Precision Additive Manufacturingfor Healthcare & Medical Devices
Forge Labs partners with medtech innovators to deliver high-performance prototypes, functional components, and short-run production parts using industrial 3D printing—all under ISO-aligned processes and cleanroom handling capabilities.
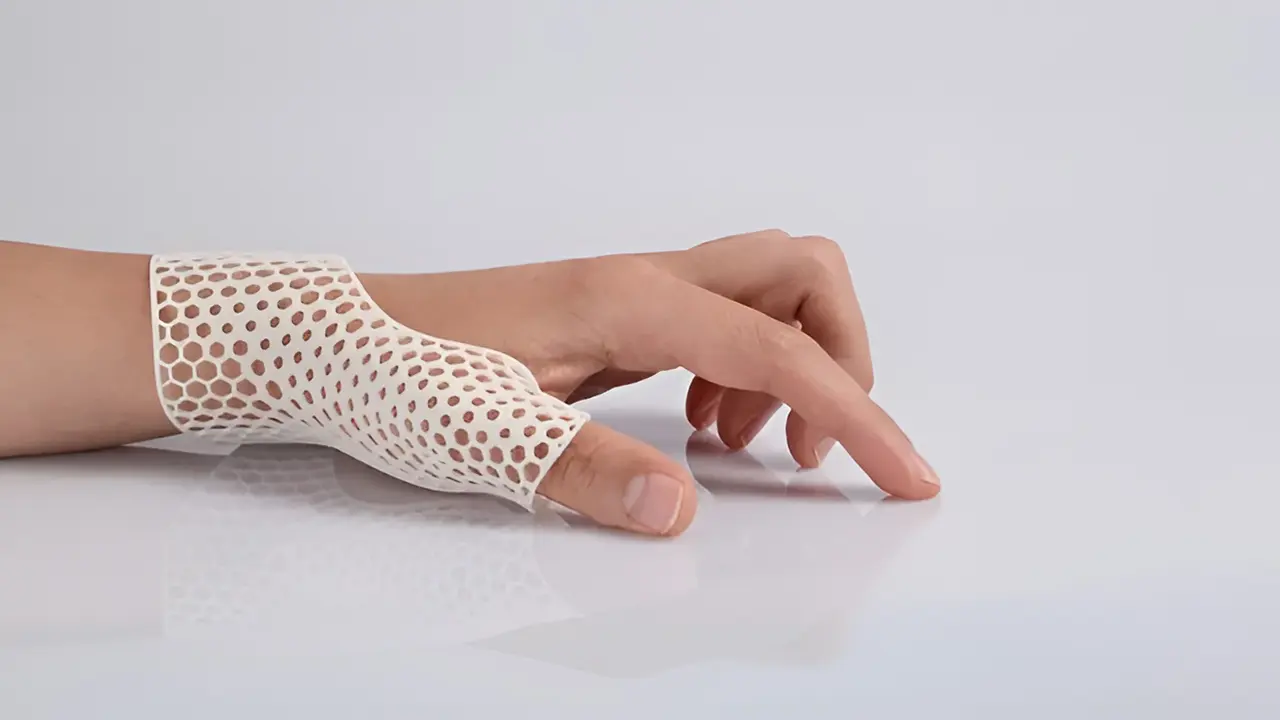
Healthcare & Medical Devices Excellence
Supporting Innovation in Medical Manufacturing
Healthcare moves fast—and medical device innovation demands rapid prototyping, precision engineering, and materials that meet strict performance and biocompatibility criteria. At Forge Labs, we help bridge the gap between concept and production with advanced additive manufacturing solutions tailored for the healthcare sector. From ventilator components and surgical prototypes to diagnostic housings and wearable enclosures, our experience spans early-stage design validation to functional parts that meet rigorous inspection standards.
Transforming Healthcare & Medical Devices Manufacturing
Healthcare moves fast—and medical device innovation demands rapid prototyping, precision engineering, and materials that meet strict performance and biocompatibility criteria. At Forge Labs, we help bridge the gap between concept and production with advanced additive manufacturing solutions tailored for the healthcare sector. From ventilator components and surgical prototypes to diagnostic housings and wearable enclosures, our experience spans early-stage design validation to functional parts that meet rigorous inspection standards.
Key Benefits of 3D Printing in Healthcare & Medical Devices
- Dramatically compress design and development cycles from weeks to days, accelerating time-to-market for critical medical innovations.
