Technology Selection Framework
Selecting the optimal 3D printing technology requires comprehensive analysis of material properties, application requirements, and manufacturing constraints. This guide provides detailed technical comparisons across five critical performance metrics to inform strategic technology decisions.
3D printing technologies have fundamentally revolutionized manufacturing and prototyping approaches across industries, offering unprecedented design freedom and rapid iteration capabilities. However, the diverse array of available technologies—each with distinct advantages, limitations, and optimal applications—requires sophisticated understanding for strategic implementation.
This comprehensive analysis examines five prominent additive manufacturing technologies: Selective Laser Sintering (SLS), Stereolithography (SLA), Fused Deposition Modeling (FDM), PolyJet Matrix, and Multi Jet Fusion (MJF). Our evaluation focuses on five critical performance metrics that directly impact application suitability: strength, flexibility, durability, heat deflection temperature, and surface finish quality.
These technologies serve diverse applications across aerospace, automotive, medical device manufacturing, and industrial design sectors, where material performance characteristics directly influence product success and regulatory compliance.
Technology Overview and Fundamental Principles
Understanding the fundamental operating principles of each technology provides essential context for performance characteristic analysis. Each additive manufacturing approach employs distinct material processing mechanisms that directly influence final part properties and application suitability.
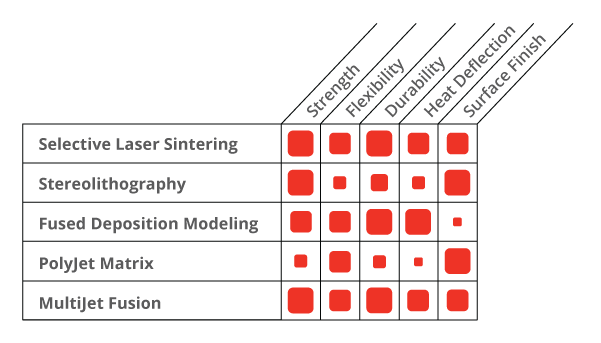
Selective Laser Sintering (SLS)
Utilizes high-powered laser systems to selectively sinter powdered thermoplastic materials, creating solid structures through layer-by-layer fusion. Excellent for complex geometries and functional prototypes.

Stereolithography (SLA)
Employs precision laser systems to photopolymerize liquid photopolymer resins through controlled UV exposure, producing parts with exceptional surface finish and dimensional accuracy.

Fused Deposition Modeling (FDM)
Extrudes heated thermoplastic filaments through precision nozzles, depositing material layer by layer. Offers extensive material versatility and excellent strength characteristics.

PolyJet Matrix
Jets and instantly cures photopolymer droplets using UV light, enabling multi-material printing and exceptional surface finish quality for detailed prototypes and visual models.

Multi Jet Fusion (MJF)
Deploys inkjet arrays to selectively apply fusing agents across nylon powder beds, followed by infrared heating for controlled fusion. Optimized for production-scale manufacturing.
Technology Selection Quick Reference
Best for Strength
SLS with reinforced materials, FDM with high-performance thermoplastics (ULTEM, PEEK)
Best for Surface Finish
SLA and PolyJet for exceptional detail and smooth surfaces right from the printer
Best for Production
MJF for consistent quality at scale, SLS for complex geometries and batch production
Comprehensive Strength Analysis
Mechanical strength represents the fundamental capacity of materials to resist deformation, fracture, or failure under applied forces. In additive manufacturing, strength characteristics are influenced by material properties, build orientation, layer adhesion, internal structure, and post-processing treatments.
Critical Strength Factors in 3D Printing
Material Properties
- • Tensile strength and yield strength
- • Flexural and compressive strength
- • Impact resistance and fatigue properties
- • Molecular structure and crystallinity
Manufacturing Variables
- • Layer thickness and infill density
- • Build orientation and anisotropy
- • Interlayer adhesion quality
- • Post-processing and thermal treatment
Technology-Specific Strength Characteristics
Selective Laser Sintering (SLS)
SLS technology produces parts with exceptional strength and stiffness characteristics, achieving tensile strengths of 48-55 MPa with Nylon PA12 materials. The powder bed fusion process creates highly isotropic parts with minimal directional weakness, making SLS ideal for structural applications requiring consistent mechanical properties.
