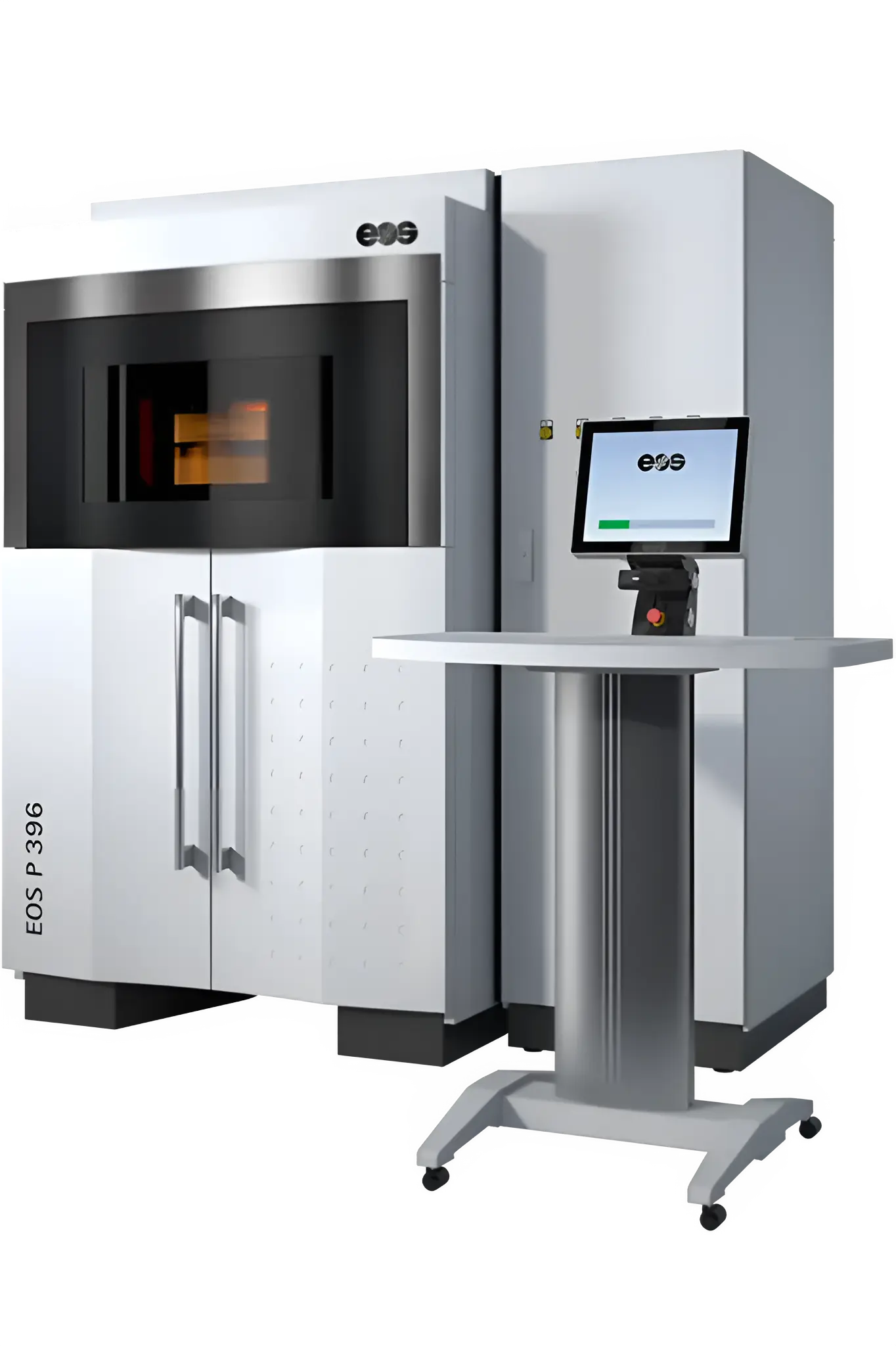
PolyJet3D Printing Design Guidelines
Our PolyJet design guidelines help engineers and designers optimize multi-material printing for exceptional detail, smooth surface finishes, and complex geometries. Whether for prototyping or presentation models, these best practices ensure high-quality parts with variable material properties.