- Create complex internal geometries optimized for airflow, optical performance, or precise fluid management that are impossible with traditional manufacturing.
- Access a comprehensive range of functional materials including biocompatible, sterilizable, and regulatory-compliant options for medical applications.
- Eliminate expensive tooling investments, enabling cost-effective iterative prototyping and economical short-run production.
- Enable cost-efficient customization and patient-specific solutions without the traditional cost penalties of low-volume manufacturing.
- Leverage ISO 13485-aligned manufacturing processes with cleanroom handling capabilities for medical device compliance.
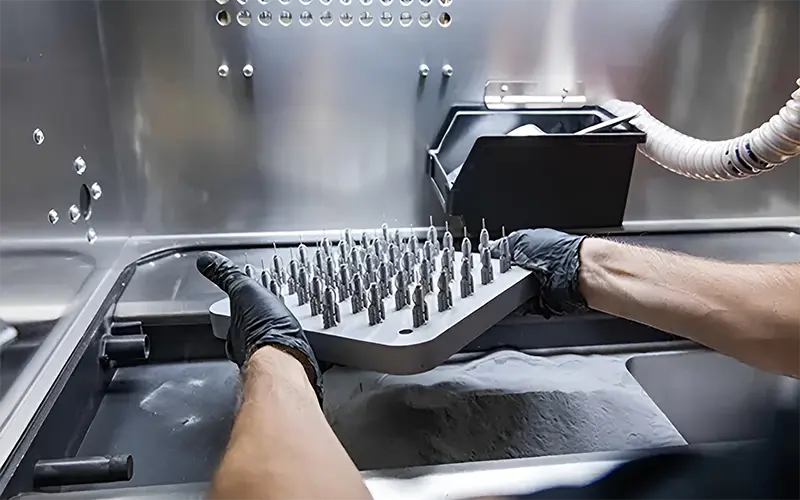
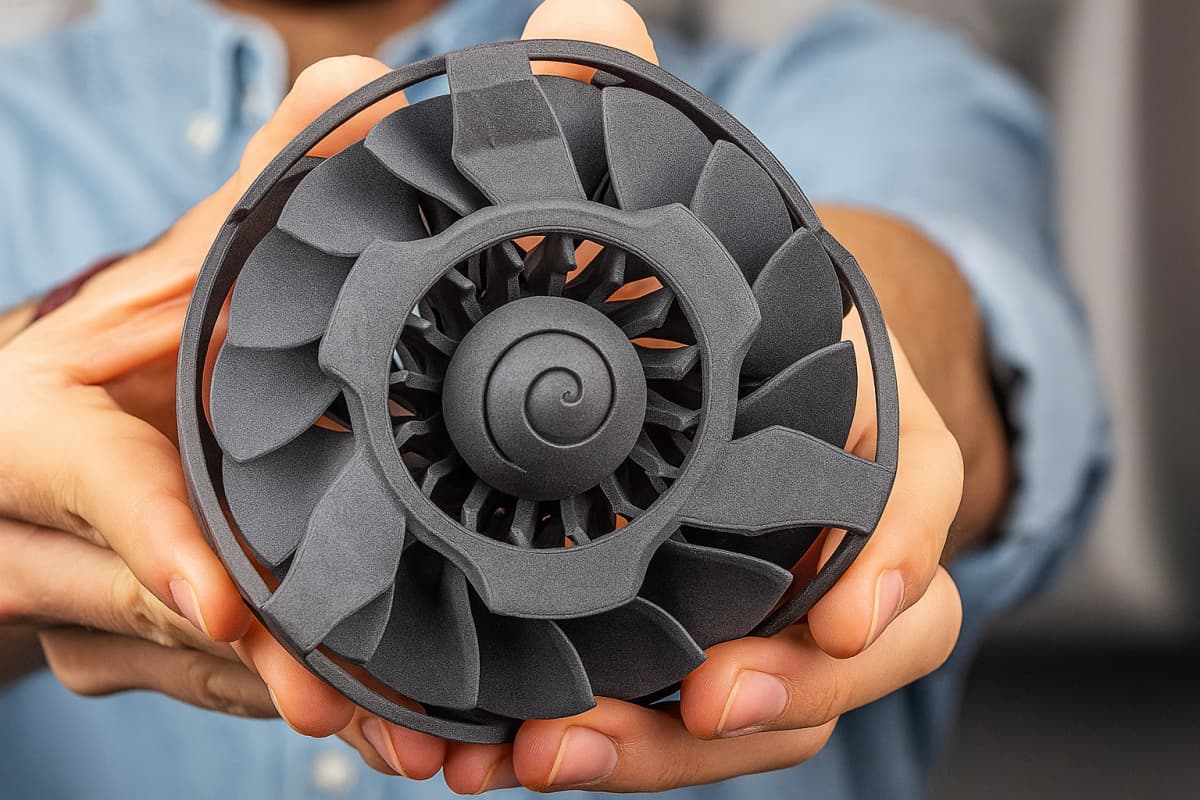
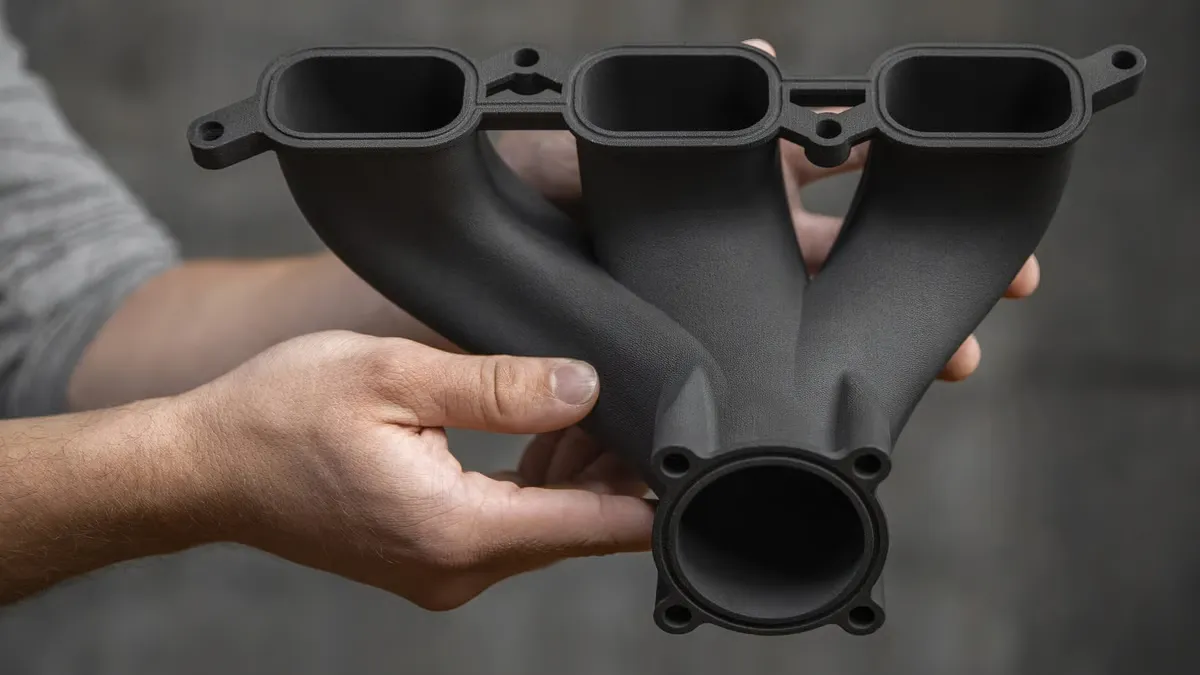
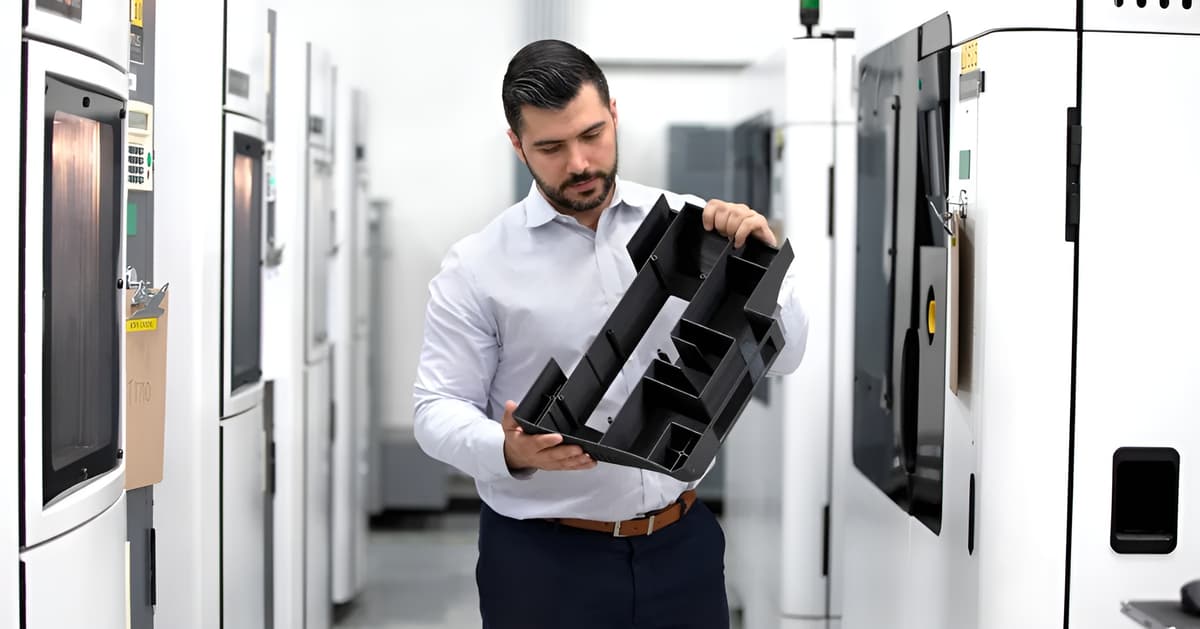
Industry Standards & Compliance
Certified for Healthcare & Medical Devices Excellence
Our manufacturing processes and quality systems meet the most stringent healthcare & medical devices industry standards, ensuring your parts are ready for critical applications.
ISO-Aligned Quality Processes
All medical parts manufactured under rigorous quality inspection aligned with ISO 9001 and ISO 13485 principles with controlled protocols.
Biocompatible Materials
USP Class VI certified materials with comprehensive biocompatibility testing and documentation for medical device applications.
Cleanroom Handling Capability
Controlled environment processing available for critical medical applications requiring contamination-free manufacturing and handling.
Material Traceability & Documentation
Complete dimensional inspection reports, material certifications, and batch traceability documentation provided upon request.
