Understanding 3D printing costs involves more than just material expenses. From machine depreciation to labor overhead, multiple factors influence the final price of your parts. This comprehensive guide breaks down the cost structure across different technologies and provides actionable strategies for optimizing your 3D printing projects for maximum cost efficiency.
Key Cost Factors
- • Material Costs: Volume-based pricing with support material considerations
- • Runtime Costs: Machine depreciation and operational expenses
- • Labor Costs: Setup, post-processing, and quality control
- • Technology Selection: Each process has unique cost characteristics
- • Design Optimization: Significant impact on overall project economics
Understanding 3D Printing Cost Structure
The question "How much does 3D printing cost?" doesn't have a simple answer because pricing involves a complex interplay of technological, design, and operational factors. Unlike traditional manufacturing where tooling costs dominate economics, additive manufacturing operates on a fundamentally different cost model where material usage, machine time, and post-processing labor create the primary cost drivers.
Modern 3D printing services leverage sophisticated instant quoting systems that analyze uploaded CAD files within seconds, calculating part volume, surface area, bounding box dimensions, and geometric complexity. These systems provide immediate cost estimates across multiple technologies and materials, enabling rapid design iteration and cost optimization.
Professional Insight
Advanced quoting systems automatically optimize part nesting for technologies like SLS and MJF, passing efficiency savings directly to customers while flagging complex geometries for manual review.
The Three Pillars of 3D Printing Costs
Professional 3D printing costs break down into three primary categories, each with distinct optimization opportunities and technology-specific characteristics. Understanding these pillars enables strategic design decisions that can significantly impact project economics.
1. Material Costs: The Primary Cost Driver
Material costs typically represent 40-70% of total part cost, making material optimization the most impactful area for cost reduction. However, material costing varies significantly across technologies due to different support requirements, material utilization efficiencies, and waste factors.
Volume-Based Technologies (SLA, PolyJet, FDM)
Technologies requiring support structures base costs primarily on total material volume, including both part geometry and necessary supports. This creates direct optimization opportunities through design modifications that reduce support requirements or enable self-supporting orientations.
Strategic cost reduction techniques include:
- Hollowing strategies: Internal lattice structures can reduce material usage by 30-50% for appropriate geometries
- Support minimization: Design features like chamfers, draft angles, and bridge-optimized geometries
- Orientation optimization: Strategic part positioning to minimize support volume
- Thickness optimization: Avoiding unnecessarily thick walls while maintaining structural integrity
Design Tip
