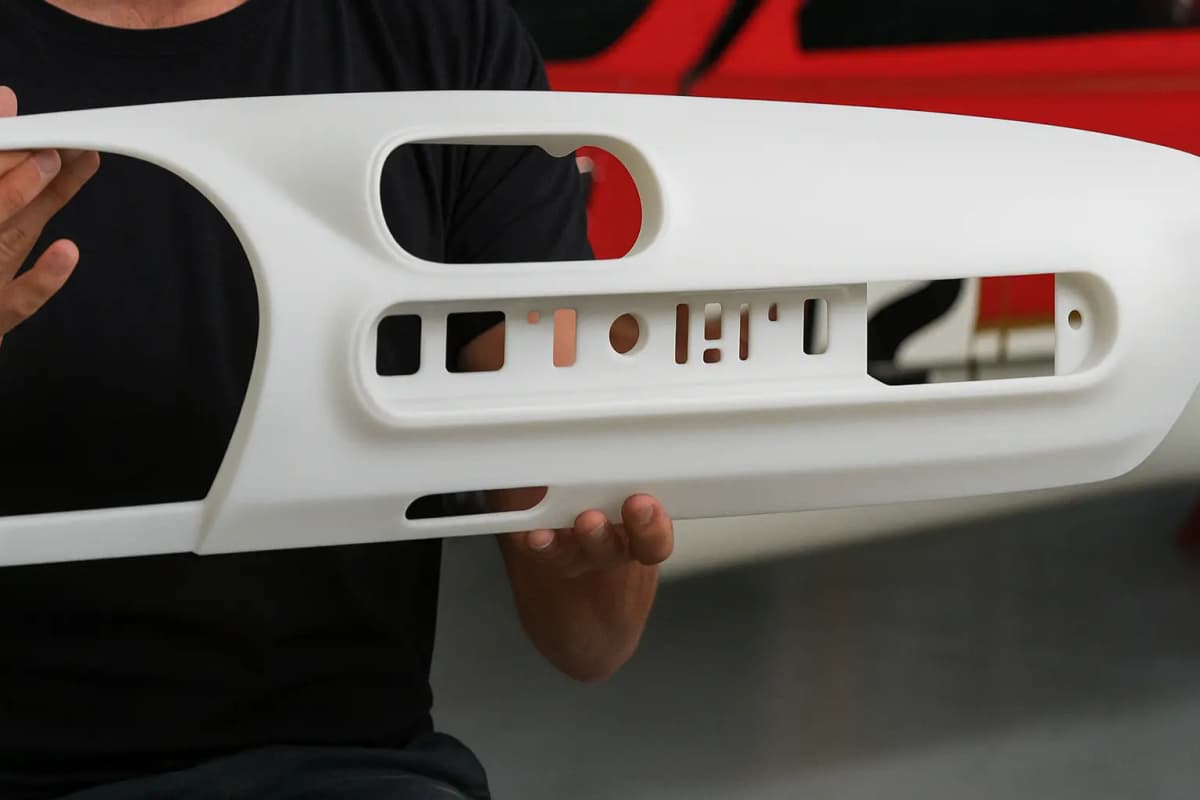
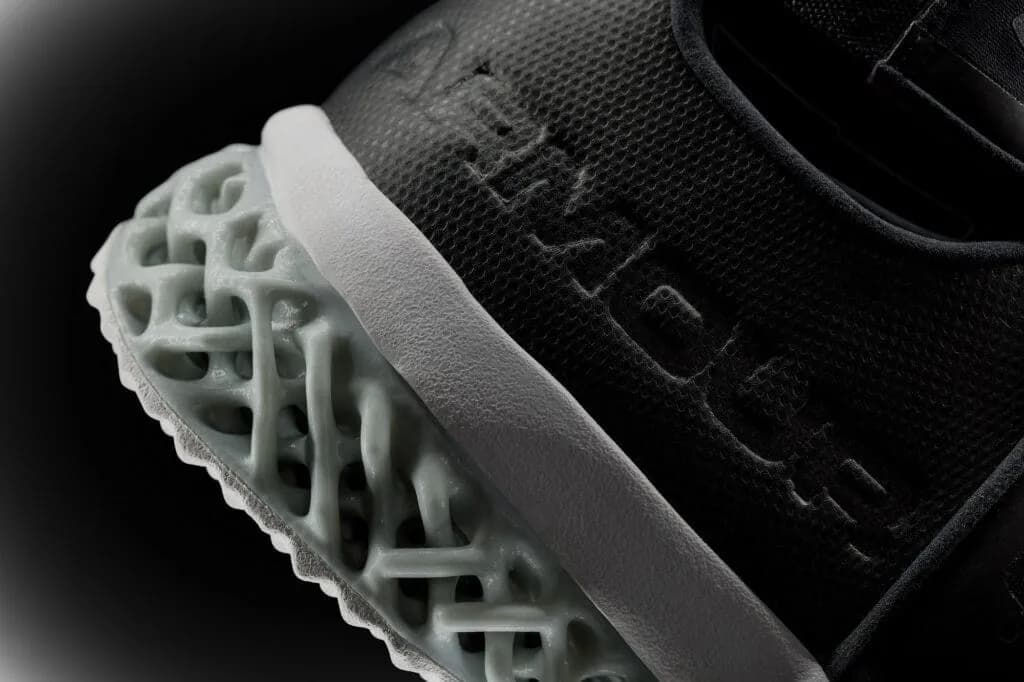
Industry Standards & Compliance
Certified for Industrial Design Excellence
Our manufacturing processes and quality systems meet the most stringent industrial design industry standards, ensuring your parts are ready for critical applications.
Design for Manufacturing (DFM)
Comprehensive design optimization guidance ensuring prototypes translate effectively to production manufacturing processes.
Material Performance Validation
Rigorous testing protocols ensuring prototype materials accurately represent production behavior and performance characteristics.
Rapid Iteration Capability
Proven workflow enabling multiple design iterations within single development cycles, accelerating time-to-market for new products.
Scale-to-Production Support
Seamless transition from prototype to pilot production with volume manufacturing capabilities and production readiness validation.
