Understanding Mechanical Properties of 3D Prints: Complete Guide to Material Selection and Performance Analysis
Master the fundamentals of mechanical properties in 3D printed materials through stress-strain analysis, material testing, and engineering design principles. Learn to select the optimal materials for your applications using scientific data and proven methodologies.
Engineering Team
Materials Engineers
Understanding mechanical properties is fundamental to successful 3D printing applications. From prototyping to end-use production, the stress-strain curve provides critical insights into material behavior under load. This comprehensive guide demystifies material data sheets and empowers engineers to make informed decisions based on quantitative analysis rather than intuition.
Key Mechanical Properties
- • Tensile Strength: Maximum stress a material can withstand
- • Yield Strength: Stress at which permanent deformation begins
- • Young's Modulus: Material stiffness and elastic behavior
- • Elongation at Break: Ductility and failure characteristics
- • Toughness: Energy absorption capacity before failure
The Foundation: Stress-Strain Curves in 3D Printing
The stress-strain curve represents the fundamental relationship between applied force and material deformation, providing essential data for engineering design and material selection. In 3D printing applications, understanding this relationship enables engineers to predict part performance, optimize designs, and select appropriate materials for specific loading conditions.
While mathematical analysis underlies all mechanical property calculations, practical understanding requires only conceptual familiarity with the stress-strain relationship. This approach makes material selection accessible to designers and engineers without extensive materials science backgrounds while maintaining scientific rigor in decision-making processes.
Tensile Testing: The Standard Methodology
Tensile testing forms the backbone of mechanical property characterization, utilizing standardized specimens and controlled loading conditions to generate reliable, reproducible data. The testing process involves clamping a precisely machined specimen in a universal testing machine and applying steadily increasing tensile force until failure occurs.
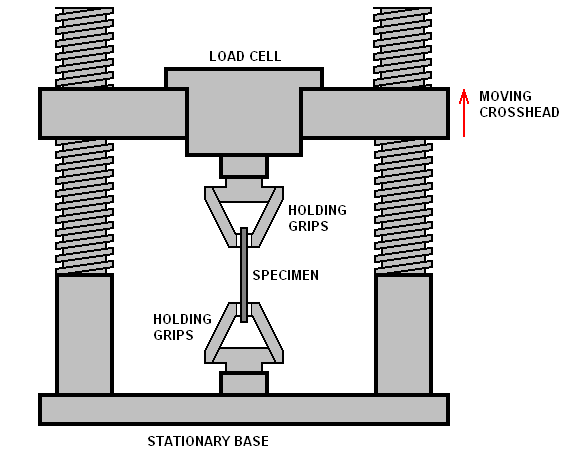
Critical aspects of tensile testing include:
- Specimen standardization: ASTM and ISO standards ensure consistent geometry and surface finish
- Loading rate control: Consistent strain rates enable reproducible material characterization
- Environmental conditioning: Temperature and humidity control for accurate data
- Data acquisition: High-resolution measurement of force and displacement
- Statistical validation: Multiple specimens provide confidence in material properties
The relationship between applied stress and resulting strain follows predictable patterns that reveal fundamental material characteristics. These patterns enable engineers to categorize materials by behavior type and select optimal candidates for specific applications.
Fundamental Stress-Strain Relationships
The stress-strain curve exhibits distinct regions that correspond to different deformation mechanisms within the material structure. Understanding these regions enables prediction of material behavior under various loading conditions and provides the foundation for safe, efficient design.
Strain: Measuring Material Deformation
Strain quantifies the relative deformation of a material under applied stress, expressed as the change in length divided by the original length. This dimensionless quantity, typically presented as a percentage, provides a normalized measure of deformation that enables comparison across different specimen sizes and geometries.
Engineering strain calculation:
ε = (L - L₀) / L₀ × 100%
Where: ε = strain (%), L = final length, L₀ = original length
The maximum strain value, recorded as "elongation at break" or "percent elongation" on material data sheets, serves as a primary indicator of material ductility. Higher elongation values indicate greater ductility, while lower values suggest brittle behavior that may limit application suitability.
