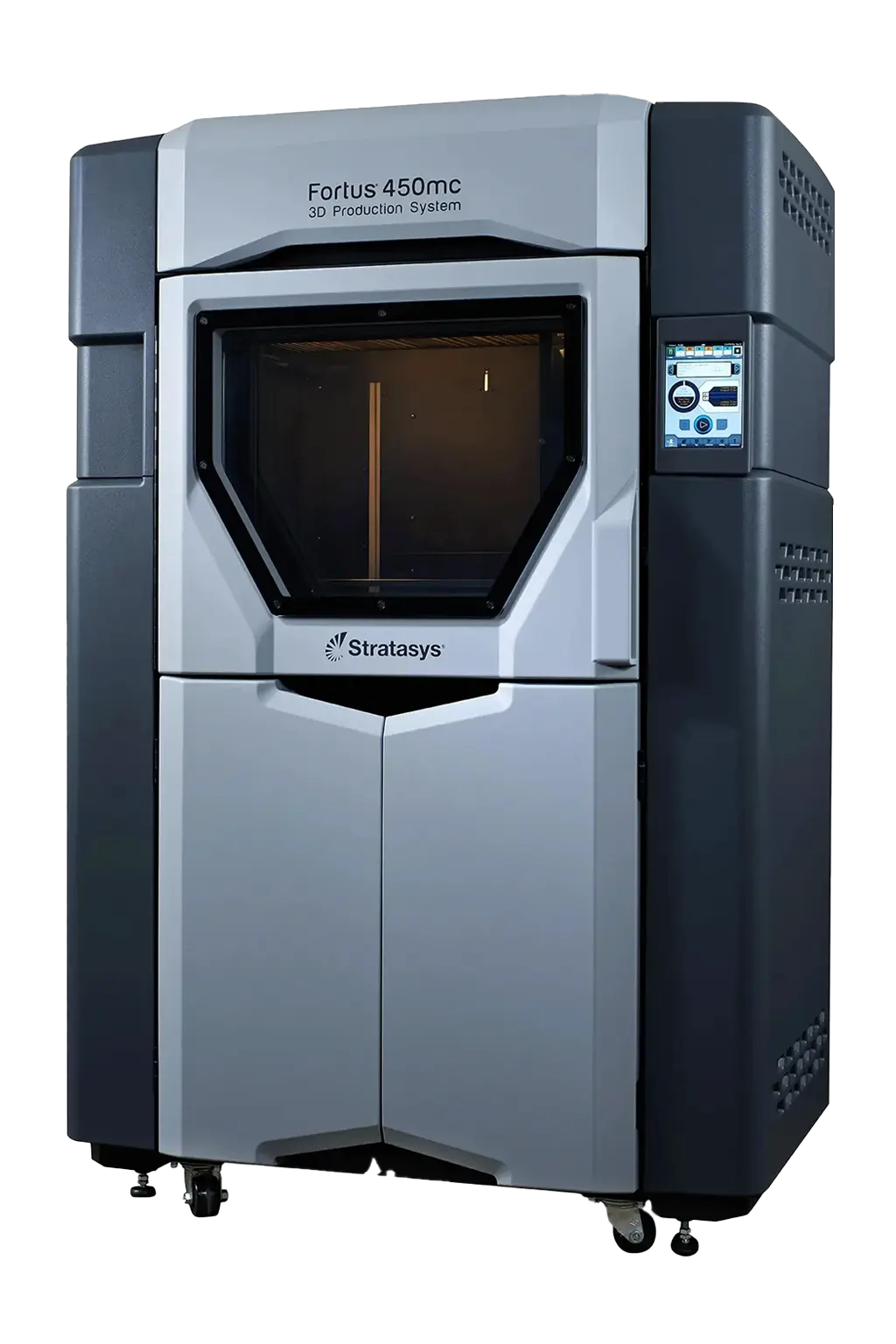
Fused Deposition Modeling3D Printing for Functional Prototypes & Large Parts
Industry-leading precision with best-in-class repeatability and layer adhesion. Manufacture using industrial-grade thermoplastics like ABS, ASA, PC, and ULTEM up to 36" × 24" × 36".
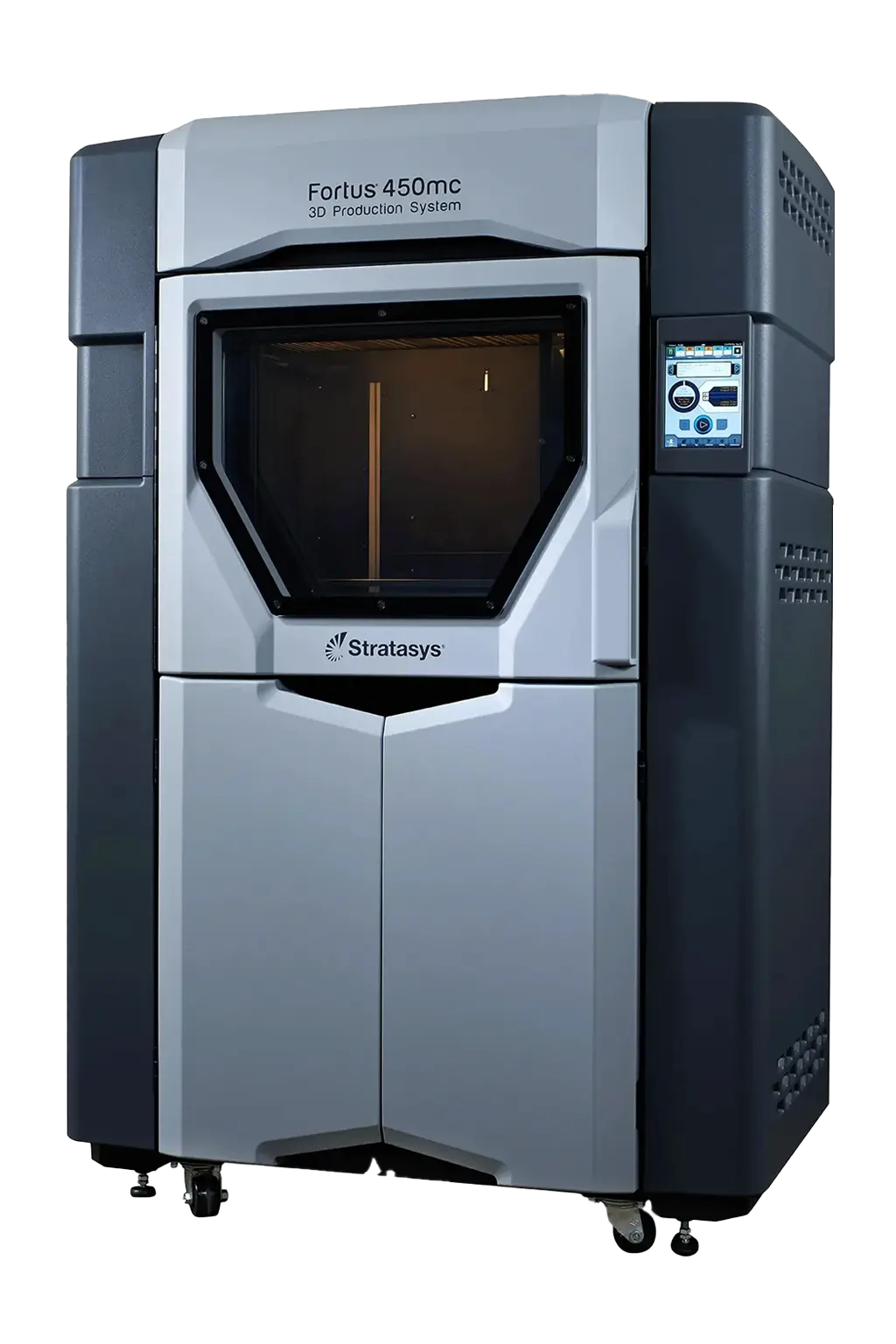
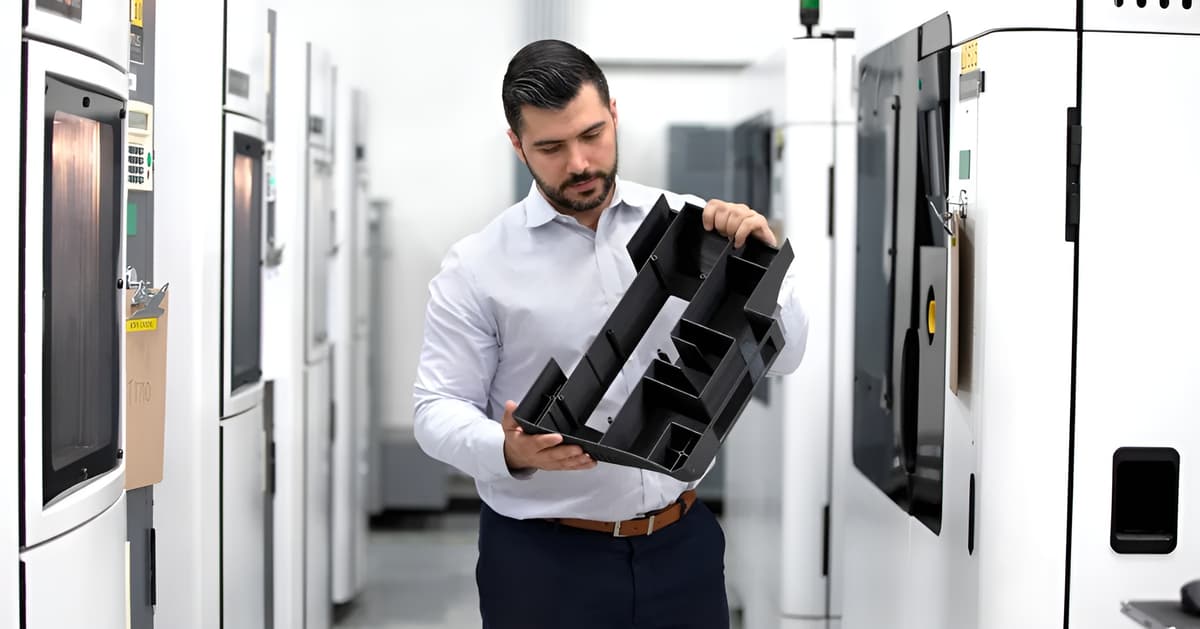
Technology Overview
Industrial-Grade Large Format 3D Printing
Industrial FDM systems deliver large-format capabilities with engineering-grade thermoplastics. From aerospace components to automotive tooling, FDM provides reliable, cost-effective manufacturing for demanding applications.