Manufacturing Capabilities
Advanced Industrial Design Solutions
From precision prototyping to full-scale production, our comprehensive capabilities deliver results that transform industrial design manufacturing.
Selective laser sintering (SLS) with PA12 nylon delivers functional prototypes with mechanical properties closely matching injection-molded parts. Material characteristics include excellent impact resistance, chemical stability, and fatigue performance suitable for comprehensive testing protocols. Integrated features like snap-fits, living hinges, and threaded connections function as designed without assembly requirements. Dimensional accuracy (±0.25% or ±0.25mm) supports tight-tolerance assemblies while surface quality enables direct testing without secondary finishing operations.
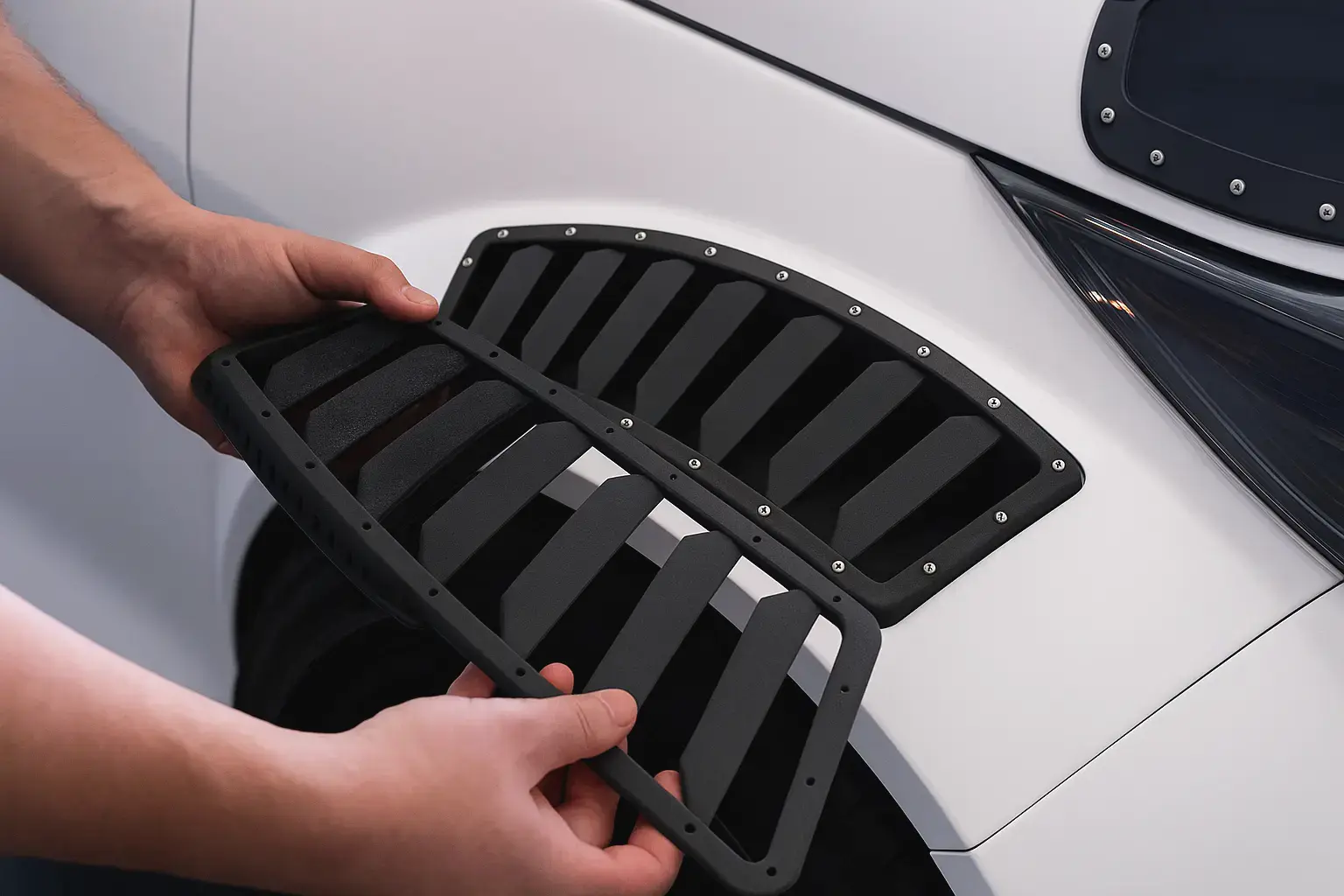
Technical Specifications
Stereolithography (SLA) with high-definition resins produces concept models with exceptional surface quality for color, material, and finish (CMF) validation studies. Multiple resin formulations simulate various material properties from rigid engineering plastics to flexible elastomers. Surface finish options include textured, polished, and painted applications with professional appearance suitable for client presentations and user research. Rapid turnaround enables multiple design iterations within single-day cycles supporting agile development methodologies.
