In safety-critical industries such as aerospace, automotive, and electronics, fire resistance isn't just a preferenceβit's a regulatory requirement. The UL-94 flammability standard serves as the benchmark for evaluating how plastics behave when exposed to flame.
At Forge Labs, we specialize in 3D printing with UL-94-rated materials including ULTEM 9085,ULTEM 1010, and PC-ABS FR, enabling manufacturers to create complex geometries while meeting stringent fire safety requirements without compromising design freedom.
Understanding the UL-94 Standard
Developed by Underwriters Laboratories (UL), the UL-94 standard evaluates the flammability characteristics of plastic materials under controlled laboratory conditions. The standard encompasses multiple test methods, with the vertical burning test being the most commonly referenced for 3D printing applications.
UL-94 Test Methodology
The UL-94 vertical burning test subjects material samples to a controlled flame source for specific durations, measuring several critical parameters:
- Burning Time: How long the material continues to burn after flame removal
- Dripping Behavior: Whether flaming particles drop from the sample
- Flame Spread: How quickly fire propagates across the material surface
- Afterglow Duration: Time required for glowing combustion to cease
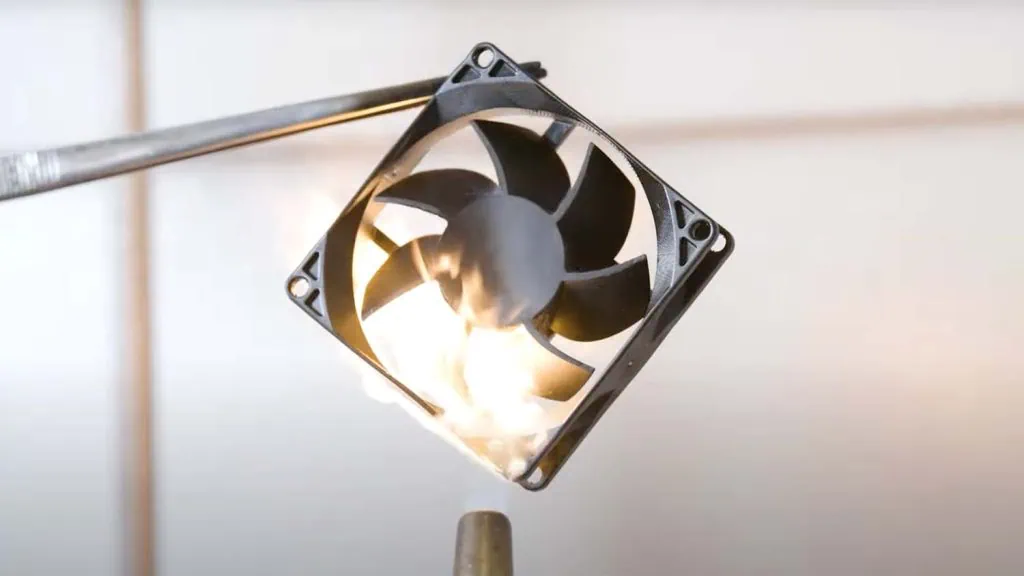
UL-94 vertical burning test setup for flame retardant material certification
UL-94 Classification System
Rating | Burning Time | Dripping | Applications |
---|---|---|---|
HB | Slow horizontal burning (<76mm/min) | Not specified | Low-risk applications |
V-2 | <30 seconds per application | Flaming drips allowed | General electronics |
V-1 | <30 seconds per application | No flaming drips | Consumer electronics |
V-0 | <10 seconds per application | No flaming drips | Aerospace, automotive, critical systems |
5VB | <60 seconds total | No flaming drips | High-performance applications |
5VA | <60 seconds total + no burn-through | No flaming drips | Mission-critical systems |
π‘ Industry Insight
V-0 rating is considered the gold standard for most aerospace and automotive applications, requiring materials to self-extinguish within 10 seconds and produce no flaming drips that could ignite surrounding materials.
UL-94 Certified Materials in Additive Manufacturing
The additive manufacturing industry has evolved to include several high-performance, UL-94-rated materials that enable fire-safe production without compromising mechanical properties or design freedom.
