Industry Revolution in Progress
The medical device manufacturing industry is experiencing unprecedented transformation through additive manufacturing. With global medical 3D printing projected to reach $3.5 billion by 2025, traditional manufacturing paradigms are being challenged by the precision, customization, and efficiency of modern 3D printing technologies.
The design of medical devices represents one of the most challenging endeavors in modern manufacturing. These critical components must meet rigorous FDA standards, interface seamlessly with diverse human anatomies, and perform complex functions where failure is not an option. Additive manufacturing has emerged as a transformative solution, overcoming traditional constraints and enabling innovations that were previously impossible with conventional manufacturing methods.
From patient-specific prosthetics that restore mobility and confidence to biocompatible implants that integrate seamlessly with human tissue, 3D printing is redefining what's possible in medical device development. This comprehensive analysis explores the profound impact of additive manufacturing across the entire medical device ecosystem, examining current applications, technological breakthroughs, regulatory considerations, and future innovations that will shape the industry.
Article Navigation
Patient-Specific Customization Revolution
The fundamental advantage of additive manufacturing in medical device production lies in its unparalleled ability to create patient-specific solutions. Unlike traditional manufacturing methods that rely on standardized dimensions and one-size-fits-all approaches, 3D printing enables the production of devices tailored precisely to individual patient anatomy, physiology, and pathological conditions.
Customization Capabilities by Technology
Stereolithography (SLA)
High-resolution biocompatible resins, dimensional accuracy ±0.1mm
Selective Laser Sintering (SLS)
Nylon-based prosthetics, functional end-use parts
Direct Metal Laser Sintering (DMLS)
Titanium implants, surgical instruments
Multi-Jet Fusion (MJF)
Functional prosthetics, orthotic devices
Advanced Prosthetic Solutions
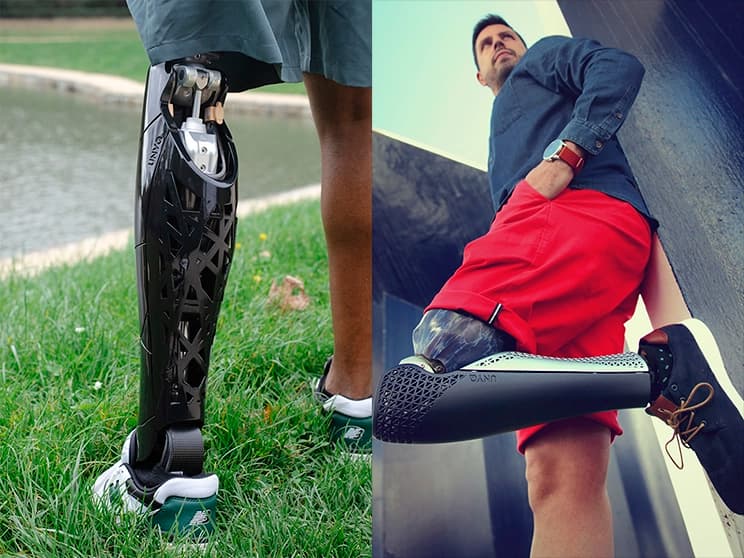
Custom prosthetic covers designed for individual style preferences
Modern prosthetic development has been revolutionized through additive manufacturing technologies that enable the creation of lightweight, durable, and highly personalized limb replacements. Companies like UNYQ have pioneered the integration of 3D scanning and printing technologies to produce prosthetic covers that not only restore functionality but also reflect individual personality and style preferences.
The technical specifications for 3D printed prosthetics have advanced significantly, with modern devices achieving weight reductions of up to 40% compared to traditional alternatives while maintaining superior durability. Advanced materials such as carbon fiber-reinforced nylon and thermoplastic polyurethane (TPU) provide the necessary flexibility and strength for daily use applications.
Precision Hearing Aid Manufacturing
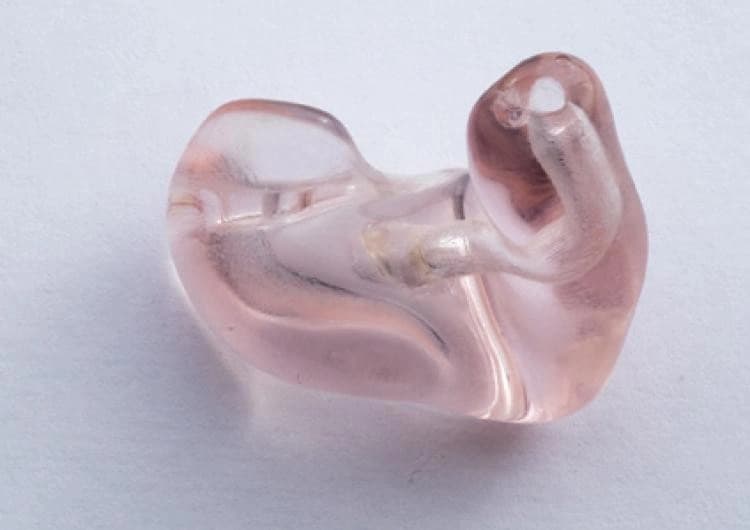
Precision-manufactured hearing aids with custom ear canal fitting
The hearing aid industry has experienced one of the most successful implementations of additive manufacturing in medical device production. Leading manufacturers like Sonova have achieved remarkable scale, producing over one million custom hearing aids annually through stereolithography processes that ensure perfect anatomical fit for each patient's unique ear canal geometry.