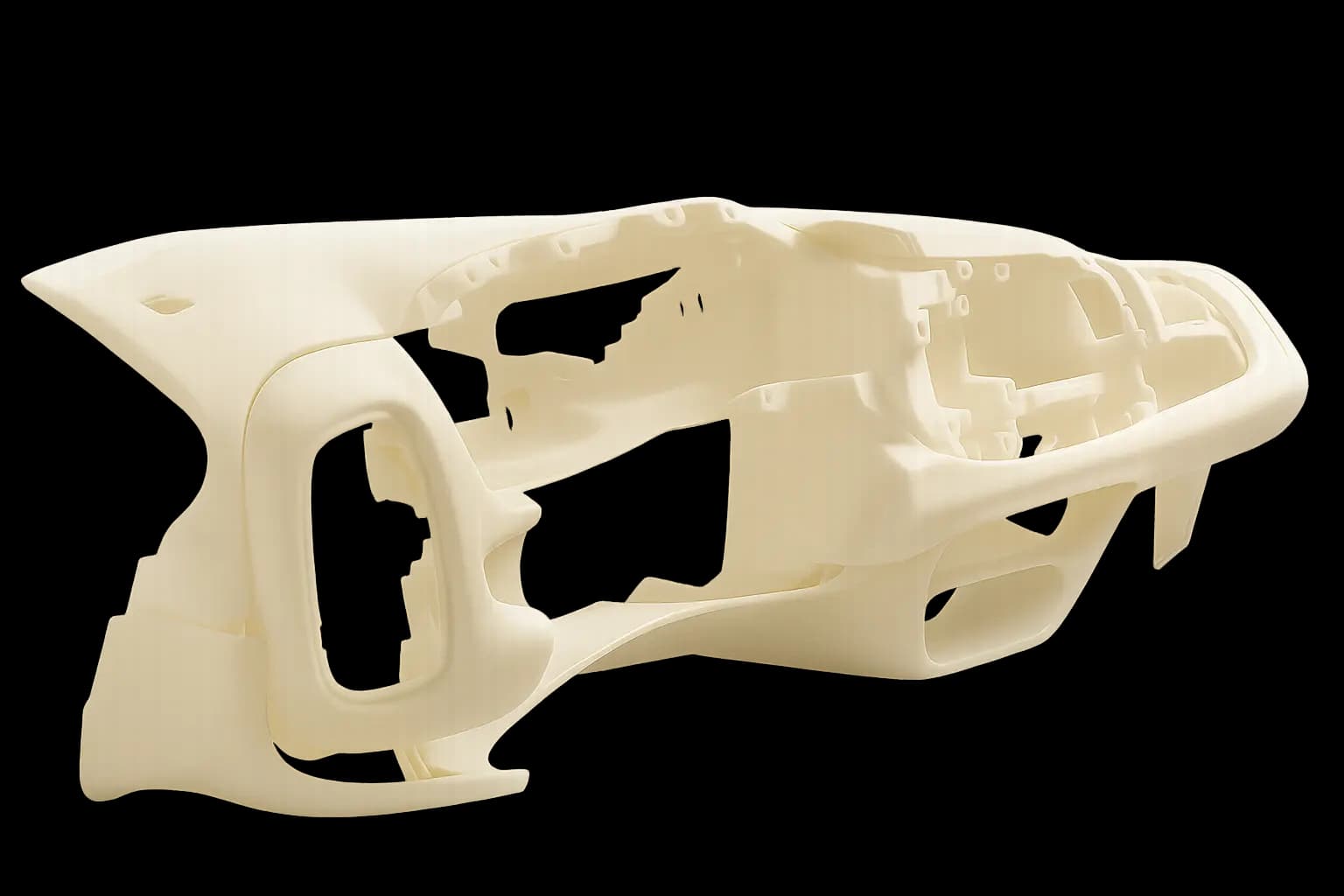
Technical Specifications
Multi Jet Fusion (MJF) technology produces mechanical assemblies with precise dimensional control and excellent surface finish for functional testing and validation. PA12 nylon material properties enable snap-fit mechanisms, threaded connections, and bearing surfaces that perform comparably to injection-molded components. Integrated assembly features eliminate secondary operations while maintaining clearances as tight as 0.5mm for moving parts. Heat-set insert compatibility and post-machining options provide production-ready fastening solutions for prototype assemblies.
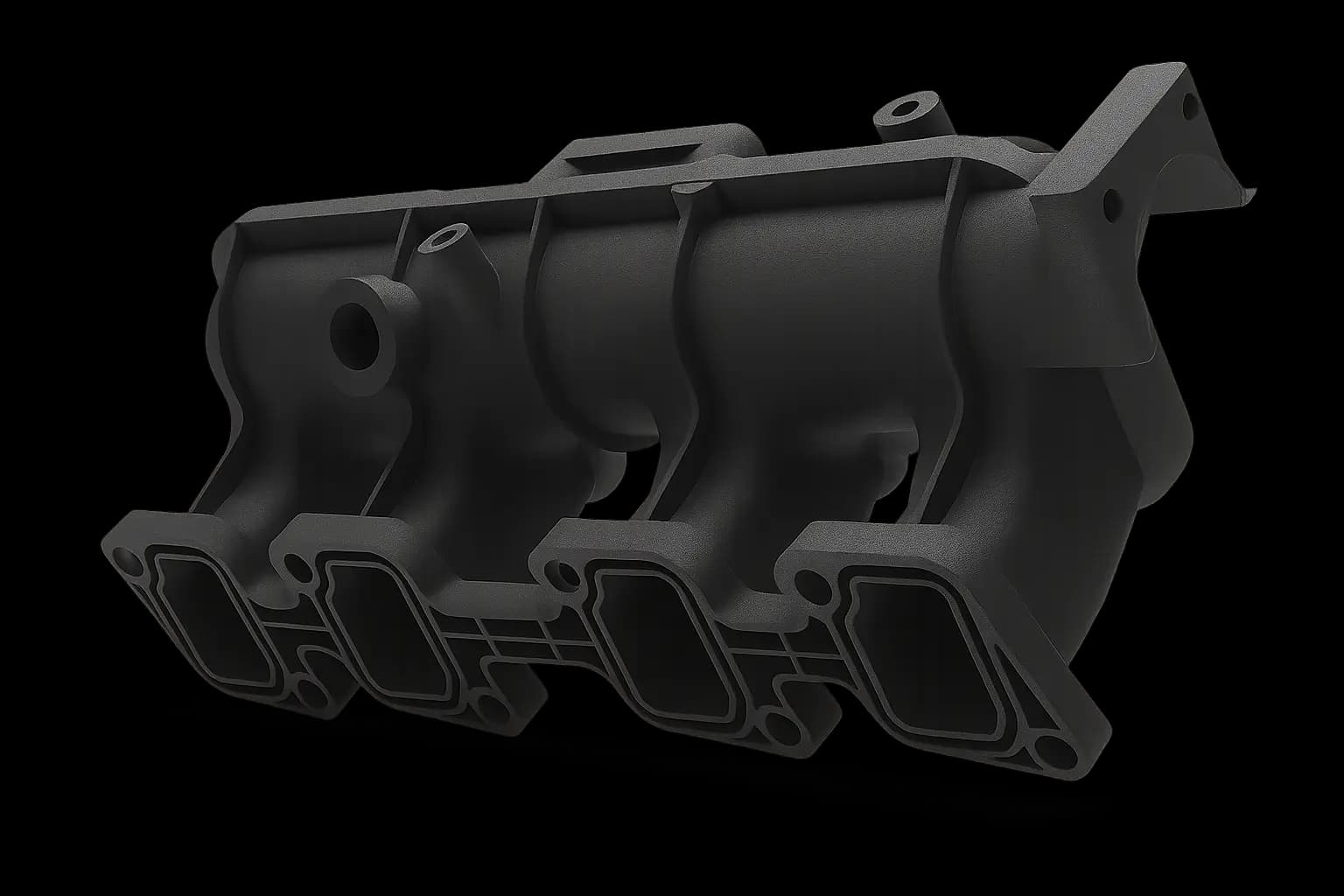
Technical Specifications
Fused deposition modeling (FDM) with maximum build volume (914 x 609 x 914mm) accommodates full-scale prototyping of outdoor gear, sports equipment, and mobility products. Engineering thermoplastics including carbon fiber reinforced nylon provide structural performance suitable for load testing and real-world validation. ASA materials offer UV stability and weather resistance for outdoor applications requiring extended environmental exposure. Large parts can be sectioned and assembled using integrated joinery features for products exceeding build volume constraints.