Stress: Quantifying Internal Forces
Stress represents the internal force distribution within a material, calculated as the applied force divided by the cross-sectional area. This normalized approach enables comparison of materials with different geometries and provides the basis for design calculations and safety factor determination.
Engineering stress calculation:
σ = F / A₀
Where: σ = stress (MPa or psi), F = applied force, A₀ = original cross-sectional area
Two critical stress values appear on material data sheets: yield strength and ultimate tensile strength (UTS). These values define the operational limits for design applications and provide essential data for safety factor calculations.
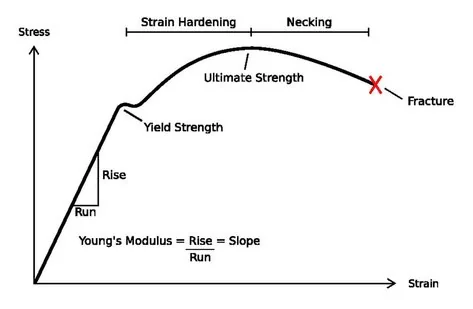
Critical Regions of the Stress-Strain Curve
The stress-strain curve exhibits distinct regions that correspond to different deformation mechanisms and material behaviors. Understanding these regions enables engineers to predict performance under various loading conditions and select appropriate materials for specific applications.
Elastic Region: Reversible Deformation
The elastic region represents the initial linear portion of the stress-strain curve where deformation remains fully reversible. Within this region, the material behaves like a spring, returning to its original dimensions when the applied load is removed. This behavior follows Hooke's Law, establishing a linear relationship between stress and strain.
Key characteristics of elastic behavior:
- Linear relationship: Stress and strain maintain proportional relationship
- Reversible deformation: Complete recovery upon load removal
- Slope significance: Line slope defines Young's Modulus (material stiffness)
- Design region: Normal operating conditions should remain within elastic limits
- Energy storage: Elastic deformation stores recoverable energy
Young's Modulus: Material Stiffness Quantification
Young's Modulus, also known as the modulus of elasticity, quantifies material stiffness by measuring the slope of the elastic region. This fundamental property determines how much a material will deform under a given load, making it crucial for applications requiring dimensional stability or precise deflection control.
Engineering Application
Higher Young's Modulus values indicate stiffer materials that resist deformation, while lower values suggest more flexible materials. For structural applications requiring minimal deflection, specify materials with high modulus values.
Yield Point: Transition to Permanent Deformation
The yield point marks the transition from elastic to plastic behavior, representing the stress level at which permanent deformation begins. Beyond this critical threshold, the material will not return to its original dimensions when the load is removed, making yield strength a crucial design parameter for applications requiring dimensional stability.
Yield strength appears on material data sheets as a fundamental design property, typically specified with a 0.2% offset criterion for materials lacking a distinct yield point. This standardized approach ensures consistent measurement and comparison across different materials and testing laboratories.
Plastic Region: Permanent Deformation Mechanisms
The plastic region encompasses the nonlinear portion of the stress-strain curve beyond the yield point, where deformation becomes permanent through mechanisms such as dislocation movement in crystalline materials or chain slippage in polymers. Understanding plastic behavior is essential for applications involving forming operations or energy absorption requirements.
Plastic region characteristics:
- Nonlinear behavior: Stress-strain relationship becomes curved
- Permanent deformation: Material retains shape changes after unloading
- Work hardening: Many materials strengthen during plastic deformation
- Ultimate strength: Maximum stress occurs within the plastic region
- Energy absorption: Plastic deformation dissipates mechanical energy
Ultimate Tensile Strength and Failure
Ultimate tensile strength (UTS) represents the maximum stress a material can withstand before the onset of necking and subsequent failure. This critical property defines the absolute load-carrying capacity and serves as a fundamental parameter for safety factor calculations and failure analysis.
Beyond UTS, most ductile materials exhibit necking, a localized reduction in cross-sectional area that concentrates deformation and leads to eventual failure. The stress appears to decrease beyond UTS due to the reduced load-bearing area, even though the actual stress within the necked region continues increasing.
