Additive manufacturing, also known as 3D printing, is revolutionizing numerous industries. This technology enables manufacturers to create parts and components with minimal material waste compared to traditional subtractive manufacturing methods.
The flexibility and efficiency of 3D printing have made it an increasingly important element of many manufacturers' strategies. However, "3D printing" encompasses various technologies, each with unique advantages and applications. Two of the most common and versatile types are Selective Laser Sintering (SLS) and Fused Deposition Modeling (FDM).
What is SLS 3D Printing?
Selective Laser Sintering (SLS) uses a high-powered laser to selectively fuse thermoplastic powder particles layer by layer. The process begins with a thin layer of powder spread across the build platform. A laser then traces the cross-section of the part, sintering the powder particles together to form a solid layer.
The SLS Process Step-by-Step:
- Powder Application: A thin layer of thermoplastic powder is spread across the build bed
- Laser Sintering: A CO₂ laser selectively fuses powder particles according to the part geometry
- Layer Progression: The build platform lowers, and a new layer of powder is applied
- Repeat: The process continues until the entire part is complete
- Cooling & Cleanup: Parts undergo controlled cooling before powder removal
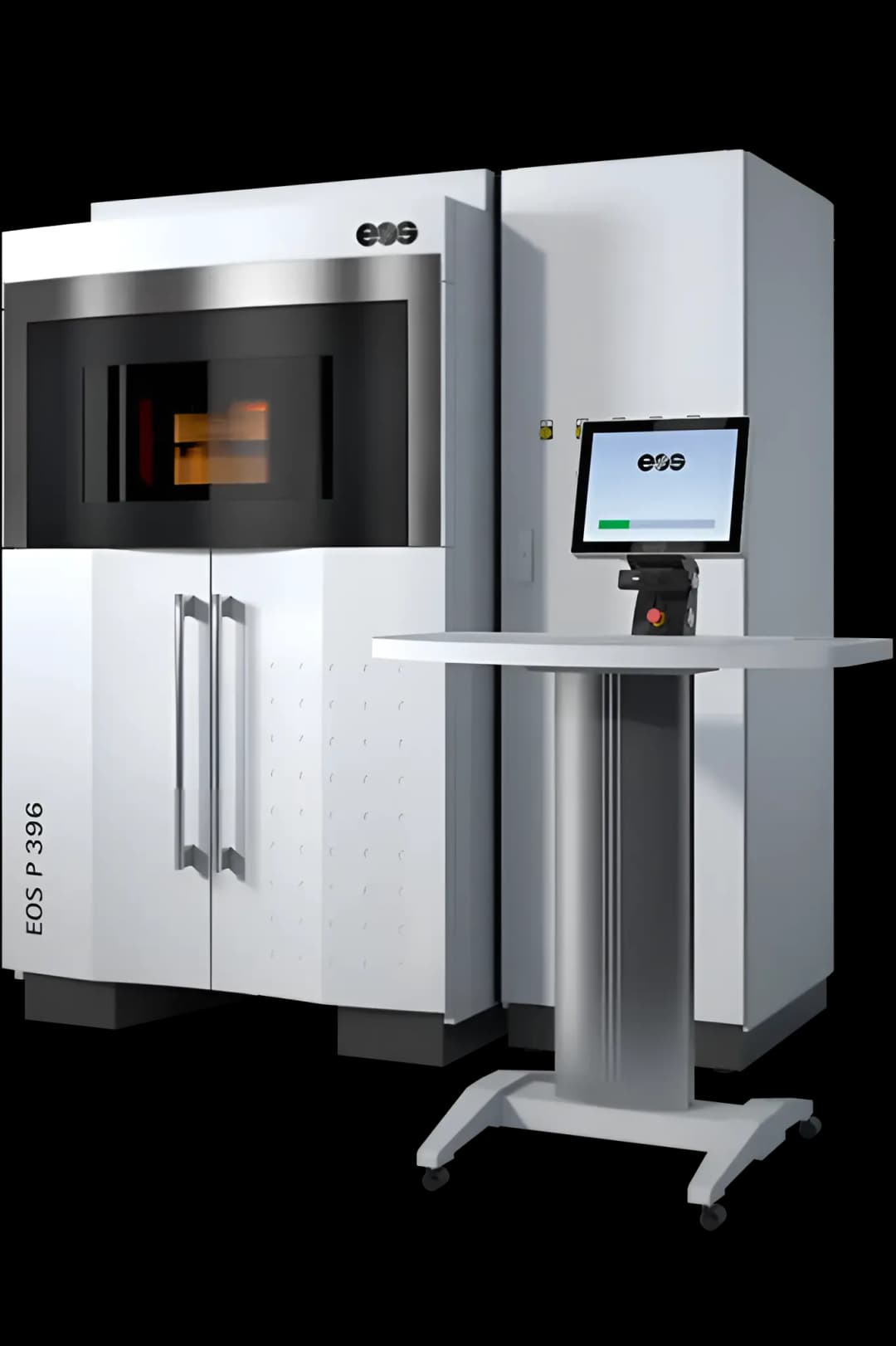
EOS P396 SLS System - Industrial-grade selective laser sintering
What is FDM 3D Printing?