Manufacturing Capabilities
Advanced Healthcare & Medical Devices Solutions
From precision prototyping to full-scale production, our comprehensive capabilities deliver results that transform healthcare & medical devices manufacturing.
Stereolithography (SLA) with USP Class VI biocompatible resins accelerates medical device development with functional prototypes suitable for clinical evaluation and human factors testing. Tolerances as tight as ±0.2mm support precise fit requirements for surgical instruments and patient interfaces. High-definition surface finish eliminates post-processing for visualization studies, while multiple biocompatible material options enable testing across device applications. Digital design iteration reduces development timelines from months to days, supporting rapid innovation cycles critical in medical device development.
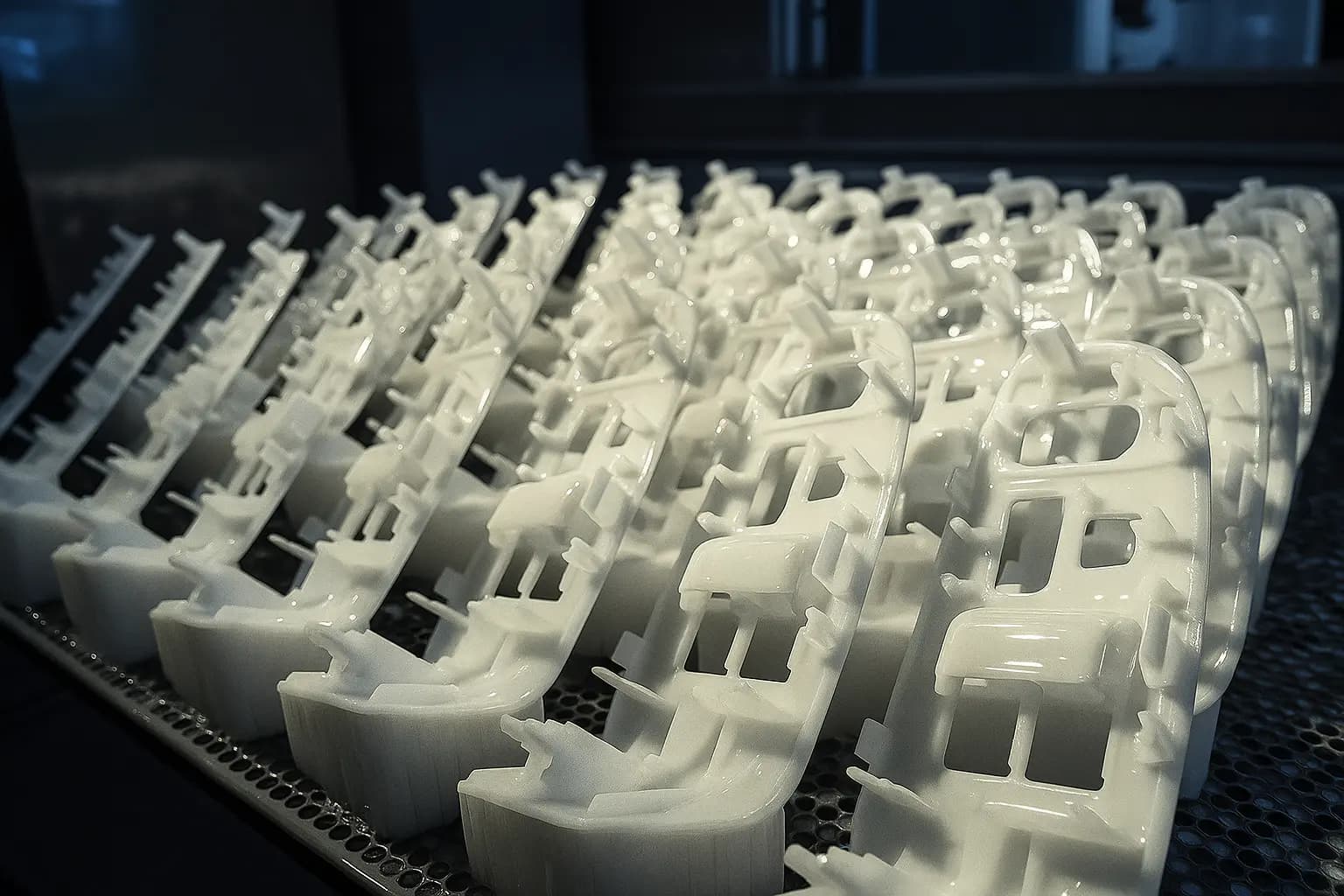
Technical Specifications
Accura ClearVue and specialized optical resins provide exceptional transparency and dimensional stability for diagnostic equipment housings, light guides, and optical assemblies. Materials achieve >95% light transmission while maintaining biocompatibility for patient-contact applications. Precision manufacturing ensures critical optical alignment features maintain tolerances throughout sterilization cycles. Custom geometries optimize light path efficiency and minimize optical losses in portable diagnostic devices. Post-processing options include optical polishing and anti-reflective coatings for enhanced performance.
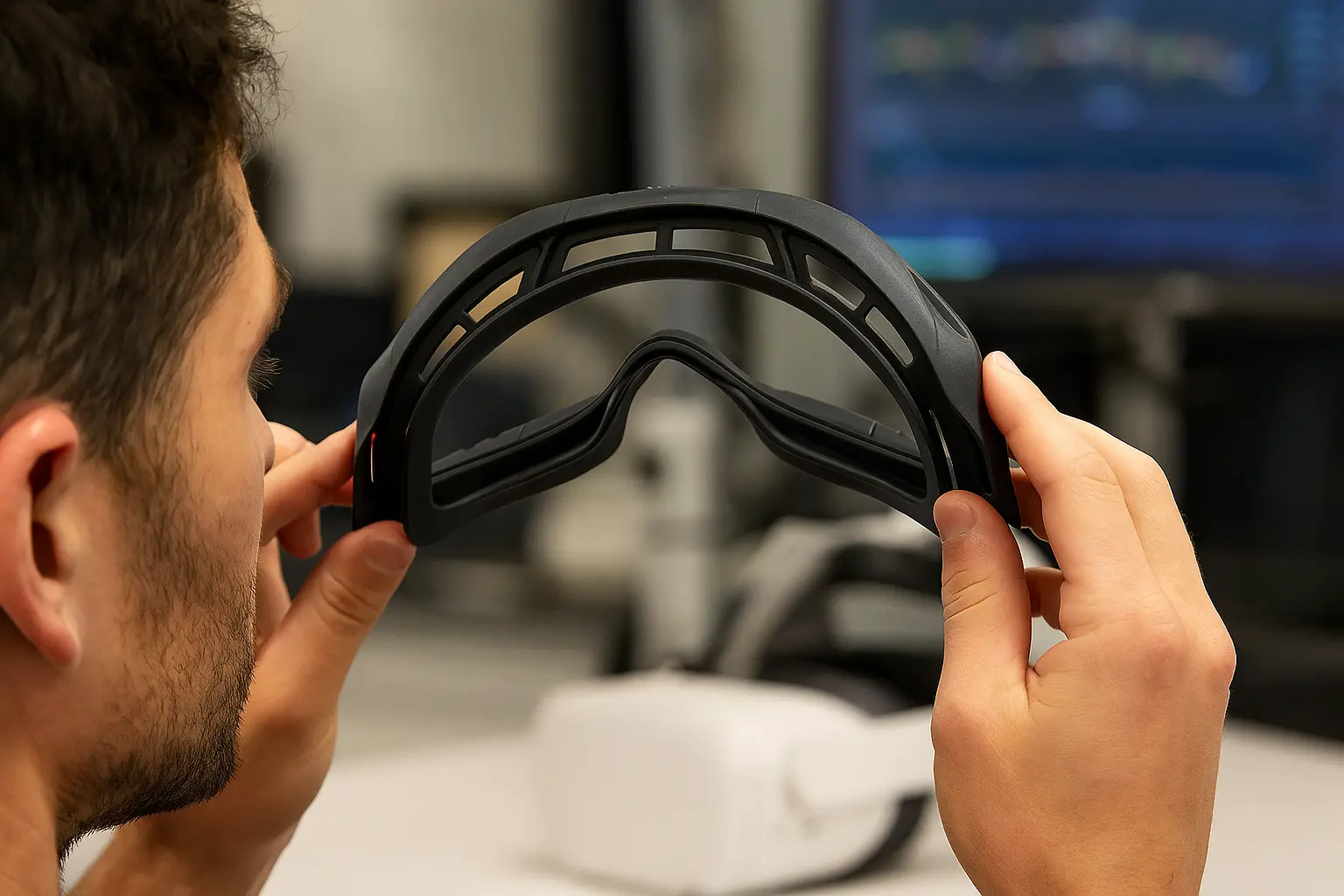
Technical Specifications
Selective laser sintering (SLS) with medical-grade PA12 nylon produces complex respiratory components with smooth internal airflow channels and precise dimensional control. Material properties include chemical resistance to disinfectants, steam sterilization compatibility, and excellent fatigue resistance for cyclic pressure applications. Internal channel geometries optimize laminar airflow while minimizing pressure drops across manifolds and valve assemblies. No support structures required enables complex geometries including integrated filters, flow sensors, and pressure relief features impossible with traditional manufacturing.