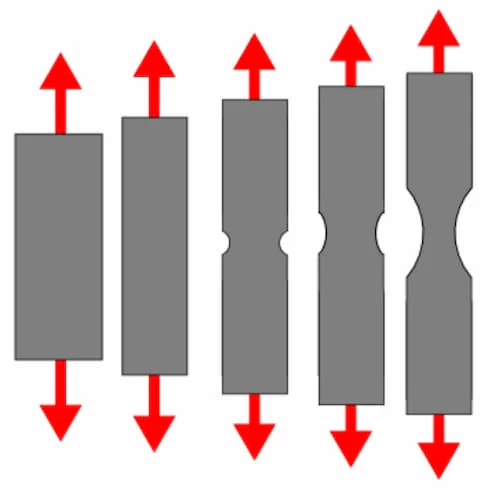
Toughness: Energy Absorption Capability
Toughness quantifies a material's ability to absorb energy through deformation before failure, represented geometrically as the area under the stress-strain curve. This property proves critical for applications involving impact loading, vibration resistance, or energy dissipation requirements.
Unlike strength or stiffness, which represent single-point properties, toughness integrates both strength and ductility into a composite measure of material performance. This integration makes toughness particularly valuable for applications requiring balanced mechanical properties rather than optimization of a single characteristic.
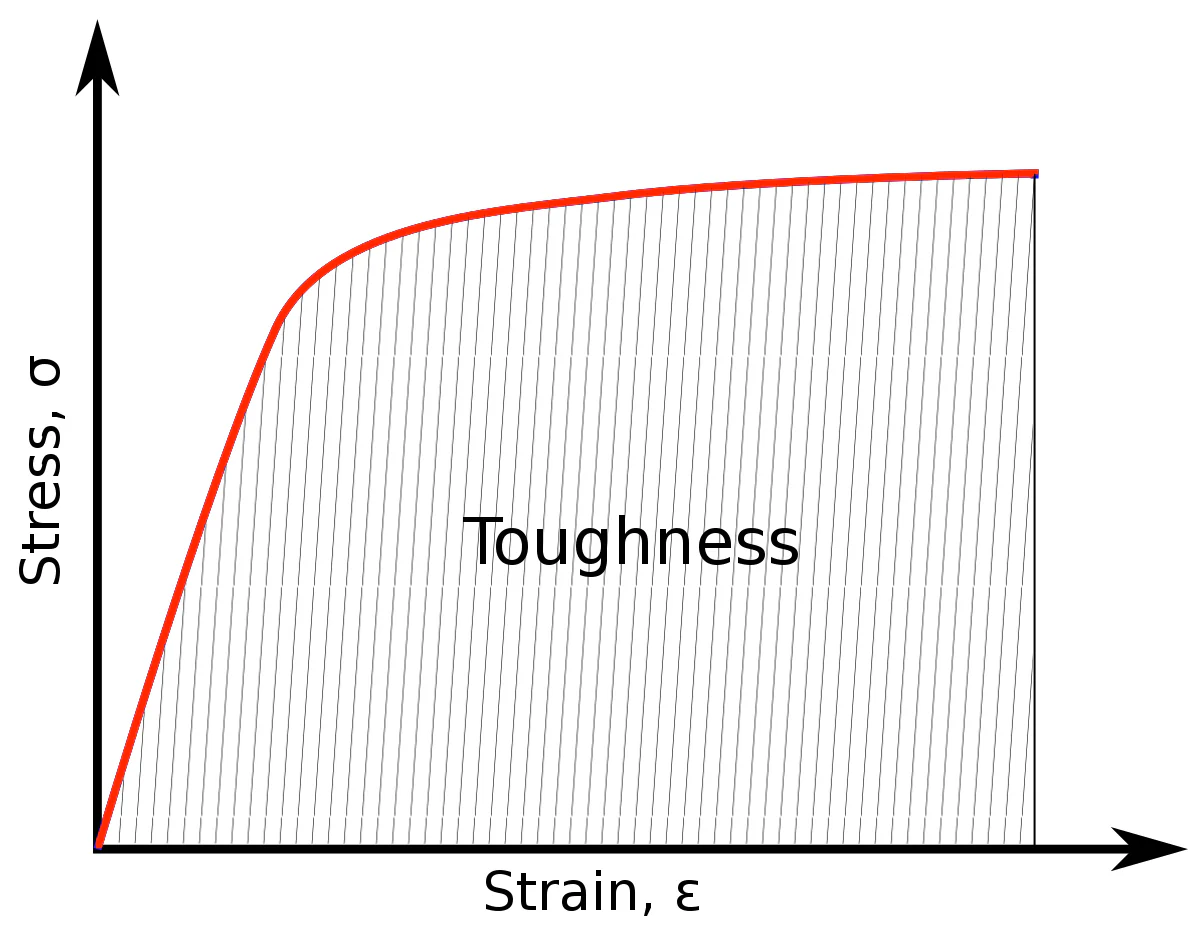
Impact Testing and Data Sheet Values
Material data sheets typically present toughness through impact testing results such as Izod impact or Charpy impact values. These standardized tests measure energy absorption under high-rate loading conditions, providing practical data for applications involving sudden loading or impact resistance requirements.