Technical Specifications
Stereolithography (SLA) and selective laser sintering (SLS) technologies produce electronics housings with precise component fitment and professional surface finish. SLA tolerances (±0.2mm achievable) ensure accurate PCB mounting, connector alignment, and button clearances critical for functional electronics assemblies. Material options include clear resins for LED diffusion, conductive formulations for EMI shielding, and flexible TPU for wearable interfaces. Integrated features like snap-fits, cable management, and heat-staking posts eliminate assembly complexity while maintaining professional appearance suitable for user testing and demonstration.

Technical Specifications
Digital manufacturing enables seamless scaling from prototype validation through pilot production volumes without tooling investment or long-term commitments. Multi Jet Fusion (MJF) and selective laser sintering (SLS) provide consistent part quality across production batches with statistical process control for dimensional verification. Batch sizes from 10 to 1,000+ units support market testing, investor demonstrations, and limited product launches. Quality documentation includes dimensional reports, material certificates, and batch traceability required for commercial validation and early-market feedback programs.
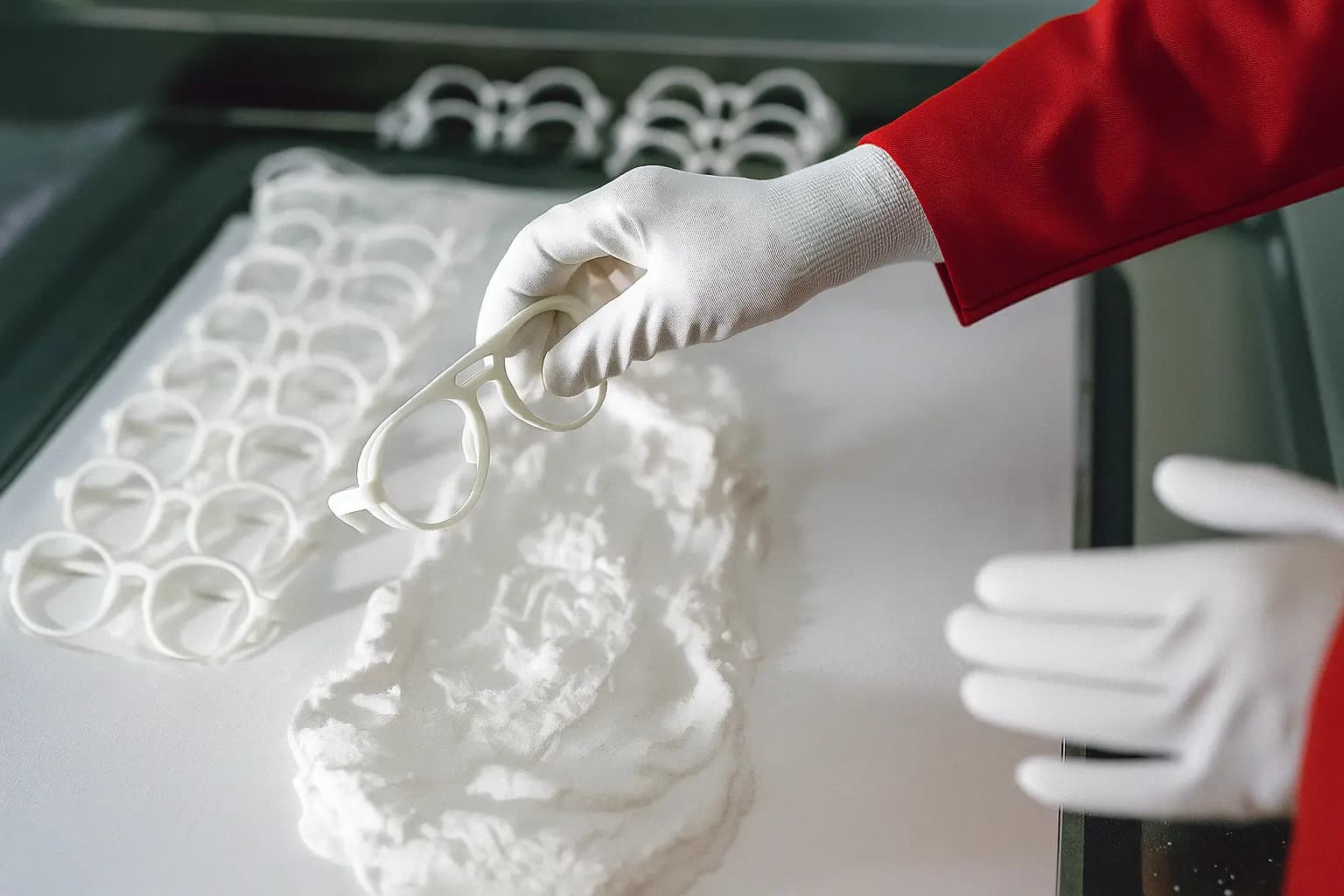
Technical Specifications
Manufacturing Technologies
Proven Technologies for Industrial Design
Each technology offers unique advantages for industrial design applications. Choose the right process for your specific requirements.