The precision achievable through SLA technology enables dimensional tolerances within ±0.05mm, ensuring optimal acoustic performance and patient comfort. This level of accuracy is impossible to achieve through traditional manufacturing methods, highlighting the transformative impact of additive manufacturing in hearing aid production.
Dental Restoration Innovation
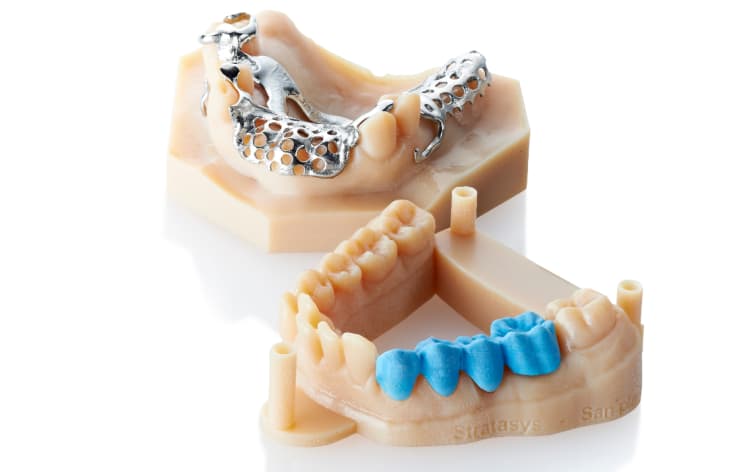
3D printed dental models for restoration planning
Digital dentistry represents one of the fastest-growing applications of 3D printing in healthcare, with companies like Align Technology demonstrating the scalability of additive manufacturing by producing over 500,000 clear aligners daily. This unprecedented production volume showcases the maturity of 3D printing technologies in medical device manufacturing.
Modern dental restorations including crowns, bridges, and implant components are now routinely produced using biocompatible ceramics and metal alloys through additive processes. These custom-manufactured components achieve superior fit, function, and aesthetics compared to traditional dental prosthetics, while significantly reducing production timelines from weeks to days.
Advanced Rapid Prototyping Solutions
Rapid prototyping capabilities in medical device development have transformed the traditional design-to-market timeline, enabling manufacturers to iterate designs quickly, test functionality comprehensively, and validate performance before committing to expensive tooling and mass production processes. This acceleration in development cycles has become crucial in responding to emerging healthcare needs and regulatory requirements.
Drug Delivery System Development
Pharmaceutical companies have embraced additive manufacturing for developing sophisticated drug delivery systems that provide precise dosing control and improved patient compliance. GlaxoSmithKline's innovative approach to inhaler prototyping demonstrates how 3D printing enables the integration of sensors and monitoring capabilities directly into drug delivery devices.
These smart inhalers, prototyped using advanced stereolithography resins, can track medication adherence patterns and provide real-time feedback to healthcare providers. The rapid prototyping capabilities allow for extensive user testing and ergonomic optimization before finalizing device designs for regulatory submission.
Surgical Instrument Innovation
Surgical instrument development has been significantly enhanced through additive manufacturing capabilities that enable the creation of procedure-specific tools and patient-specific surgical guides. Companies like OssDsign utilize 3D printing to develop custom surgical guides that ensure precise implant placement with accuracy levels exceeding traditional surgical techniques.
These surgical guides, manufactured using biocompatible stereolithography resins, undergo sterilization processes and provide surgeons with patient-specific anatomical references that reduce operative time and improve surgical outcomes. The ability to prototype and test these guides rapidly accelerates the surgical planning process significantly.
Anatomical Model Production
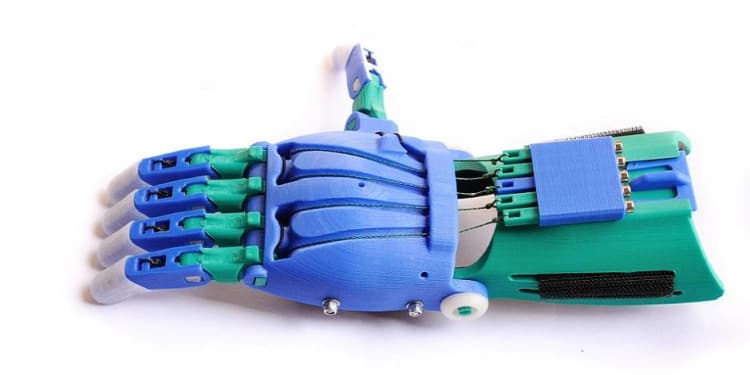
Advanced prosthetic hand with 3D printed mechanical components
Medical education and surgical planning have been revolutionized through the production of highly detailed anatomical models that replicate patient-specific pathologies and anatomical variations. Materialise, a leader in medical 3D printing services, produces anatomical models that enable surgeons to practice complex procedures and develop optimal surgical approaches before entering the operating room.