Common impact test methods:
- Izod Impact: Cantilever beam test with notched specimen
- Charpy Impact: Simply supported beam with central notch
- Drop dart impact: Falling weight test for thin specimens
- Tensile impact: High-rate tensile loading to failure
3D Printing Material Categories and Behavior Patterns
3D printing materials exhibit distinct stress-strain patterns that reflect their underlying molecular structure and processing history. Understanding these patterns enables engineers to categorize materials by behavior type and select optimal candidates for specific applications.
Thermoplastic Behavior Patterns
Thermoplastic materials used in FDM and SLS technologies exhibit characteristic stress-strain patterns that depend on molecular weight, crystallinity, and processing conditions. These materials generally display significant plastic deformation capability, making them suitable for applications requiring impact resistance or energy absorption.
Typical thermoplastic categories:
Material Type | Stiffness | Strength | Ductility | Typical Applications |
---|---|---|---|---|
Commodity (PLA, ABS) | Moderate | Moderate | Good | Prototyping, consumer products |
Engineering (Nylon, PC) | High | High | Excellent | Functional parts, tooling |
High-Performance (PEEK, PEI) | Very High | Very High | Moderate | Aerospace, medical implants |
Photopolymer Characteristics
Photopolymer materials used in SLA and PolyJet technologies exhibit distinct stress-strain patterns dominated by their crosslinked molecular structure. These materials typically display higher stiffness but lower ductility compared to thermoplastics, making them suitable for applications requiring dimensional accuracy and surface quality.
Photopolymer behavior characteristics:
- High initial stiffness: Crosslinked structure provides excellent dimensional stability
- Limited ductility: Brittle failure mode with minimal plastic deformation
- Temperature sensitivity: Properties vary significantly with temperature
- UV degradation: Long-term exposure affects mechanical properties
- Surface quality: Excellent detail resolution and smooth surface finish
Metal Additive Manufacturing Behavior
Metal 3D printing technologies such as DMLS produce parts with mechanical properties comparable to wrought metals, exhibiting characteristic metallic stress-strain behavior including significant plastic deformation and work hardening effects.
The unique thermal history of metal additive manufacturing creates microstructures that may differ from conventional processing methods, potentially affecting properties such as anisotropy, residual stress, and fatigue performance.
Practical Material Selection Strategies
Effective material selection requires systematic evaluation of application requirements against available material properties. The stress-strain curve provides the fundamental data needed for this analysis, enabling engineers to make informed decisions based on quantitative criteria rather than subjective assessments.
Load Analysis and Safety Factors
Material selection begins with comprehensive analysis of applied loads, environmental conditions, and performance requirements. This analysis establishes the baseline criteria against which candidate materials can be evaluated using stress-strain data and safety factor calculations.
Critical design considerations:
- Maximum operating stress: Determine peak loads and stress concentrations
- Deflection requirements: Establish acceptable deformation limits
- Cyclic loading: Consider fatigue effects for repeated loading
- Environmental factors: Temperature, humidity, chemical exposure
- Safety margins: Apply appropriate safety factors for load uncertainty
Comparative Analysis Framework
The stress-strain curve enables direct comparison of candidate materials through overlay plotting and property normalization. This visual approach reveals trade-offs between competing properties and identifies materials that best match application requirements.
