Metal 3D Printing: Advanced Design Techniques for DMLS Optimization
Master sophisticated design strategies for Direct Metal Laser Sintering (DMLS) to unlock complex geometries, optimize performance, and achieve manufacturing excellence in industrial applications.
Ron Luther
Manufacturing Specialist
Additive manufacturing in metal represents one of the most transformative technologies in modern manufacturing. As industries from aerospace to medical devices increasingly rely on metal 3D printing, understanding advanced design techniques becomes crucial for engineers and designers seeking to fully leverage DMLS's capabilities.
What You'll Learn
- • DMLS fundamentals and process capabilities
- • Critical design considerations for metal additive manufacturing
- • Advanced optimization techniques: topology, lattice structures, and generative design
- • Software tools and simulation methodologies
- • Post-processing integration strategies
- • Industry best practices for design-for-manufacture
Understanding DMLS Technology
Before diving into advanced design techniques, it's essential to grasp the fundamentals of Direct Metal Laser Sintering (DMLS). This process involves the use of a high-powered laser to selectively sinter powdered metal particles, layer by layer, to form solid metal parts with exceptional mechanical properties and geometric complexity.
Unlike traditional manufacturing methods such as machining or casting, DMLS can produce parts with complex internal geometries, integrated features, and high levels of customization without the need for tooling or fixtures. This freedom of design opens new possibilities for lightweighting, functional integration, and performance optimization that were previously impossible to achieve.
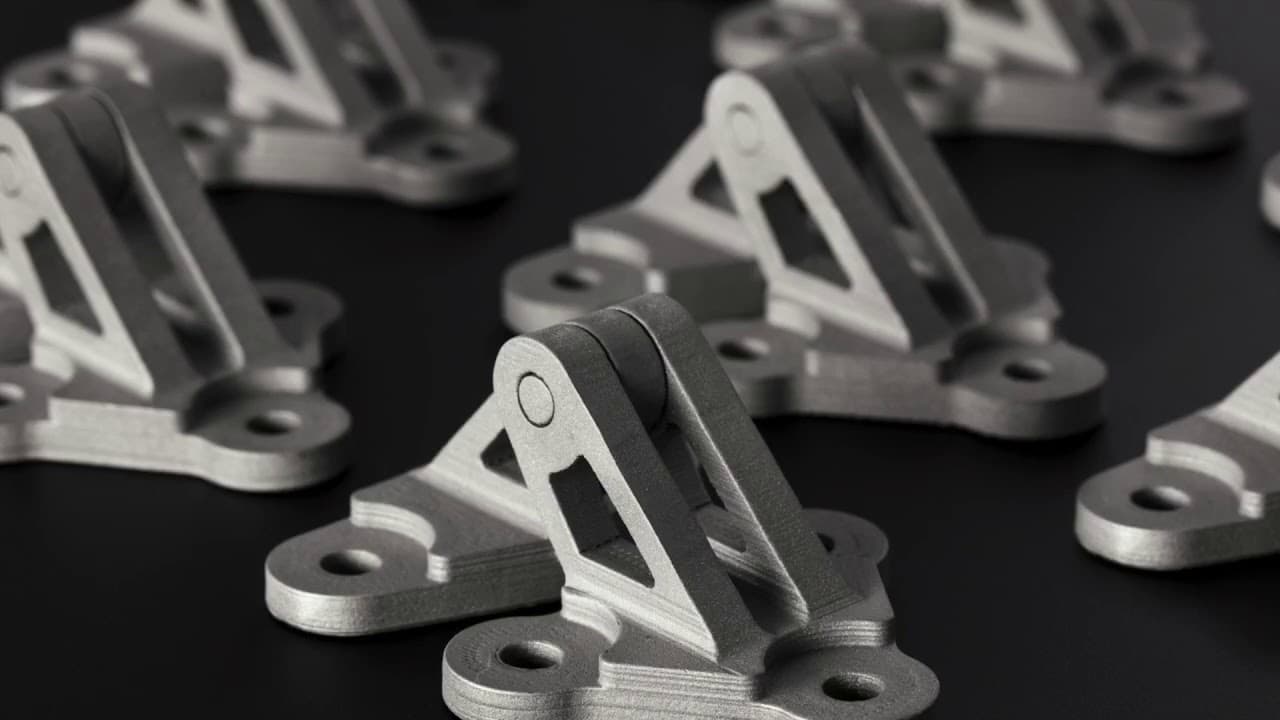
Critical Design Considerations for DMLS
When designing for DMLS, several key factors must be considered to ensure the success of the final product. These considerations span geometric constraints, material properties, thermal management, and post-processing requirements.
