Mold making represents one of the foundational manufacturing processes that has enabled mass production across countless industries. When combined with modern 3D printing technology, traditional mold making transforms into a precision-driven, flexible manufacturing solution that dramatically reduces development time while expanding geometric possibilities. This technological convergence offers unprecedented opportunities for manufacturers seeking to optimize their production workflows and enhance product quality.
Stereolithography (SLA) 3D printing emerges as the optimal technology for mold design applications, delivering exceptional surface finish quality, high dimensional accuracy, and watertight part construction. These characteristics make SLA ideally suited for creating master patterns, mold components, and casting tools that meet the stringent requirements of professional manufacturing environments.
Article Navigation
Master Pattern Development with SLA Technology
Master patterns serve as the foundational components in mold-making processes, functioning as precise replicas of the final intended product. These patterns must exhibit exceptional dimensional accuracy and surface quality, as any imperfections will be reproduced throughout the entire casting process. SLA technology delivers the precision required for professional master pattern creation, achieving layer resolutions as fine as 0.025mm with dimensional tolerances within ±0.1mm.
Material Considerations and Shrinkage Compensation
Professional master pattern development requires careful consideration of material shrinkage characteristics throughout the casting process. Different casting materials exhibit varying shrinkage rates, typically ranging from 0.5% to 3% depending on material composition and curing conditions. Master patterns must be scaled appropriately to compensate for these dimensional changes, ensuring the final cast parts meet specified tolerances.
Common Casting Material Shrinkage Rates
Thermoplastic Materials
- • Polyethylene: 1.5-3.0%
- • Polypropylene: 1.2-2.5%
- • ABS: 0.4-0.8%
- • Polycarbonate: 0.5-0.7%
Thermoset Materials
- • Polyurethane: 0.2-1.0%
- • Epoxy resins: 0.1-0.5%
- • Silicone: 0.1-0.3%
- • Polyester: 0.5-1.5%
Surface Finishing and Durability Enhancement
SLA master patterns require post-processing to achieve optimal surface quality and durability. Professional finishing techniques include progressive sanding from 400 to 2000 grit, followed by vapor polishing or clear coating application. These processes eliminate layer lines, enhance surface smoothness, and improve pattern longevity for repeated use in production environments.
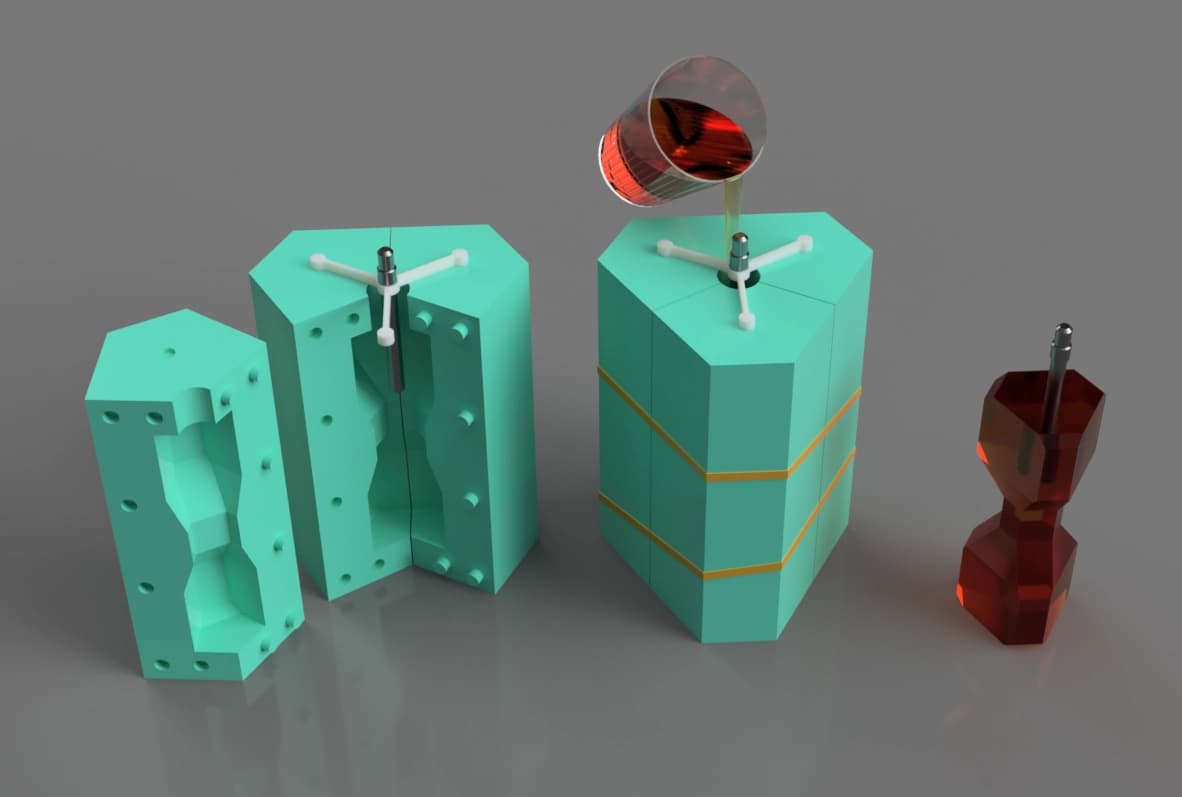
High-precision SLA master pattern demonstrating the surface quality and dimensional accuracy required for professional mold making applications.