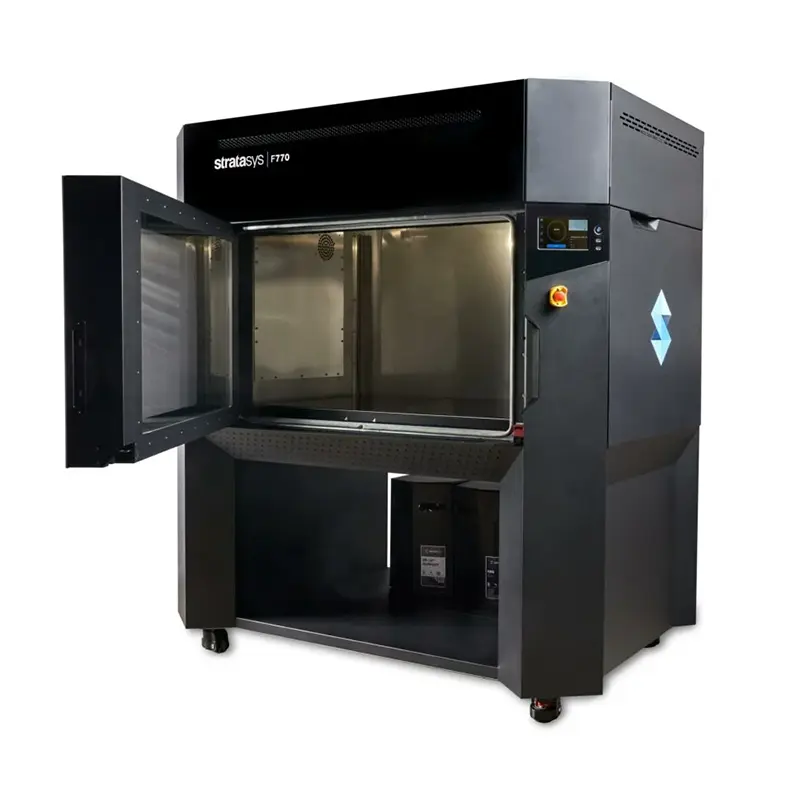
Stratasys F770 FDM System - Large-format fused deposition modeling
Fused Deposition Modeling (FDM), also known as Fused Filament Fabrication (FFF), is the most recognizable 3D printing technology. It works by heating thermoplastic filament to its melting point and extruding it through a nozzle that moves in precise patterns to build parts layer by layer.
The FDM Process Step-by-Step:
- Filament Heating: Thermoplastic filament is heated in the extruder to its melting point
- Material Extrusion: Molten plastic is extruded through a nozzle onto the build platform
- Layer Formation: The nozzle traces the part geometry, depositing material in precise patterns
- Cooling: Each layer cools and solidifies before the next layer is applied
- Support Removal: Support structures are removed after printing (if required)
Key Differences: SLS vs FDM
Understanding the fundamental differences between these technologies is crucial for selecting the right process for your application:
🕐 Build Speed & Efficiency
SLS Advantages:
- • Entire layer sintered simultaneously
- • Multiple parts can be nested efficiently
- • No support structures required
- • Higher part density per build
FDM Considerations:
- • Nozzle must trace each layer sequentially
- • Support structures may be required
- • Faster cooling between layers
- • Build time scales with part complexity
♻️ Material Efficiency & Waste
SLS excels in material efficiency since unfused powder can be collected, sieved, and reused for future builds. No support structures are needed, as surrounding powder supports overhanging features during the build process.
FDM may require support structures for overhanging geometries, which are removed and discarded after printing. However, modern FDM systems use soluble support materials that can be dissolved away, reducing waste.
