Direct Metal Laser Sintering (DMLS) has emerged as a transformative technology in aerospace manufacturing, enabling the production of complex, lightweight components that were previously impossible to create with traditional manufacturing methods. From GE Aviation's revolutionary fuel nozzles to NASA's rocket engine injectors, metal 3D printing is reshaping how the aviation industry approaches design, production, and performance optimization.
Fundamental Advantages of DMLS in Aerospace
Complex Geometries
DMLS enables the production of intricate internal geometries, lattice structures, and conformal cooling channels that are impossible to achieve with traditional subtractive manufacturing. This capability is crucial for aerospace components requiring optimized airflow, reduced weight, and enhanced performance.
Technical Benefit: Internal channels can be designed with variable cross-sections, eliminating the need for complex assembly and reducing potential failure points.
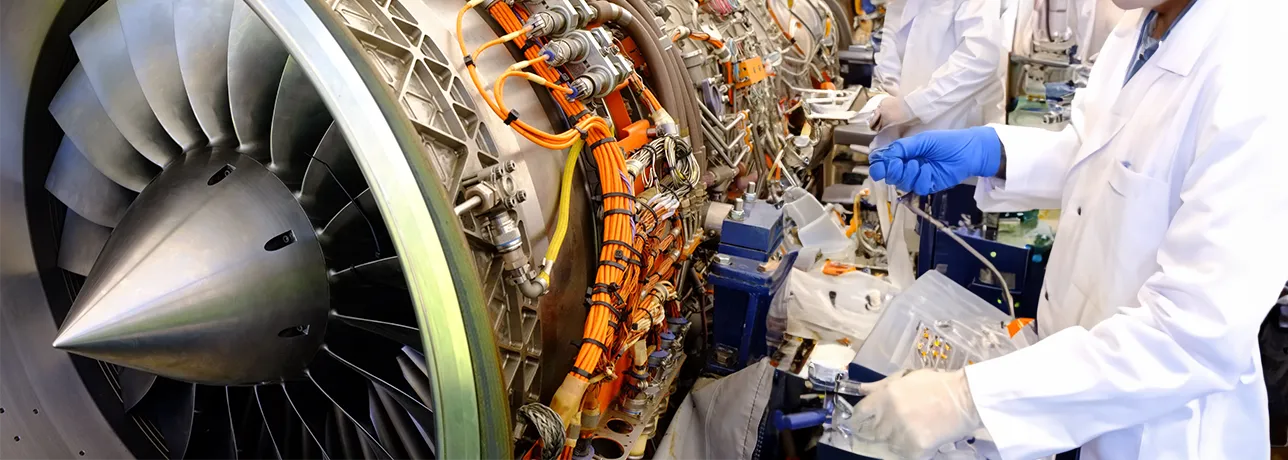
Fundamental Advantages of DMLS in Aerospace
Complex Geometries
DMLS enables the production of intricate internal geometries, lattice structures, and conformal cooling channels that are impossible to achieve with traditional subtractive manufacturing. This capability is crucial for aerospace components requiring optimized airflow, reduced weight, and enhanced performance.
Technical Benefit: Internal channels can be designed with variable cross-sections, eliminating the need for complex assembly and reducing potential failure points.
Weight Reduction
Aerospace components must achieve maximum strength-to-weight ratios. DMLS enables topology optimization, lattice structures, and hollow geometries that maintain structural integrity while dramatically reducing mass.
Performance Impact: Weight reductions of 40–60% are common, directly translating to improved fuel efficiency and increased payload capacity.
Material Efficiency
Traditional aerospace manufacturing can waste 90% of raw materials through machining. DMLS is additive, using only the material needed for the final part, with unused powder recycled for future builds.
Cost Savings: Material utilization rates of 95%+ reduce waste costs, particularly important for expensive aerospace alloys like titanium and Inconel.
Customization & Flexibility
DMLS enables rapid design iterations and customization without tooling changes. This flexibility is essential for aerospace applications requiring frequent design modifications or small-batch production.