Selective Laser Sintering
Support-free manufacturing of complex geometries with engineering-grade nylon materials. Ideal for functional prototypes...
Stereolithography
Ultra-high resolution resin printing for exceptional surface quality and fine detail. Perfect for concept models, visual...
Fused Deposition Modeling
Industry-leading precision with engineering thermoplastics and carbon fiber composites. Excellent for large-format proto...
Multi Jet Fusion
Precision engineering with fine detail resolution and excellent surface finish. Outstanding for mechanical assemblies, m...
Not sure which technology is right for your project?
Our application engineers can help you select the optimal manufacturing process based on your specific requirements, materials, and timeline.
Certified Materials
Industrial Design-Grade Materials
High-performance materials engineered and certified for demanding industrial design applications with full traceability and compliance documentation.
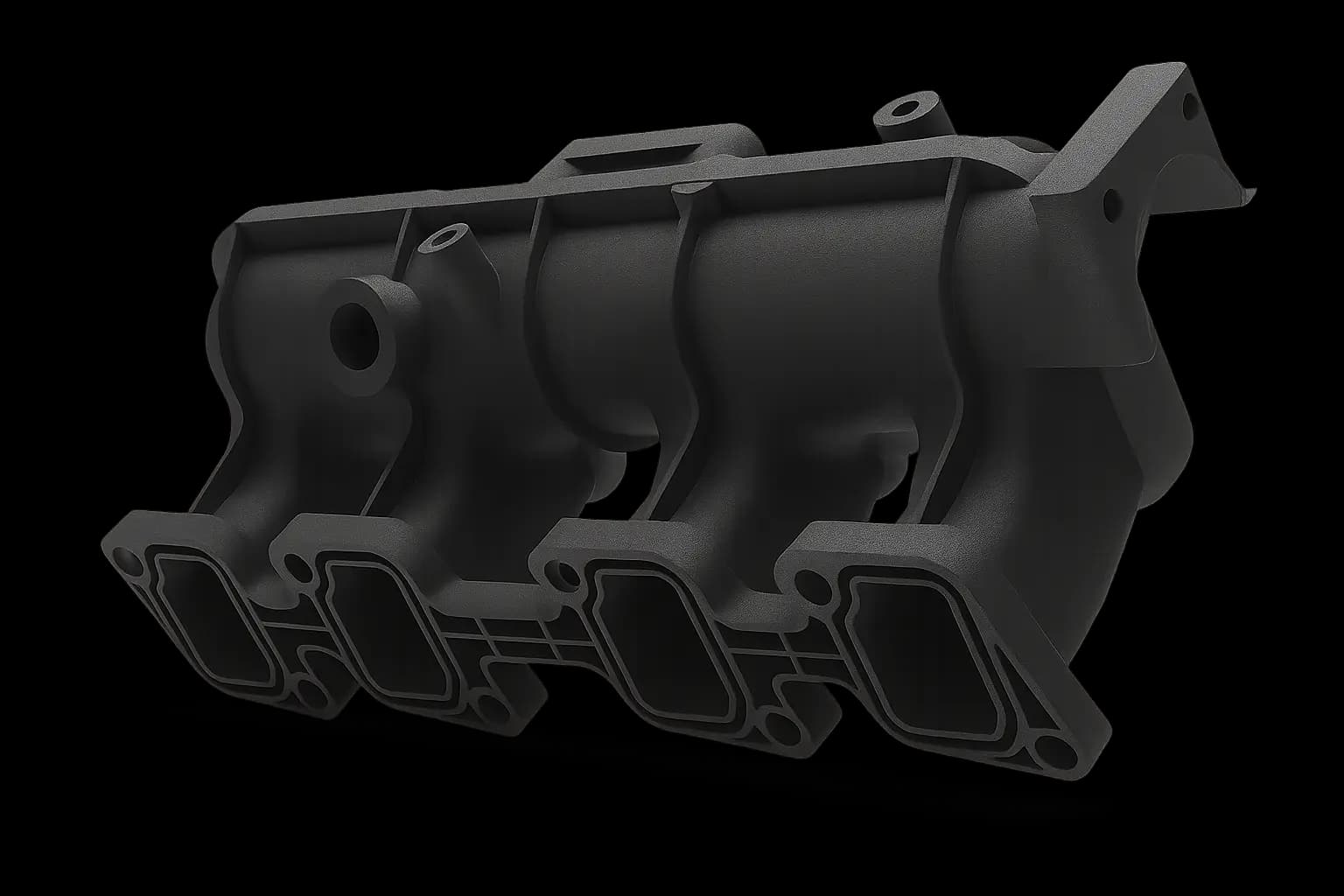
Nylon PA12
SLS nylon for functional prototypes