Advanced manufacturing capabilities enable complex geometries, functional prototypes, and end-use production parts that would be impossible or cost-prohibitive with traditional manufacturing methods. From functional prototypes to end-use production parts, this technology delivers exceptional performance across demanding industries.
Industrial Manufacturing
High Performance FDM Thermoplastics
Trusted by manufacturers for large-scale production and industrial applications, FDM technology enables cost-effective manufacturing of oversized parts and complex assemblies. Engineering-grade thermoplastics like ULTEM, PEEK, and carbon fiber composites provide exceptional strength-to-weight ratios and chemical resistance. From aerospace ducting to automotive tooling, FDM offers unmatched scalability for both prototyping and end-use manufacturing with minimal material waste.
Manufactured for Demanding Applications
Manufacturing environments demand reliable, repeatable processes that FDM consistently delivers through heated chamber technology and precise material deposition. Large build volumes accommodate parts up to 900mm, while multi-axis capabilities enable complex overhangs and internal structures. The heated chamber ensures dimensional stability in engineering thermoplastics, critical for jigs, fixtures, and end-use components in demanding industrial applications.
Key Advantages
Complex Geometries: Intricate internal channels, overhangs, and assemblies impossible with traditional manufacturing.
Functional Prototypes: Test mechanical properties and fit before investing in production tooling.
Custom Tooling: Jigs, fixtures, and manufacturing aids tailored to specific production requirements.
End-Use Parts: Production components for aerospace, medical, automotive, and industrial applications.
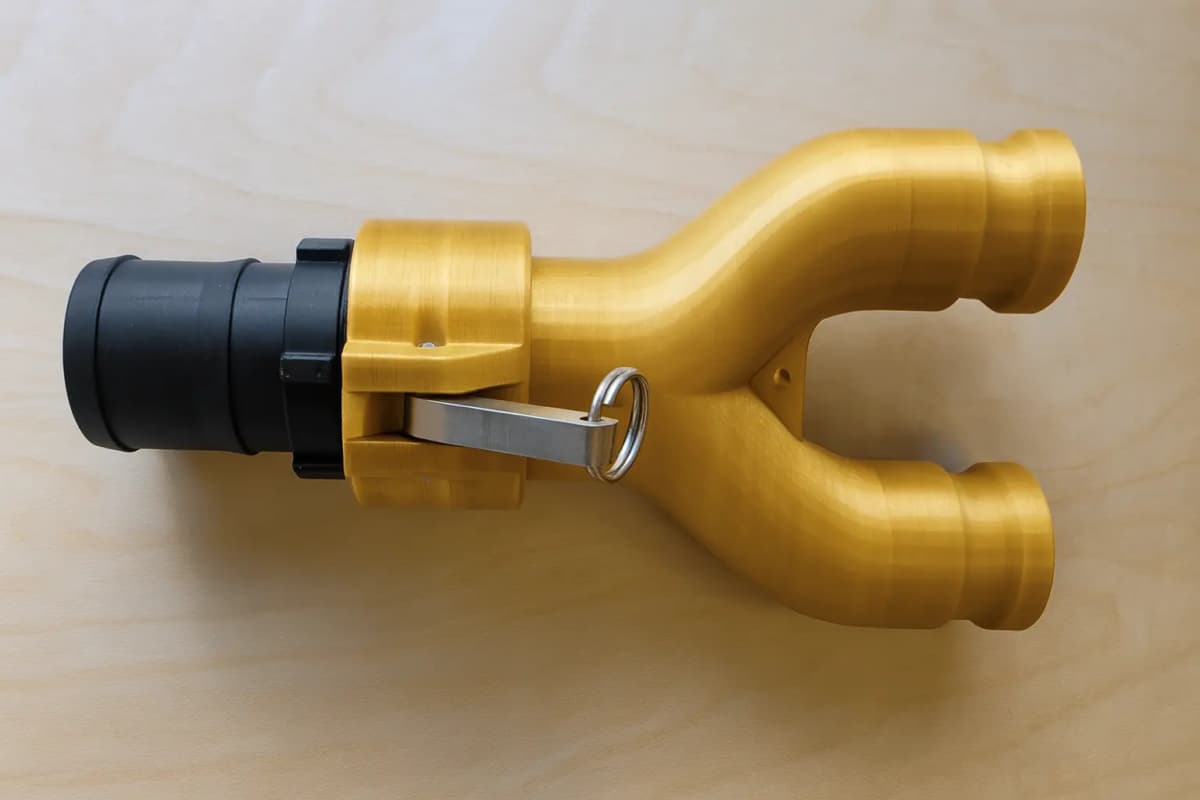
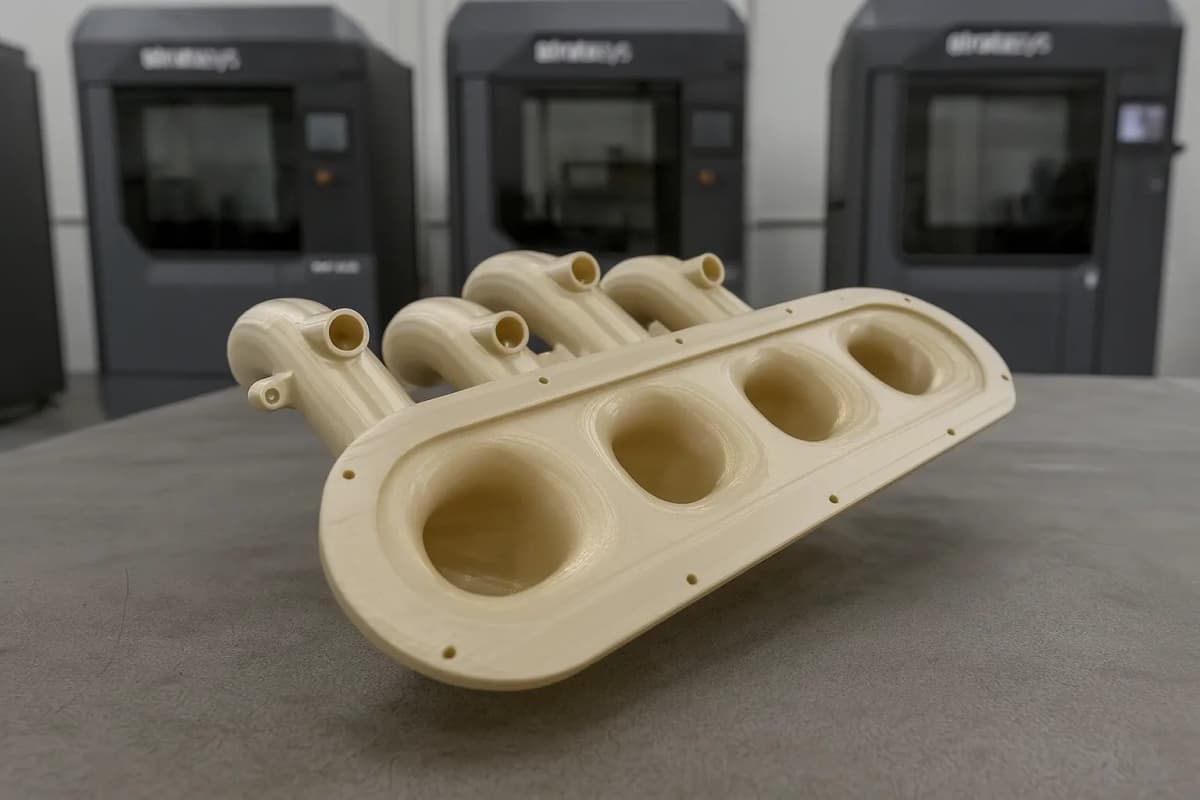
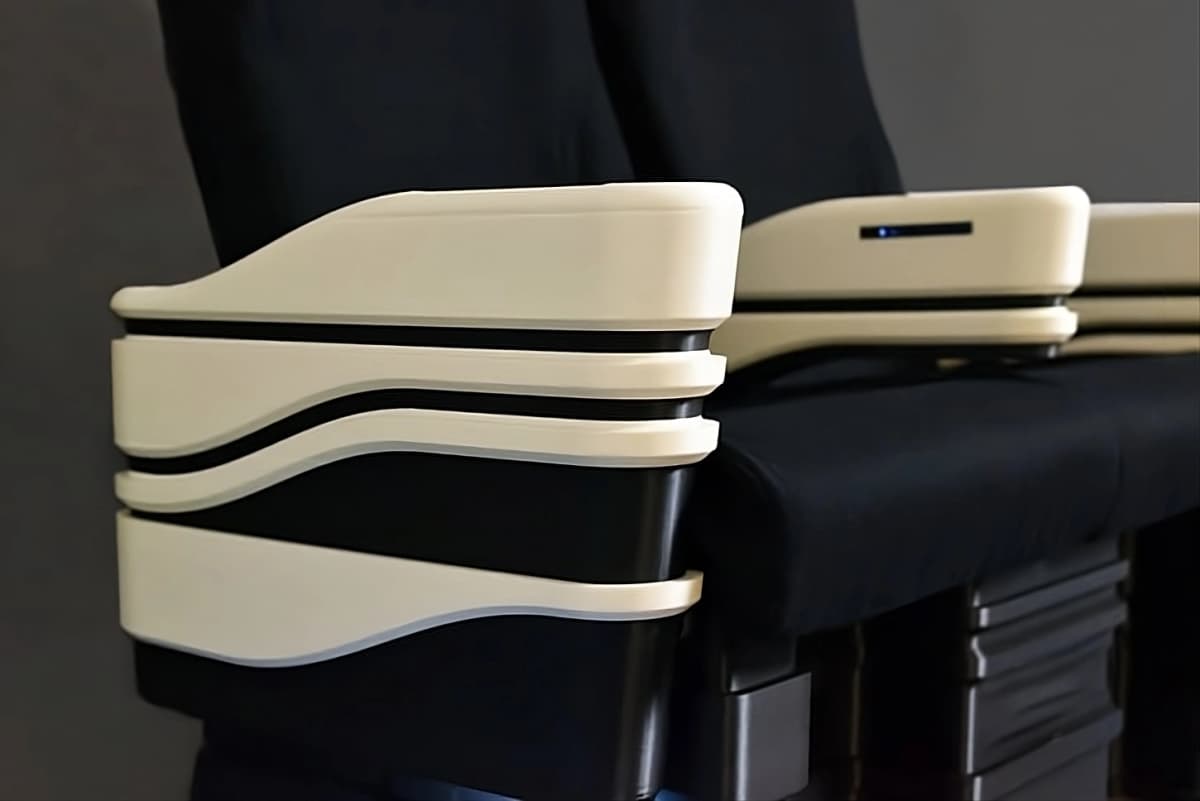
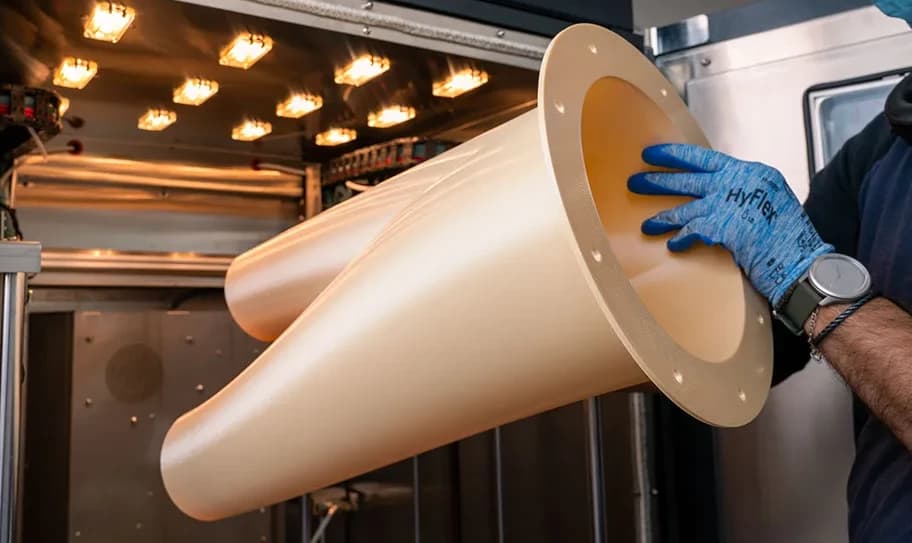
How FDM 3D Printing Works
Fused Deposition Modeling uses industrial Stratasys 3D printers with heated extruders and enclosed build chambers to melt and deposit thermoplastic filament layer by layer, creating strong, durable parts with excellent material properties.
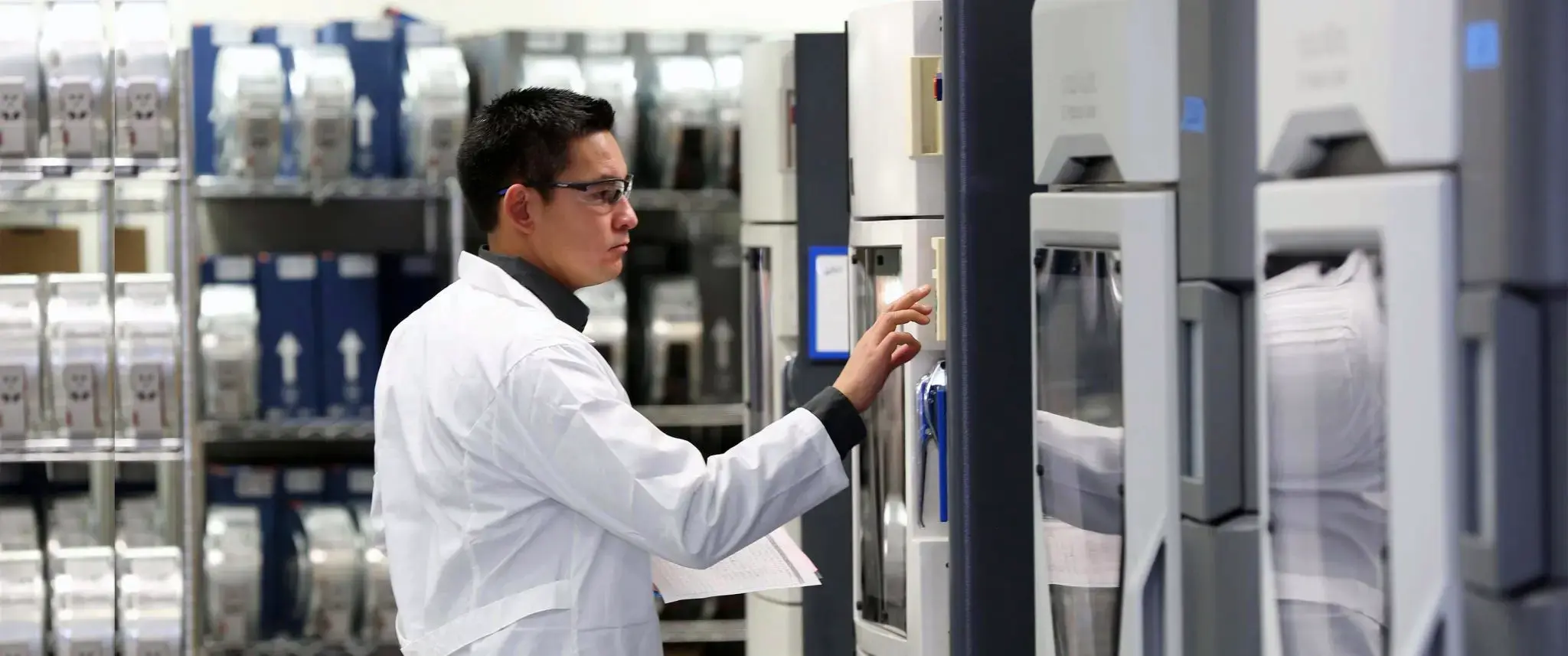
Material Loading & Preparation
Industrial-grade thermoplastic filament is loaded into the heated extruder system. The enclosed build chamber is preheated to optimal temperature to prevent warping and ensure consistent layer adhesion.
Step Specifications
High Performance FDM Thermoplastics
Professional-grade FDM thermoplastics engineered for strength, precision, and reliability. From standard engineering plastics to high-performance PEEK and carbon fiber composites, our material library covers applications from prototyping to end-use manufacturing.