Operational Advantage: Design changes can be implemented within hours rather than weeks required for traditional tooling modifications.
Industry Leaders: Real-World DMLS Applications
GE Aviation: LEAP Engine Revolution
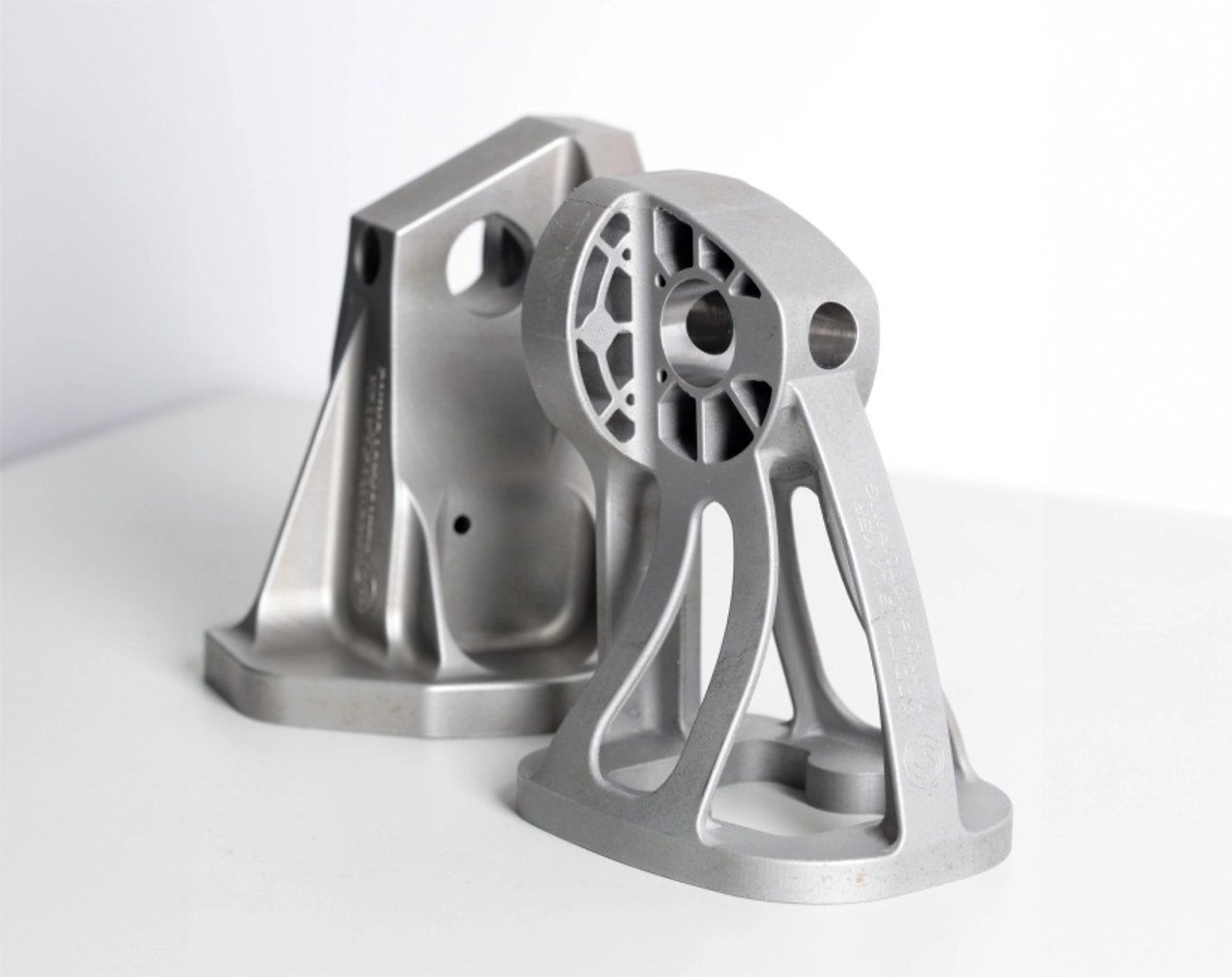
GE Aviation's LEAP engine represents the most successful commercial application of DMLS in aerospace. The fuel nozzle, traditionally assembled from 20 separate parts, is now manufactured as a single DMLS component.