For dense geometries, implementing honeycomb internal structures or optimized lattices can reduce material costs by up to 50% while maintaining equivalent strength characteristics in many applications.
Powder Bed Technologies (SLS, MJF)
SLS and MJF technologies eliminate support structure requirements, as unsintered powder provides natural support during printing. However, these technologies introduce different cost considerations including bounding box optimization and surface area considerations that affect powder adhesion and removal complexity.
Cost factors specific to powder bed technologies:
- Bounding Box Impact: Print chamber utilization affects per-part costs through build efficiency
- Surface Area Considerations: Complex surface geometries increase powder removal labor
- Material Refresh Requirements: Powder degradation necessitates periodic material replacement
- Packing Efficiency: Multiple parts can share build space without additional material costs
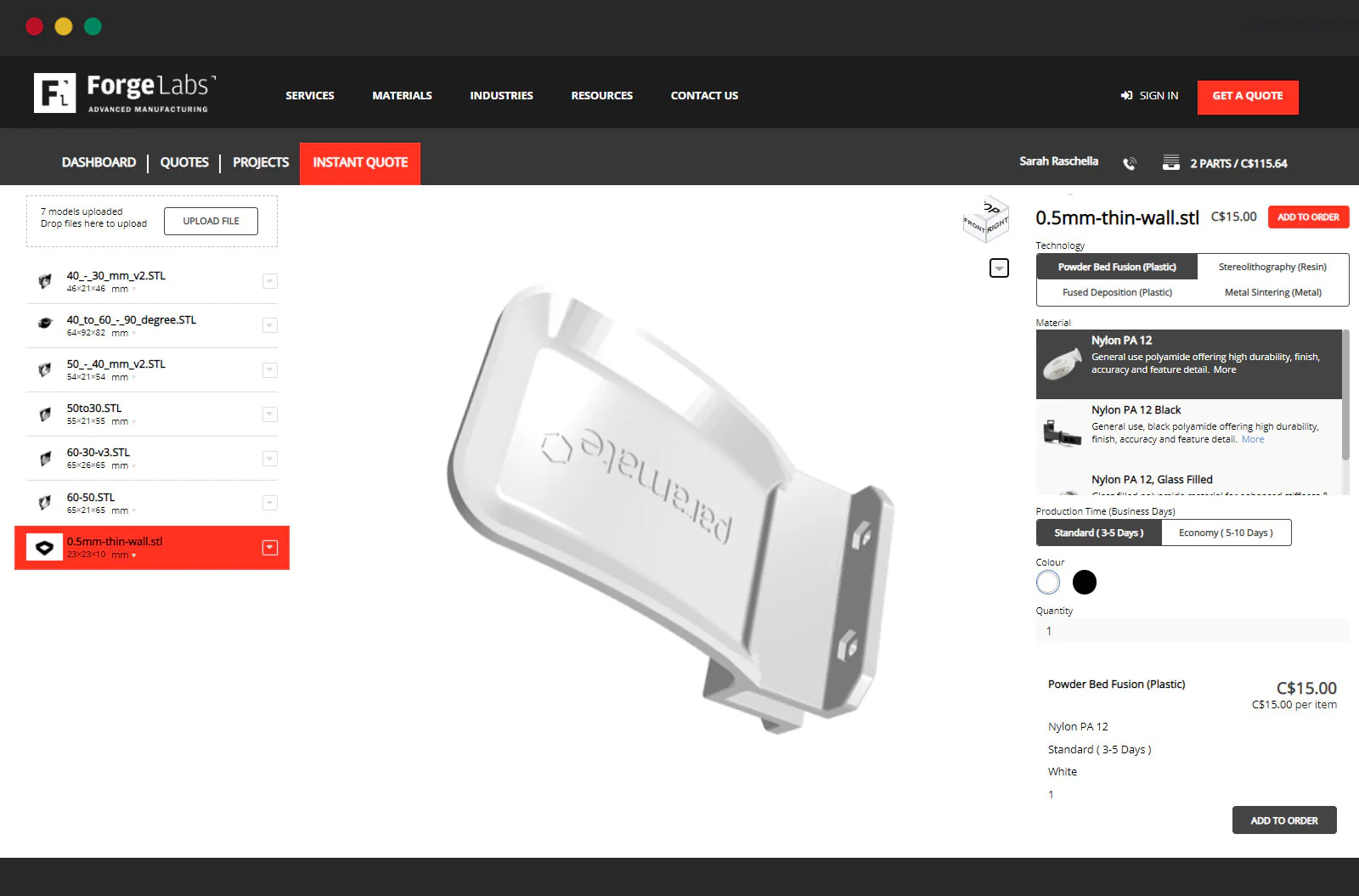
2. Runtime Costs: Machine Economics
Runtime costs reflect the capital investment in 3D printing equipment, which ranges from $140,000 to $380,000 for industrial systems. These costs are amortized over machine lifespan and annual operating hours, creating an hourly rate that varies by technology and part requirements.
Technology-Specific Runtime Characteristics
Different technologies exhibit distinct runtime cost patterns based on their printing mechanisms and speed limitations:
Technology | Speed Factor | Runtime Impact | Optimization Strategy |
---|---|---|---|
SLS/MJF | Layer-based | Minimal for small parts | Efficient packing |
FDM | Height-dependent | Significant for tall parts | Minimize Z-height |
SLA | Height-dependent | Moderate | Optimize orientation |
DMLS | Volume-dependent | High overall | Topology optimization |
Runtime Optimization Strategies
Effective runtime cost management requires understanding each technology's primary time drivers and designing accordingly:
- Orientation Optimization: Minimize Z-height for FDM and SLA technologies
- Build Volume Utilization: Consolidate multiple parts into single builds when possible
- Geometry Simplification: Reduce unnecessary complexity that extends print times
- Support Structure Minimization: Reduce post-processing time and material waste
3. Labor Costs: Human Expertise Requirements
Despite automation advances, skilled labor remains essential for setup, monitoring, post-processing, and quality control. Labor costs vary significantly by technology and part complexity, representing 20-40% of total costs depending on the application.
Setup and Planning Labor
While CAD file preprocessing is largely automated, skilled technicians remain essential for:
- File Validation: Ensuring geometric integrity and printability
- Orientation Planning: Optimizing part placement for quality and efficiency
- Support Strategy: Balancing support effectiveness with removal complexity
- Build Planning: Maximizing chamber utilization while maintaining quality
Design files that conform to technology guidelines and are free from geometric errors minimize setup time and associated costs. Clear documentation and standard CAD practices significantly reduce preparation requirements.