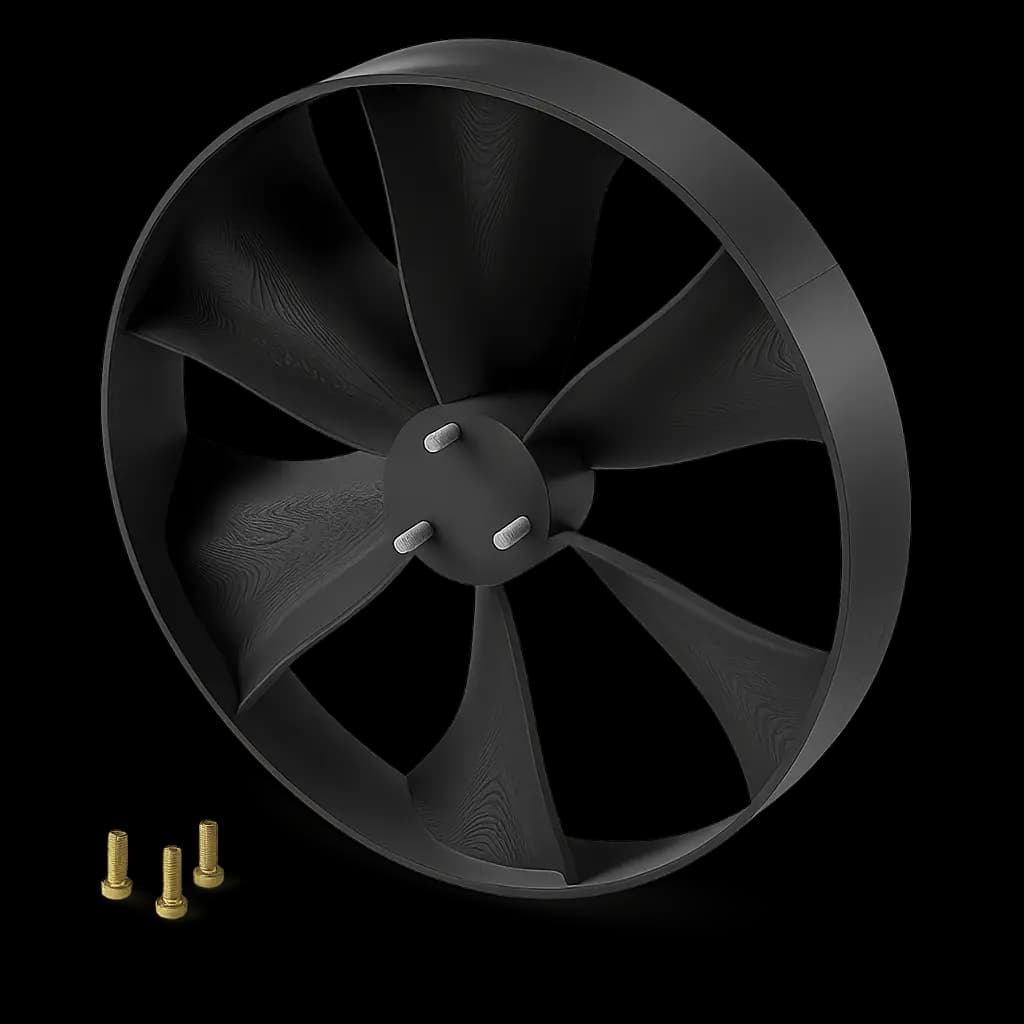
ABS
Engineering Grade Material
The strongest ABS plastic - up to 70% stronger than standard ABS with superior layer bonding and impact resistance
Applications:
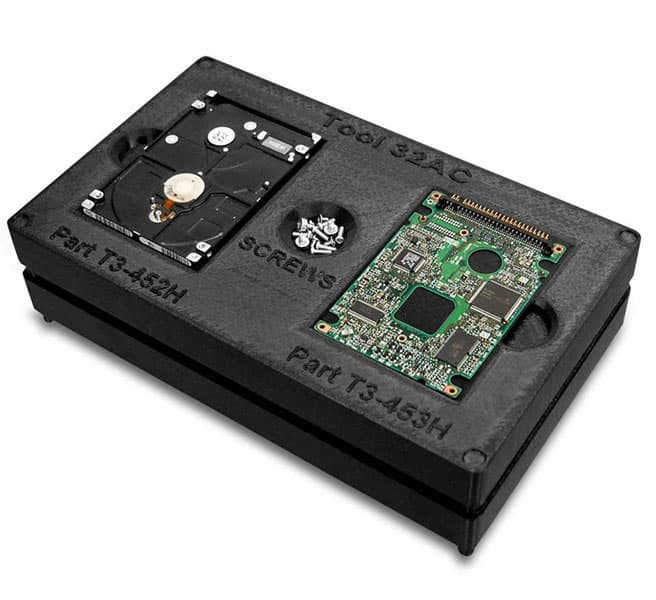
ABS-ESD7
Electrostatic Dissipative Properties
Static dissipative ABS thermoplastic ideal for applications where static charge can damage products or cause explosions
Applications:
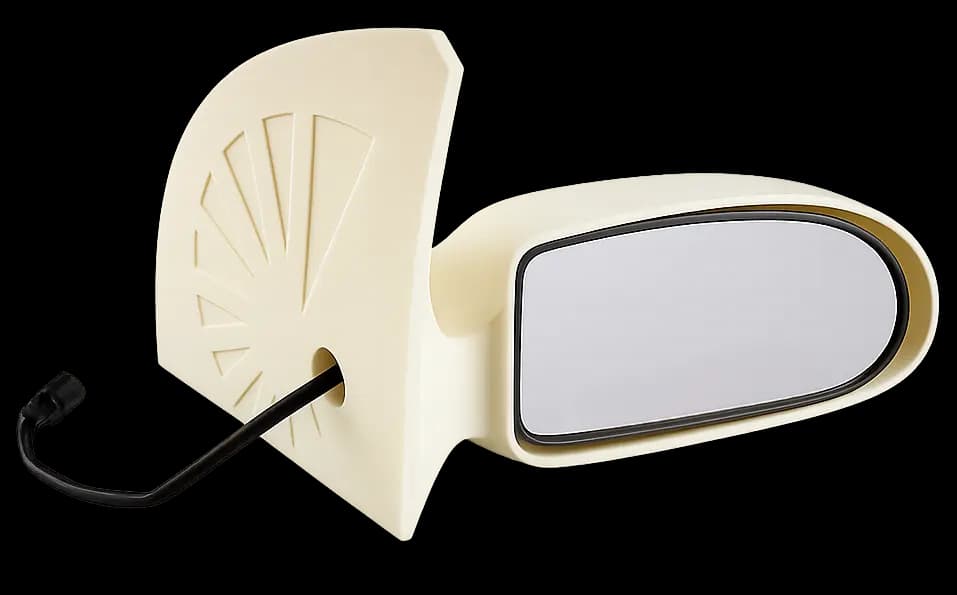
ASA
Engineering Grade Material
UV-stable thermoplastic with excellent weather resistance and strong mechanical properties
Applications:
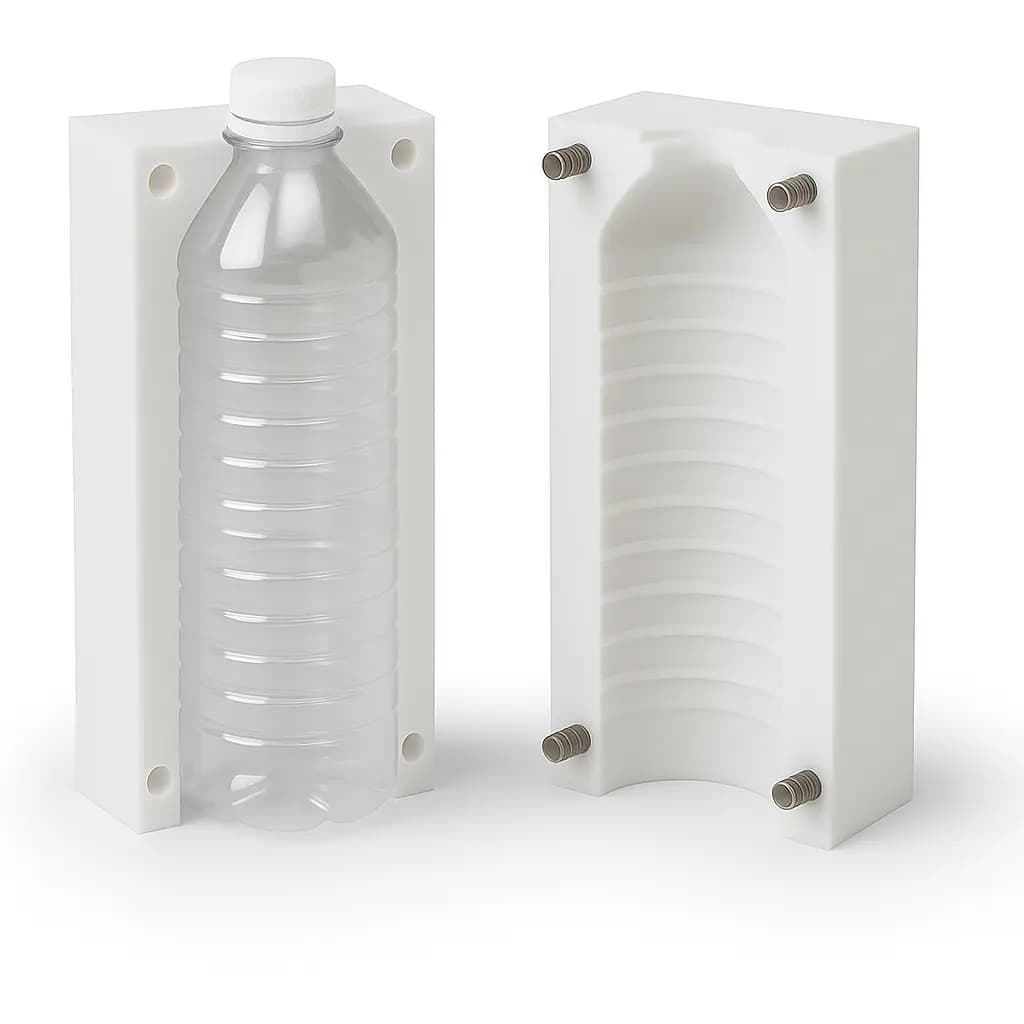
Polycarbonate (PC)
Engineering Grade Material
Exceptionally high tensile and flexural strength thermoplastic for demanding applications
Applications:
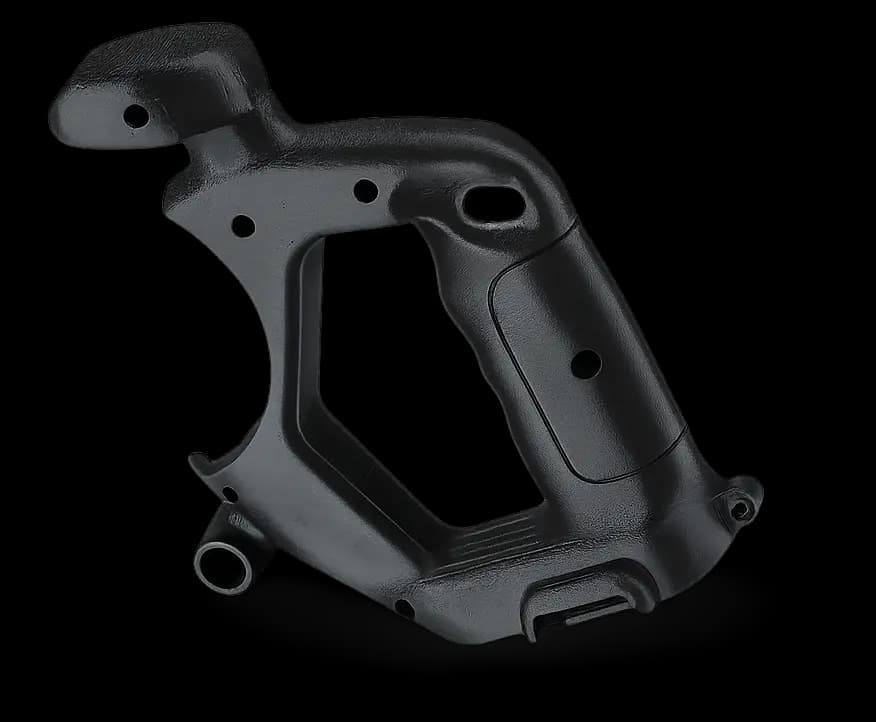
PC-ABS
Engineering Grade Material
Combines PC strength and heat resistance with ABS flexibility and cost advantages