Master Mold Fabrication and CAD Integration
Advanced mold fabrication leverages CAD-driven design processes to create master molds that define the precise geometry and interface characteristics of each mold component. This approach eliminates the manual clay modeling and sectioning work traditionally required, replacing it with digital design workflows that ensure consistent results and enable rapid iteration.
Digital Mold Design Workflows
Professional CAD software enables engineers to design complete mold assemblies digitally, incorporating draft angles, parting lines, registration features, and venting systems directly into the master mold geometry. This comprehensive approach allows for virtual assembly verification, interference checking, and optimization of mold performance before physical production begins.
CAD Design Considerations
- • Draft Angles: Minimum 1-3° for thermoplastics, 0.5-1° for flexible materials
- • Registration Keys: Interlocking features ensure precise mold alignment
- • Venting Channels: Prevent air entrapment during casting operations
- • Fill Gates: Optimize material flow and minimize waste
- • Ejection Features: Facilitate easy part removal without damage
Multi-Part Mold Assembly Systems
Complex geometries often require multi-part mold systems to accommodate undercuts, internal features, and challenging parting line configurations. SLA technology enables the production of intricate mold components with precise interlocking features, ensuring accurate assembly and consistent part quality across production runs.
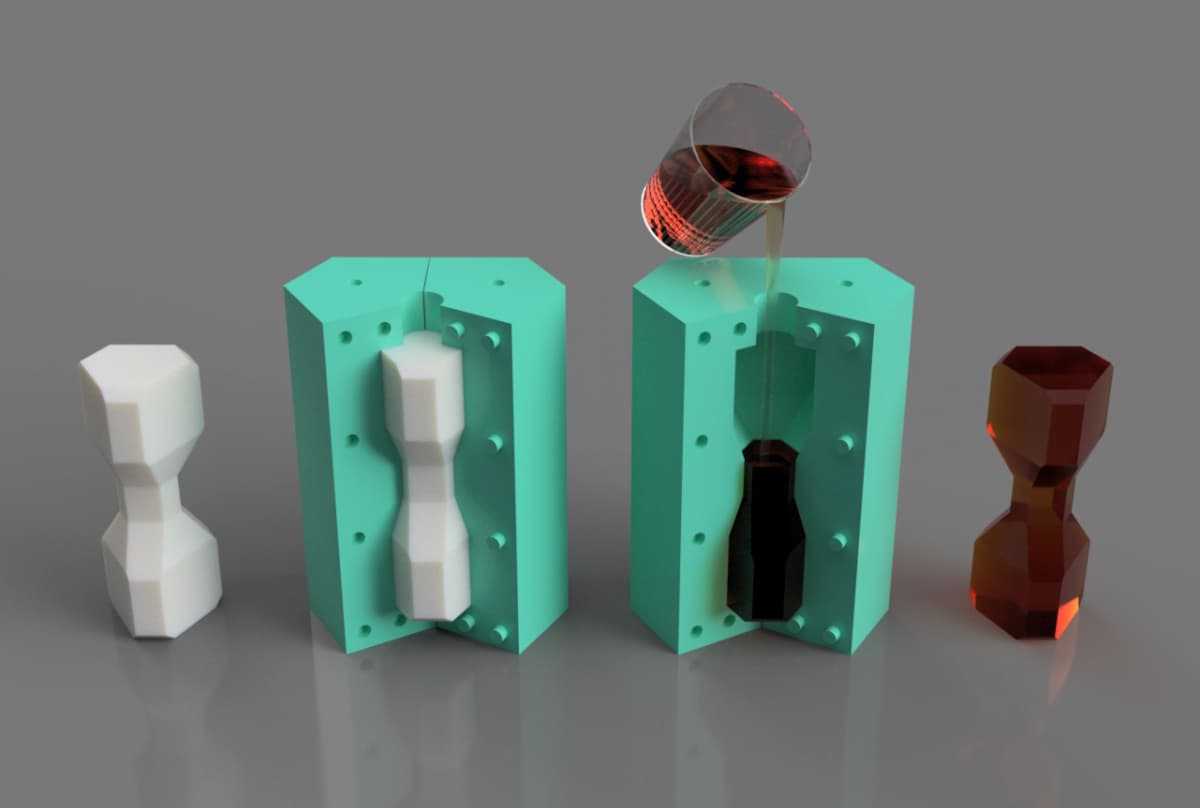
Advanced master mold created using SLA technology, demonstrating complex geometry capabilities and precision registration features for professional manufacturing applications.