Technical Specifications
- Material: Cobalt‑chromium alloy
- Weight reduction: 25% vs. traditional design
- Durability: 5× more durable than welded assemblies
- Production: 35,000+ nozzles manufactured annually
The LEAP engine incorporates over 30% additive manufactured components, powering the Airbus A320neo and Boeing 737 MAX aircraft families. This represents the largest commercial deployment of DMLS technology in aerospace.
Airbus: A350 XWB Structural Optimization
Airbus leverages DMLS for critical bracket structures in the A350 XWB aircraft, securing hydraulic systems and electrical harnesses throughout the airframe. These components showcase the technology's ability to create complex, lightweight structures with integrated functionality.
Performance Metrics
- Weight reduction: Up to 40% vs. machined brackets
- Material: Titanium Ti‑6Al‑4V
- Integration: Multiple attachment points in single part
- Certification: Full EASA/FAA approval for flight‑critical applications
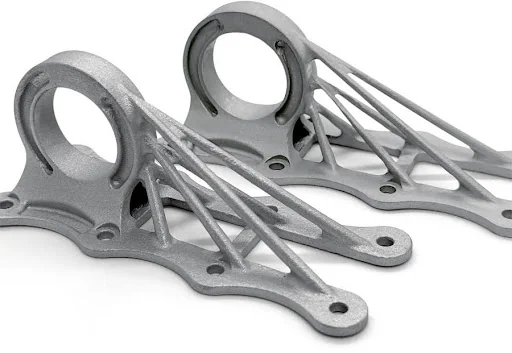
NASA: Next‑Generation Rocket Engine Technology
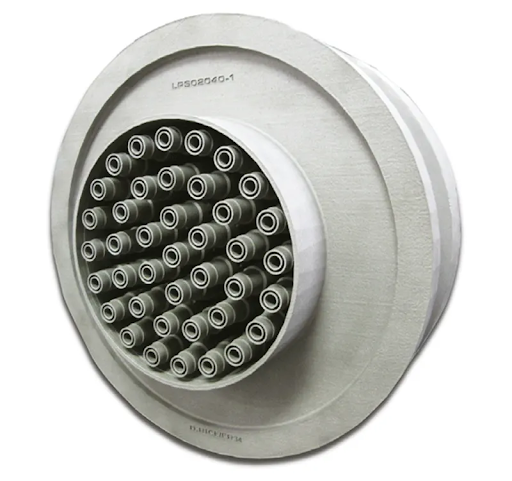
NASA's Space Launch System (SLS) incorporates numerous DMLS components, including rocket engine injectors with complex internal geometries that optimize fuel mixing and combustion efficiency.
Innovation Highlights
- Design: Complex internal channels for optimized fuel flow
- Material: Inconel 625 superalloy for extreme temperature resistance
- Manufacturing: 75% faster than traditional methods
- Testing: Over 1,200 hot‑fire tests completed successfully
These components demonstrate DMLS capability for the most demanding aerospace applications, withstanding extreme temperatures and pressures in rocket engine environments.