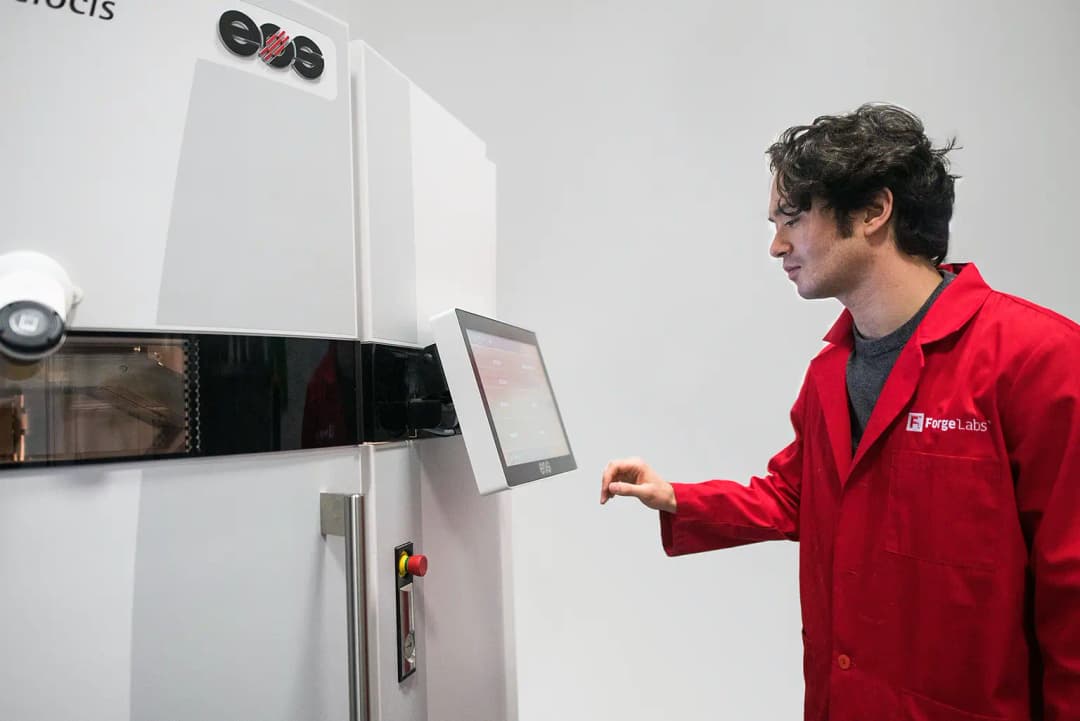
SLS production environment showing powder bed efficiency
💪 Mechanical Properties & Strength
SLS Material Properties:
- • Isotropic strength: Uniform properties in all directions
- • Higher temperature resistance: Suitable for demanding applications
- • Superior surface finish: Minimal layer lines
- • Complex geometries: No design restrictions for overhangs
FDM Material Properties:
- • Anisotropic strength: Layer adhesion affects directional strength
- • Wide material range: From basic plastics to high-performance polymers
- • Visible layer lines: May require post-processing for smooth finishes
- • Design considerations: Overhangs limited to ~45° without supports
🎯 Precision & Detail Resolution
SLS achieves superior detail resolution due to the precision of laser sintering. Typical layer heights range from 0.1-0.15mm, with feature resolution down to 0.3mm. The powder bed fusion process eliminates the "stair-stepping" effect common in other technologies.
FDM resolution is limited by nozzle diameter (typically 0.4mm) and layer height (0.1-0.3mm). While modern FDM systems achieve excellent results, fine details may require smaller nozzles and longer print times.