Post-Processing Labor Requirements
Post-processing labor varies dramatically by technology and part complexity, creating significant cost implications:
Minimal Post-Processing
- • SLS/MJF: Powder removal (5-10 minutes)
- • FDM: Support removal (5-15 minutes)
- • Automated processes dominate
- • Predictable labor requirements
Intensive Post-Processing
- • SLA/PolyJet: Washing and curing (15-30 minutes)
- • DMLS: Support removal and finishing (30-60 minutes)
- • Complex manual operations
- • Higher per-part startup costs
Quality Control and Inspection
Professional additive manufacturing operations implement comprehensive quality control protocols, particularly for functional and end-use applications. ISO 9001:2015 quality inspection includes:
- Visual Inspection: Surface quality, dimensional accuracy, defect identification
- Dimensional Verification: Critical measurement validation
- Material Property Validation: Mechanical testing for critical applications
- Documentation: Traceability and compliance reporting
Technology-Specific Cost Analysis
Each 3D printing technology exhibits unique cost characteristics that influence optimal application areas and design strategies. Understanding these patterns enables informed technology selection and cost optimization.
Selective Laser Sintering (SLS) Economics
SLS technology offers excellent economics for complex geometries and batch production due to its support-free nature and excellent packing efficiency. Cost advantages become particularly pronounced for:
- Complex Internal Geometries: No support structure penalties
- Batch Production: Multiple parts share build chamber efficiently
- Organic Shapes: No design complexity penalties for smooth, curved surfaces
- Functional Prototypes: Excellent material properties at competitive costs
Cost optimization strategies for SLS include maximizing build chamber utilization, designing parts that nest efficiently, and leveraging the technology's geometric freedom for material-efficient designs.
Multi Jet Fusion (MJF) Cost Advantages
MJF builds upon SLS economics while offering superior surface finish and material properties. The technology excels in applications requiring:
- High Volume Production: Excellent throughput and material utilization
- Superior Surface Quality: Reduced post-processing requirements
- Consistent Material Properties: Reliable mechanical characteristics
- Efficient Packing: Optimized chamber utilization algorithms
Stereolithography (SLA) Cost Considerations
SLA offers exceptional surface quality and dimensional accuracy but requires careful cost management due to support structure requirements and post-processing intensity. Optimal applications include:
- High-Detail Parts: Superior surface finish justifies processing costs
- Small Components: Material costs remain reasonable for compact geometries
- Visual Prototypes: Appearance quality matches or exceeds injection molded parts
- Master Patterns: Excellent dimensional accuracy for tooling applications
Fused Deposition Modeling (FDM) Economics
FDM provides cost-effective solutions for larger parts and engineering materials, with economics favoring:
- Large Components: Competitive material costs for substantial volumes
- Engineering Materials: Access to high-performance thermoplastics
- Simple Geometries: Minimal support requirements reduce complexity
- Rapid Prototyping: Fast iteration cycles for design validation
Advanced Cost Optimization Strategies
Professional cost optimization extends beyond basic design modifications to encompass strategic manufacturing decisions, material selection, and process optimization.
Design for Additive Manufacturing (DfAM)
DfAM principles specifically target cost reduction while leveraging additive manufacturing capabilities:
- Part Consolidation: Combining multiple components into single prints
- Topology Optimization: Material distribution optimization for weight and cost reduction
- Lattice Structures: Internal geometry optimization for strength-to-weight ratios
- Multi-Functional Designs: Integrating multiple functions into single components
Material Selection Economics
Strategic material selection balances performance requirements with cost considerations across multiple factors:
Material Category | Cost Level | Applications | Value Proposition |
---|---|---|---|
Standard Polymers | Low | Prototyping, concept models | Cost-effective validation |
Engineering Plastics | Medium | Functional prototypes, tooling | Performance-cost balance |
High-Performance Polymers | High | End-use parts, critical applications | Superior properties justify cost |
Metal Alloys | Very High | Aerospace, medical implants | Unique capabilities |
Batch Production Optimization
Economies of scale in additive manufacturing operate differently than traditional manufacturing, creating unique optimization opportunities:
- Build Chamber Utilization: Maximizing part density per build
- Setup Amortization: Spreading preparation costs across multiple parts
- Material Efficiency: Reducing waste through optimized planning
- Processing Batch Economies: Simultaneous post-processing of multiple parts
Industry-Specific Cost Considerations
Different industries exhibit unique cost sensitivities and optimization priorities that influence technology selection and design strategies.