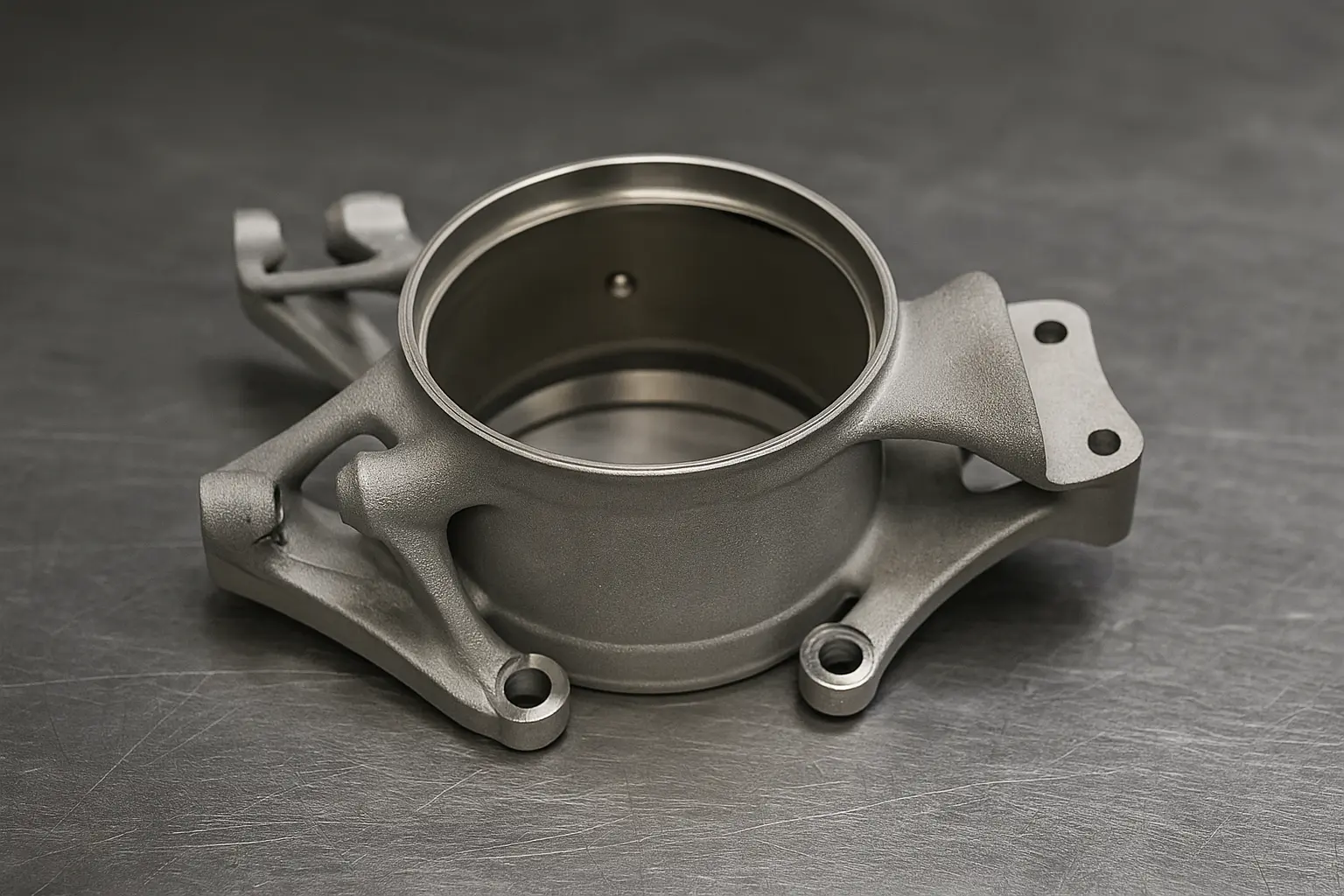
The Future of Aerospace Manufacturing
Direct Metal Laser Sintering is fundamentally transforming aerospace manufacturing, enabling design freedoms and performance optimizations that were previously impossible. The success stories from GE Aviation, Airbus, NASA, Rolls‑Royce, and Boeing demonstrate the technology's maturity and readiness for production applications.
Key Takeaways
Technology Benefits
- Complex geometries enable optimized designs
- 40–60% weight reduction in many applications
- 95% material utilization vs. 10% in machining
- Rapid design iteration without tooling changes
Industry Impact
- Production deployment in commercial aircraft
- Critical applications in space exploration
- Significant cost and time savings realized
- Technology adoption accelerating across the sector
As DMLS technology continues advancing with improved materials, larger build volumes, and enhanced process monitoring, it will play an increasingly vital role in next‑generation aerospace platforms. The combination of design freedom, performance optimization, and production efficiency positions metal 3D printing as a cornerstone technology for the future of aviation and space exploration.