Selection Example
For impact-resistant applications, prioritize materials with high area under the stress-strain curve (toughness) over those optimized for maximum strength or stiffness alone. The balanced approach provides better overall performance for dynamic loading conditions.
Processing Effects on Mechanical Properties
3D printing process parameters significantly influence final mechanical properties through effects on microstructure, residual stress, and material orientation. Understanding these relationships enables optimization of both material selection and processing conditions for specific applications.
Build Orientation Effects
Layer-by-layer construction in additive manufacturing creates inherent anisotropy, with mechanical properties varying according to build orientation relative to applied loads. This directional dependence requires careful consideration during design and material characterization phases.
Typical orientation effects:
- Z-axis weakness: Interlayer bonding typically weaker than in-plane properties
- Surface quality variation: Orientation affects surface finish and dimensional accuracy
- Support requirements: Overhanging features require support structures
- Property optimization: Orient critical load paths parallel to stronger directions
Post-Processing Impacts
Post-processing operations such as heat treatment, surface finishing, and stress relief can significantly modify mechanical properties from their as-printed state. These treatments offer opportunities to optimize properties for specific applications while addressing processing-induced limitations.
Common post-processing effects include:
- Annealing: Reduces residual stress and improves ductility
- Hot isostatic pressing: Eliminates porosity and improves fatigue performance
- Surface treatment: Improves fatigue resistance through surface finishing
- Chemical treatment: Modifies surface properties for specific applications
Industry-Specific Requirements and Standards
Different industries impose specific requirements for mechanical property documentation, testing protocols, and quality assurance procedures. Understanding these requirements ensures material selection and characterization meet regulatory and performance standards.
Aerospace Applications
Aerospace applications demand comprehensive mechanical property documentation with strict adherence to industry standards such as ASTM, SAE, and AS specifications. These requirements often include extensive testing matrices, statistical analysis, and long-term performance validation.
Critical aerospace considerations:
- Fatigue performance: Million-cycle testing for rotating components
- Temperature effects: Property retention across operating temperature range
- Damage tolerance: Crack growth resistance and fail-safe design
- Weight optimization: Specific strength and stiffness parameters
Medical Device Requirements
Medical device applications require biocompatibility testing in addition to mechanical property characterization, with particular attention to long-term stability and degradation behavior in biological environments.
Medical device considerations:
- Biocompatibility: ISO 10993 testing for biological safety
- Sterilization effects: Property changes during sterilization cycles
- Long-term stability: Degradation behavior in physiological conditions
- Fatigue resistance: Cyclic loading performance for implantable devices
Automotive Standards
Automotive applications emphasize impact resistance, temperature performance, and environmental durability, often requiring specialized testing protocols that simulate real-world operating conditions.
Advanced Characterization Techniques
Beyond basic tensile testing, advanced characterization techniques provide additional insights into material behavior under complex loading conditions, environmental exposure, and long-term performance requirements.
Dynamic Mechanical Analysis
Dynamic mechanical analysis (DMA) characterizes material response to oscillatory loading over a range of frequencies and temperatures, providing insights into viscoelastic behavior and temperature-dependent properties crucial for many applications.
DMA applications include:
- Glass transition identification: Critical temperature ranges for polymer materials
- Damping characterization: Energy dissipation and vibration control properties
- Frequency effects: Rate-dependent behavior for dynamic applications
- Comparative analysis: Material ranking for temperature-sensitive applications
Fatigue Testing and Analysis
Fatigue testing characterizes material response to repeated loading cycles, providing essential data for applications involving cyclic loading conditions. This testing reveals failure mechanisms not captured by static testing and enables life prediction for cyclically loaded components.
Fatigue testing approaches:
- High-cycle fatigue: Million-cycle testing at lower stress levels
- Low-cycle fatigue: Thousand-cycle testing with plastic deformation
- S-N curve development: Stress versus cycle count relationships
- Mean stress effects: Impact of load ratio on fatigue performance
Quality Control and Testing Protocols
Consistent mechanical property characterization requires standardized testing protocols, proper specimen preparation, and statistical analysis of results. These quality control measures ensure reliable data for design decisions and regulatory compliance.