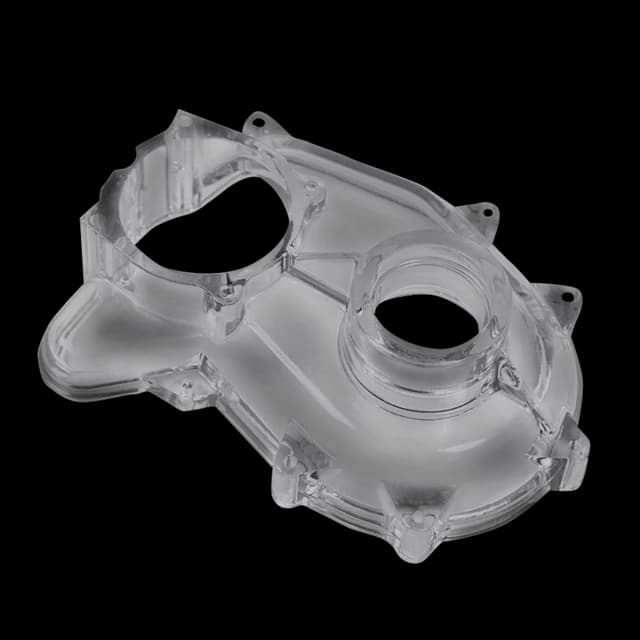
Accura ClearVue
Crystal clear SLA resin
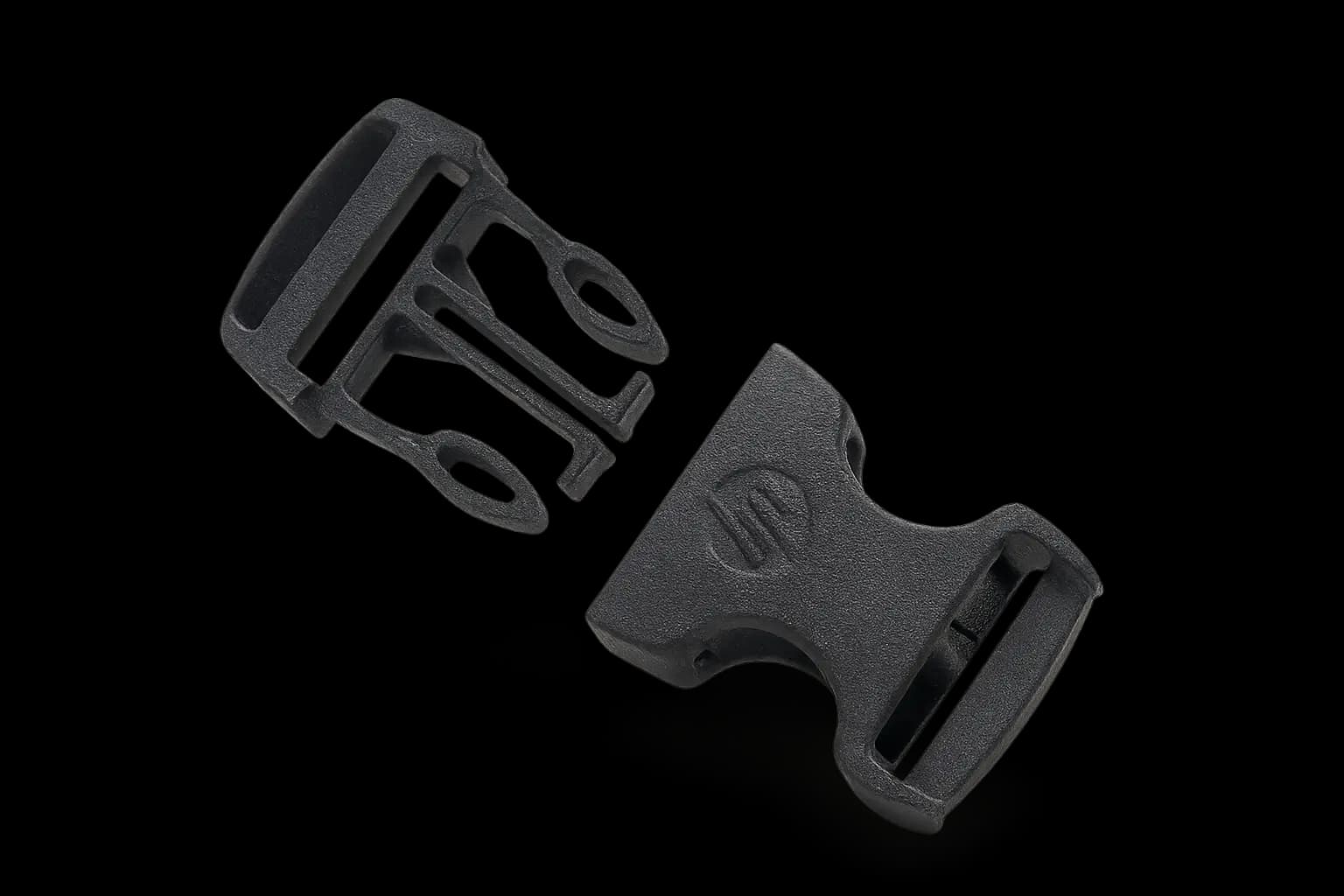
Glass Filled Nylon
High-strength composite
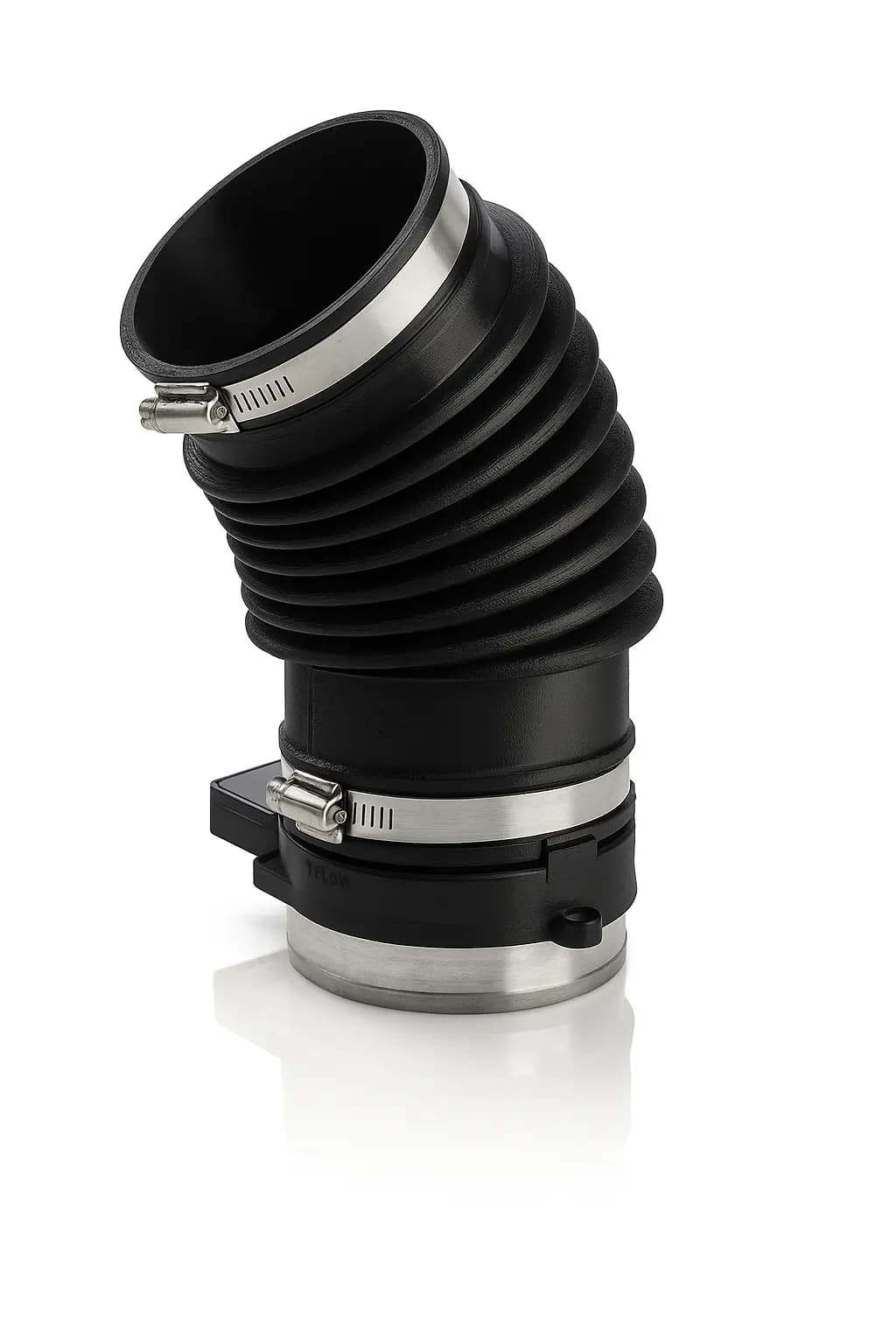
TPU 88A
Flexible elastomer
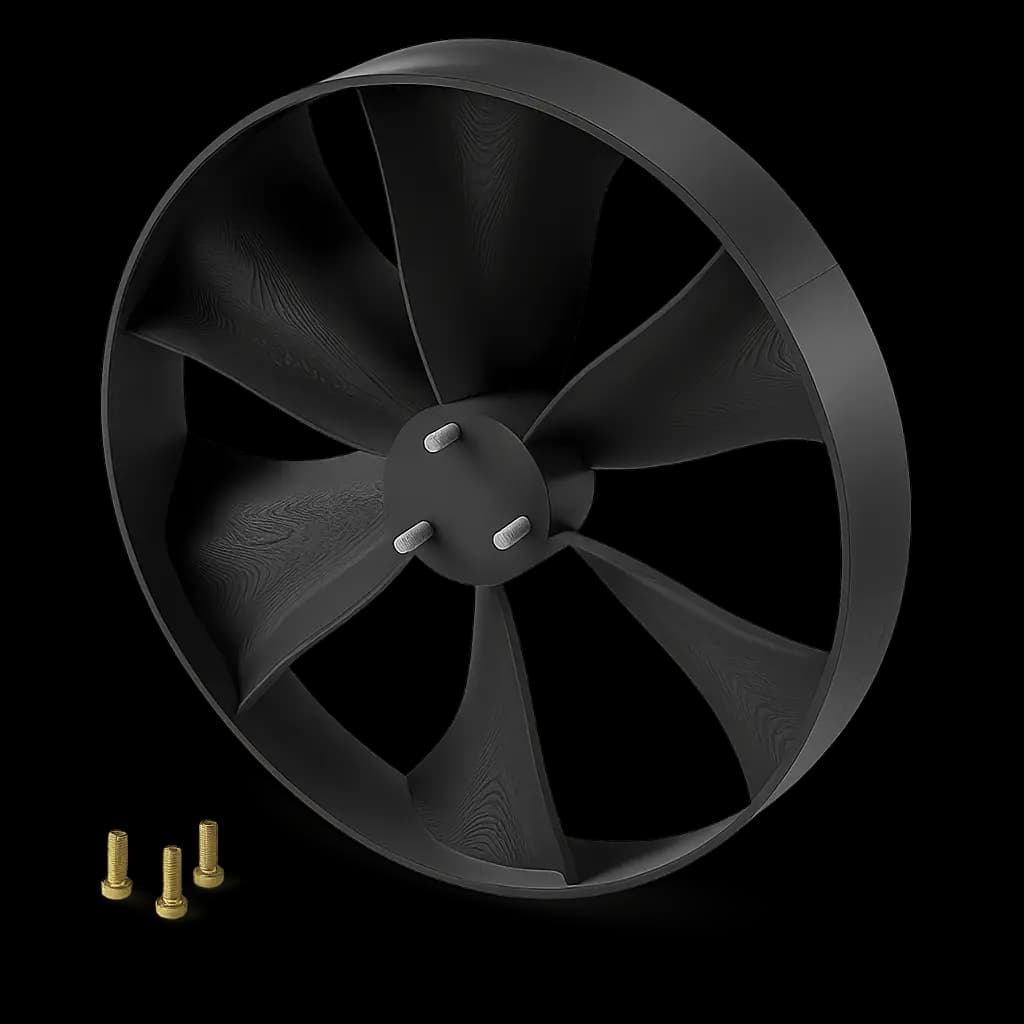
ABS
Engineering thermoplastic
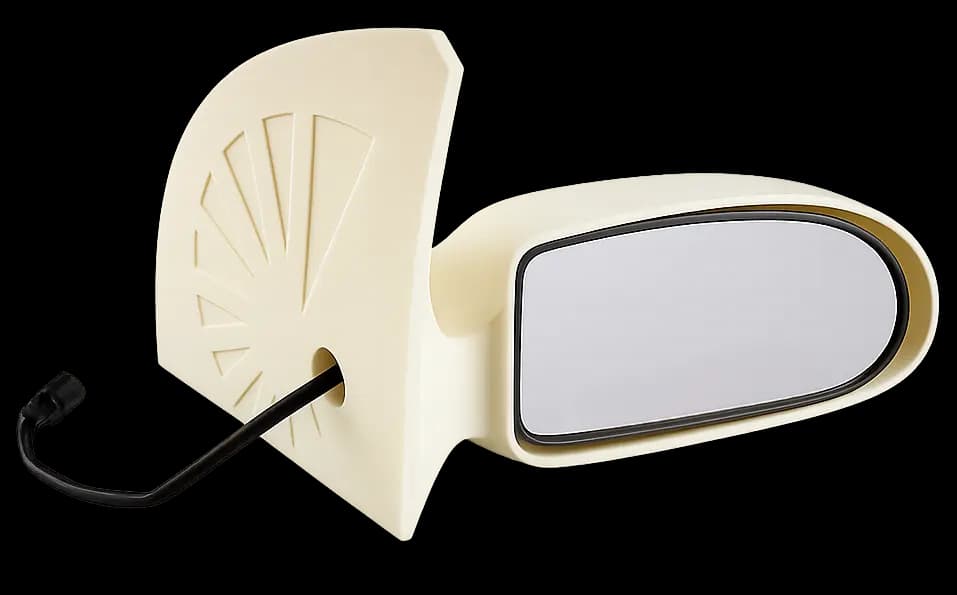
ASA
UV-stable thermoplastic
Explore Our Complete Material Matrix
Compare properties, applications, and certifications across our entire material portfolio. Filter by technology, industry, or specific requirements.