💰 Cost Considerations
SLS Cost Factors:
- • Higher equipment costs: Industrial-grade systems
- • Material costs: Specialized powders
- • Lower per-part costs: High build density
- • Minimal post-processing: Parts often ready to use
FDM Cost Factors:
- • Lower equipment costs: Desktop to industrial options
- • Affordable materials: Wide range of filament prices
- • Support material costs: Additional material usage
- • Post-processing: Support removal and finishing
Material Options Comparison
SLS Materials Available at Forge Labs:
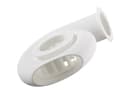
Nylon PA12
Excellent mechanical properties, chemical resistance
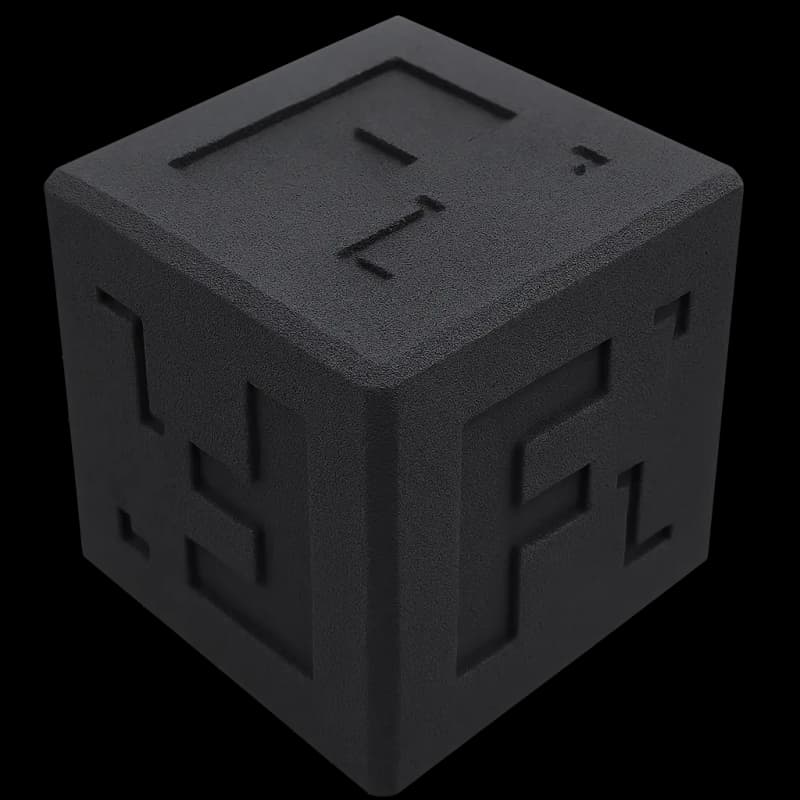
FDM Materials Available at Forge Labs:
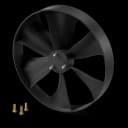
ABS & ASA
Durable, impact-resistant thermoplastics
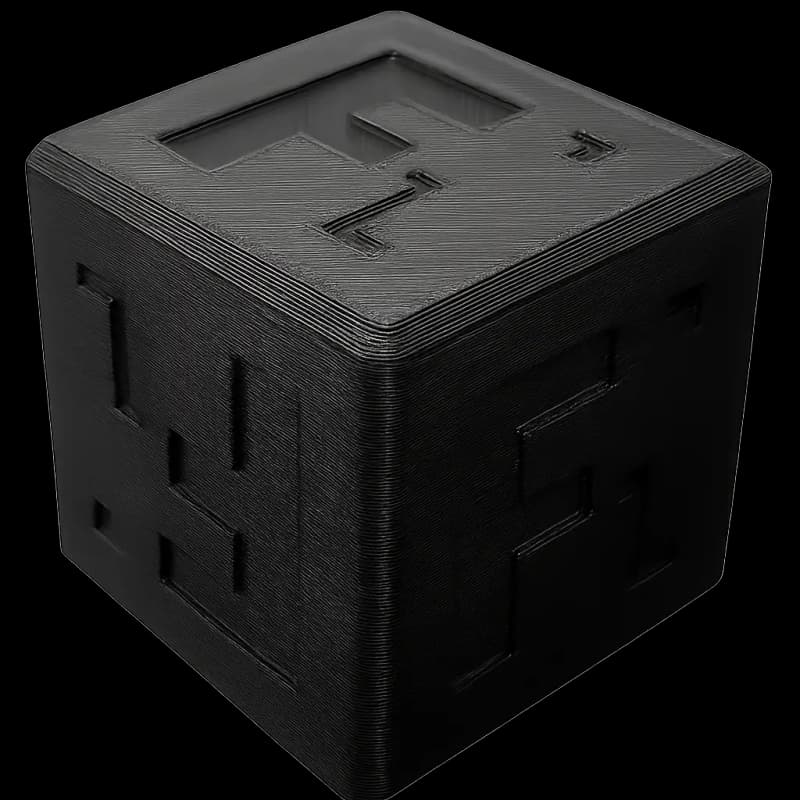
Industry Applications
🚗 Automotive Industry
The automotive sector leverages both technologies extensively. SLS excels in producing functional prototypes, end-use parts, and complex geometries like air ducts with integrated mounting features.
FDM is ideal for tooling, jigs, fixtures, and large-format parts where build volume is critical.