Quick Specifications
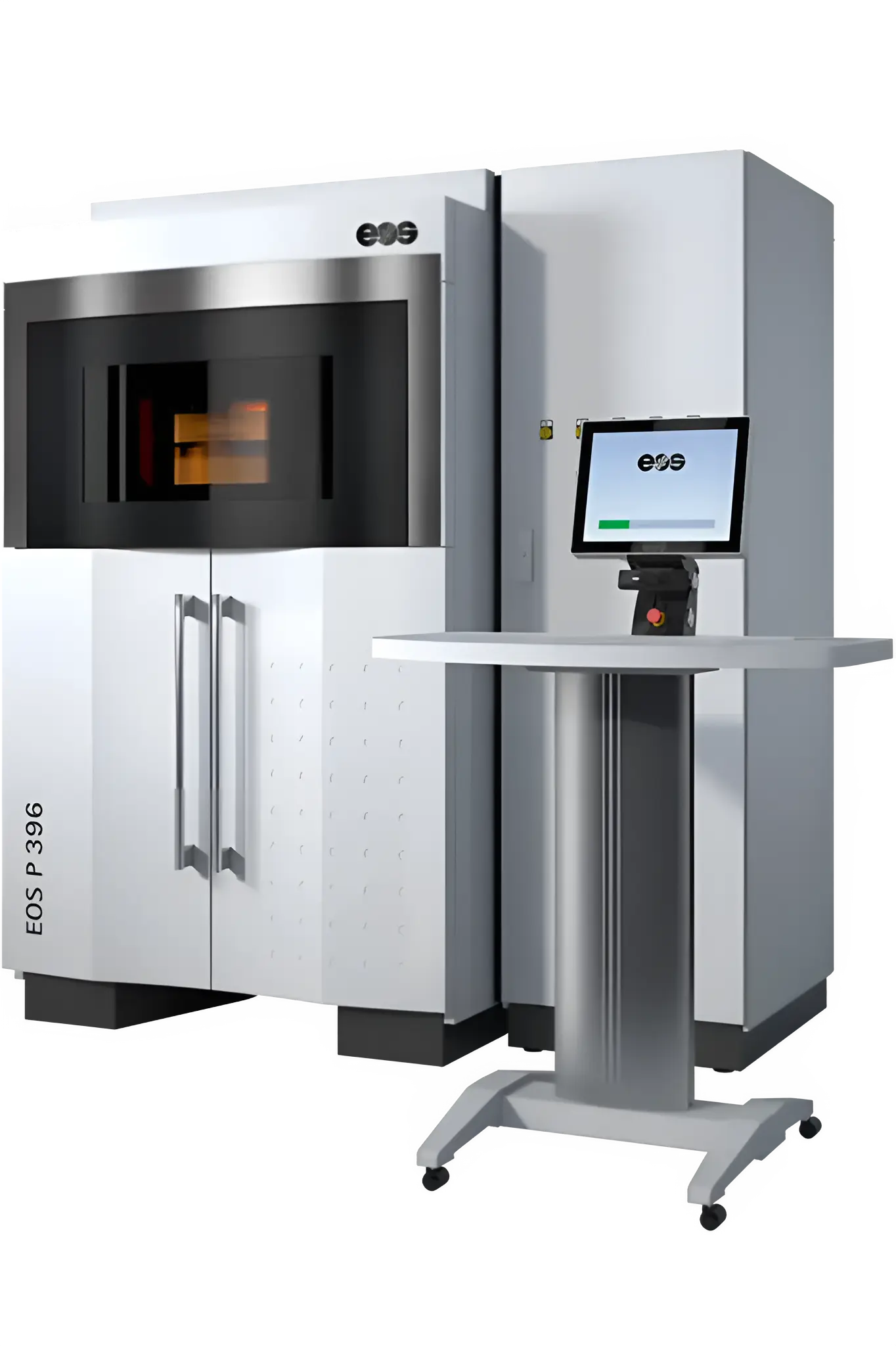
Quick Navigation
Overview
PolyJet is a precision 3D printing technology that uses inkjet heads to deposit liquid photopolymer resins in ultra-thin layers. The ability to combine up to 3 different materials in a single build makes it ideal for multi-material prototypes, overmolds, and complex assemblies.