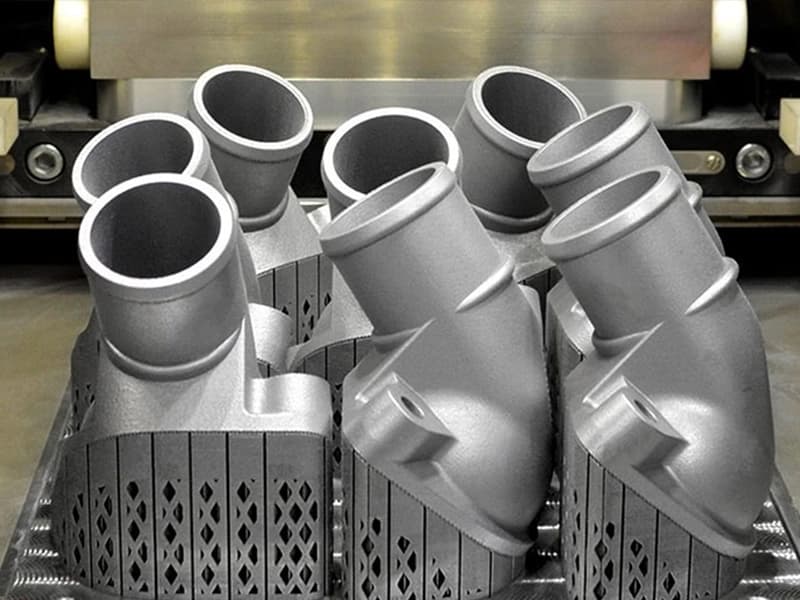
Technical Specifications
Flexible TPU materials and lightweight nylon enable patient-specific wearable device prototypes with anatomical conformance and comfort optimization. Flexible shore hardness options (70A-95A) accommodate varying compression requirements for monitoring devices, therapeutic equipment, and prosthetic interfaces. Design iteration supports anthropometric optimization across patient populations while maintaining consistent performance characteristics. Biocompatible formulations ensure skin compatibility for extended wear applications in research and clinical validation studies.
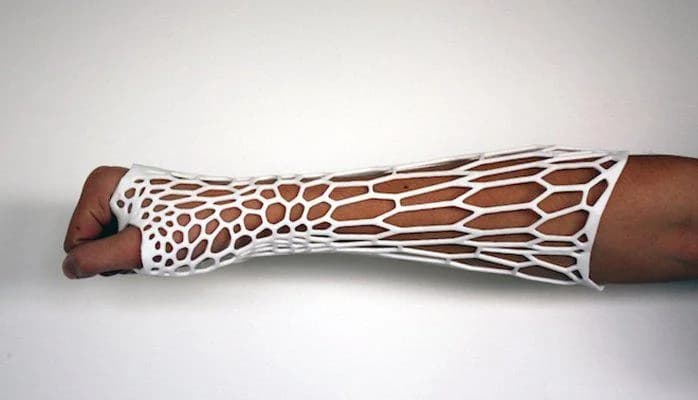
Technical Specifications
ISO 13485 quality management systems support cleanroom manufacturing for medical device pilot production and clinical trial components. Environmental controls maintain Class 10,000 (ISO 7) cleanliness standards with documented contamination control procedures. Material handling protocols ensure lot traceability from raw powder through final packaging with comprehensive documentation packages. Statistical process control monitoring validates dimensional consistency across production batches while maintaining full chain of custody for regulatory compliance. Cleanroom protocols accommodate volumes from 10 to 10,000+ parts with scalable quality assurance.
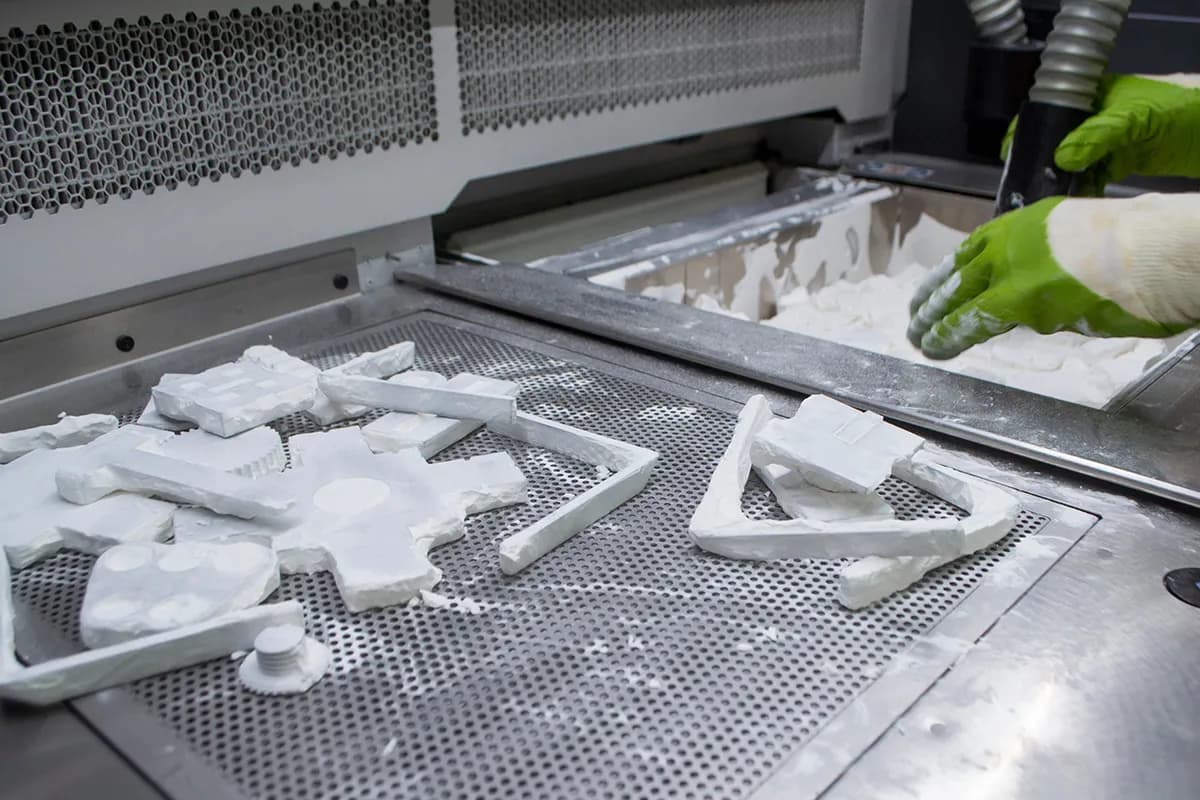
Technical Specifications
High-precision surgical guides and clinical instrumentation manufactured with dimensional accuracies suitable for patient-specific surgical planning and training applications. ULTEM and biocompatible materials withstand repeated sterilization cycles while maintaining dimensional stability and surface quality. Custom patient-specific geometries enable precise surgical placement of implants, optimize access angles, and reduce procedure time. Training models provide realistic tactile feedback with appropriate material properties for skill development and procedural validation in medical education programs.