Success Stories
Real results from our industrial design partnerships
Outdoor Gear Development Program
Comprehensive prototyping program for North American outdoor gear brand, including snowboard binding components, bike frame assemblies, and field-ready equipment. Enabled rapid design iteration and real-world testing validation before production tooling investment.
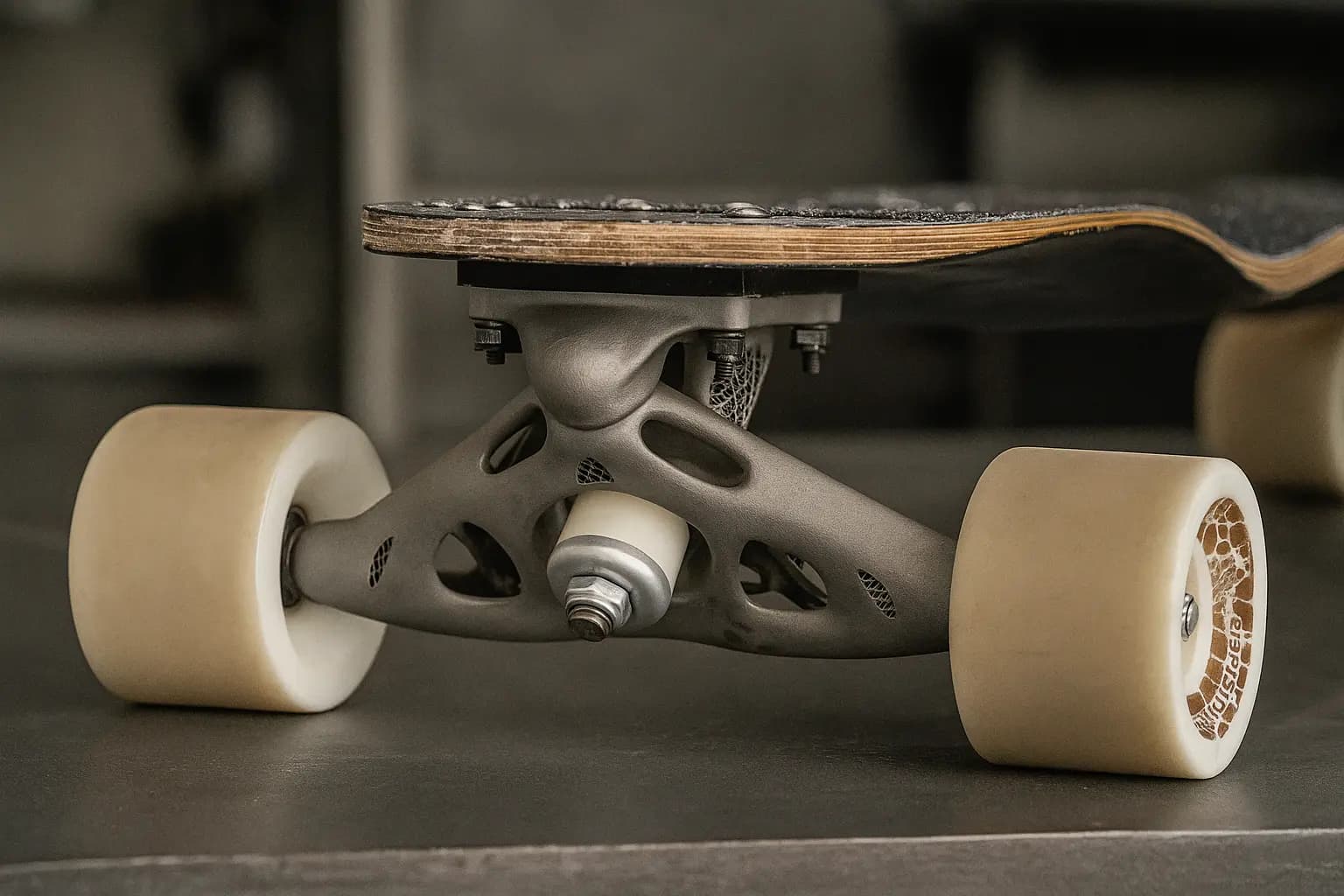
Consumer Electronics Prototyping
Rapid prototyping of wearable device housings and consumer electronics for tech startup, including functional assemblies with integrated mounting features, button mechanisms, and display housings. Accelerated time-to-market for investor demos and user testing.

Ready to Transform Your Industrial Design Manufacturing?
Upload your CAD files for an instant quote or speak with our application engineers about your specific requirements.
Click to start your quote
STL, STEP, OBJ, 3MF supported • Get instant pricing