These PolyJet design guidelines outline critical considerations for multi-material design, support removal, tolerances, and surface quality. Following these practices ensures optimal results for both functional prototypes and presentation models.
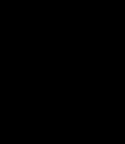
Maximum Build Volume
380 × 284 × 380 mm (15 × 11.2 × 15 in)
Our Stratasys J750 DAP and Connex3 printers offer a maximum build volume of 380 × 284 × 380 mm (15 × 11.2 × 15 in), accommodating both small detailed components and larger assemblies. The system operates with a precise 28-micron layer height for exceptional detail resolution.
Multi-material builds require multi-body STEP files with separate bodies for each material assignment.
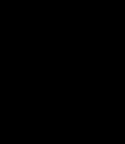
Tolerances
±0.2% (Lower limit of ±0.2 mm)
PolyJet achieves exceptional dimensional accuracy with tolerances of ±0.2% (minimum ±0.2 mm). Parts with large flat surfaces may experience slight warping, so avoid these geometries when tight tolerances are critical.
Include engineering drawings for parts requiring specific tolerances.
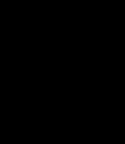
Layer Height
28 Microns
The ultra-fine 28-micron layer height provides exceptional detail resolution and smooth surface finish. This precision enables fine features, sharp edges, and intricate geometries that would be difficult to achieve with other 3D printing technologies.
The fine layer height minimizes stepping artifacts on curved surfaces and angled features.
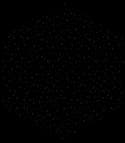
Surface Finish
Smooth, Ra 1-3 μm
PolyJet parts emerge with smooth, injection-molded quality surface finish straight from the printer. The combination of fine layer height and precise material deposition results in minimal post-processing requirements for most applications.
Gel-like support material removes cleanly without leaving marks on supported surfaces.
Wall Thickness
Wall thickness requirements vary based on material type and support conditions. Multi-material designs require careful consideration of material transitions and interface bonding.
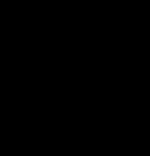
Rigid Material Walls
0.6 mm (0.8 mm recommended)
Rigid materials like RGD450 require a minimum wall thickness of 0.6 mm, though 0.8 mm is recommended for optimal strength and durability. Thinner walls may be fragile and prone to cracking during support removal.
Recommendations:
- Use 0.8 mm minimum for functional prototypes
- Consider stress concentrations at material interfaces
- Add reinforcement ribs for large thin-walled sections
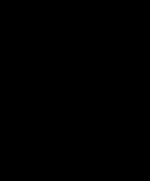
Flexible Material Walls
1.0 mm minimum
Flexible materials like Agilus30 require thicker walls (minimum 1.0 mm) to maintain structural integrity. These materials are designed for gaskets, overmolds, and soft-touch applications.
Recommendations:
- Design with intended flexibility in mind
- Consider shore hardness requirements
- Test material transitions with prototypes
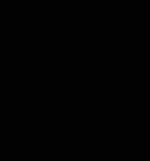
Multi-Material Interface
Design Considerations
Multi-material interfaces require careful design to ensure proper bonding between materials. The chemical bonding between materials during printing creates strong interfaces when properly designed.
Recommendations:
- Design gradual transitions between materials
- Avoid sharp corners at material boundaries
- Test interface strength with prototypes
Minimum Detail
PolyJet excels at fine detail reproduction due to its 28-micron layer height and precise material deposition. Features can be much smaller than other 3D printing technologies.
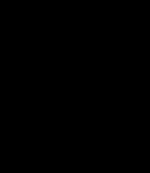
Engraved Details
Minimum Width and Depth: 0.2 mm
Engraved features can be as small as 0.2 mm in width and depth due to the precision of the inkjet heads. The smooth surface finish preserves fine details without layer line interference.
Recommendations:
- Use bold, clear fonts for text
- Consider surface orientation for optimal detail
- Test small features with prototype builds
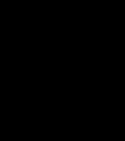
Embossed Details
Minimum Width and Height: 0.2 mm
Raised features benefit from the smooth surface finish and can be reproduced with exceptional clarity. The gel-like support material supports overhanging details without surface marks.