✈️ Aerospace Applications
Aerospace manufacturers utilize SLS for lightweight, complex components that meet stringent performance requirements. The technology's ability to create parts with internal channels and lattice structures makes it invaluable for weight reduction initiatives.
FDM serves the industry with certified materials like ULTEM for interior components and tooling applications.
🏥 Medical Device Manufacturing
Both technologies play crucial roles in medical applications. SLS produces patient-specific implants, surgical guides, and prosthetics with biocompatible materials.
FDM creates anatomical models, surgical instruments, and custom medical devices using USP Class VI certified materials.
"The choice between SLS and FDM often comes down to part geometry, material requirements, and production volume. SLS excels for complex, high-performance parts, while FDM offers versatility and cost-effectiveness for a wide range of applications." - Forge Labs Application Engineering Team
Rapid Prototyping: SLS vs FDM
Both technologies revolutionize the prototyping process, but each serves different needs:
When to Choose SLS for Prototyping:
- ✓Complex geometries with overhangs, undercuts, or internal features
- ✓Functional prototypes requiring isotropic mechanical properties
- ✓Multiple design iterations requiring consistent material properties
- ✓Parts that will transition directly to production using the same process
- ✓High-detail prototypes with fine features and smooth surfaces
When to Choose FDM for Prototyping:
- ✓Large-scale prototypes that exceed SLS build volumes
- ✓Concept models and form-fit studies
- ✓Budget-conscious projects with simple geometries
- ✓Rapid iteration cycles requiring quick turnaround
- ✓Prototypes requiring specific material properties (transparency, flexibility)
Design Guidelines
SLS Design Considerations:
FDM Design Considerations:
Future Trends & Innovations
Both SLS and FDM technologies continue evolving with exciting developments:
🔬SLS Advancements:
⚡FDM Innovations:
Making the Right Choice
Selecting between SLS and FDM depends on several key factors:
Choose SLS When:
- • Complex geometries with overhangs or internal features
- • High-performance mechanical properties required
- • Superior surface finish is critical
- • Multiple parts can be nested efficiently
- • Isotropic strength properties needed
Choose FDM When:
- • Large parts exceed SLS build volume constraints
- • Budget considerations are primary
- • Specific material properties required (transparency, extreme flexibility)
- • Simple geometries without complex overhangs
- • Rapid prototyping with quick turnaround needed
Partner with Forge Labs
As a leading provider of advanced 3D printing services, Forge Labs offers both SLS and FDM technologies with comprehensive material options and expert application engineering support. Our team helps you select the optimal technology for your specific requirements, ensuring successful outcomes from prototype to production.
Ready to get started? Upload your CAD files to our instant quoting platform or speak with our application engineers to discuss your project requirements. We'll help you navigate the technology selection process and deliver exceptional results.
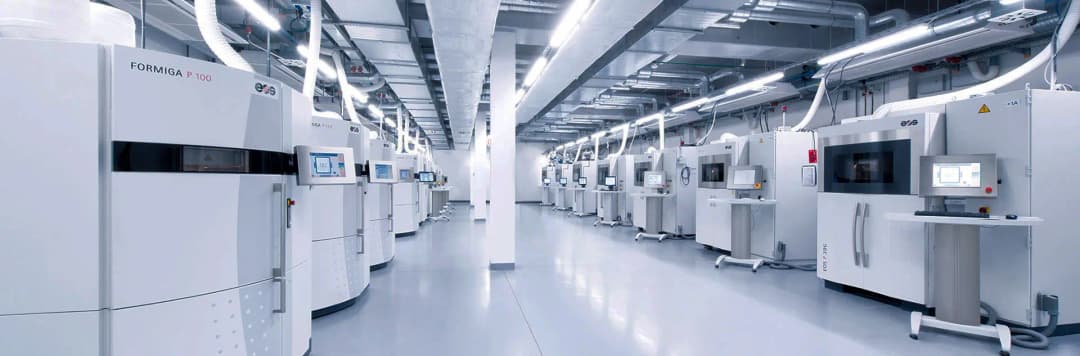
State-of-the-art SLS manufacturing facility at Forge Labs
Key Takeaways:
- • SLS excels for complex geometries, superior mechanical properties, and high part density
- • FDM offers cost-effectiveness, large build volumes, and diverse material options
- • Both technologies serve distinct roles in modern manufacturing workflows
- • Material selection and part geometry are primary decision factors
- • Expert consultation ensures optimal technology selection for your application