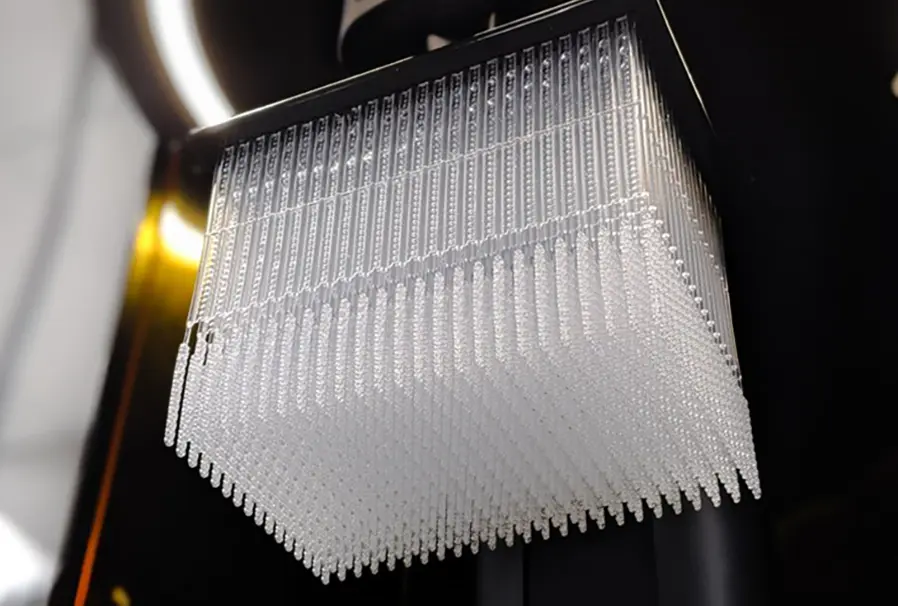
Technical Specifications
Manufacturing Technologies
Proven Technologies for Healthcare & Medical Devices
Each technology offers unique advantages for healthcare & medical devices applications. Choose the right process for your specific requirements.
Stereolithography
Ultra-high resolution resin printing for exceptional surface quality and fine detail. Perfect for concept models, visual...
Selective Laser Sintering
Support-free manufacturing of complex geometries with engineering-grade nylon materials. Ideal for functional prototypes...
Multi Jet Fusion