Impact resistance and fatigue performance are particularly notable, with SLS parts demonstrating excellent resistance to cyclic loading. Glass fiber and carbon fiber reinforcement options can increase tensile strength to 85+ MPa, positioning SLS as the preferred choice for demanding aerospace and automotive applications.
Stereolithography (SLA)
SLA technology produces parts with high tensile strength (55-65 MPa) and exceptional dimensional accuracy, particularly when utilizing high-performance resins. However, photopolymer materials tend to exhibit brittle characteristics with lower impact resistance compared to thermoplastic alternatives.
The UV-cured structure provides excellent short-term strength but may experience degradation over time due to continued UV exposure and moisture absorption. Post-curing processes can significantly improve mechanical properties, with some formulations achieving strength values comparable to injection molded parts.
Fused Deposition Modeling (FDM)
FDM technology offers moderate to excellent strength characteristics depending on material selection and print parameters. Standard materials like ABS achieve tensile strengths of 22-35 MPa, while high-performance options like ULTEM 9085 can reach 85+ MPa with exceptional chemical resistance.
The primary limitation involves anisotropic properties due to layer-by-layer construction, resulting in reduced strength perpendicular to layer planes. However, strategic orientation and advanced materials enable FDM to serve demanding applications in aerospace and industrial manufacturing.
PolyJet Matrix
PolyJet technology prioritizes surface finish and detail over mechanical strength, typically achieving tensile strengths of 50-65 MPa with rigid materials. While adequate for many prototyping applications, the photopolymer base limits suitability for high-stress structural components.
The unique multi-material capability enables gradient properties within single parts, allowing for strategic reinforcement in critical areas while maintaining flexibility in others—a characteristic particularly valuable for medical device manufacturing and specialized tooling applications.
Multi Jet Fusion (MJF)
MJF technology delivers exceptional strength characteristics comparable to injection molded parts, with Nylon PA12 achieving tensile strengths of 48-52 MPa and excellent impact resistance. The uniform thermal fusion process creates highly consistent mechanical properties throughout the part volume.
The technology's production-oriented design enables consistent quality at scale, making MJF particularly valuable for end-use part manufacturing where strength requirements must be maintained across high-volume production runs.
Flexibility and Elastomeric Properties
Flexibility represents the material's ability to undergo elastic deformation without permanent damage or failure. This characteristic is critical for applications requiring conformable parts, gaskets, living hinges, or components subject to dynamic loading conditions.
Technology | Flexible Materials | Shore Hardness Range | Applications |
---|---|---|---|
SLS | TPU 88A, Flexible Nylon | Shore A 85-95 | Gaskets, Cushioning, Footwear |
SLA | Flexible Resins, Elastic 50A | Shore A 40-80 | Prototypes, Medical Models |
FDM | TPU, TPE, Flexible PLA | Shore A 85-95 | Phone Cases, Toys, Seals |
PolyJet | Agilus30, TangoBlack+ | Shore A 30-95 | Multi-material, Overmolding |
MJF | TPU 88A | Shore A 85-90 | Production Parts, Tooling |
Durability and Environmental Resistance
Durability encompasses a material's ability to maintain performance characteristics over extended periods or under challenging environmental conditions. This includes resistance to wear, chemical exposure, UV degradation, thermal cycling, and mechanical fatigue.
Environmental Stress Factors
Chemical Exposure
- • Solvent resistance
- • Acid/base compatibility
- • Fuel and oil resistance
Environmental Conditions
- • UV radiation exposure
- • Thermal cycling effects
- • Humidity and moisture
Mechanical Wear
- • Abrasion resistance
- • Fatigue life cycles
- • Creep under load
Technology-Specific Durability Analysis
SLS and MJF technologies excel in durability applications due to their thermoplastic material base and uniform material distribution. These technologies can withstand harsh environmental conditions and repeated stress cycles, making them optimal for automotive under-hood components and aerospace structural elements.