Aerospace Applications
Aerospace manufacturing prioritizes weight reduction and part consolidation, often justifying premium materials and processes for:
- Weight Savings Value: Fuel efficiency improvements offset higher manufacturing costs
- Part Consolidation: Reducing assembly complexity and inventory costs
- Performance Materials: High-temperature and lightweight alloys justify premium pricing
- Rapid Prototyping: Accelerated development cycles reduce time-to-market costs
Medical Device Economics
Medical device applications emphasize customization and biocompatibility, creating distinct cost-value relationships:
- Mass Customization: Patient-specific devices command premium pricing
- Biocompatible Materials: Specialized materials justify higher costs for safety
- Regulatory Compliance: Quality control costs offset by improved patient outcomes
- Small Batch Production: Economic viability for limited production runs
Automotive Cost Optimization
Automotive applications focus on tooling cost reduction and rapid prototyping, with optimization strategies including:
- Tooling Alternatives: 3D printed jigs and fixtures reduce capital investment
- Rapid Prototyping: Faster iteration cycles reduce development costs
- Low-Volume Production: Economic alternative for specialized components
- Customization Capabilities: Cost-effective personalization options
Instant Quoting Technology and Cost Transparency
Modern instant quoting systems represent a significant advancement in cost transparency and project planning, enabling real-time cost optimization during the design process.
Automated Cost Calculation
Sophisticated algorithms analyze uploaded CAD files to extract critical cost-driving parameters:
- Volume Analysis: Precise material quantity calculations
- Surface Area Assessment: Post-processing complexity estimation
- Bounding Box Optimization: Build chamber utilization calculations
- Geometric Complexity: Automated support requirement estimation
Real-Time Cost Optimization
Advanced systems provide immediate feedback for design modifications, enabling iterative cost optimization:
- Material Comparison: Instant cost differences across material options
- Technology Selection: Comparative analysis across printing processes
- Quantity Optimization: Economies of scale visualization
- Design Feedback: Automated suggestions for cost reduction
Future Trends in 3D Printing Economics
The economic landscape of additive manufacturing continues evolving through technological advancement, material innovation, and process optimization.
Automation and Labor Cost Reduction
Increasing automation in post-processing and quality control reduces labor components while improving consistency:
- Automated Support Removal: Mechanical and chemical removal systems
- Intelligent Post-Processing: Robotic finishing and surface treatment
- Quality Control Automation: Machine vision and automated inspection
- Process Monitoring: Real-time quality control reducing rework costs
Material Cost Trends
Material costs continue declining through increased competition, improved processing, and economies of scale:
- Commodity Materials: Standard polymers approaching traditional manufacturing costs
- Specialized Formulations: High-performance materials becoming more accessible
- Recycling Integration: Sustainable materials reducing raw material costs
- Local Production: Reduced transportation and inventory costs
Practical Cost Optimization Checklist
Implementing systematic cost optimization requires attention to design, technology selection, and manufacturing strategy decisions.
Design Optimization
- ✓ Minimize support structure requirements through strategic orientation
- ✓ Implement internal lattices or honeycomb structures for material reduction
- ✓ Optimize wall thickness for strength requirements
- ✓ Consider part consolidation opportunities
- ✓ Design for specific technology capabilities and limitations
Technology Selection
- ✓ Match technology capabilities to application requirements
- ✓ Consider total cost of ownership including post-processing
- ✓ Evaluate material options within technology constraints
- ✓ Assess volume requirements for batch production benefits
- ✓ Factor quality requirements into technology selection
Production Strategy
- ✓ Optimize batch sizes for build chamber utilization
- ✓ Coordinate production timing for material efficiency
- ✓ Plan post-processing workflows for labor optimization
- ✓ Implement quality control appropriate to application criticality
- ✓ Consider outsourcing versus in-house production economics
Conclusion: Strategic Cost Management in 3D Printing
Effective 3D printing cost management requires understanding the complex interplay between design decisions, technology capabilities, and production strategies. Unlike traditional manufacturing where tooling costs dominate early stages, additive manufacturing enables continuous cost optimization throughout the design and production process.
The key to successful cost optimization lies in early-stage design decisions that consider material usage, support requirements, and post-processing complexity. Advanced instant quoting systems provide immediate feedback for design iterations, enabling real-time cost optimization during development.
As the technology continues maturing, costs continue declining through automation, material improvements, and process optimization. Organizations that understand these cost drivers and implement systematic optimization strategies will realize the greatest value from additive manufacturing investments.
The future of 3D printing economics points toward increased automation, material cost reduction, and improved process efficiency. By staying informed about these trends and implementing best practices, manufacturers can leverage additive manufacturing for cost-effective production across an expanding range of applications.
Ready to Optimize Your 3D Printing Costs?
Our instant quoting system provides immediate cost analysis across multiple technologies and materials, enabling real-time design optimization for maximum cost efficiency.
Get instant pricing for your project, or consult with our experts for advanced cost optimization strategies.