Applications:
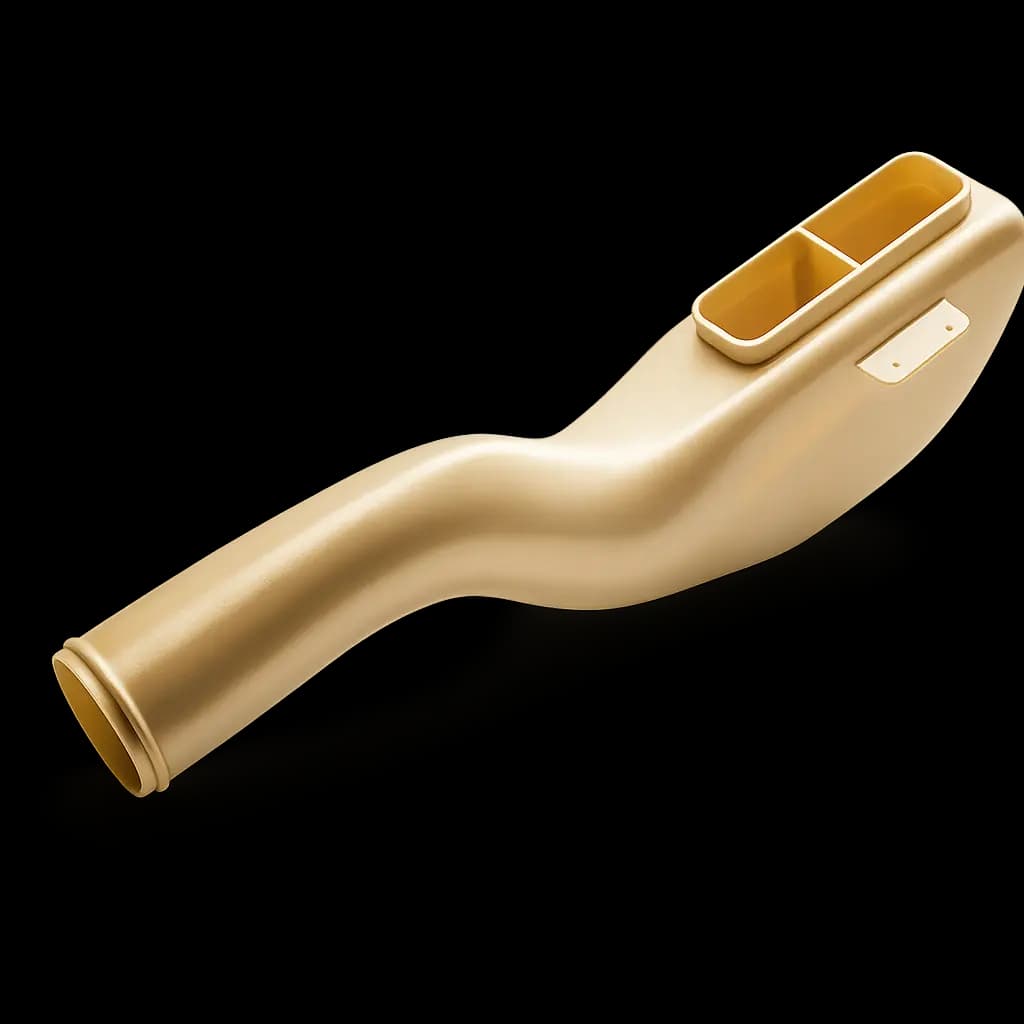
ULTEM 9085
Engineering Grade Material
High-performance polyetherimide with excellent strength-to-weight ratio and FST ratings
Applications:
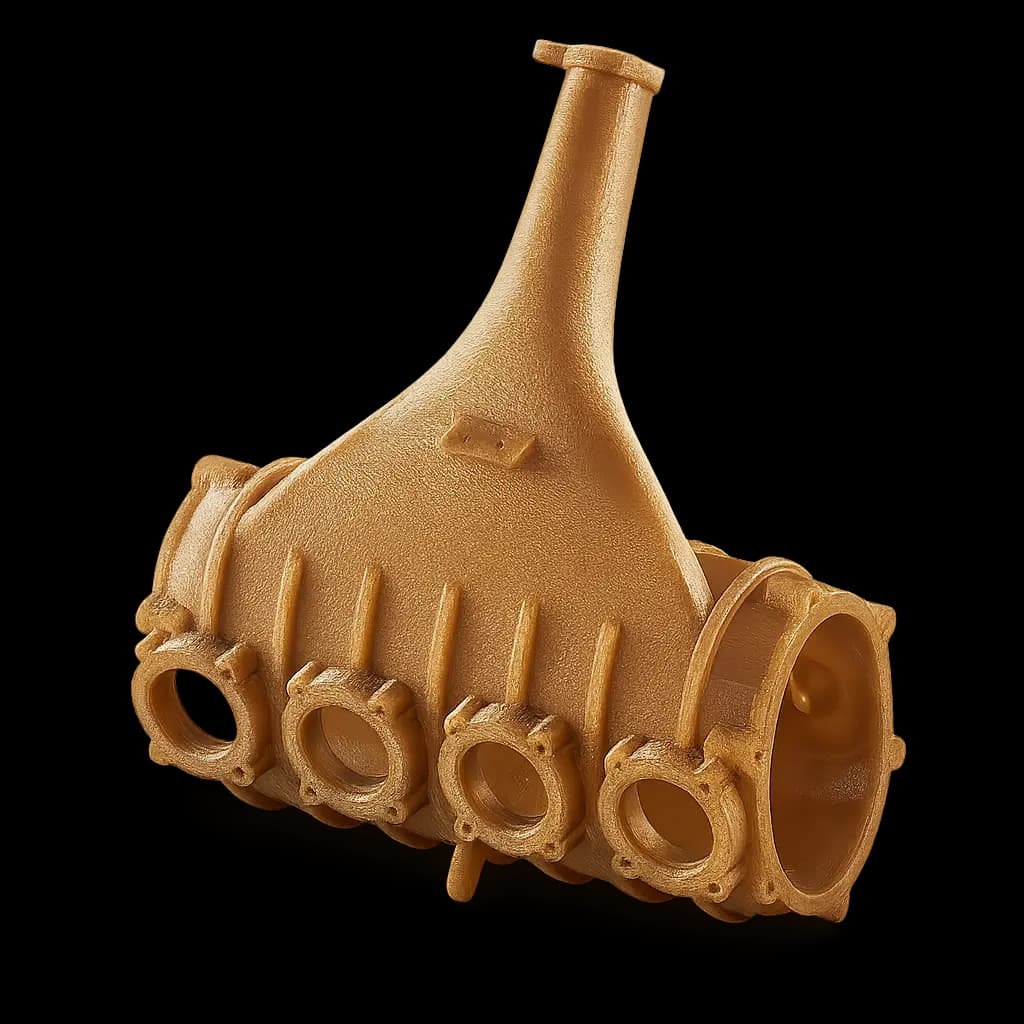
ULTEM 1010
Engineering Grade Material
Highest tensile strength, heat and chemical resistance of any additive thermoplastic
Applications:
Material Surface Finishes
FDM parts have a distinct layer-by-layer texture with visible striations, resulting in a slightly rough, ribbed surface finish. While the natural finish is durable and functional for most applications, post-processing techniques can significantly enhance appearance and performance. Vapor smoothing chemically melts the outer surface, creating a glossy, sealed finish with improved strength. Performance painting provides a professional, polished look with custom color matching capabilities.