Precision engineering with fine detail resolution and excellent surface finish. Outstanding for mechanical assemblies, m...
Fused Deposition Modeling
Industry-leading precision with engineering thermoplastics and carbon fiber composites. Excellent for large-format proto...
Not sure which technology is right for your project?
Our application engineers can help you select the optimal manufacturing process based on your specific requirements, materials, and timeline.
Certified Materials
Healthcare & Medical Devices-Grade Materials
High-performance materials engineered and certified for demanding healthcare & medical devices applications with full traceability and compliance documentation.
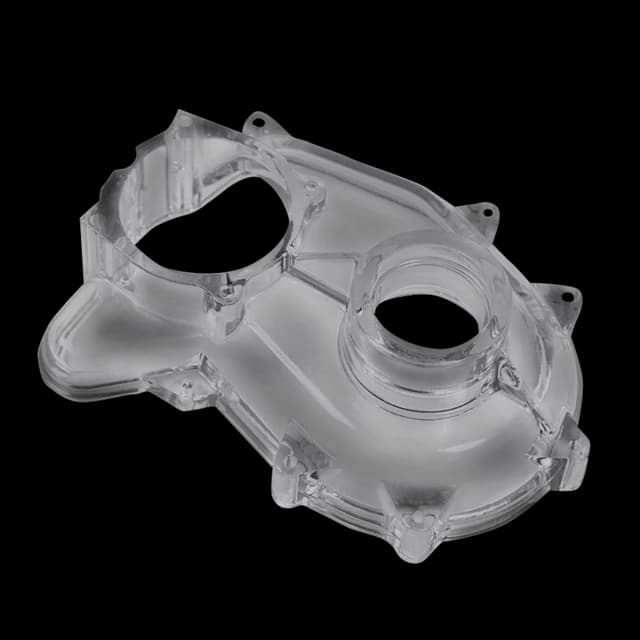
Accura ClearVue
Crystal clear biocompatible resin
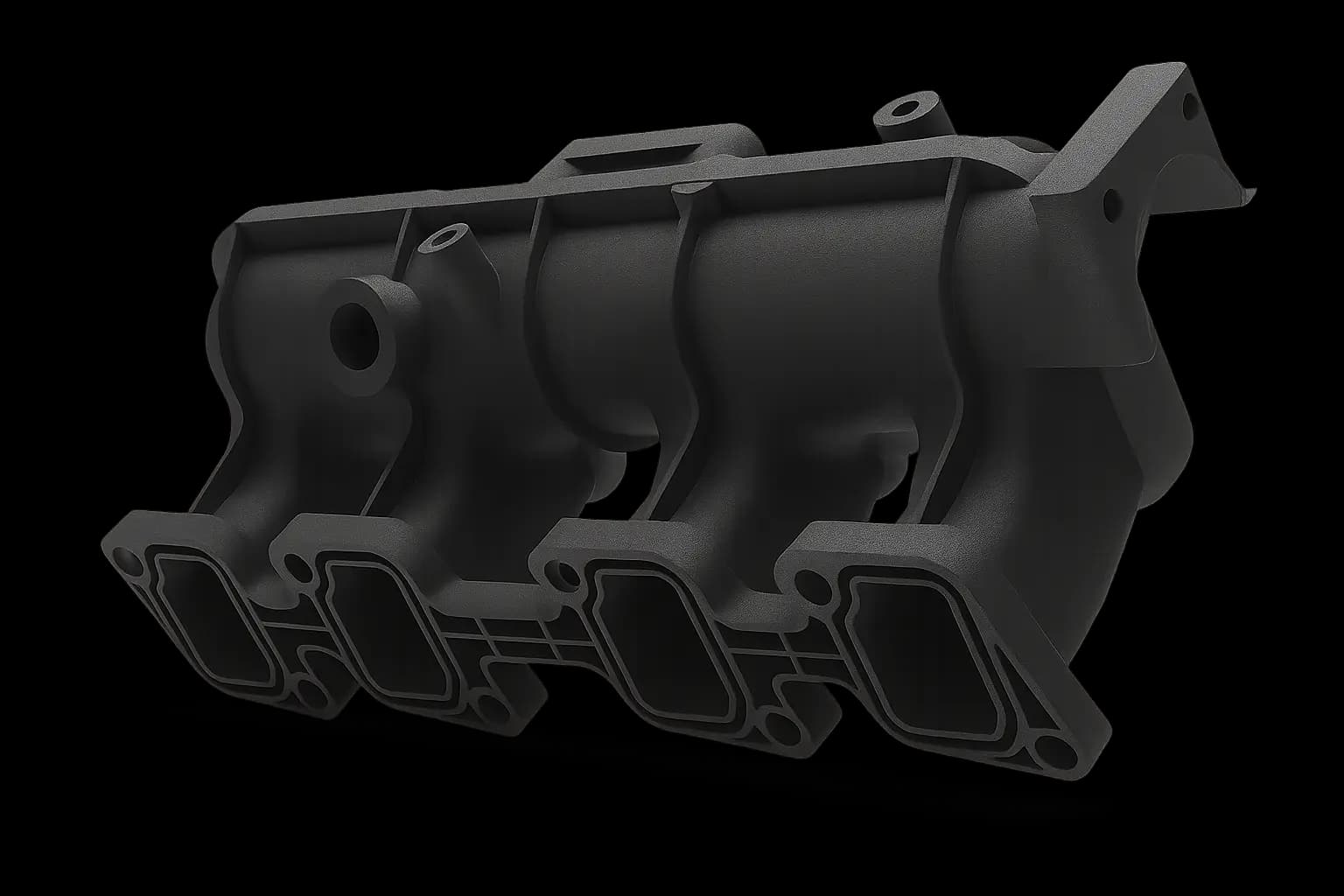
Nylon PA12
Biocompatible engineering grade
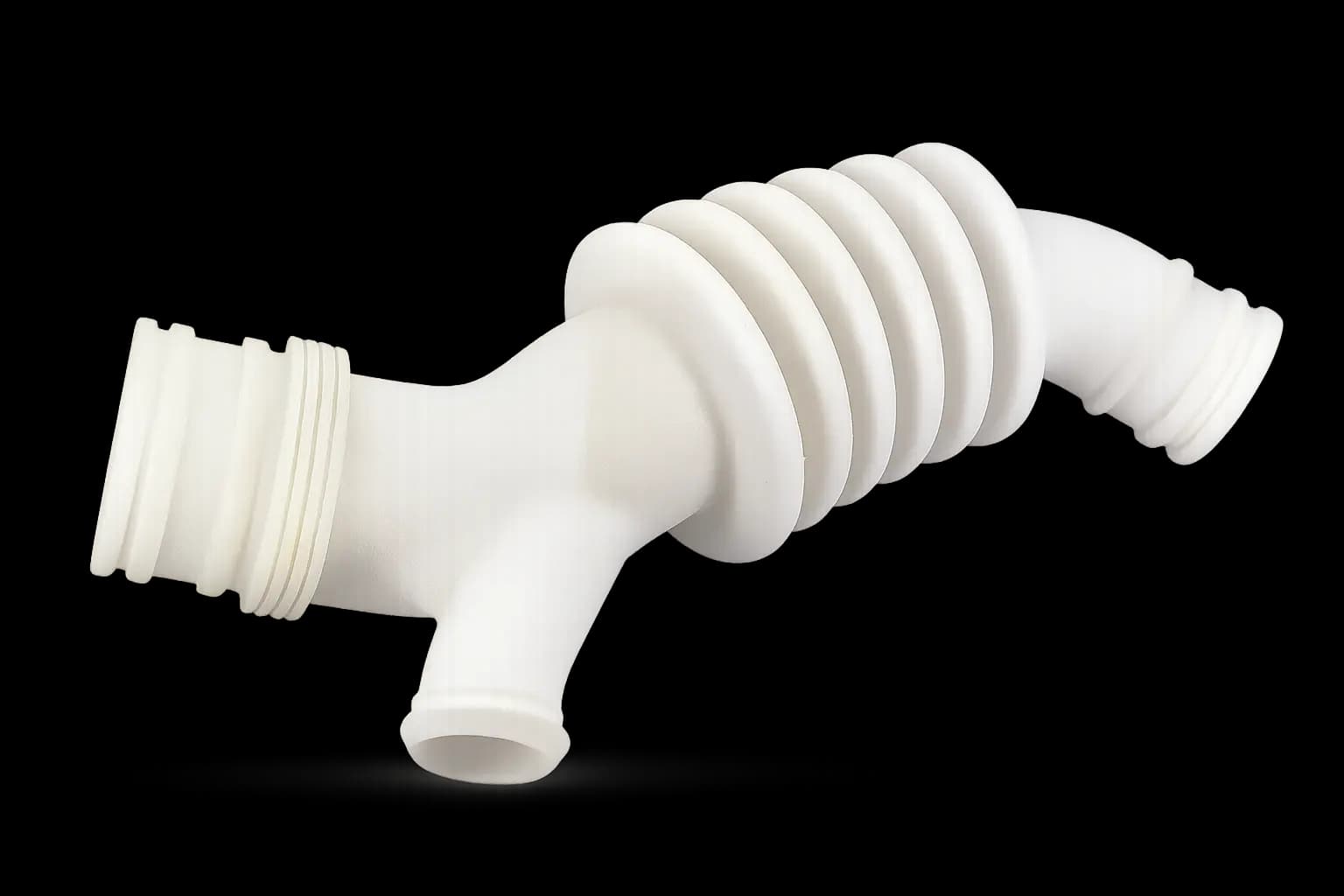
TPU Medical
Medical grade flexible polymer
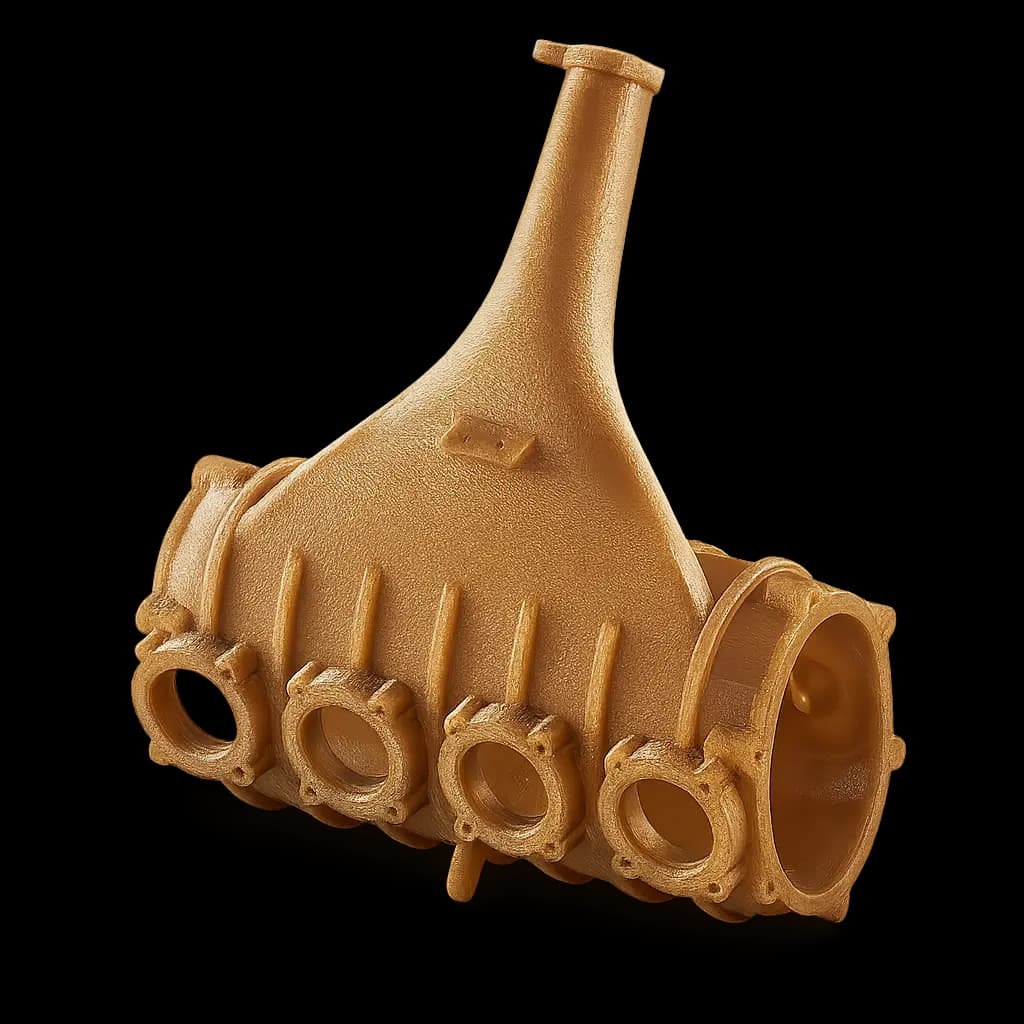
ULTEM 1010
High-performance thermoplastic
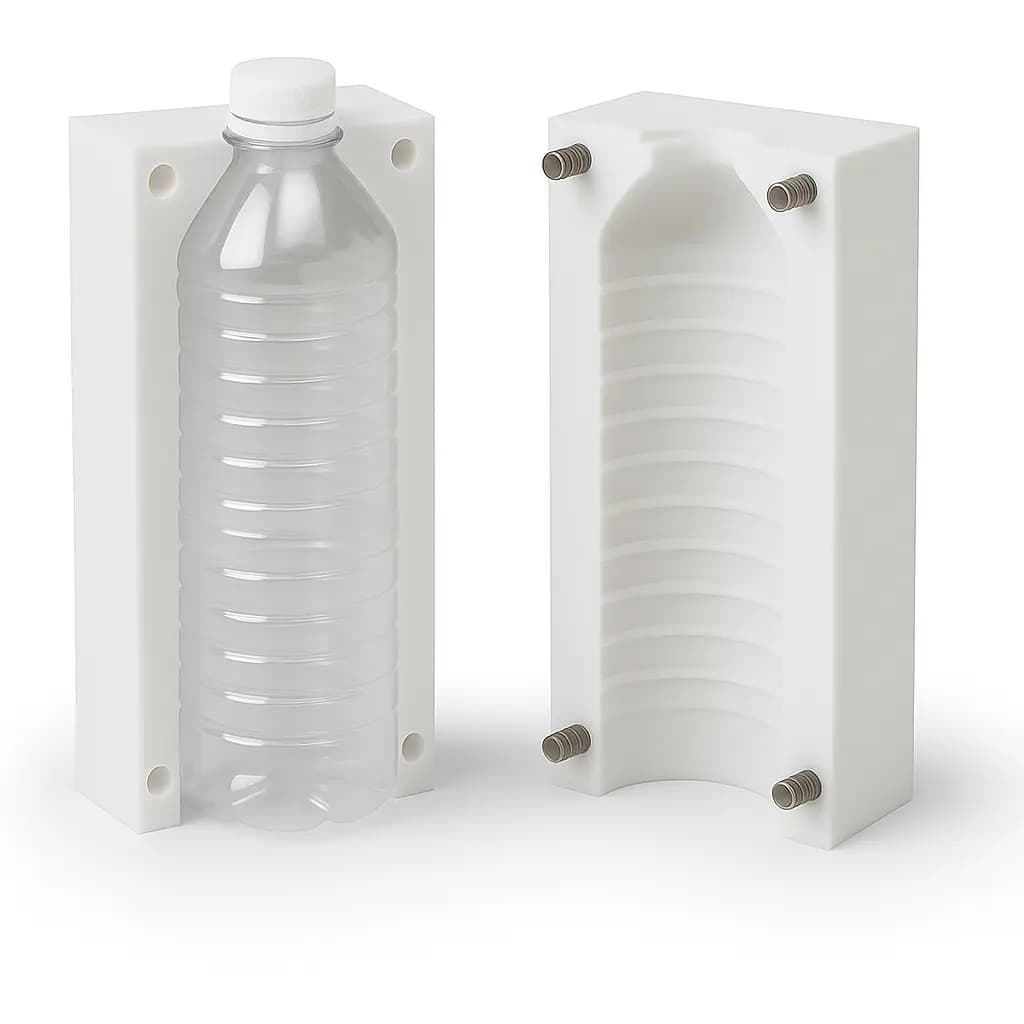
PC ISO
Medical grade polycarbonate
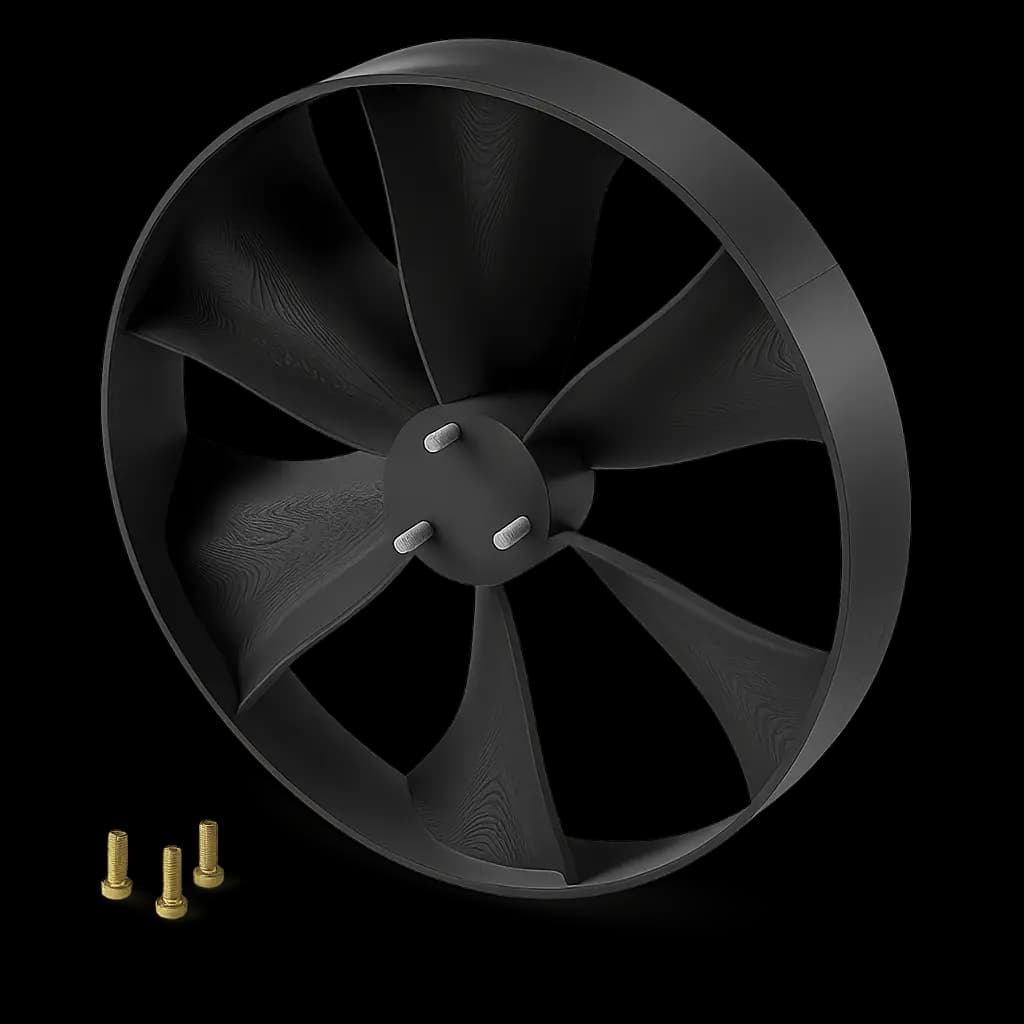
ABS M30i
Medical grade ABS
Explore Our Complete Material Matrix
Compare properties, applications, and certifications across our entire material portfolio. Filter by technology, industry, or specific requirements.