ULTEM 9085
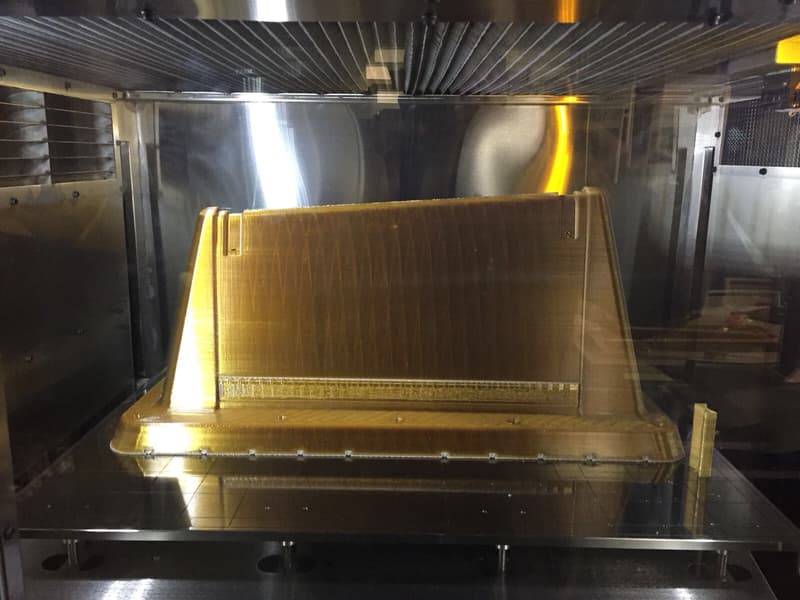
- UL-94 Rating: V-0 at 1.5mm thickness
- Operating Temperature: -54Β°C to 180Β°C
- Tensile Strength: 33 MPa
- Flame Retardant: Inherent (no additives)
- Applications: Aircraft interiors, electronics housings
PC-ABS FR
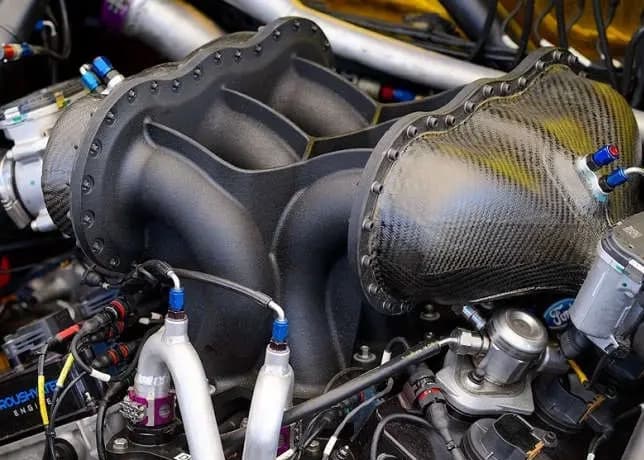
- UL-94 Rating: V-0 at 1.5mm thickness
- Operating Temperature: -40Β°C to 110Β°C
- Impact Strength: 340 J/m (notched Izod)
- Flame Retardant: Halogen-free additives
- Applications: Automotive interiors, consumer electronics
π Material Selection Considerations
When selecting UL-94-rated materials for additive manufacturing, several factors must be evaluated:
- β’ Thickness Dependency: UL-94 ratings are thickness-specific. A material rated V-0 at 3mm may only achieve V-1 at 1mm
- β’ Processing Effects: 3D printing parameters can influence flame retardant properties
- β’ Environmental Conditions: UV exposure, humidity, and thermal cycling may affect long-term fire resistance
- β’ Chemical Compatibility: Some flame retardants may interact with other materials in assemblies
Industry Applications and Compliance Requirements
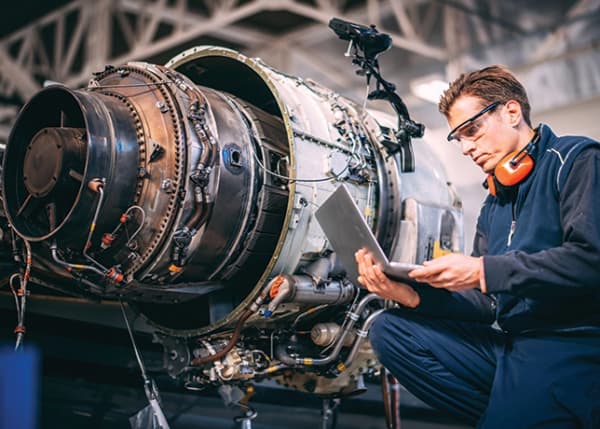
Aerospace
FAA regulations require V-0 or better ratings for most cabin components. Critical applications include seat components, ducting, and electronics housings.
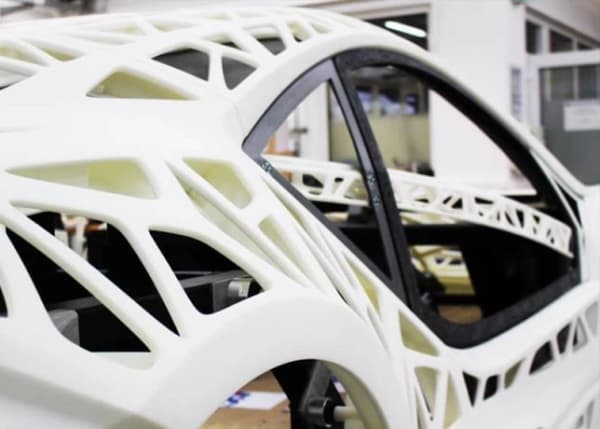
Automotive
FMVSS 302 and ISO 3795 standards mandate specific flame resistance for interior materials. Dashboard components, trim pieces, and electrical housings.