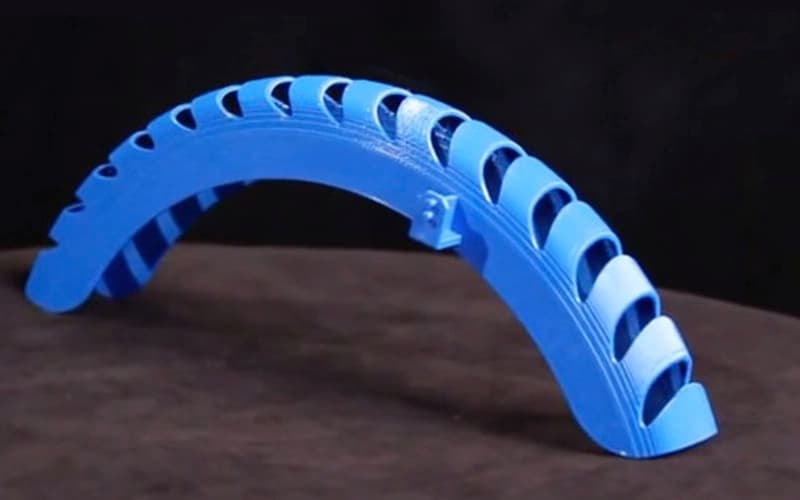
Standard Finish
Visible Layer-by-Layer Texture
FDM 3D printed parts have a visible layer-by-layer texture with slight ridges and striations, resulting in a rougher surface finish compared to other 3D printing technologies like SLS or SLA. Soluble supports are dissolved in an ultrasonic cleaning tank, while physical supports on high-temperature materials are removed by hand if required.
Finish Attributes
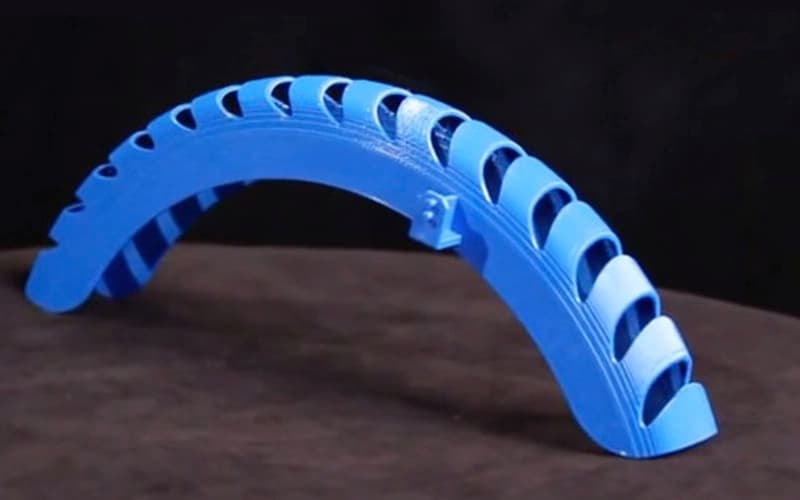
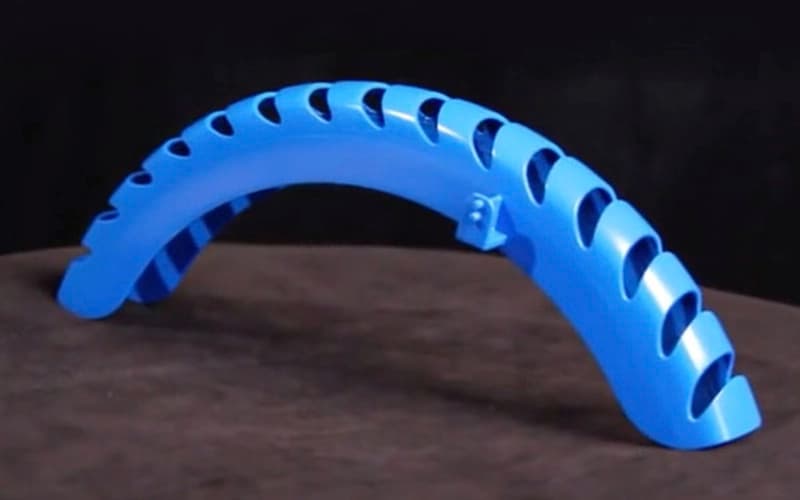
Vapor Smoothing
Chemically Smoothed Surface
Vapor smoothing dissolves the outer layer, causing it to smooth out and blend, reducing layer lines and enhancing the part's appearance. This process creates a glossy, sealed surface with improved strength, reduced porosity, and increased chemical resistance, making it ideal for functional and aesthetic applications.
Finish Attributes
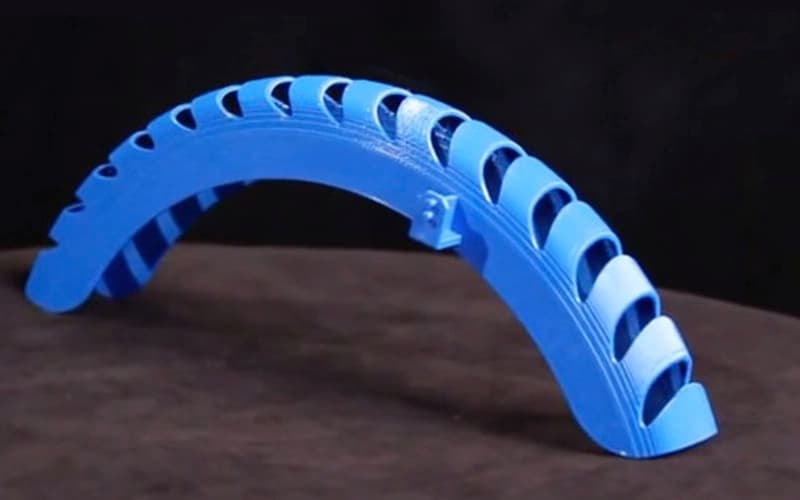
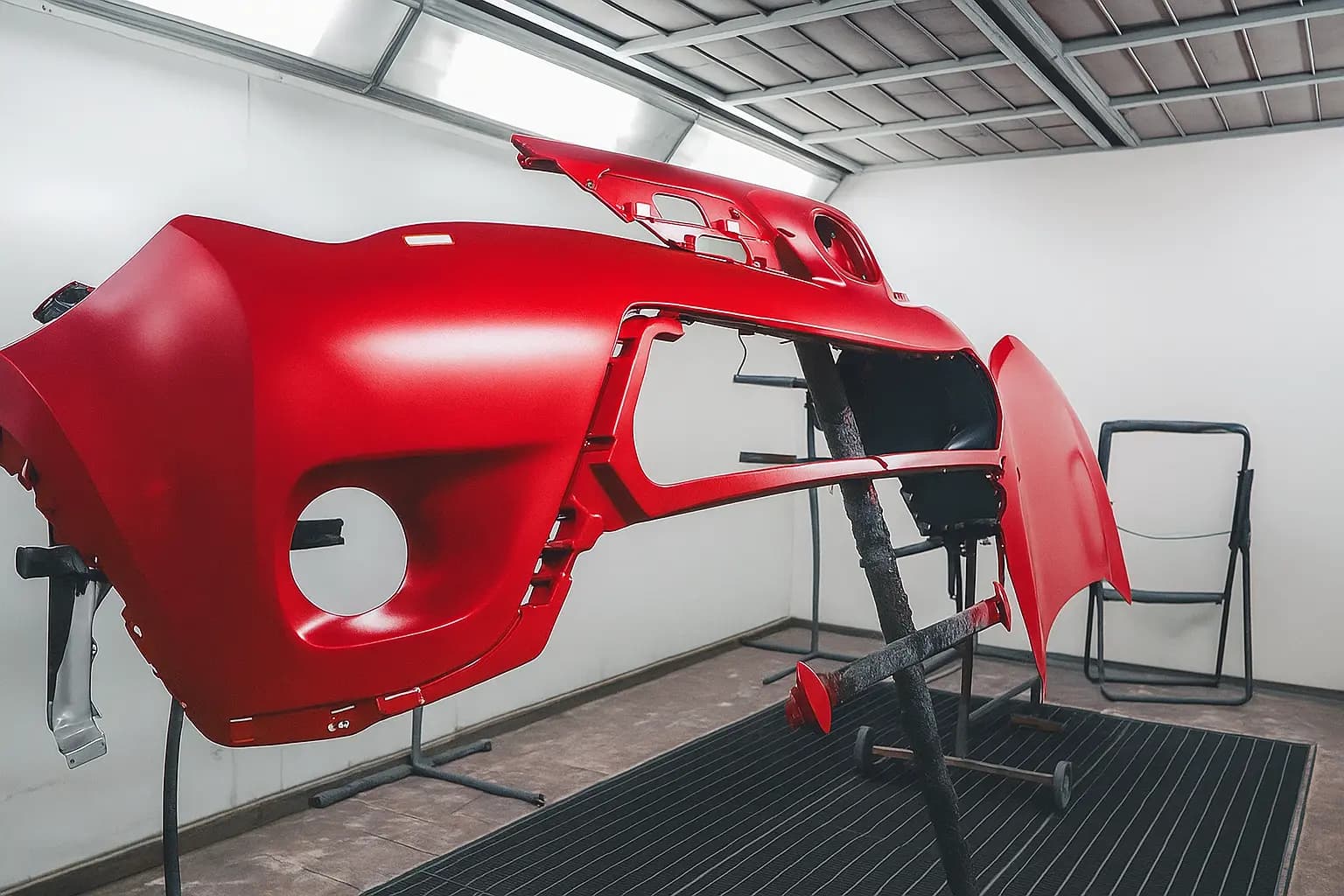
Performance Paint
Automotive-Grade Coating
Painting offers a highly durable, automotive-grade coating that enhances the aesthetics and durability of 3D-printed parts. Each part is hand-finished to ensure smooth surfaces and a premium quality appearance. Using professional-grade coating equipment, this process allows for precise application and exceptional adhesion. Custom color matching is available, making it ideal for applications that require specific branding or visual impact.