FDM technology offers exceptional durability when utilizing engineering-grade materials like ULTEM or PEEK, which provide outstanding chemical resistance and thermal stability. SLA and PolyJet technologies typically require environmental protection but excel in controlled indoor applications where precision and surface quality are paramount.
Heat Deflection Temperature Analysis
Heat Deflection Temperature (HDT) represents the temperature at which materials experience significant deformation under standardized loading conditions. This metric is critical for applications exposed to elevated temperatures, particularly in automotive under-hood components and aerospace applications.
Technology | Standard Materials HDT | High-Temp Materials HDT | Max Service Temp |
---|---|---|---|
SLS | PA12: 80°C | Glass-filled: 120°C | 150°C continuous |
SLA | Standard: 45-60°C | High-temp: 190°C | 200°C intermittent |
FDM | ABS: 98°C | ULTEM 9085: 186°C | 250°C continuous |
PolyJet | 40-50°C | 85°C (specialized) | 100°C short-term |
MJF | PA12: 85°C | PA11: 135°C | 160°C continuous |
Surface Finish Quality and Post-Processing Requirements
Surface finish quality directly impacts both aesthetic appeal and functional performance, influencing factors such as friction, wear resistance, sealing effectiveness, and biocompatibility. Each technology produces characteristic surface textures requiring different post-processing approaches.
Superior Surface Finish
SLA & PolyJet
Ra 0.5-2.0 μm as-printed, minimal post-processing required
Applications
Visual prototypes, master patterns, detailed models
Functional Surface Finish
SLS, MJF & FDM
Ra 5-25 μm as-printed, post-processing available
Applications
Functional prototypes, end-use parts, tooling
Strategic Technology Selection Framework
Optimal technology selection requires systematic evaluation of application requirements against technology capabilities. The following decision matrix provides guidance for technology selection based on primary performance requirements and application constraints.
Technology Selection Decision Matrix
Strength Priority Applications
Recommended: SLS, MJF, FDM (High-Performance)
- • Structural components
- • Load-bearing assemblies
- • Mechanical testing prototypes
- • End-use production parts
Surface Finish Priority
Recommended: SLA, PolyJet
- • Visual prototypes
- • Master patterns
- • Detailed models
- • Film props
High-Temperature Applications
Recommended: FDM (ULTEM), SLA (High-Temp)
- • Under-hood automotive
- • Aerospace components
- • Industrial tooling
- • High-temp testing
Industry-Specific Technology Applications
Each industry sector presents unique requirements that favor specific technology selections. Understanding these sector-specific preferences enables optimal technology matching for specialized applications and regulatory compliance requirements.
Aerospace Industry
Requirements: High strength-to-weight ratio, temperature resistance, regulatory compliance
Primary Technologies:
FDM (ULTEM, PEEK), SLS (Carbon Fiber Nylon)
Applications:
Ducting, brackets, interior components, tooling
Medical Device Manufacturing
Requirements: Biocompatibility, sterilization compatibility, precision
Primary Technologies:
SLA (USP VI), PolyJet (Multi-material), SLS
Applications:
Surgical guides, implants, anatomical models
Comprehensive Performance Summary
The comparative analysis reveals that no single technology provides optimal performance across all metrics. Strategic technology selection requires careful consideration of primary application requirements, secondary performance characteristics, and economic constraints.
Key Technology Recommendations
Maximum Strength & Durability:
SLS with reinforced materials or FDM with high-performance thermoplastics
Optimal Surface Finish:
SLA for detailed parts, PolyJet for multi-material applications
Production-Scale Manufacturing:
MJF for consistent quality and throughput optimization
High-Temperature Performance:
FDM with ULTEM/PEEK or specialized high-temperature SLA resins
The evolution of additive manufacturing continues to expand material options and improve performance characteristics across all technologies. Future developments in hybrid processing, advanced materials, and post-processing automation will further enhance the competitive positioning of each technology for specific application sectors.
Expert Technology Consultation
Selecting the optimal 3D printing technology for your specific application requires comprehensive analysis of performance requirements, material properties, and manufacturing constraints. Our technology specialists provide detailed guidance to ensure optimal outcomes.
Contact our engineering team for personalized technology recommendations and application analysis.
Phone: 1-877-329-9131 | Email: sales@forgelabs.com