Direct SLA Molding Applications
Direct SLA molding represents an advanced application where 3D printed components function as permanent mold parts rather than temporary patterns. This approach requires careful material selection, appropriate draft angle implementation, and thorough understanding of demolding forces to ensure successful part release without mold damage.
Material Compatibility and Release Agent Systems
Successful direct SLA molding depends on compatible material combinations and effective release agent application. Silicone-based casting materials generally exhibit excellent release characteristics with SLA resins, while other materials may require specialized release agents or surface treatments to prevent adhesion during the curing process.
Direct Molding Material Combinations
Excellent Compatibility
- • Platinum-cure silicones
- • Polyurethane foams
- • Water-based casting materials
- • Low-temperature waxes
Requires Release Agents
- • Tin-cure silicones
- • Epoxy casting resins
- • High-temperature materials
- • Reactive polyurethanes
Draft Angle Optimization and Geometric Considerations
Direct SLA molding requires more generous draft angles compared to traditional machined molds due to the material properties of photopolymer resins. Minimum draft angles of 2-5° are recommended, with steeper angles preferred for deep cavities or materials with high adhesion characteristics.
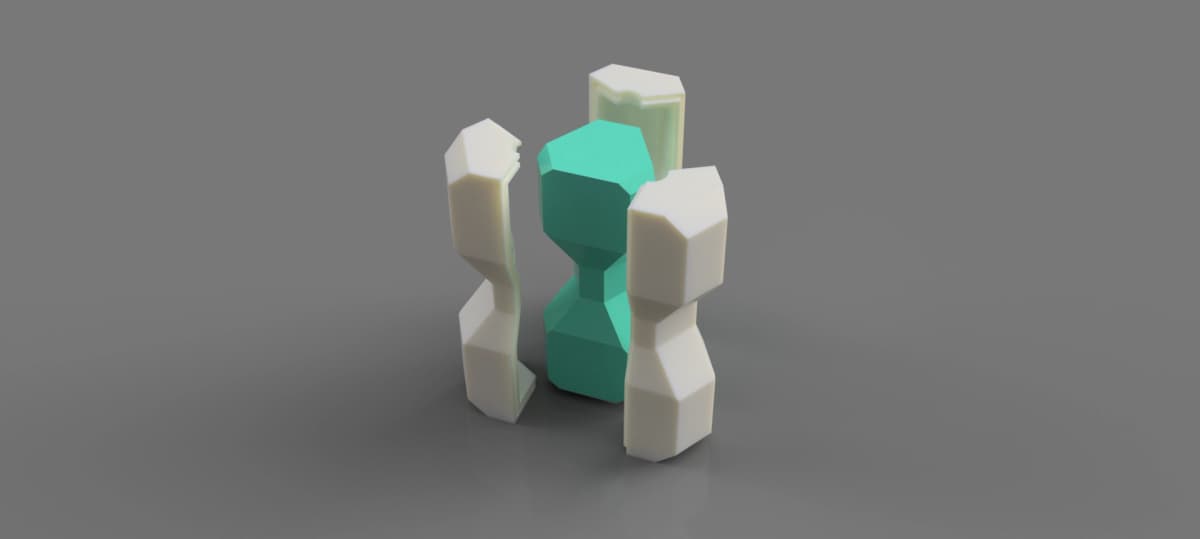
Multi-part SLA mold system optimized for direct casting applications, showcasing proper draft angles and registration features for consistent part production.