Finish Attributes
Additional Manufacturing Services
Complete your FDM parts with our precision post-processing services for production-ready components with enhanced performance and aesthetics.
Threading
Precision threads for functional assemblies
Tapping
Drill press tapped holes for connections
Heat Set Inserts
Threaded inserts for durable fastening
Assembly Services
Professional part assembly & integration
CAD Optimization
Optimize parts for FDM production
Fused Deposition Modeling Design Guidelines
Essential design considerations to optimize your Fused Deposition Modeling parts for manufacturing success.
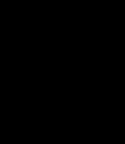
Maximum Build Volume
914mm x 609mm x 914mm (36" x 24" x 36")
FDM produces parts up to 36 inches in a single build. Parts larger than the build volume can be printed in sections and assembled.
This is one of the largest build volumes available for industrial FDM systems.
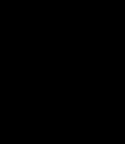
Tolerances
Machine-dependent tolerances
Fortus 450 (16" x 14" x 16"): ±0.25 mm (±0.010"), or ±0.2%, whichever is greater. Fortus 900 (36" x 24" x 36"): ±0.762 mm (±0.030"), or ±0.5%, whichever is greater.
Tolerances as tight as +/- 0.127 mm (+/-0.005") can be achieved on request with engineering drawings.
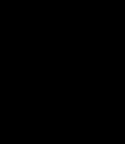
Layer Height
127 - 330 microns
Standard layer height is 254 microns (0.010″) unless otherwise stated. Industrial FDM machines can print parts with custom layer thickness, in the range of 127 - 330 microns thick. Thicker layers typically result in better adhesion and better mechanical properties.
Thicker layers provide better strength but lower surface quality.
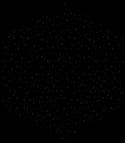
Surface Finish
Visible Layer Lines
Parts made with FDM will always show visible layer lines, especially on curved surfaces. However, the visibility of layer lines can be reduced with smaller layer heights at the expense of print speed.
Layer lines are inherent to the FDM process and cannot be completely eliminated.
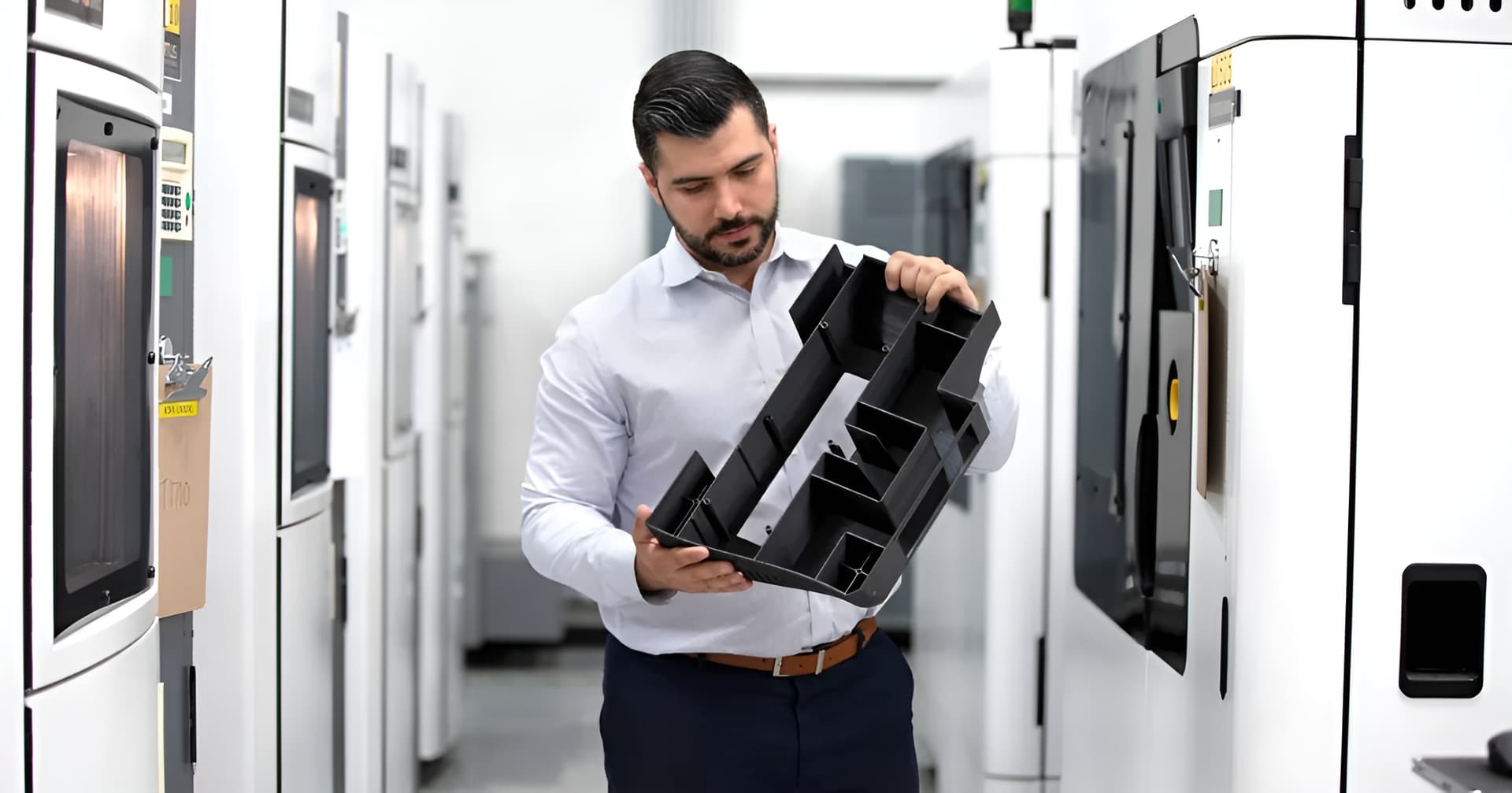
Advantages of FDM 3D Printing for Prototyping & Production
Fused Deposition Modeling offers unique advantages for modern manufacturing applications, delivering exceptional performance and versatility for both prototyping and production requirements. Key benefits include cost-effective manufacturing, superior material properties, and the ability to produce complex geometries that would be impossible or expensive with traditional manufacturing methods.
- Large-Format Printing
- Capable of producing sizable parts in a single build, FDM is well-suited for applications requiring large prototypes, jigs, and fixtures
- Cost-Effective Manufacturing
- FDM is one of the most affordable 3D printing technologies, making it ideal for rapid prototyping and low-volume production
- Functional Prototyping
- Parts can be printed using industrial thermoplastics with properties close to injection-molded components
- Material Variety
- Compatible with a wide range of thermoplastics, including ABS, PC, high-performance ULTEM, and fiber-reinforced composites
- Strong Layer Adhesion
- Engineered for high-strength applications, FDM prints offer excellent interlayer bonding for durable, impact-resistant parts
- Scalable Production
- Adaptable for both single-part manufacturing and batch production while maintaining cost efficiency
- Mechanical Strength & Durability
- FDM parts exhibit excellent mechanical strength and impact resistance, ideal for tooling and functional components
Instant Quote Tool
From Upload to Delivery
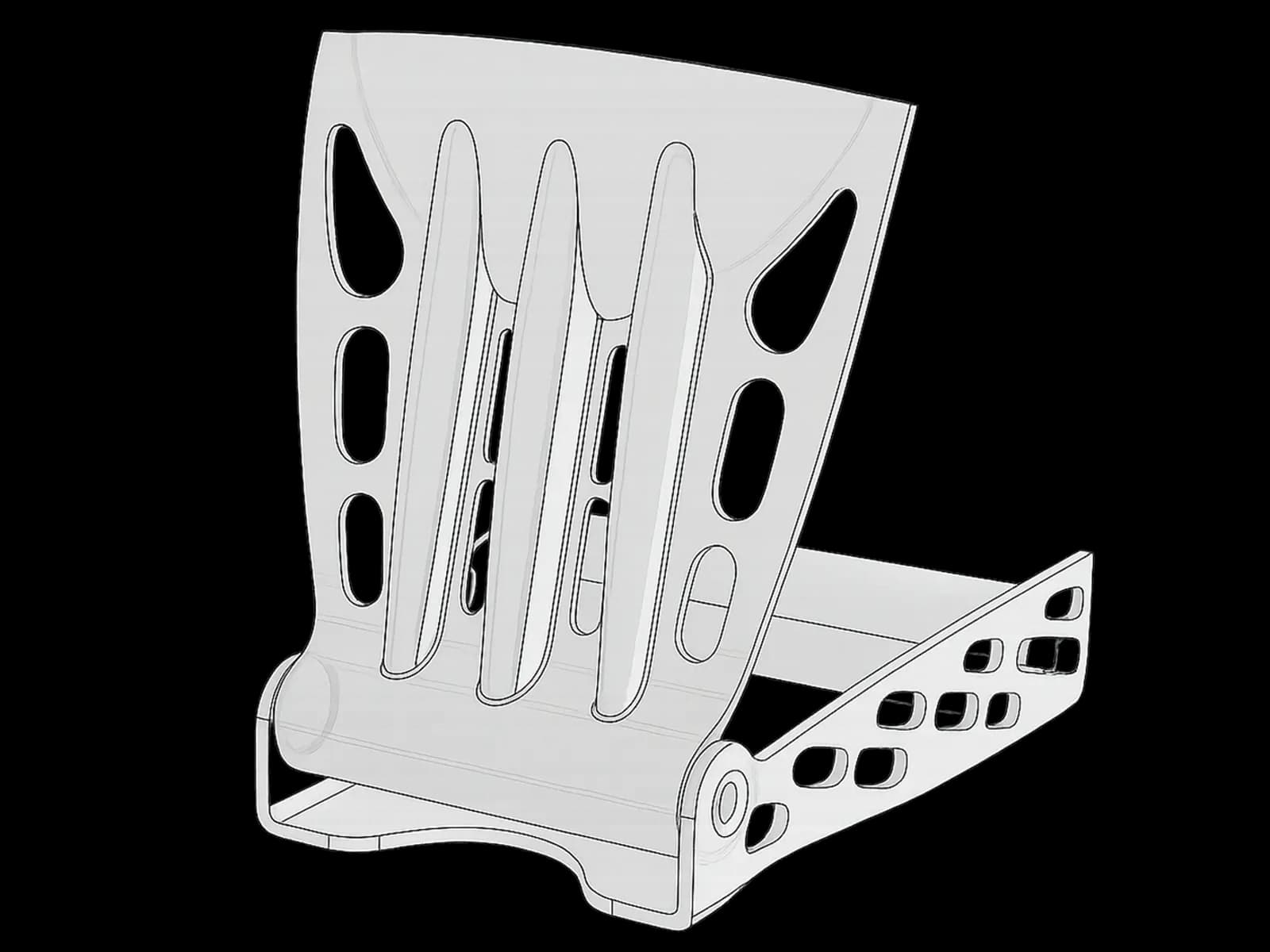
75% complete
Simple File Upload Process
Drag and drop your 3D files or browse to upload. Our system automatically analyzes your designs and provides instant feedback on printability and optimization suggestions.