Recommendations:
- Design with adequate clearance from support areas
- Consider printing orientation for best results
- Use chamfers on sharp edges for durability
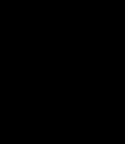
Text Size
Minimum: 8pt (embossed), 10pt (engraved)
Text can be much smaller than other 3D printing technologies due to the precision of PolyJet. Sans-serif fonts work best for small text applications.
Recommendations:
- Use bold fonts for better readability
- Test text sizes with material samples
- Consider contrast between materials for multi-material text
Part Clearances
Clearances for moving parts and assemblies can be tighter than other 3D printing technologies due to the precision and smooth surface finish of PolyJet.
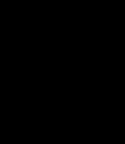
Minimum Clearance
0.2 mm
The smooth surface finish and precision of PolyJet allows for tighter clearances than other 3D printing technologies. A minimum of 0.2 mm clearance is recommended for moving parts.
Recommendations:
- Test clearances with functional prototypes
- Consider material combinations for different friction properties
- Account for post-processing effects on dimensions
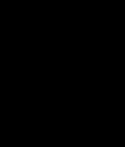
Living Hinges
0.3-0.5 mm thickness
PolyJet excels at printing living hinges using flexible materials. Design hinges 0.3-0.5 mm thick for optimal flexibility and durability.
Recommendations:
- Use Agilus30 or blended materials for hinges
- Test hinge design with prototype builds
- Consider stress relief features at hinge points

Snap-Fit Connections
Design for material properties
Multi-material capabilities enable snap-fits with rigid tabs and flexible clips in single builds. Design based on material properties and intended use.
Recommendations:
- Use rigid materials for structural elements
- Use flexible materials for clips and springs
- Test engagement forces with prototypes
Support Material
PolyJet uses gel-like water-soluble support material that enables complex geometries and removes cleanly without surface marks.
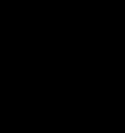
Support Removal
Water-soluble gel support
The gel-like support material dissolves in water and can be removed through water jetting and manual cleaning. This enables complex internal geometries and overhangs.
Recommendations:
- Design adequate access for support removal
- Consider hollow part drainage requirements
- Orient parts to minimize support contact on critical surfaces
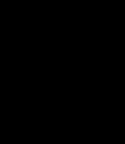
Drain Holes for Hollow Parts
2-3 mm diameter minimum
Hollow parts filled with support material require drain holes for complete removal. Design multiple holes for complex internal geometries.
Recommendations:
- Use multiple drain holes for complex shapes
- Position holes in non-critical areas
- Consider post-processing to close holes if needed
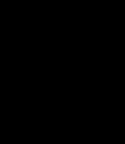
Overhang Angles
All angles supported
Unlike other 3D printing technologies, PolyJet can print any overhang angle due to its comprehensive support system. This enables maximum design freedom.
Design freedom allows for complex geometries impossible with other technologies.
Multi-Material Design
PolyJet's unique multi-material capability enables complex assemblies with integrated soft and hard components in single builds.
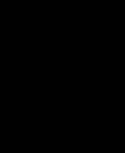
Material Assignment
Multi-body STEP files required
Multi-material parts require multi-body STEP files where each component is modeled as a separate body. Our team assigns materials based on design intent and requirements.
Recommendations:
- Model each material as a separate body
- Maintain clear material boundaries
- Document material requirements clearly
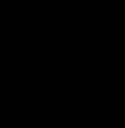
Variable Shore Hardness
Shore A30-A95 range
By blending rigid and flexible materials, PolyJet can create custom shore hardness values from A30 to A95 in precise ratios for specific applications.
Recommendations:
- Specify target shore hardness values
- Test material properties with samples
- Consider application requirements for hardness
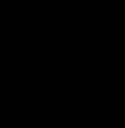
Overmolds and Soft-Touch
Integrated multi-material design
Create overmolds with rigid substrates and flexible covers in single builds. This eliminates assembly requirements and ensures perfect fit.
Recommendations:
- Design proper material transitions
- Consider grip patterns and textures
- Test ergonomics with functional prototypes
Ready to Start Your PolyJet Project?
Upload your design and get an instant quote optimized for polyjet manufacturing.
Click to start your quote
STL, STEP, OBJ, 3MF supported • Get instant pricing