Specimen Preparation Standards
Proper specimen preparation critically affects test results and data reliability. Standardized procedures ensure consistent surface finish, geometric accuracy, and freedom from processing defects that could influence mechanical properties.
Preparation requirements:
- Geometric tolerances: Precise dimensions according to test standards
- Surface finish: Controlled roughness to minimize stress concentrations
- Machining effects: Minimize heat generation and surface damage
- Defect inspection: Visual and dimensional inspection before testing
Statistical Analysis and Data Interpretation
Mechanical property data exhibits natural variation that requires statistical analysis for proper interpretation and application. Understanding data distribution, confidence intervals, and design allowables ensures appropriate safety margins and reliable performance prediction.
Statistical considerations:
- Sample size requirements: Adequate specimen count for statistical validity
- Distribution analysis: Normal, Weibull, or other appropriate distributions
- Confidence intervals: Quantified uncertainty in property values
- Design allowables: Conservative values for design calculations
Digital Material Data Management
Modern material selection increasingly relies on digital databases, simulation tools, and integrated design workflows that leverage stress-strain data for automated analysis and optimization. These digital approaches enhance efficiency while maintaining scientific rigor in material selection processes.
Material Database Integration
Comprehensive material databases enable rapid property comparison, automated material selection, and integration with finite element analysis tools. These systems facilitate evidence-based decision making while reducing time required for material evaluation and qualification.
Digital workflow benefits:
- Rapid screening: Filter materials by property criteria
- Automated analysis: Generate stress-strain plots and property comparisons
- Design integration: Direct import of material models into simulation software
- Traceability: Maintain links between properties and source data
Future Trends in Mechanical Characterization
Advancing technologies in testing equipment, data analysis, and material modeling are expanding the scope and precision of mechanical property characterization. These developments promise to enhance material selection accuracy while reducing testing time and costs.
High-Throughput Testing
Automated testing systems enable rapid characterization of large material libraries, accelerating material development and optimization cycles. These systems combine robotic specimen handling with advanced data analysis to provide comprehensive property databases with minimal human intervention.
Machine Learning Applications
Machine learning algorithms are increasingly applied to material property prediction, enabling estimation of mechanical properties from processing parameters or limited test data. These approaches show promise for reducing testing requirements while maintaining accuracy in property prediction.
Practical Implementation Guidelines
Successful implementation of stress-strain analysis requires systematic approaches that balance thoroughness with practical constraints. These guidelines provide a framework for integrating mechanical property analysis into design and material selection workflows.
Material Selection Checklist
- ✓ Define load requirements and operating conditions
- ✓ Identify critical mechanical properties for application
- ✓ Screen candidate materials using stress-strain data
- ✓ Consider processing effects and anisotropy
- ✓ Validate selection through prototype testing
- ✓ Establish quality control procedures
- ✓ Document material selection rationale
Conclusion: Evidence-Based Material Selection
Understanding mechanical properties through stress-strain analysis provides the foundation for successful 3D printing applications across industries and applications. The systematic approach outlined in this guide enables engineers to move beyond intuitive material selection toward evidence-based decisions supported by quantitative analysis.
The stress-strain curve serves as a universal language for material behavior, enabling communication between designers, manufacturers, and end users. This common framework facilitates collaborative problem-solving and ensures that material selection decisions align with application requirements and performance expectations.
As 3D printing technologies continue advancing, the fundamental principles of mechanical property analysis remain constant. The investment in understanding these principles pays dividends across all applications, from initial prototyping through production implementation and long-term performance optimization.
Success in material selection requires balancing multiple competing properties while maintaining focus on application-critical characteristics. The stress-strain curve provides the analytical framework needed for these complex trade-off decisions, enabling optimal material selection for each unique application.
Need Material Selection Guidance?
Our materials engineering team specializes in application-specific material selection and mechanical property analysis. We provide comprehensive testing services and design consultation to ensure optimal material choices for your 3D printing projects.
Contact our materials experts for personalized consultation, or explore our materials database for detailed property information.
Related Topics
Continue Reading
Explore more insights from our manufacturing experts