Part Orientation & Build Strategy
The orientation of a part on the build platform significantly affects surface quality, mechanical properties, and support structure requirements.
- • Surface finish optimization: Critical surfaces should face upward when possible
- • Anisotropic properties: Consider layer orientation for stress directions
- • Support minimization: Reduce overhangs below 45° when feasible
- • Build efficiency: Nest multiple parts for optimal powder utilization
Support Structure Design
Support structures are essential for overhanging features and thermal management during the build process.
- • Thermal anchoring: Dissipate heat to prevent warping and distortion
- • Removability: Design breakaway points for easy post-processing
- • Access considerations: Ensure tooling can reach support attachment points
- • Material efficiency: Minimize support volume while maintaining functionality
Feature Resolution & Tolerances
Understanding the resolution capabilities of DMLS systems is vital for designing manufacturable features.
- • Minimum wall thickness: 0.4mm for most alloys, material-dependent
- • Hole diameter limits: ≥1.0mm for round holes, ≥0.8mm for slots
- • Surface roughness: Ra 15-25μm as-built, Ra 0.4-0.8μm post-processed
- • Dimensional accuracy: ±0.1mm typical, ±0.05mm achievable
Thermal Management
DMLS involves rapid heating and cooling cycles that can introduce residual stresses and distortion.
- • Stress relief features: Incorporate gradual transitions and fillets
- • Uniform cooling: Avoid large solid sections that trap heat
- • Simulation validation: Use FEA to predict and mitigate distortion
- • Material selection: Choose alloys with appropriate thermal properties
Advanced Optimization Techniques
Beyond basic design considerations, several advanced techniques can be employed to maximize the unique capabilities of DMLS technology. These approaches leverage computational design tools and sophisticated algorithms to achieve performance outcomes impossible with conventional manufacturing.
Topology Optimization
Topology optimization software analyzes load conditions and constraints to optimize material distribution within a design, resulting in parts that are both lightweight and structurally efficient. This technique is particularly valuable in aerospace and automotive applications where weight reduction directly impacts performance and efficiency.
Leading Topology Optimization Software
Industrial Solutions
- • Altair HyperWorks (OptiStruct)
- • ANSYS Mechanical
- • Dassault Systèmes SIMULIA (Tosca)
- • Siemens NX
- • PTC Creo
Accessible Platforms
- • Autodesk Fusion 360
- • SolidWorks Simulation
- • nTopology
- • Grasshopper3D (with Karamba3D)
Lattice Structure Design
Lattice structures represent one of the most compelling applications of metal 3D printing technology. These repeating geometric patterns can be precisely tuned to achieve specific mechanical, thermal, or fluid flow properties while dramatically reducing weight and material consumption.
Lattice Design Methodology
1. Define Performance Requirements
Establish clear objectives such as weight reduction targets, stiffness requirements, thermal conductivity needs, or vibration damping characteristics.
2. Select Appropriate Lattice Geometry
Choose from proven geometries based on intended properties:
- • Cubic: Isotropic stiffness, simple manufacturability
- • Diamond: High strength-to-weight ratio, excellent energy absorption
- • Gyroid: Smooth stress distribution, superior fatigue performance
- • Honeycomb: Optimal for in-plane loading, efficient material use
3. Optimize Design Parameters
Cell Size: Balance between resolution and performance
Strut Thickness: Match to printer capabilities (≥0.3mm)
Density: Overall porosity affecting weight and strength
Gradation: Variable density for load path optimization
4. Validate Through Simulation
Use finite element analysis to predict mechanical behavior, identify stress concentrations, and optimize the design before physical testing.
Lattice Design Software Solutions
- • nTopology: Advanced lattice design and optimization
- • Autodesk Fusion 360: Generative design extension
- • ANSYS SpaceClaim: Lattice creation and analysis tools
- • Grasshopper (Rhino): Parametric lattice generation
- • SolidWorks: Integrated lattice design capabilities
- • Altair Inspire: Combined topology and lattice optimization
Generative Design Algorithms
Generative design represents the next evolution in engineering design methodology. By leveraging artificial intelligence and machine learning algorithms, these systems can explore vast design spaces to identify optimal solutions that human designers might never consider.