Success Stories
Real results from our healthcare & medical devices partnerships
Ventilator Component Development
Rapid prototyping and production of critical ventilator manifold components during global health crisis. Delivered functional parts with smooth internal airflow channels and biocompatible materials, enabling accelerated device deployment and patient care.
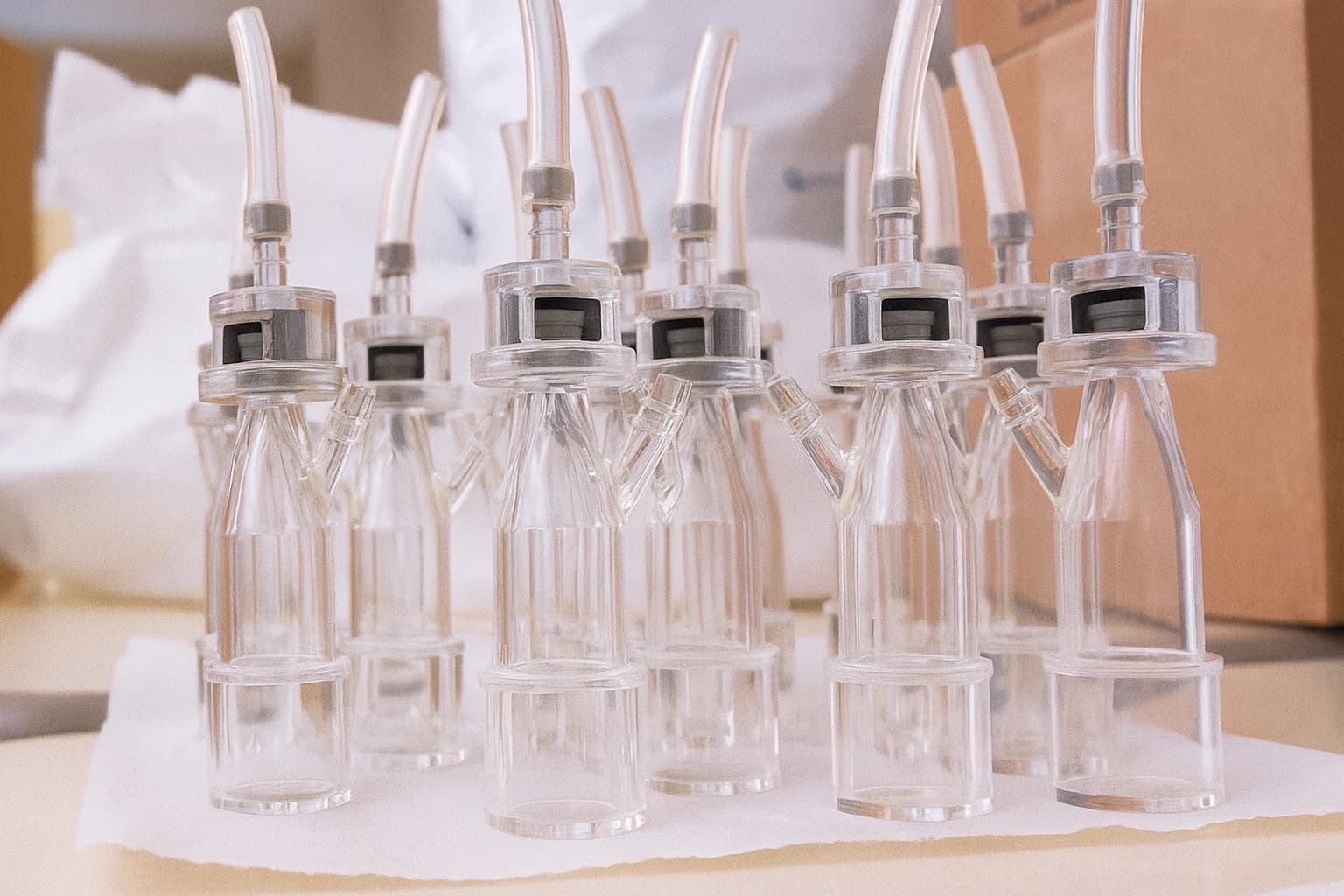
Diagnostic Equipment Housing
Custom optical housing for portable diagnostic device featuring integrated light guides and precise optical alignment features. Achieved optical clarity requirements while maintaining impact resistance for field use applications.
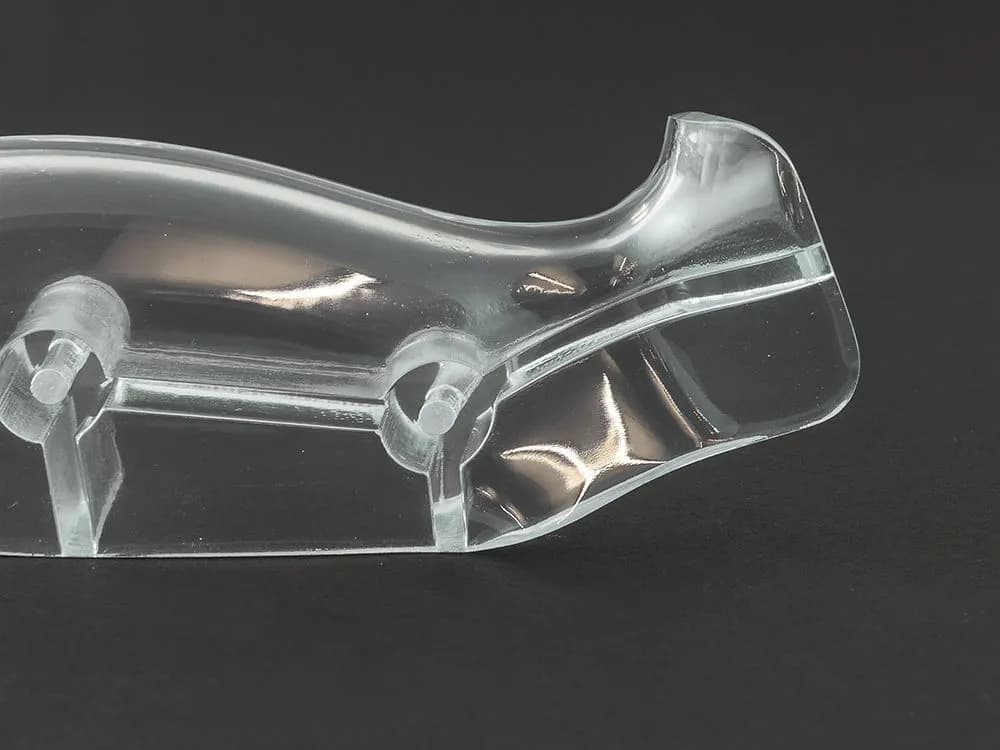
Ready to Transform Your Healthcare & Medical Devices Manufacturing?
Upload your CAD files for an instant quote or speak with our application engineers about your specific requirements.
Click to start your quote
STL, STEP, OBJ, 3MF supported • Get instant pricing