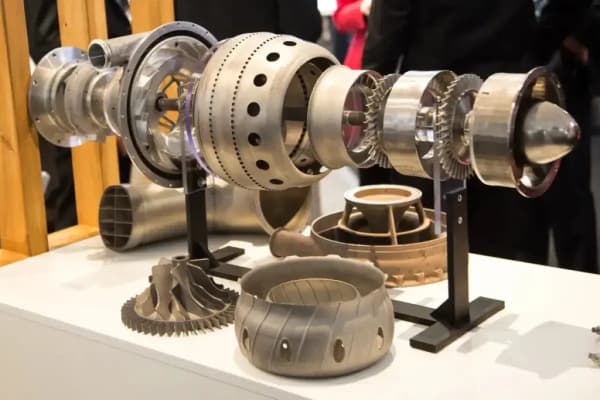
Electronics
IEC 60950 and UL 2089 require V-1 or V-0 ratings for device housings. Critical for power supplies, circuit boards, and connector housings.
π Regulatory Landscape
Understanding the regulatory requirements is crucial for compliance:
- β’ FAR 25.853: Federal Aviation Regulation for aircraft interior materials
- β’ FMVSS 302: Federal Motor Vehicle Safety Standard for automotive interiors
- β’ IEC 60695: International standard for fire hazard testing of electrotechnical products
- β’ ASTM D635: Standard test method for rate of burning of plastics
Design Guidelines for UL-94 Compliant Parts
βοΈ Critical Design Parameters
Achieving UL-94 compliance requires careful attention to part design and manufacturing parameters:
Wall Thickness Optimization
- β’ Minimum Thickness: Most UL-94 certifications require minimum 1.5mm wall thickness
- β’ Uniform Thickness: Avoid sudden thickness changes that may create weak points
- β’ Reinforcement: Use ribs and bosses to maintain structural integrity while meeting thickness requirements
Part Orientation and Build Strategy
- β’ Layer Adhesion: Orient parts to maximize inter-layer bonding strength
- β’ Surface Finish: Smooth surfaces may perform differently than textured surfaces in flame tests
- β’ Support Material: Ensure complete removal to prevent contamination affecting fire performance
π§ Post-Processing Considerations
Post-processing steps can significantly impact UL-94 performance:
- β’ Annealing: Heat treatment may improve material properties but could affect flame retardants
- β’ Machining: Secondary operations should maintain minimum thickness requirements
- β’ Assembly: Adhesives and fasteners must also meet fire safety requirements
- β’ Coating: Surface treatments must not compromise flame retardant properties
Quality Assurance and Testing
π¬ In-House Testing Protocols
At Forge Labs, we implement comprehensive quality assurance measures for UL-94 compliant parts:
- β’ Material Verification: Batch testing of incoming materials for consistency
- β’ Process Validation: Regular testing of production parameters
- β’ Dimensional Inspection: Ensuring thickness requirements are met
- β’ Documentation: Complete traceability from material lot to final part
π Third-Party Certification
For critical applications, third-party testing and certification may be required:
- β’ UL Listing: Official UL recognition for specific part geometries
- β’ Material Supplier Certification: Verification of material properties
- β’ Batch Testing: Statistical sampling for production lots
- β’ Accelerated Aging: Testing long-term stability of flame retardant properties
Advanced Applications and Future Developments
π Emerging Technologies
The intersection of UL-94 standards and additive manufacturing continues to evolve:
- β’ Multi-Material Printing: Combining flame retardant and standard materials in single parts
- β’ Continuous Fiber Reinforcement: Enhancing mechanical properties while maintaining fire safety
- β’ In-Situ Monitoring: Real-time quality control during printing process
- β’ Bio-Based Flame Retardants: Sustainable alternatives to traditional chemical additives
π Industry Trends
Several trends are shaping the future of fire-safe additive manufacturing:
- β’ Stricter Regulations: Increasing safety requirements across industries
- β’ Material Innovation: Development of new flame retardant formulations
- β’ Digital Certification: Blockchain-based material traceability
- β’ AI-Driven Design: Optimization algorithms for fire-safe part design
Best Practices Summary
Successful implementation of UL-94 compliant additive manufacturing requires a holistic approach:
β Key Recommendations
- β Select materials with appropriate UL-94 ratings for your application
- β Design parts with adequate wall thickness (minimum 1.5mm for most materials)
- β Validate flame retardant properties through proper testing
- β Maintain complete documentation for regulatory compliance
- β Consider long-term environmental effects on material properties
- β Work with experienced manufacturers who understand fire safety requirements
Conclusion
UL-94 fire safety standards represent a critical consideration for additive manufacturing in safety-sensitive applications. As the technology continues to mature, the availability of high-performance, flame retardant materials like ULTEM 9085 and PC-ABS FR enables manufacturers to leverage the design freedom of 3D printing while meeting stringent safety requirements.
At Forge Labs, our expertise in UL-94 compliant additive manufacturing ensures that your critical components meet both performance and safety specifications. Whether developing aerospace cabin components, automotive interior parts, or electronic device housings, our comprehensive approach to fire-safe manufacturing delivers the reliability your applications demand.
π Ready to Start Your UL-94 Compliant Project?
Contact our team of materials experts to discuss your fire safety requirements and explore how our UL-94 rated materials can support your next project.