Investment Casting Applications
Investment casting, also known as lost-wax casting, represents a precision manufacturing process for creating complex metal components with exceptional surface finish and dimensional accuracy. The integration of 3D printing technology into investment casting workflows revolutionizes pattern creation, enabling rapid prototyping and small-batch production of intricate metal parts.
Pattern Creation and Wax Replacement Strategies
Traditional investment casting relies on wax patterns that are melted out during the ceramic shell firing process. 3D printing offers multiple integration points: direct printing of castable patterns using specialized resins, creation of master patterns for wax injection molding, or development of reusable molds for wax pattern production. Each approach offers distinct advantages depending on production volume and part complexity requirements.
For applications requiring the highest precision and surface quality, Direct Metal Laser Sintering (DMLS) technology offers an alternative approach, enabling direct production of metal components without the complexity of investment casting workflows. This technology is particularly valuable for aerospace and high-performance applications where material properties and geometric complexity are critical factors.
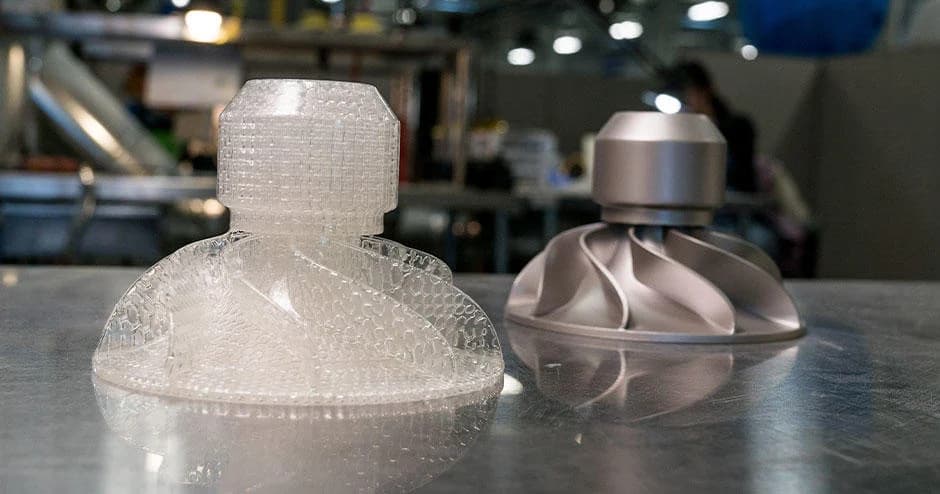
High-precision stainless steel component created through investment casting process utilizing 3D printed master pattern technology.
Digital Manufacturing Integration and Future Outlook
The convergence of traditional mold making with digital manufacturing technologies represents a fundamental shift in how manufacturers approach tooling and production planning. This integration enables unprecedented design flexibility, reduces development timelines, and provides access to complex geometries that were previously impossible or economically unfeasible with conventional manufacturing methods.
Skill Development and Learning Acceleration
Traditional mold making requires years of experience to master the subtle techniques needed for complex pattern creation, parting line development, and troubleshooting casting defects. 3D printing technology accelerates this learning process by providing immediate feedback on design decisions, enabling rapid iteration cycles, and reducing the cost of experimentation.
Digital Manufacturing Advantages
Design Capabilities
- • Complex internal geometries
- • Organic surface forms
- • Consolidated assemblies
- • Integrated functional features
Process Benefits
- • Reduced development time
- • Lower tooling costs
- • Improved repeatability
- • Enhanced precision control
Production Scalability and Economic Considerations
While 3D printing excels for prototyping and low-volume production, understanding when to transition to traditional manufacturing methods remains crucial for economic optimization. Digital manufacturing workflows provide the flexibility to validate designs quickly and cost-effectively before committing to high-volume production tooling, reducing overall development risk and accelerating time-to-market for new products.
Transform Your Manufacturing Capabilities
The integration of 3D printing technology with traditional mold making processes opens unprecedented opportunities for manufacturers seeking competitive advantages through enhanced design capabilities, reduced development timelines, and improved product quality. Whether you're developing prototypes, creating specialized tooling, or exploring new manufacturing approaches, advanced additive manufacturing solutions can transform your production workflows.
Professional stereolithography services provide the precision, reliability, and material properties required for demanding mold making applications. From concept validation through production tooling, comprehensive 3D printing capabilities support every stage of your development process.