- Drag & drop multiple file formats
- Automatic design analysis
- Printability feedback
- File optimization suggestions
FDM Applications Across Industries
Discover how Fused Deposition Modeling is transforming manufacturing across industries with innovative solutions and enhanced capabilities.
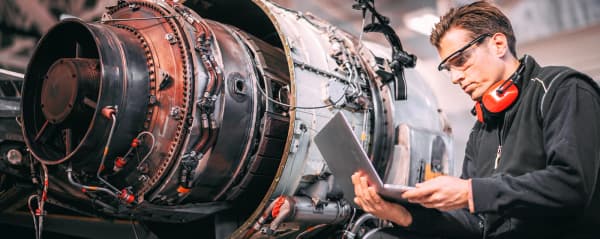
Aerospace Components
Lightweight, strong parts for aircraft interiors, tooling, and UAV components with high-performance materials
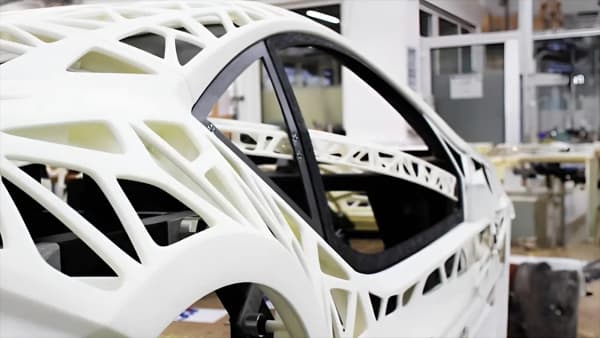
Automotive Manufacturing
Functional prototypes, under-hood components, and production tooling with heat and chemical resistance
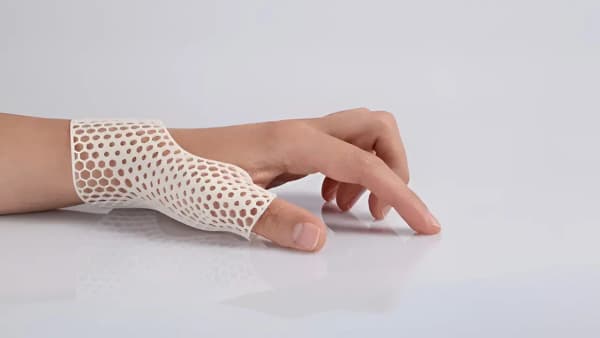
Medical Devices
Biocompatible parts for medical equipment, surgical guides, and custom prosthetics
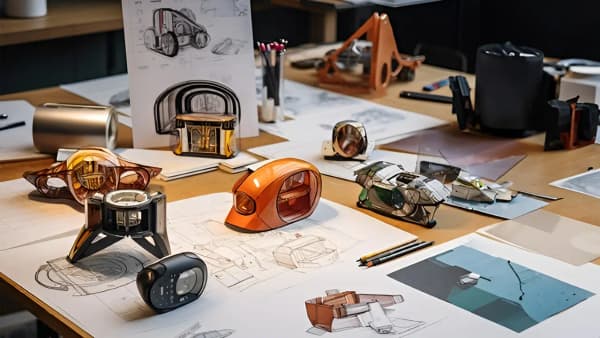
Industrial Design
Functional prototypes, design validation, and low-volume production for product development
Success Stories
Real results from our FDM manufacturing partnerships
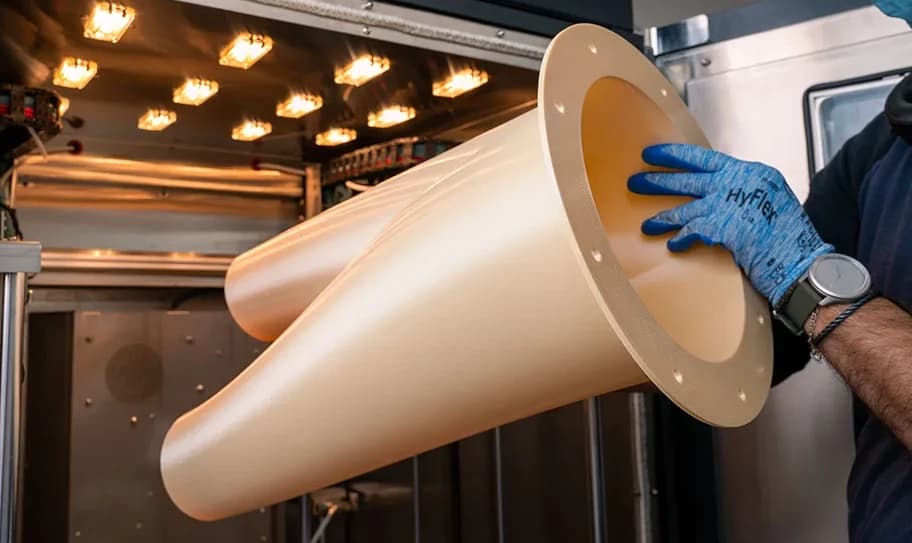
Aerospace Ducting System
Large-format ULTEM ducting components for commercial aircraft with integrated mounting features
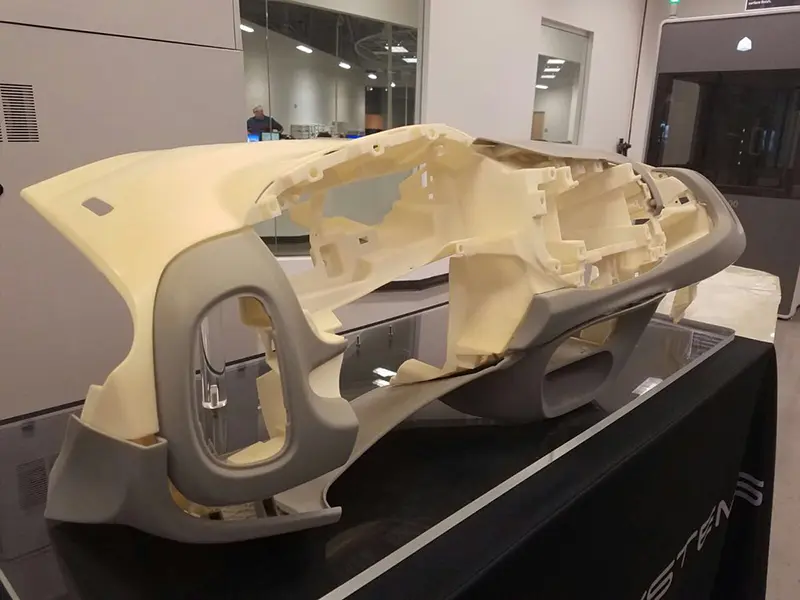
Automotive Dashboard Prototype
Full-scale automotive dashboard prototype with integrated clip features and mounting points
Ready to manufacture your parts?
Upload your CAD files to get instant quotes for FDM 3D printing. Professional-grade manufacturing with fast turnaround times.
Click to start your quote
STL, STEP, OBJ, 3MF supported • Get instant pricing
FDM Questions & Answers
Common questions about FDM 3D printing technology. Can't find what you're looking for? Reach out to our technical team.