These models, created using patient CT and MRI data, provide tactile feedback and visual references that significantly improve surgical outcomes. The rapid production capabilities of modern 3D printing technologies enable same-week delivery of patient-specific models, supporting time-critical surgical planning requirements.
Future Technological Innovations
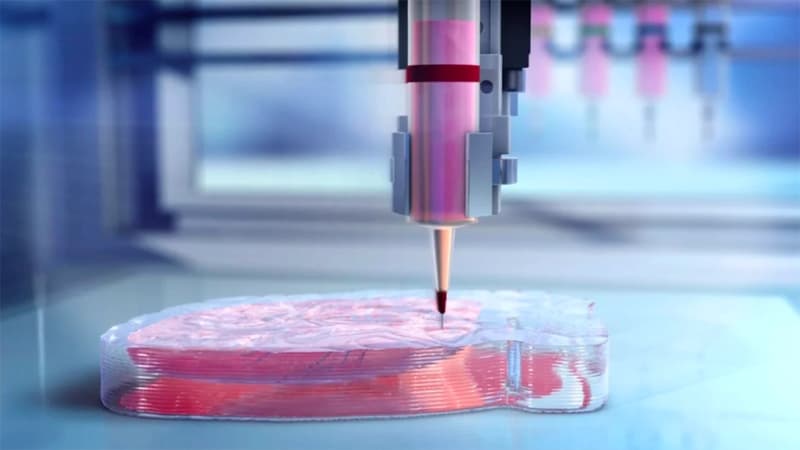
Advanced bioprinting technology for tissue engineering applications
The future of 3D printing in medical device manufacturing promises revolutionary advances that will fundamentally transform healthcare delivery and patient outcomes. Emerging technologies including bioprinting, smart materials, and integrated electronics are opening new possibilities for personalized medicine and regenerative therapies.
Bioprinting and Tissue Engineering
Companies like BIOLIFE4D are pioneering bioprinting technologies that enable the creation of living tissue constructs for medical research and therapeutic applications. These bioengineered heart models provide researchers with physiologically relevant platforms for drug testing and disease modeling that closely replicate human cardiac function.
The integration of multiple cell types, growth factors, and biocompatible scaffolds creates complex tissue architectures that support cellular proliferation and differentiation. Future developments in this field may enable the production of transplantable organs and tissues that eliminate rejection risks and organ shortage challenges.
Antimicrobial Surface Technologies
Research teams at the University of Sheffield have developed 3D printable compounds with inherent antimicrobial properties that can eliminate common pathogens including E. coli and Staphylococcus aureus. These materials incorporate antimicrobial agents directly into the polymer matrix, providing long-lasting infection resistance for medical implants and surgical instruments.
The antimicrobial efficacy is achieved through controlled release mechanisms that maintain therapeutic concentrations at the device surface while minimizing systemic exposure. This technology has significant potential for reducing healthcare-associated infections and improving patient outcomes in surgical applications.
Integrated Sensor Technologies
Stanford University researchers have demonstrated the feasibility of 3D printing flexible sensors directly onto moving organs, enabling real-time monitoring of vital physiological parameters. These sensors can track cardiac strain, blood pressure fluctuations, and oxygen saturation levels with unprecedented accuracy and minimal tissue disruption.
The sensor technology utilizes biocompatible conductive polymers and flexible substrates that conform to organ surfaces without affecting normal physiological function. Future applications may include permanent monitoring systems for chronic disease management and early detection of medical emergencies.
Forge Labs: Your Partner in Medical Device Innovation
The transformative impact of 3D printing on the medical device industry represents one of the most significant technological advances in modern healthcare. From personalized prosthetics to biocompatible implants, additive manufacturing has proven its ability to improve patient outcomes while reducing costs and accelerating innovation cycles.
As the industry continues to evolve with projected growth to $60 billion by 2030, medical device manufacturers must embrace these technologies to remain competitive and deliver superior patient care. The regulatory framework continues to mature, providing clearer pathways for bringing innovative 3D printed medical devices to market.
Ready to Explore Medical Device 3D Printing?
Our biocompatible Accura Clearvue material is specifically designed for medical applications, offering USP Class VI certification and exceptional dimensional accuracy for surgical guides, anatomical models, and temporary implants.
Contact our medical device specialists to discuss your project requirements and explore how additive manufacturing can enhance your product development process.