The process involves defining design goals, constraints, and manufacturing parameters, then allowing the algorithm to generate thousands of potential solutions. The key to success lies in properly defining the input parameters—following the principle of "garbage in, garbage out"—and understanding that the generated output typically requires further refinement to create a production-ready part.
Simulation and Analysis Integration
Utilizing simulation and finite element analysis (FEA) tools during the design process enables engineers to predict part performance under various conditions before committing to physical production. This approach is particularly valuable for identifying and addressing potential issues related to thermal stress, mechanical failure modes, and distortion.
Key Simulation Categories
Structural Analysis
- • Static stress analysis
- • Dynamic response
- • Fatigue life prediction
- • Buckling analysis
Thermal Simulation
- • Build process modeling
- • Residual stress prediction
- • Distortion analysis
- • Cooling optimization
Flow Analysis
- • Internal channel design
- • Heat exchanger optimization
- • Pressure drop analysis
- • Mixing efficiency
Post-Processing Integration Strategy
Designing with post-processing in mind significantly impacts both the efficiency and effectiveness of the DMLS workflow. This holistic approach considers support removal, surface finishing, machining operations, and quality inspection requirements from the initial design phase.
Design for Support Removal
- • Access planning: Ensure cutting tools can reach all support connections
- • Breakaway design: Create controlled failure points for clean removal
- • Surface protection: Position supports to minimize impact on critical surfaces
- • Stress relief: Consider residual stresses from support removal
Machining Considerations
- • Datum references: Include machining datums in the printed part
- • Stock allowances: Add material for critical dimensions
- • Tool access: Design clearances for cutting tools
- • Clamping surfaces: Provide adequate fixturing surfaces
Advanced Post-Processing Strategies
Experienced designers often integrate specialized post-processing aids directly into their designs, including custom jigs, fixtures, and tooling that can be printed alongside the primary workpiece.
Integrated Tooling
- • Print-in-place fixtures for machining operations
- • Custom gauges for quality inspection
- • Sacrificial supports for complex assemblies
Quality Assurance
- • Built-in measurement references
- • Test coupons for material verification
- • Witness marks for process validation
Industry Applications and Case Studies
These advanced design techniques have been successfully implemented across numerous industries, enabling breakthrough innovations in performance, efficiency, and functionality. Here are some real-world applications demonstrating the power of optimized DMLS design:
Aerospace Applications
Topology-optimized turbine components with integrated cooling channels achieve 30% weight reduction while maintaining thermal performance requirements.
- • Conformal cooling in engine components
- • Lattice-filled structural brackets
- • Generative-designed mounting brackets
Medical Device Innovation
Patient-specific implants with bone-integration lattice structures promote natural healing while reducing implant weight by up to 70%.
- • Porous titanium implants
- • Custom surgical guides
- • Biometric-optimized prosthetics
Expert Design Support at Forge Labs
At Forge Labs, our team of manufacturing specialists brings decades of experience in advanced metal 3D printing design optimization. We understand that successful DMLS implementation requires more than just understanding the technology—it demands deep expertise in design-for-manufacture principles, material science, and process optimization.
Whether you're developing next-generation aerospace components, optimizing automotive parts, or creating innovative marine applications, our design consultation services can help you unlock the full potential of metal additive manufacturing.
Our Design Optimization Services
Design Review & Analysis
- • DfAM assessment and recommendations
- • Printability analysis and optimization
- • Material selection consultation
- • Cost optimization strategies
Advanced Optimization
- • Topology optimization implementation
- • Lattice structure design and validation
- • Generative design consultation
- • Multi-material design strategies
Process Support
- • Build preparation and orientation
- • Support structure optimization
- • Post-processing planning
- • Quality assurance protocols
Our collaborative approach combines your engineering expertise with our manufacturing knowledge to create optimized designs that push the boundaries of what's possible with metal 3D printing. From initial concept through production validation, we're your partner in advanced manufacturing innovation.
Ready to Optimize Your Metal 3D Printing Designs?
Connect with our manufacturing specialists to discuss your project requirements and discover how advanced design techniques can enhance your metal additive manufacturing outcomes.
Related Topics
Continue Reading
Explore more insights from our manufacturing experts